Metal Injection Molding (MIM)
Table of Contents
Imagine a manufacturing process that merges the intricate detail and design freedom of plastic injection molding with the unparalleled strength and durability of metal. That’s the magic of Metal Injection Molding (MIM), a game-changer in the world of metalworking.
What is Metal Injection Molding (MIM)?
MIM is a near-net-shape manufacturing technique that utilizes a unique blend of metal powder and a polymeric binder. This combination, known as feedstock, behaves much like a moldable paste. The MIM process strategically injects this feedstock into a mold cavity under high pressure, replicating the desired intricate geometry. Here’s the breakdown of the MIM process into its key stages:
- Feedstock Preparation: Finely-powdered metal, typically stainless steel, steel alloys, or even exotic materials like tungsten carbide, is meticulously mixed with a binder system. This binder ensures the flowability of the mixture during injection molding.
- Molding: The prepared feedstock is injected into a precisely designed mold cavity under high pressure. This replicates the intricate near-net shape of the desired metal component.
- Debinding: After molding, the binder needs to be removed from the molded part. This delicate process, often called debinding, can involve thermal techniques (heating) or solvent debinding, depending on the chosen binder system.
- Sintering: The debindered part, now a fragile structure of metal powder, undergoes a high-temperature sintering process in a controlled atmosphere. This crucial step fuses the metal particles together, achieving the desired strength and density for the final component.
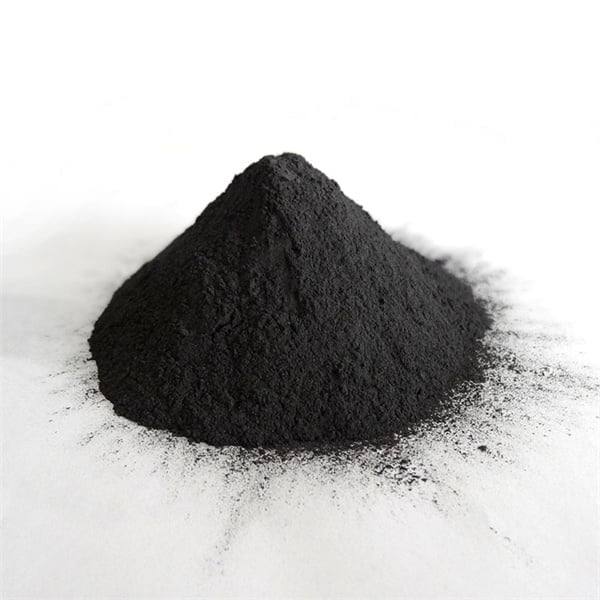
The Advantages of Metal Injection Molding (MIM)
MIM offers a compelling set of advantages that make it a highly sought-after process for various industries:
- Complex Geometries: Unlike traditional machining techniques that can struggle with intricate shapes, MIM excels at producing components with complex features, tight tolerances, and thin walls. This opens doors for innovative designs that were previously difficult or impossible to achieve with conventional methods.
- High Precision and Repeatability: MIM leverages the precision of injection molding, resulting in highly consistent parts with minimal dimensional variations. This translates to reliable performance and reduced post-processing needs.
- Mass Production: MIM is a well-suited process for high-volume production runs. Once the mold is set up, MIM can churn out a large number of identical parts efficiently, making it ideal for applications requiring consistent quality and large quantities.
- Material Versatility: MIM boasts a wide range of compatible materials, from common stainless steels and tool steels to exotic options like titanium and inconel. This allows for selection of the optimal material based on the specific strength, corrosion resistance, or other performance requirements of the application.
- Cost-Effectiveness: Compared to traditional machining techniques, especially for complex geometries, MIM can offer significant cost savings. The near-net-shape capability minimizes material waste and reduces the need for extensive machining operations.
Applications of Metal Injection Molding (MIM)
The diverse advantages of MIM have made it a popular choice across a wide spectrum of industries. Here are some prominent examples:
- Automotive: MIM shines in the automotive industry, producing intricate components like gears, sprockets, valve components, and fuel system parts known for their durability and dimensional accuracy.
- Medical Devices: The biocompatible nature of certain MIM materials makes it perfect for medical applications. MIM is used to create intricate surgical instruments, implants, and components for various medical devices.
- Consumer Electronics: The ability to produce small, complex parts with high precision makes MIM ideal for the consumer electronics industry. MIM finds applications in connectors, housings, and internal components for various electronic devices.
- Aerospace & Defense: The demanding requirements of the aerospace and defense sectors are well-suited for MIM. MIM produces high-strength, lightweight components for aircraft, spacecraft, and weapon systems.
