Metal Injection Moulding (MIM)
Table of Contents
Metal Injection Moulding (MIM) is a revolutionary manufacturing process that merges the design flexibility of plastic injection molding with the material strength and integrity of metal. This technique has opened new possibilities in various industries, making it easier to produce complex metal parts with precision and efficiency. Let’s dive into the intricacies of MIM, exploring its advantages, applications, specific metal powders used, and more.
Overview of Metal Injection Moulding (MIM)
Metal Injection Moulding (MIM) is a process that involves mixing metal powders with a binder material to create a feedstock, which is then injection molded into a desired shape. This molded part is then subjected to a series of debinding and sintering processes to remove the binder and fuse the metal particles into a solid, high-density component.
Key Steps in the MIM Process:
- Feedstock Preparation: Metal powders are blended with a binder to form a homogeneous feedstock.
- Injection Molding: The feedstock is injected into a mold to form the desired shape.
- Debinding: The binder is removed from the molded part through thermal or chemical processes.
- Sintering: The debound part is heated to a high temperature, causing the metal particles to fuse and form a dense, solid piece.
- Finishing: Additional processes such as machining, heat treatment, or surface finishing may be applied to achieve the final specifications.
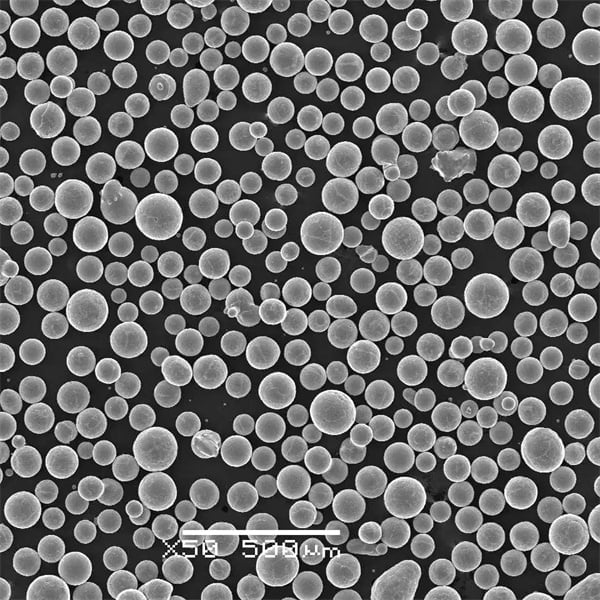
Types of Metal Powders Used in MIM
The choice of metal powder is crucial in MIM as it directly affects the properties and performance of the final product. Below are some commonly used metal powders in MIM, along with their descriptions:
Metal Powder | Description |
---|---|
316L Stainless Steel | Known for its excellent corrosion resistance and mechanical properties, suitable for medical and dental instruments. |
17-4 PH Stainless Steel | Offers high strength and corrosion resistance, ideal for aerospace and military applications. |
M2 High-Speed Steel | Provides excellent wear resistance and toughness, used in cutting tools and industrial applications. |
Titanium Alloy (Ti-6Al-4V) | Lightweight with high strength and corrosion resistance, commonly used in aerospace and medical implants. |
Copper | Excellent electrical and thermal conductivity, used in electrical components and heat exchangers. |
Inconel 718 | High-temperature strength and corrosion resistance, suitable for aerospace and gas turbine components. |
Cobalt-Chromium Alloy | Biocompatible and wear-resistant, used in dental and orthopedic implants. |
Nickel Alloy (NiCr) | Good oxidation resistance and high-temperature strength, used in turbine blades and industrial applications. |
Tungsten Heavy Alloy | High density and strength, used in radiation shielding and aerospace components. |
Aluminum Alloy (AlSi10Mg) | Lightweight with good mechanical properties, used in automotive and aerospace parts. |
Applications of Metal Injection Moulding (MIM)
MIM is used across a wide range of industries due to its ability to produce complex parts with high precision. Here are some of the key applications:
Industry | Applications |
---|---|
Medical | Surgical instruments, dental implants, orthopedic devices |
Automotive | Fuel injectors, turbocharger parts, gear components |
Aerospace | Engine components, fasteners, structural parts |
Consumer Electronics | Connectors, heat sinks, mobile phone parts |
Industrial | Cutting tools, valve components, fasteners |
Defense | Firearm components, ordnance parts, tactical equipment |
Advantages of Metal Injection Moulding (MIM)
Metal Injection Moulding offers several benefits over traditional manufacturing methods:
- Complex Geometries: MIM can produce intricate and complex shapes that are difficult or impossible to achieve with conventional methods.
