metal jet machine: application in 3D Printing
Table of Contents
The world of manufacturing is undergoing a significant transformation, driven by advancements in 3D printing technologies. Among these advancements, metal jetting stands out as a revolutionary force, capable of producing complex, high-quality metal parts with unmatched speed and precision. But what exactly is a metal jet machine, and how does it work? Buckle up, because we’re about to delve into the fascinating realm of metal additive manufacturing!
The Working Principle of a Metal Jet Machine
Imagine a sophisticated inkjet printer that, instead of colored ink cartridges, utilizes a powerful arsenal of metal-laden droplets. This, in essence, is the core concept behind a metal jet machine. Here’s a breakdown of the process:
- Digital Blueprint: The journey begins with a 3D computer-aided design (CAD) model of the desired metal part. This intricate digital blueprint serves as the roadmap for the printing process.
- Powder Bed Preparation: A fine layer of metal powder, typically consisting of materials like titanium, stainless steel, or even precious metals like gold, is meticulously spread across a platform within the machine.
- Jetting the Binders: Multiple printheads, similar to those found in inkjet printers, traverse the platform. But instead of ink, these heads strategically jet a binding agent onto the metal powder, selectively gluing particles together according to the CAD design.
- Layer by Layer Creation: Once a single layer is complete, the platform lowers slightly, and a fresh layer of metal powder is deposited. The binding agent jets continue their meticulous dance, building the part layer by layer until the entire design is brought to life.
- Post-Processing: The printed part, still encased in a network of binding material, is carefully removed from the machine. This “green” part then undergoes a debinding process, where the temporary binders are removed through thermal or chemical means. Finally, the part is sintered, a high-temperature treatment that fuses the metal particles together, resulting in a robust, near-net-shape metal component.
Think of it like building a sandcastle on the beach, but with layers of metal powder instead of sand, and a high-tech glue dispenser instead of your wet hands.
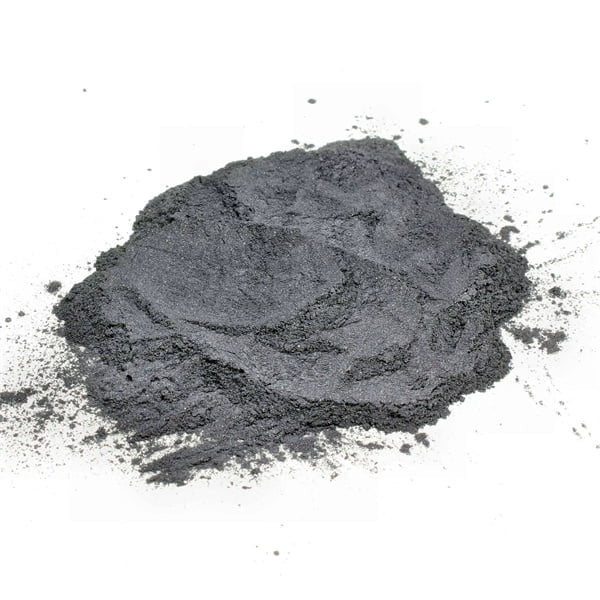
Advantages of Metal Jetting
Metal jetting boasts a compelling set of advantages that make it a highly attractive option for various manufacturing applications:
- Unmatched Speed: Compared to traditional metal fabrication techniques like machining or casting, metal jetting offers significantly faster production times. This allows for quicker product development cycles, faster prototyping, and reduced time-to-market for new products.
- Design Freedom Unleashed: Metal jetting excels at producing intricate and complex geometries that would be incredibly challenging, or even impossible, to achieve with conventional methods. Imagine internal channels, lattice structures, and other lightweight yet strong designs – metal jetting makes them a reality.
- Economical for Small Batch Production: Unlike some metal additive manufacturing processes that require significant upfront investments, metal jetting can be cost-effective for producing small batches of parts. This makes it ideal for prototyping, low-volume production runs, and customized components.
