Metal Binder Jet Solution(MBJ)
Table of Contents
Overview of Metal Binder Jet Solution
Metal Binder Jetting (MBJ) is a revolutionary 3D printing technology that enables the creation of complex metal parts by binding metal powder particles together layer by layer. This innovative approach is transforming the manufacturing landscape, providing significant advantages in terms of design flexibility, production speed, and cost-effectiveness.
Binder Jetting, unlike other additive manufacturing techniques, does not rely on melting the metal powder. Instead, a liquid binder is selectively deposited onto a bed of metal powder, forming a layer of the desired shape. This process is repeated, building up the part layer by layer until it is complete. After printing, the part undergoes a post-processing step, such as sintering, to fuse the powder into a solid metal part.
Key Features of Metal Binder Jetting
- No Heat Involved: Eliminates thermal stresses and distortions common in other 3D printing methods.
- High Speed: Faster production times compared to traditional methods.
- Cost-Effective: Lower material waste and energy consumption.
- Design Flexibility: Capable of producing complex geometries that are difficult or impossible with conventional techniques.
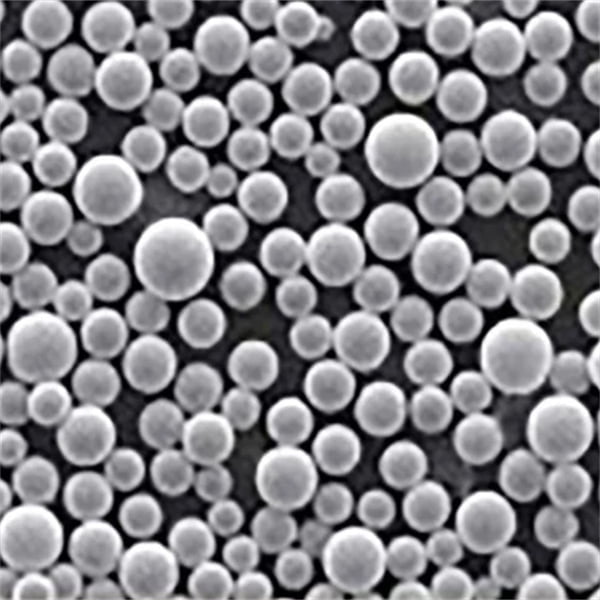
Types and Characteristics of Metal Powders for Binder Jetting
Metal powders are crucial for the success of the binder jetting process. Here, we’ll discuss specific metal powder models, their compositions, properties, and characteristics.
Metal Powder | Composition | Properties | Characteristics |
---|---|---|---|
316L Stainless Steel | Iron, Chromium, Nickel, Molybdenum | High corrosion resistance, good mechanical properties | Ideal for medical and food applications |
17-4 PH Stainless Steel | Iron, Chromium, Nickel, Copper | High strength, good corrosion resistance, heat-treatable | Used in aerospace and automotive industries |
Inconel 625 | Nickel, Chromium, Molybdenum, Niobium | Excellent high-temperature strength, oxidation resistance | Suitable for aerospace and chemical industries |
Inconel 718 | Nickel, Chromium, Iron, Niobium, Molybdenum | High strength at elevated temperatures, good corrosion resistance | Preferred in aerospace and gas turbines |
Cobalt-Chrome | Cobalt, Chromium, Molybdenum | High wear resistance, biocompatibility | Used in medical implants and dental restorations |
Aluminum 6061 | Aluminum, Magnesium, Silicon | Lightweight, good mechanical properties, corrosion resistance | Common in automotive and aerospace industries |
Titanium Ti-6Al-4V | Titanium, Aluminum, Vanadium | High strength-to-weight ratio, corrosion resistance, biocompatibility | Widely used in medical and aerospace sectors |
Copper | Pure Copper | Excellent thermal and electrical conductivity | Utilized in electronics and heat exchangers |
Bronze | Copper, Tin | Good wear resistance, machinability | Often used for artistic and historical restorations |
Tool Steel (M2) | Iron, Tungsten, Molybdenum, Chromium | High hardness, wear resistance | Suitable for cutting tools and dies |
Applications of Metal Binder Jetting Solutions
Metal Binder Jetting offers versatile applications across various industries. Here’s how it impacts different sectors:
Industry | Applications | Benefits |
---|---|---|
Aerospace | Turbine blades, structural components | Lightweight, high-strength parts, design flexibility |
Automotive | Engine components, brackets, gears | Reduced weight, complex geometries, rapid prototyping |
Medical | Implants, surgical instruments | Biocompatible materials, custom designs |
Dental | Crowns, bridges, dentures | Precision, customization, fast production |
Consumer Goods | Jewelry, eyewear, custom parts | Design freedom, personalization, cost-effective production |
Industrial | Tooling, fixtures, molds | Durable, high-performance parts, quick turnaround |
Electronics | Heat sinks, connectors, housings | Efficient thermal management, precise designs |
Energy | Turbine components, heat exchangers | High-temperature resistance, durability |
Specifications, Sizes, Grades, and Standards
Understanding the specifications, sizes, grades, and standards for metal powders and the binder jetting process is crucial for achieving desired outcomes.