- Material Utilization: The process has high material utilization, reducing waste and lowering costs.
- Superior Properties: MIM parts can achieve properties similar to wrought materials, including high density and strength.
- Cost-Effective for High Volumes: MIM is economical for producing large quantities of small to medium-sized parts.
- Versatility: A wide range of materials can be used in MIM, providing flexibility in design and application.
Disadvantages of Metal Injection Moulding (MIM)
Despite its advantages, MIM also has some limitations:
- Initial Costs: The initial setup costs for molds and equipment can be high.
- Size Limitations: MIM is typically limited to small and medium-sized parts.
- Binder Removal: The debinding process can be time-consuming and requires precise control.
- Material Restrictions: Not all materials are suitable for MIM, and some may require specific processing conditions.
Comparing Metal Injection Moulding (MIM) with Other Manufacturing Methods
To better understand the unique benefits of MIM, let’s compare it to other common manufacturing methods:
Aspect | MIM | Casting | Machining | Powder Metallurgy |
---|---|---|---|---|
Complexity | High | Medium | Low | Medium |
Material Waste | Low | High | High | Medium |
Tooling Cost | High | Low | Low | Medium |
Part Size | Small to Medium | Large | Small to Large | Small to Medium |
Surface Finish | Excellent | Good | Excellent | Good |
Mechanical Properties | Excellent | Good | Excellent | Good |
Specifications and Standards for MIM Materials
When selecting materials for MIM, it’s essential to consider the specifications and standards to ensure the desired performance and quality. Here are some common specifications for MIM materials:
Material | Standard | Grade | Density | Hardness | Tensile Strength |
---|---|---|---|---|---|
316L Stainless Steel | ASTM A276 | 316L | 7.9 g/cm³ | 150 HB | 485 MPa |
17-4 PH Stainless Steel | ASTM A564 | 17-4 PH | 7.7 g/cm³ | 350 HB | 1000 MPa |
M2 High-Speed Steel | ASTM A600 | M2 | 8.1 g/cm³ | 64 HRC | 4000 MPa |
Titanium Alloy (Ti-6Al-4V) | ASTM B348 | Grade 5 | 4.4 g/cm³ | 35 HRC | 900 MPa |
Copper | ASTM B152 | C11000 | 8.9 g/cm³ | 40 HB | 220 MPa |
Inconel 718 | ASTM B637 | N07718 | 8.2 g/cm³ | 40 HRC | 1241 MPa |
Cobalt-Chromium Alloy | ASTM F75 | CoCr | 8.3 g/cm³ | 36 HRC | 655 MPa |
Nickel Alloy (NiCr) | ASTM B160 | Ni201 | 8.9 g/cm³ | 80 HRB | 370 MPa |
Tungsten Heavy Alloy | ASTM B777 | WHA | 17.0 g/cm³ | 35 HRC | 950 MPa |
Aluminum Alloy (AlSi10Mg) | ASTM B85 | AlSi10Mg | 2.7 g/cm³ | 95 HB | 320 MPa |
Suppliers and Pricing for MIM Materials
Knowing where to source materials and understanding the cost implications is crucial for any manufacturing process. Here are some key suppliers and indicative pricing for MIM materials:
Supplier | Material | Price (per kg) | Location |
---|---|---|---|
Sandvik Osprey | 316L Stainless Steel | $30 | Global |
Carpenter Technology | 17-4 PH Stainless Steel | $40 | USA |
Höganäs | M2 High-Speed Steel | $50 | Global |
GKN Powder Metallurgy | Titanium Alloy (Ti-6Al-4V) | $200 | Global |
Kymera International | Copper | $10 | USA |
ATI Specialty Alloys | Inconel 718 | $120 | USA |
Arcam AB | Cobalt-Chromium Alloy | $150 | Europe |
Powder Alloy Corporation | Nickel Alloy (NiCr) | $50 | USA |
Global Tungsten & Powders | Tungsten Heavy Alloy | $80 | USA |
ECKA Granules | Aluminum Alloy (AlSi10Mg) | $20 | Europe |
Pros and Cons of Metal Injection Moulding (MIM)
Understanding the advantages and limitations of MIM helps in making informed decisions. Here’s a detailed comparison:
Aspect | Advantages | Limitations |
---|---|---|