- Material Versatility: Metal jetting machines are capable of working with a wide range of metal powders, opening doors to a vast array of material properties and functionalities. From lightweight aluminum to high-strength steels and even exotic materials like Inconel, the choice of metal caters to diverse application needs.
- High-Quality Parts: Metal jetting produces parts with exceptional dimensional accuracy and surface finish. This reduces the need for extensive post-processing steps, leading to faster turnaround times and improved overall production efficiency. Imagine a metal part coming straight out of the machine, ready for use with minimal finishing touches, that’s the beauty of metal jetting.
Metal jetting is like having a manufacturing superpower – it’s fast, versatile, and delivers high-quality results that push the boundaries of design.
Disadvantages of Metal Jetting
While metal jetting offers a plethora of benefits, it’s essential to acknowledge its limitations:
- Limited Part Size: Compared to some other 3D printing technologies, metal jetting machines currently have limitations on the maximum build size for parts. This might not be suitable for large-scale industrial applications.
- Material Property Optimization: The sintering process used in metal jetting can sometimes result in material properties that are slightly different from those of traditionally manufactured metals. However, ongoing research and development are continuously improving material properties achievable through metal jetting.
- Support Structure Considerations: Similar to other 3D printing processes, metal jetting often necessitates the use of support structures during printing. These temporary structures are necessary to prevent overhangs from collapsing, but their removal can add complexity to the post-processing stage and potentially leave behind blemishes on the final part.
- Cost Considerations for Large Volumes: While cost-effective for small batches, metal jetting can become expensive for high-volume production runs. The cost of metal powders and the overall printing process can add up for larger quantities.
Metal jetting, like any powerful tool, requires careful consideration of its limitations to ensure it’s the right fit for the application.
Applications of metal jet machine
The potential applications of metal jetting are vast and constantly expanding. Here are some prominent examples of how this technology is revolutionizing various industries:
- Aerospace: Metal jetting is a game-changer for the aerospace industry. Its ability to produce lightweight, high-strength components with complex geometries is ideal for aircraft parts, rocket engine components, and even spacecraft heat shields. Imagine reducing the weight of an aircraft engine by using a metal jetted lattice structure – that translates to better fuel efficiency and increased range.
- Medical Devices: Metal jetting is making significant strides in the medical field. From customized implants for hip and knee replacements to intricate dental prosthetics, this technology is enabling the creation of biocompatible metal parts that perfectly fit individual patient needs. Imagine a custom-made prosthetic that seamlessly integrates with a patient’s bone structure – that’ the level of personalization metal jetting can bring to medical devices.
- Automotive: The automotive industry is also embracing metal jetting for various applications. From lightweight components for electric vehicles to intricate parts for fuel injection systems, this technology is helping to create more efficient and innovative vehicles. Imagine a lighter car body structure that maintains strength, thanks to metal jetted components – that’s the contribution metal jetting can make to fuel efficiency.
- Consumer Goods: Metal jetting is finding its way into the consumer goods market as well. From customized jewelry pieces to high-performance sports equipment components, this technology is enabling the creation of unique and functional products. Imagine a pair of custom-made sunglasses with intricate metal frames, produced using metal jetting – that’s the level of personalization possible.
The applications of metal jetting are truly limited only by our imagination. As the technology continues to evolve, we can expect to see even more innovative and groundbreaking uses emerge in the years to come.
Metal Jetting vs Other Metal Additive Manufacturing Processes
Metal jetting isn’t the only player in the metal additive manufacturing game. Let’s compare it to two other prominent technologies:
- Metal Laser Sintering (MLS):
- Similarities: Both MLS and metal jetting utilize a layer-by-layer approach to build metal parts from powder. They also offer high-quality results and design freedom.
- Differences: MLS uses a laser to selectively melt the metal powder, while metal jetting employs a binding agent. MLS can produce parts with a wider range of mechanical properties, but metal jetting generally offers faster printing speeds.
- Electron Beam Melting (EBM):
- Similarities: Both EBM and metal jetting can create complex geometries and work with a variety of metal powders.
