Metal Injection Molding
Table of Contents
Overview of Metal Injection Molding
Metal Injection Molding (MIM) is a transformative manufacturing process that merges the versatility of plastic injection molding with the strength and integrity of powdered metallurgy. It allows for the production of complex metal parts with high precision, excellent surface finish, and fine details. Essentially, MIM enables the creation of metal components that are too intricate or costly to produce through traditional methods.
This article dives deep into the world of Metal Injection Molding, exploring its intricacies, applications, advantages, and more. Whether you’re a seasoned engineer or a curious newcomer, this guide will provide valuable insights into MIM’s remarkable capabilities.
What is Metal Injection Molding?
At its core, Metal Injection Molding involves mixing fine metal powders with a binder material to create a feedstock that is then injected into a mold. The molded part undergoes a series of debinding and sintering processes to remove the binder and densify the metal, resulting in a final product that is nearly 100% dense and exhibits excellent mechanical properties.
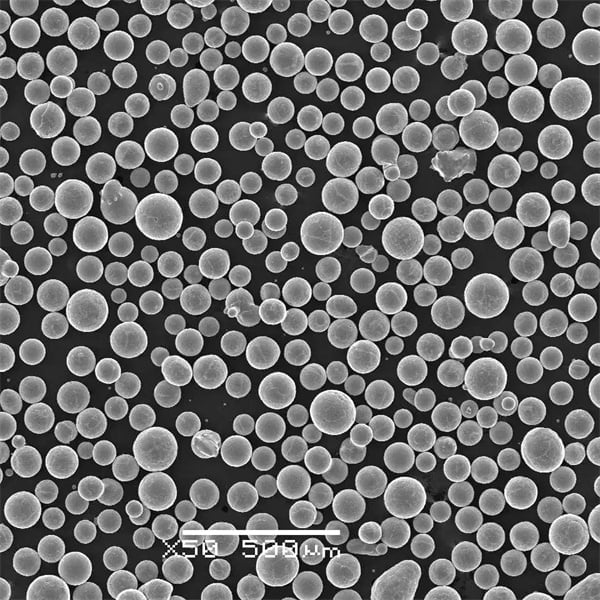
The Metal Injection Molding Process
The MIM process consists of several key steps:
- Feedstock Preparation: Fine metal powders are mixed with a thermoplastic binder to form a homogeneous mixture.
- Injection Molding: The feedstock is heated and injected into a mold to form the desired shape.
- Debinding: The binder is removed from the molded part, typically through a solvent or thermal process.
- Sintering: The debound part is heated in a controlled atmosphere to fuse the metal particles, achieving the final density and strength.
Types of Metal Powders Used in MIM
A variety of metal powders can be used in MIM, each offering unique properties and advantages. Here are ten specific metal powders commonly employed in the process:
- Stainless Steel 316L: Known for its corrosion resistance and high strength, making it ideal for medical and food industry applications.
- Stainless Steel 17-4PH: Offers excellent mechanical properties and can be heat-treated to improve hardness and strength.
- Carbonyl Iron Powder: Used for its high purity and excellent magnetic properties.
- Nickel Alloy 718: Provides high strength and resistance to extreme temperatures and corrosion.
- Titanium Ti-6Al-4V: Lightweight and biocompatible, commonly used in aerospace and medical implants.
- Copper C11000: Highly conductive and used in electrical and thermal applications.
- Inconel 625: Exhibits excellent oxidation and corrosion resistance, suitable for high-temperature applications.
- Molybdenum TZM: High-temperature strength and creep resistance, used in aerospace and defense.
- Cobalt-Chrome Alloy: High wear resistance and biocompatibility, often used in dental and orthopedic implants.
- Tool Steel M2: High hardness and wear resistance, ideal for cutting tools and dies.