Complexity | Can produce complex geometries | Limited to small to medium-sized parts |
Material Utilization | High material utilization, minimal waste | Not all materials are suitable |
Properties | High-density, superior mechanical properties | Debinding process can be time-consuming |
Cost | Cost-effective for high volumes | High initial tooling costs |
Versatility | Wide range of materials | Requires precise process control |
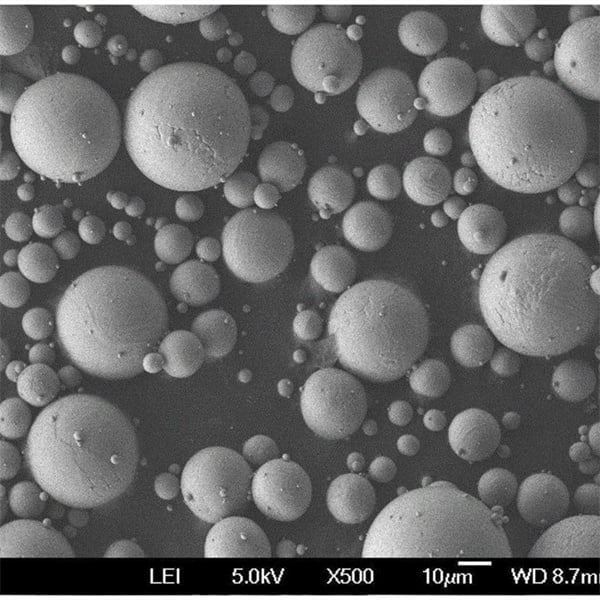
FAQs
What is Metal Injection Moulding (MIM)?
Metal Injection Moulding (MIM) is a manufacturing process that combines metal powders with a binder to create a feedstock, which is then injection molded, debound, and sintered to form high-density metal parts.
What are the key advantages of MIM?
MIM allows for the production of complex geometries, high material utilization, excellent mechanical properties, and is cost-effective for high volumes.
What materials can be used in MIM?
Materials such as stainless steels, high-speed steels, titanium alloys, copper, Inconel, cobalt-chromium alloys, nickel alloys, tungsten heavy alloys, and aluminum alloys can be used in MIM.
What industries benefit from MIM?
Industries such as medical, automotive, aerospace, consumer electronics, industrial, and defense benefit from MIM.
What are the limitations of MIM?
Limitations include high initial costs, size restrictions, time-consuming debinding processes, and material restrictions.
How does MIM compare to other manufacturing methods?
MIM offers higher complexity and better material utilization compared to casting and machining, with superior properties similar to wrought materials.
Who are the key suppliers of MIM materials?
Key suppliers include Sandvik Osprey, Carpenter Technology, Höganäs, GKN Powder Metallurgy, Kymera International, ATI Specialty Alloys, Arcam AB, Powder Alloy Corporation, Global Tungsten & Powders, and ECKA Granules.
What are the typical applications of MIM?
Typical applications include surgical instruments, fuel injectors, engine components, connectors, cutting tools, and firearm components.
What are the typical specifications for MIM materials?
Specifications include standards such as ASTM, with considerations for density, hardness, and tensile strength, depending on the material.
Is MIM environmentally friendly?
MIM is considered environmentally friendly due to high material utilization and minimal waste generation.
What is the future outlook for MIM?
The future outlook for MIM is promising, with advancements in materials and processes expected to expand its applications and efficiency further.
Conclusion
Metal Injection Moulding (MIM) is a versatile and efficient manufacturing process that bridges the gap between plastic injection molding and traditional metalworking. Its ability to produce complex parts with high precision and excellent mechanical properties makes it a preferred choice for various industries. By understanding the materials, applications, advantages, and limitations of MIM, manufacturers can make informed decisions to leverage this technology for their specific needs.
Share On
MET3DP Technology Co., LTD is a leading provider of additive manufacturing solutions headquartered in Qingdao, China. Our company specializes in 3D printing equipment and high-performance metal powders for industrial applications.
Inquiry to get best price and customized Solution for your business!
Related Articles
About Met3DP
Recent Update
Our Product
CONTACT US
Any questions? Send us message now! We’ll serve your request with a whole team after receiving your message.
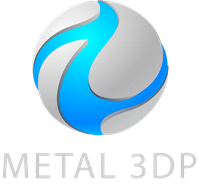
Metal Powders for 3D Printing and Additive Manufacturing