- Differences: EBM uses a high-powered electron beam to melt the metal powder in a vacuum chamber. This results in parts with excellent mechanical properties, but EBM machines are typically more expensive and have a larger environmental footprint compared to metal jetting systems.
Choosing between metal jetting, MLS, and EBM depends on the specific needs of the application. Factors like desired material properties, build size requirements, and budget constraints all play a crucial role in the decision-making process.
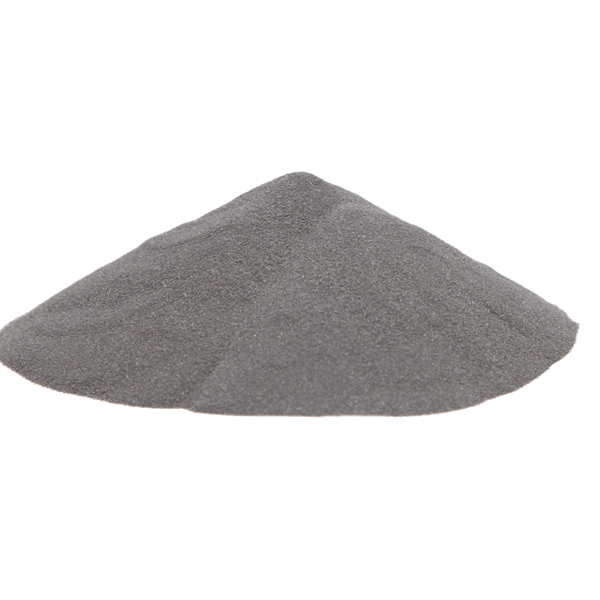
FAQ
1. What are the typical materials used in metal jetting?
Metal jetting can work with a wide range of metal powders, including:
- Stainless Steel (various grades)
- Titanium Alloys
- Inconel (superalloys)
- Aluminum Alloys
- Precious Metals (gold, silver)
2. What are the surface finishes achievable with metal jetting?
Metal jetting can produce parts with good surface finishes, ranging from slightly rough to smooth depending on the material and post-processing techniques used.
3. How strong are metal jetted parts?
The strength of metal jetted parts depends on the chosen material and the sintering process parameters. However, metal jetting can produce parts with excellent mechanical properties that are comparable to traditionally manufactured metals.
4. Is metal jetting safe?
Metal jetting, like any industrial process, requires adherence to safety protocols. The fine metal powders used can pose inhalation risks, so proper ventilation systems and personal protective equipment are essential during operation. Additionally, the high-pressure binding agents and sintering processes necessitate following safety guidelines established by the machine manufacturer.
5. What is the future of metal jetting?
The future of metal jetting is incredibly bright. Here are some exciting trends to watch:
- Advancements in Material Properties: Researchers are continuously developing new techniques to optimize the sintering process, leading to metal jetted parts with mechanical properties even closer to those of traditionally manufactured metals.
- Multi-Material Printing: The ability to jet multiple metal powders within the same printing process is being explored. This would allow for the creation of parts with graded properties or even integration of dissimilar metals in a single build.
- Increased Build Sizes: As metal jetting technology matures, we can expect to see machines capable of producing larger parts, opening doors for wider industrial applications.
- Reduced Costs: As the technology becomes more established and production scales up, the cost of metal jetting is expected to decrease, making it even more competitive with traditional manufacturing methods.
Metal jetting has the potential to revolutionize the way we design and manufacture metal parts. With its speed, precision, and design freedom, this technology is poised to shape the future of various industries.
Share On
MET3DP Technology Co., LTD is a leading provider of additive manufacturing solutions headquartered in Qingdao, China. Our company specializes in 3D printing equipment and high-performance metal powders for industrial applications.
Inquiry to get best price and customized Solution for your business!
Related Articles
About Met3DP
Recent Update
Our Product
CONTACT US
Any questions? Send us message now! We’ll serve your request with a whole team after receiving your message.
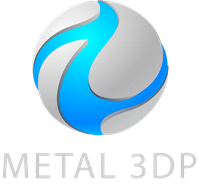
Metal Powders for 3D Printing and Additive Manufacturing