Beyond the Benefits: Considerations for MIM
While MIM offers a plethora of advantages, it’s essential to consider some factors before choosing it for your specific application:
- Part Size Limitations: MIM currently has limitations on the maximum size of parts it can produce. Parts exceeding a certain volume might be better suited for traditional metalworking techniques.
- Material Limitations: Although MIM offers a wide range of materials, some exotic or specialty alloys might not be readily available or cost-effective through MIM.
- Development Costs: Setting up the MIM process for a new component requires upfront investment in mold development and process optimization. This cost factor needs to be weighed against the potential production volume and long-term benefits.
Understanding MIM: A Technical Deep Dive
For those interested in the technical intricacies of MIM, here’s a closer look at some key aspects:
Feedstock Selection: The selection of the right feedstock is crucial for successful MIM. Here are some key aspects to consider:
- Metal Powder:
- Particle Size and Distribution: The size and distribution of the metal powder significantly impact the final part properties. Finer powders generally enable tighter tolerances and smoother finishes, but they can also be more challenging to process due to flowability issues. A well-balanced particle size distribution is often preferred.
- Powder Morphology: The shape of the metal particles also plays a role. Spherical powders tend to flow better and pack more densely, leading to improved strength and dimensional accuracy.
- Binder System: The binder system acts as a temporary glue, holding the metal powder together during molding and debinding. Different binder systems offer varying characteristics, such as thermal stability, debinding behavior, and compatibility with the chosen debinding process.
Mold Design for MIM:
MIM molds share similarities with plastic injection molding molds but require specific considerations for the metal powder behavior:
- Gate Design: The design of the gates, which are the entry points for the feedstock into the mold cavity, needs to ensure proper flow and minimize turbulence that can lead to defects.
- Venting: Venting channels are crucial for allowing trapped air to escape during injection, preventing voids and ensuring complete part filling.
- Draft Angles: Draft angles on the mold walls are essential to facilitate the easy removal of the molded part after cooling.
Debinding Techniques in MIM:
As mentioned earlier, debinding is the critical step of removing the binder from the molded part. Here’s a breakdown of the two primary debinding techniques:
- Thermal Debinding: This method involves gradually heating the molded part in a controlled atmosphere. As the temperature rises, the binder degrades and decomposes, leaving behind the metal powder structure. The heating profile needs to be carefully designed to ensure complete binder removal without damaging the delicate metal structure.
- Solvent Debinding: This technique utilizes a solvent that selectively dissolves the binder system. The molded part is submerged in the solvent, allowing the binder to leach out while the metal powder remains intact. Solvent debinding can be faster than thermal debinding but might require special handling and disposal considerations for the used solvent.
Sintering in MIM:
Sintering is the final stage of the MIM process, where the debindered metal powder transforms into a solid, functional component. During sintering, the part is exposed to high temperatures (typically in the range of 1/2 to 2/3 of the melting point of the metal) in a controlled atmosphere. This high temperature promotes diffusion bonding between the metal particles, resulting in densification and significant improvement in strength and other mechanical properties.
Quality Control in MIM:
Maintaining consistent quality is paramount in MIM production. Here are some essential quality control measures:
- Feedstock Characterization: Regular testing of the feedstock’s properties, such as metal powder size distribution and binder content, ensures consistent material behavior during processing.
- Dimensional Inspection: The dimensions of the molded parts are meticulously inspected to ensure they meet the design specifications and maintain tight tolerances.
- Density Measurement: The density of the sintered parts is a critical indicator of their strength and performance. Various techniques, such as Archimedes’ principle or pycnometry, can be used to measure density.
- Microstructure Analysis: Microscopic examination of the sintered part’s microstructure reveals information about grain size, porosity, and potential defects.
The Future of Metal Injection Molding
MIM is a continuously evolving technology with ongoing research and development efforts focused on:
- Expanding Material Range: The exploration of new materials and binder systems compatible with MIM broadens the application possibilities for this versatile process.
- Improved Process Efficiency: Research aims to optimize the debinding and sintering stages to reduce cycle times and enhance overall production efficiency.
- Advanced Part Complexity: Developments in mold design and material science are pushing the boundaries of achievable part complexity through MIM.
Metal Injection Molding offers a unique blend of design freedom, material versatility, and cost-effectiveness for a wide range of industries. As the technology continues to mature, we can expect even more innovative applications and advancements in the exciting world of MIM.