Properties of Common Metal Powders
Metal Powder | Composition | Properties | Applications |
---|---|---|---|
Stainless Steel 316L | Fe, Cr, Ni, Mo | Corrosion resistance, high strength | Medical devices, food processing |
Stainless Steel 17-4PH | Fe, Cr, Ni, Cu | Heat-treatable, high strength | Aerospace, automotive |
Carbonyl Iron Powder | Pure Iron | High purity, magnetic properties | Electronics, automotive |
Nickel Alloy 718 | Ni, Cr, Fe, Nb, Mo, Ti, Al | High strength, corrosion resistance | Aerospace, oil & gas |
Titanium Ti-6Al-4V | Ti, Al, V | Lightweight, biocompatible | Medical implants, aerospace |
Copper C11000 | Pure Copper | High conductivity | Electrical components, thermal systems |
Inconel 625 | Ni, Cr, Mo, Nb | Oxidation resistance, strength | High-temperature applications |
Molybdenum TZM | Mo, Ti, Zr | High-temperature strength | Aerospace, defense |
Cobalt-Chrome Alloy | Co, Cr, Mo | Wear resistance, biocompatibility | Dental, orthopedic implants |
Tool Steel M2 | Fe, Mo, W, Cr, V | High hardness, wear resistance | Cutting tools, dies |
Applications of Metal Injection Molding
MIM finds applications across various industries due to its ability to produce complex and high-precision parts. Here are some notable applications:
Industry | Applications |
---|---|
Aerospace | Turbine blades, fuel nozzles, structural components |
Medical | Surgical instruments, dental implants, orthodontic brackets |
Automotive | Engine components, fuel injectors, transmission parts |
Consumer Electronics | Connectors, heat sinks, mobile device components |
Defense | Firearm components, missile parts, communication devices |
Industrial Equipment | Gears, valves, fasteners, precision tools |
Jewelry | Watch cases, clasps, ornamental components |
Energy | Heat exchangers, drilling equipment, power generation parts |
Specifications and Standards for Metal Injection Molding
When selecting metal powders for MIM, various specifications and standards are considered to ensure quality and performance. Here’s a look at some common standards:
Metal Powder | Specifications | Standards |
---|---|---|
Stainless Steel 316L | ASTM A276, ASTM F138 | ISO 5832-1 |
Stainless Steel 17-4PH | ASTM A564, AMS 5643 | ISO 15156-3 |
Carbonyl Iron Powder | ASTM A131, ASTM B311 | MIL-I-16923 |
Nickel Alloy 718 | ASTM B637, AMS 5662 | ISO 15156-3 |
Titanium Ti-6Al-4V | ASTM B348, ASTM F1472 | ISO 5832-3 |
Copper C11000 | ASTM B152, ASTM F68 | ISO 1336 |
Inconel 625 | ASTM B446, AMS 5666 | ISO 15156-3 |
Molybdenum TZM | ASTM B387, ASTM F289 | MIL-M-14075 |
Cobalt-Chrome Alloy | ASTM F75, ASTM F1537 | ISO 5832-4 |
Tool Steel M2 | ASTM A600, AMS 6431 | ISO 4957 |
Advantages of Metal Injection Molding
Metal Injection Molding offers several significant advantages compared to traditional manufacturing processes:
- Complex Geometries: MIM can produce intricate shapes that would be difficult or impossible to achieve with other methods.
- Material Efficiency: The process minimizes material waste, as excess feedstock can often be reused.
- High Precision: MIM parts are manufactured to tight tolerances, reducing the need for secondary machining.
- Cost-Effective: For large production runs, MIM can be more economical than machining or casting.
- Excellent Mechanical Properties: MIM parts exhibit high strength, density, and durability.
- Wide Material Range: A broad spectrum of metal powders can be used, providing versatility in application.
Disadvantages of Metal Injection Molding
Despite its benefits, MIM also has some limitations:
- Initial Costs: The tooling and feedstock preparation can be expensive for small production runs.
- Size Limitations: MIM is typically suited for smaller parts, usually weighing less than 100 grams.
- Debinding Challenges: The debinding process can be time-consuming and requires careful control to avoid defects.
- Complexity in Sintering: Achieving uniform sintering without distortion or shrinkage can be challenging.
- Material Restrictions: Not all metals are suitable for MIM, particularly those with high melting points.