Metal Powder | Size Range (µm) | Grade | Standards |
---|---|---|---|
316L Stainless Steel | 15-45 | ASTM F138 | ASTM, ISO 5832-1 |
17-4 PH Stainless Steel | 20-53 | ASTM A564 | ASTM, SAE AMS 5643 |
Inconel 625 | 15-45 | ASTM B443 | ASTM, UNS N06625 |
Inconel 718 | 15-53 | AMS 5662 | ASTM, AMS 5663 |
Cobalt-Chrome | 20-50 | ASTM F75 | ISO 5832-4, ASTM F1537 |
Aluminum 6061 | 20-63 | ASTM B209 | ASTM, SAE AMS 4027 |
Titanium Ti-6Al-4V | 15-45 | ASTM F136 | ASTM, ISO 5832-3 |
Copper | 15-45 | ASTM B152 | ASTM, UNS C11000 |
Bronze | 20-63 | ASTM B584 | ASTM, UNS C83600 |
Tool Steel (M2) | 15-45 | ASTM A600 | ASTM, UNS T11302 |
Suppliers and Pricing Details
Finding the right supplier and understanding pricing details is vital for budgeting and project planning.
Supplier | Metal Powders Offered | Pricing (per kg) | Contact Information |
---|---|---|---|
Sandvik | Stainless steels, tool steels, titanium alloys | $100 – $250 | www.materials.sandvik/contact |
Höganäs | Stainless steels, tool steels, bronze | $80 – $200 | www.hoganas.com/contact |
Carpenter Additive | Nickel alloys, titanium alloys, stainless steels | $120 – $300 | www.carpenteradditive.com/contact |
GKN Additive | Stainless steels, tool steels, copper | $90 – $220 | www.gknpm.com/contact |
AP&C (GE Additive) | Titanium alloys, aluminum alloys, nickel alloys | $150 – $350 | www.ge.com/additive/contact |
LPW Technology | Stainless steels, nickel alloys, cobalt-chrome | $130 – $320 | www.lpwtechnology.com/contact |
TLS Technik | Tool steels, stainless steels, nickel alloys | $110 – $270 | www.tls-technik.de/contact |
Praxis Powder Technology | Aluminum alloys, stainless steels, bronze | $85 – $210 | www.praxispowdertech.com/contact |
Arcam (GE Additive) | Titanium alloys, cobalt-chrome, nickel alloys | $140 – $330 | www.arcam.com/contact |
Oerlikon Metco | Nickel alloys, titanium alloys, stainless steels | $120 – $310 | www.oerlikon.com/metco/contact |
Comparing Pros and Cons: Advantages and Limitations
Metal Binder Jetting, like any technology, has its pros and cons. Let’s compare the advantages and limitations to give a balanced view.