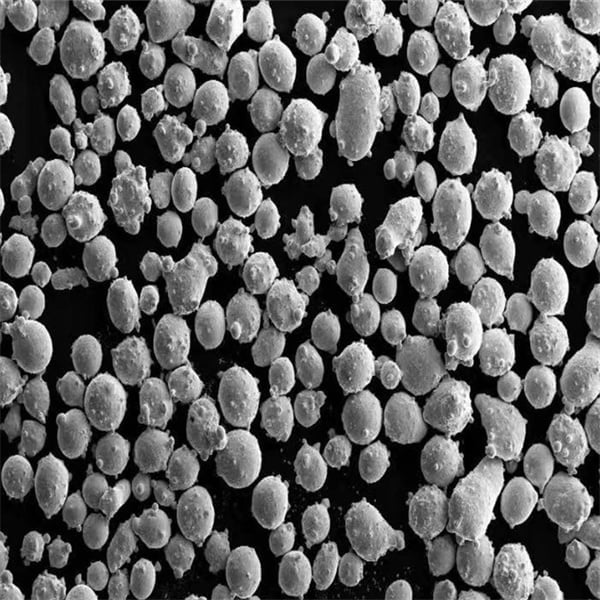
FAQ
Table 1: Frequently Asked Questions on Metal Injection Molding (MIM)
Question | Answer |
---|---|
What are the typical size limitations for MIM parts? | The maximum size of MIM parts is generally limited to a few cubic inches. This limitation is due to challenges with feedstock flow and ensuring uniform debinding in larger parts. |
Can MIM be used for prototyping? | Yes, MIM can be a viable option for prototyping complex metal parts, especially when a high degree of accuracy and fidelity to the final design is required. However, the upfront cost of mold development needs to be considered. |
What are the advantages of MIM compared to traditional machining? | MIM offers several advantages over traditional machining, including: Ability to produce complex geometries with tight tolerances Greater design freedom for intricate features High precision and repeatability for consistent parts Mass production efficiency for large quantities Reduced material waste compared to subtractive techniques |
What are the disadvantages of MIM compared to traditional machining? | There are also some limitations to consider with MIM: Part size limitations compared to techniques like casting or forging Material limitations for certain exotic or specialty alloys Higher upfront costs due to mold development Surface finish might not match exceptionally smooth finishes achievable through polishing or grinding |
What are some factors to consider when choosing between MIM and traditional metalworking? | The ideal choice depends on your specific application. Here are some key factors to weigh: Part geometry complexity Production volume requirements Material selection needs Cost considerations including upfront investment and potential savings Surface finish requirements |
What are some future trends in MIM technology? | Research and development efforts in MIM are focused on expanding the material range, improving process efficiency for faster cycle times, and pushing the boundaries of achievable part complexity. |
What are some typical applications of MIM? | MIM finds applications in a diverse range of industries, including: Automotive (gears, sprockets, valve components) Medical devices (surgical instruments, implants) Consumer electronics (connectors, housings) Aerospace & Defense (high-strength, lightweight components) |
What are the different types of feedstock used in MIM? | MIM feedstock typically consists of a metal powder (e.g., stainless steel, steel alloys, titanium) mixed with a polymeric binder system. The specific type of metal powder and binder will depend on the desired final properties of the part. |
What are the different debinding techniques used in MIM? | There are two primary debinding techniques: Thermal debinding: Gradual heating to remove the binder. Solvent debinding: Using a solvent to selectively dissolve the binder. |
Choosing the Right Process: MIM vs. Traditional Metalworking
The decision between MIM and traditional metalworking techniques depends on various factors specific to your application. Here are some key considerations to guide your choice:
- Part Geometry: If your component has complex features, tight tolerances, and intricate details, MIM offers a significant advantage.
- Production Volume: For high-volume production runs, MIM’s efficiency and repeatability make it a compelling option.
- Material Selection: Ensure the material you require is compatible with MIM. If you need an exotic alloy not readily available in MIM, traditional metalworking might be the way to go.
- Cost Considerations: Factor in the upfront costs of mold development for MIM versus the potential material waste and longer production times of traditional techniques for complex parts.
- Surface Finish Requirements: If a flawless surface finish is paramount, traditional techniques like polishing might be necessary.
Conclusion
Metal Injection Molding (MIM) stands as a powerful and versatile manufacturing process, offering a unique combination of design freedom, material options, and cost-effectiveness for a wide range of applications. By understanding its advantages, limitations, and how it compares to traditional metalworking techniques, you can make informed decisions to leverage MIM for your specific needs and unlock the potential for innovative and high-performance metal components.
Share On
MET3DP Technology Co., LTD is a leading provider of additive manufacturing solutions headquartered in Qingdao, China. Our company specializes in 3D printing equipment and high-performance metal powders for industrial applications.
Inquiry to get best price and customized Solution for your business!
Related Articles
About Met3DP
Recent Update
Our Product
CONTACT US
Any questions? Send us message now! We’ll serve your request with a whole team after receiving your message.
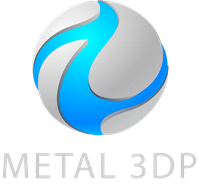
Metal Powders for 3D Printing and Additive Manufacturing