Comparison of Metal Injection Molding with Other Manufacturing Methods
Parameter | MIM | Machining | Casting | Powder Metallurgy |
---|---|---|---|---|
Complexity | High complexity, intricate shapes | Limited by tool accessibility | Moderate complexity | Moderate complexity |
Material Efficiency | High, low waste | High waste | Moderate waste | Low waste |
Precision | High precision, tight tolerances | High precision, but costly | Lower precision | Moderate precision |
Cost for Large Runs | Cost-effective | Expensive | Cost-effective | Cost-effective |
Initial Tooling Cost | High | Low to moderate | High | Moderate |
Suitable Part Size | Small to medium | Any size | Large to very large | Small to medium |
Mechanical Properties | Excellent | Excellent | Good | Good to excellent |
Suppliers and Pricing of Metal Powders for MIM
Finding the right supplier for MIM powders is crucial for ensuring quality and cost-effectiveness. Here’s a look at some key suppliers and approximate pricing details:
Supplier | Metal Powders | Pricing (per kg) | Notes |
---|---|---|---|
**Sandvik Osprey | Stainless Steel, Nickel Alloys | $50 – $200 | High-quality powders, wide range |
Höganäs AB | Iron, Stainless Steel, Titanium | $30 – $150 | Leading supplier, consistent quality |
Carpenter Technology | Tool Steels, Titanium, Inconel | $100 – $300 | Premium powders, extensive options |
Advanced Powder Products | Custom Alloys, Stainless Steels | $40 – $180 | Specializes in custom solutions |
Epson Atmix | Fine Stainless Steel, Magnetic Powders | $50 – $220 | High-purity, fine powders |
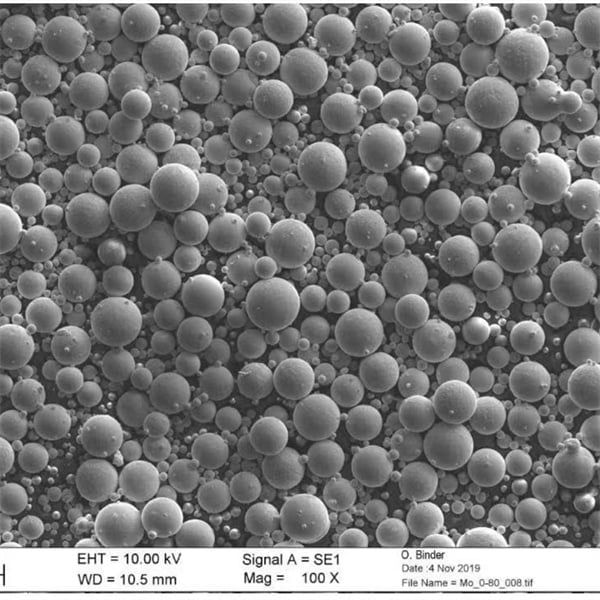
Pros and Cons of Metal Injection Molding
Understanding the pros and cons of MIM helps in making informed decisions regarding its implementation:
Pros | Cons |
---|---|
Produces complex, high-precision parts | High initial tooling and feedstock costs |
Efficient use of materials | Limited to smaller part sizes |
Suitable for large production runs | Debinding and sintering processes are delicate |
Wide range of materials available | Not all metals are suitable for MIM |
Excellent mechanical properties | Uniform sintering can be challenging |
FAQ
Question | Answer |
---|---|
What is Metal Injection Molding (MIM)? | MIM is a manufacturing process that combines metal powders with a binder to create intricate metal parts. |
What types of metals can be used in MIM? | Various metals including stainless steels, nickel alloys, titanium, and more. |
What are the advantages of MIM? | High complexity, material efficiency, precision, and excellent mechanical properties. |
What are the disadvantages of MIM? | High initial costs, size limitations, debinding challenges, and complexity in sintering. |
Which industries use MIM parts? | Aerospace, medical, automotive, consumer electronics, defense, and more. |
How does MIM compare to other methods? | MIM offers higher complexity and material efficiency but can be more costly initially and has size limitations. |
What is the typical part size for MIM? | Usually smaller than 100 grams. |
Are there any restrictions on MIM materials? | Yes, metals with very high melting points or unsuitable sintering characteristics are not ideal for MIM. |
How are MIM parts processed after molding? | Parts undergo debinding to remove the binder and sintering to densify the metal. |
What is the cost of metal powders for MIM? | Costs vary, typically ranging from $30 to $300 per kilogram depending on the metal and supplier. |
Conclusion
Metal Injection Molding is a powerful manufacturing process that offers unique advantages in producing complex, high-precision metal parts. By understanding its nuances, applications, and the various metal powders available, manufacturers can leverage MIM to achieve superior results in a cost-effective manner. Whether for aerospace, medical, automotive, or other industries, MIM continues to push the boundaries of what’s possible in metal part production.
Share On
MET3DP Technology Co., LTD is a leading provider of additive manufacturing solutions headquartered in Qingdao, China. Our company specializes in 3D printing equipment and high-performance metal powders for industrial applications.
Inquiry to get best price and customized Solution for your business!
Related Articles
About Met3DP
Recent Update
Our Product
CONTACT US
Any questions? Send us message now! We’ll serve your request with a whole team after receiving your message.
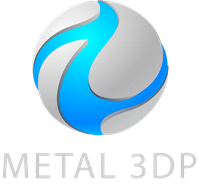
Metal Powders for 3D Printing and Additive Manufacturing