Aspect | Advantages | Limitations |
---|---|---|
Design Flexibility | Can create complex geometries with ease | Limited by powder bed size |
Production Speed | Faster production compared to traditional methods | May require post-processing |
Material Utilization | Minimal waste, efficient use of materials | Limited to specific metal powders |
Cost-Effectiveness | Reduced energy consumption and material costs | High initial setup costs |
Thermal Stress | No thermal distortion | Requires careful control of binder and powder |
Surface Finish | Good as-printed surface finish | May need additional finishing for some applications |
Mechanical Properties | Comparable to wrought materials | Sintering process can impact final properties |
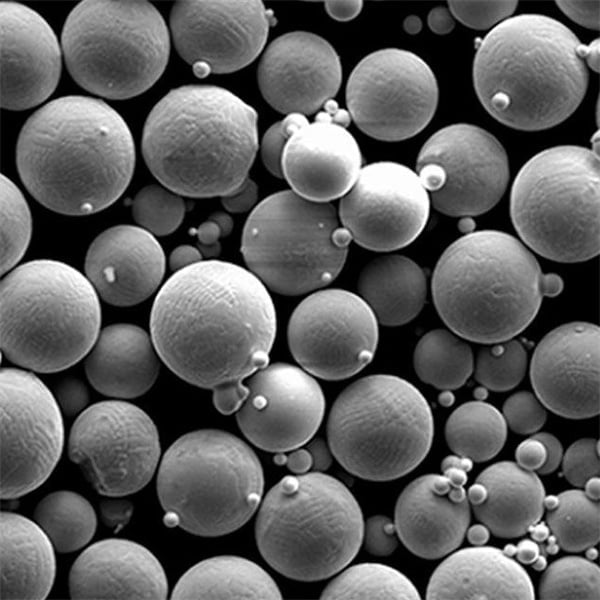
FAQs
What is Metal Binder Jetting?
Metal Binder Jetting is an additive manufacturing process where a liquid binder is used to bond layers of metal powder together to form complex metal parts.
What is metal binder jetting?
Metal binder jetting is a 3D printing process that uses a liquid binder to selectively glue metal powder particles together, layer by layer, building up a 3D object. It’s similar to how an inkjet printer works, but instead of ink on paper, it uses a binder on metal powder.
How does it work?
- Create a 3D model: Design your part using CAD software.
- Slice the model: Prepare the model for printing by slicing it into thin layers.
- Printing:
- A thin layer of metal powder is spread across a platform.
- An inkjet printhead deposits binder onto the powder, adhering particles according to the sliced model.
- The platform lowers, and a new layer of powder is spread.
- This process repeats, building the part layer by layer.
- Post-processing:
- The printed part is weak and needs a binder burnout stage to remove the temporary binder.
- Finally, the part is sintered in a furnace at high temperatures to fuse the metal particles and achieve final strength and density.
What are the benefits of metal binder jetting?
- Faster printing: Compared to other metal 3D printing methods like laser powder bed fusion, binder jetting can be significantly faster.
- Mass production potential: Binder jetting is well-suited for high-volume production due to its speed and printability of complex geometries.
- Wider material range: It can work with a variety of metal powders, including stainless steel, inconel, and titanium.
What are the limitations of metal binder jetting?
- Part strength: While sintering strengthens the parts, they may not be quite as strong as those made with other metal additive manufacturing techniques.
- Surface finish: The surface finish of binder jetted parts can be rougher than other methods. Post-processing techniques like machining may be required for a smoother finish.
What are some applications of metal binder jetting?
- Aerospace components: Lightweight and complex parts for airplanes and spacecraft.
- Medical devices: Custom implants and surgical tools.
- Automotive parts: Prototypes and low-volume production of complex components.
Share On
MET3DP Technology Co., LTD is a leading provider of additive manufacturing solutions headquartered in Qingdao, China. Our company specializes in 3D printing equipment and high-performance metal powders for industrial applications.
Inquiry to get best price and customized Solution for your business!
Related Articles
About Met3DP
Recent Update
Our Product
CONTACT US
Any questions? Send us message now! We’ll serve your request with a whole team after receiving your message.
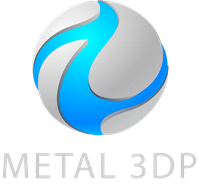
Metal Powders for 3D Printing and Additive Manufacturing