Metal Injection Moulding
Table of Contents
Welcome to our comprehensive guide on Metal Injection Moulding (MIM). If you’ve ever wondered how intricate metal parts are manufactured with high precision and efficiency, you’re in the right place. We’re about to dive deep into the world of MIM, exploring its nuances, advantages, applications, and much more. Let’s get started!
Overview of Metal Injection Moulding
Metal Injection Moulding (MIM) is a manufacturing process that combines the versatility of plastic injection moulding with the strength and integrity of powdered metallurgy. This technology allows for the mass production of complex metal parts with high precision, making it a go-to method for industries ranging from automotive to medical devices.
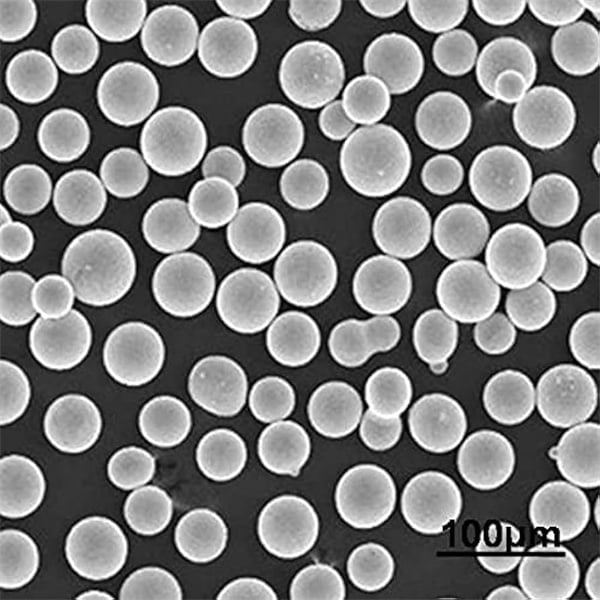
Types, Composition, Properties, and Characteristics of Metal Powders
To better understand MIM, let’s first explore the different types of metal powders used in the process. Here’s a detailed table highlighting various metal powders, their compositions, properties, and characteristics:
Metal Powder | Composition | Properties | Characteristics |
---|---|---|---|
Stainless Steel 316L | Fe-Cr-Ni-Mo | High corrosion resistance, good mechanical properties | Commonly used in medical and food applications |
Titanium Alloy Ti-6Al-4V | Ti-Al-V | High strength-to-weight ratio, excellent corrosion resistance | Used in aerospace and medical implants |
Inconel 718 | Ni-Cr-Fe | High-temperature strength, oxidation resistance | Suitable for aerospace and gas turbine applications |
Carbonyl Iron Powder | Fe | High purity, good magnetic properties | Used in electronic and magnetic applications |
Cobalt-Chrome Alloy | Co-Cr | High wear resistance, biocompatibility | Ideal for dental and orthopedic implants |
Tool Steel M2 | Fe-Cr-Mo-V | High hardness, excellent wear resistance | Used in cutting tools and high-speed applications |
Copper | Cu | Excellent electrical and thermal conductivity | Utilized in electrical components and heat exchangers |
Nickel Alloy 625 | Ni-Cr-Mo-Nb | Outstanding fatigue and thermal-fatigue strength | Used in marine and nuclear applications |
Aluminum 6061 | Al-Mg-Si | Good mechanical properties, corrosion resistance | Common in automotive and consumer electronics |
Tungsten Carbide | WC | Extremely hard, high wear resistance | Suitable for cutting and drilling tools |
Applications of Metal Injection Moulding
Metal Injection Moulding is versatile and finds applications in a wide range of industries. Here’s a breakdown of where MIM is commonly used:
Industry | Applications |
---|---|
Automotive | Fuel injectors, turbocharger parts, gears |
Medical | Surgical instruments, orthopedic implants, dental implants |
Aerospace | Engine components, fasteners, brackets |
Consumer Electronics | Connectors, phone components, small mechanical parts |
Industrial | Tools, machinery parts, filtration components |
Defense | Firearm components, tactical gear, ordinance |
Specifications, Sizes, Grades, and Standards
In MIM, adhering to specifications and standards is crucial for ensuring the quality and performance of the final products. Here are some typical specifications and standards followed in MIM:
Parameter | Details |
---|---|
Part Size Range | Typically 0.1 to 100 grams |
Tolerance | ±0.5% of dimension |
Density | Up to 98% of wrought material density |
Surface Finish | As low as 1 micron Ra |
ISO Standards | ISO 22068:2020 (Metal Injection Moulding) |
ASTM Standards | ASTM B883-12 (Standard Specification for Metal Injection Molded Parts) |
Suppliers and Pricing Details
Choosing the right supplier and understanding pricing is critical for any manufacturing process. Here’s a table summarizing some leading MIM suppliers and typical pricing details:
Supplier | Location | Specialty | Typical Pricing |
---|---|---|---|
Indo-MIM | India | High-volume, automotive, medical | $10 – $100 per part |
ARC Group Worldwide | USA | Aerospace, defense, medical | $15 – $150 per part |
Smith Metal Products | USA | Small to medium-sized parts, various alloys | $20 – $200 per part |
Advanced Forming Technology | USA | Complex shapes, high precision | $25 – $250 per part |
Parmaco Metal Injection Molding AG | Switzerland | Precision components, high quality | $30 – $300 per part |
Advantages and Disadvantages of Metal Injection Moulding
Understanding the pros and cons of MIM can help in making informed decisions. Here’s a detailed comparison:
Advantages | Disadvantages |
---|---|
Produces complex shapes with high precision | Higher initial tooling costs |
High production rates suitable for mass production | Limited to smaller part sizes |
Excellent material properties (strength, durability) | Requires careful control of material properties |
Reduces machining and finishing operations | Longer lead times for tooling development |
Allows for intricate geometries not possible with other methods | Higher cost for low-volume production |
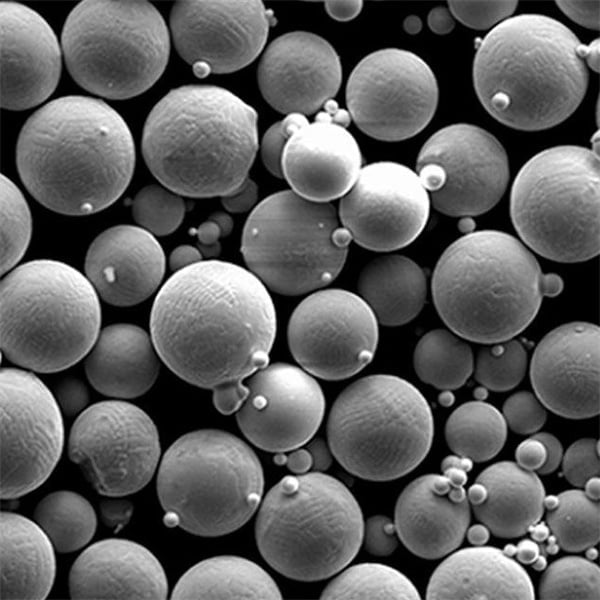
FAQ
To wrap up, let’s address some common questions about Metal Injection Moulding:
Question | Answer |
---|---|
What is Metal Injection Moulding? | MIM is a process combining plastic injection moulding with powdered metallurgy to produce intricate metal parts. |
What materials can be used in MIM? | Various metal powders like stainless steel, titanium, and nickel alloys. |
What are the main advantages of MIM? | High precision, complex shapes, high production rates, excellent material properties. |
What industries use MIM? | Automotive, medical, aerospace, electronics, industrial, and defense sectors. |
How does MIM compare to traditional manufacturing? | MIM offers higher precision and complexity, but with higher initial tooling costs. |
What are typical tolerances achievable with MIM? | Generally, tolerances are around ±0.5% of the dimension. |
Is MIM suitable for high-volume production? | Yes, it is highly suitable for mass production due to its high production rates. |
Conclusion
Metal Injection Moulding is a transformative manufacturing technology that bridges the gap between plastic injection moulding and metal parts production. Its ability to produce complex, high-precision components makes it invaluable across various industries. While it does come with higher initial costs and some limitations, the benefits often outweigh these drawbacks, especially for high-volume production.
Whether you’re in automotive, aerospace, medical, or any other industry requiring precise metal components, MIM could be the solution you need. We hope this guide has provided you with a comprehensive understanding of Metal Injection Moulding and its applications. If you have any more questions or need further information, feel free to reach out!
Share On
MET3DP Technology Co., LTD is a leading provider of additive manufacturing solutions headquartered in Qingdao, China. Our company specializes in 3D printing equipment and high-performance metal powders for industrial applications.
Inquiry to get best price and customized Solution for your business!
Related Articles
About Met3DP
Recent Update
Our Product
CONTACT US
Any questions? Send us message now! We’ll serve your request with a whole team after receiving your message.
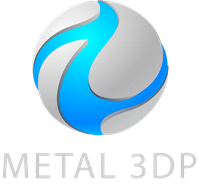
Metal Powders for 3D Printing and Additive Manufacturing
COMPANY
PRODUCT
cONTACT INFO
- Qingdao City, Shandong, China
- [email protected]
- [email protected]
- +86 19116340731