metal powder for motorsport
Table of Contents
Metal powder for motorsport are the building blocks of this revolution. These finely-grained metallic particles, each meticulously engineered for specific properties, are used in 3D printing technologies to create lightweight, high-strength components for race cars. Let’s delve deeper into this fascinating world and explore how these innovative materials are pushing the boundaries of motorsport performance.
Different types of metal powder for motorsport
Not all metal powders are created equal. Each offers a unique blend of properties tailored for specific motorsport applications. Here are ten of the most prominent players in this arena:
- Titanium Grade 2 (Ti-6Al-4V): The undisputed champion, this titanium alloy offers an incredible balance of strength, low weight, and excellent corrosion resistance. It’s a popular choice for suspension components, engine parts, and lightweight body panels.
- Titanium Grade 5 (Ti-6Al-4ELI): A slightly stronger variant of Grade 2, Ti-6Al-4ELI boasts even better fatigue strength. This makes it ideal for highly stressed components like connecting rods and crankshafts that endure immense forces during races.
- Inconel 625: This nickel-chromium superalloy is a true warrior. It withstands extreme temperatures, oxidation, and harsh environments – perfect for exhaust components, turbocharger housings, and parts exposed to intense heat.
- Aluminum Alloy AlSi10Mg: Imagine shaving off precious pounds without sacrificing strength. AlSi10Mg, an aluminum alloy with silicon and magnesium, delivers just that. Its lightweight nature makes it perfect for non-critical components like brackets and housings, contributing to overall weight reduction.
- Stainless Steel 316L: This versatile stainless steel powder offers excellent corrosion resistance and good strength. Think intricate brackets, fluid fittings, and even some bodywork components that need to withstand the elements.
- Cobalt Chrome (CoCr): This biocompatible alloy shines in applications demanding high wear resistance and strength. While not as lightweight as titanium, its exceptional durability makes it suitable for gears and other parts that experience high friction.
- Nickel Alloy 718: Another high-performance contender, Nickel Alloy 718 boasts exceptional strength and good high-temperature properties. It’s a valuable option for suspension components and drivetrain parts that need to handle significant loads.
- Aluminum Alloy Scalmalloy: Pushing the boundaries of aluminum, Scalmalloy offers impressive strength-to-weight ratios. This makes it a potential game-changer for lightweight, high-performance components like wheels and suspension arms.
- Titanium Alloy Ti-4Al-3Mo-2Sn: This titanium alloy boasts exceptional creep resistance – its ability to withstand deformation under high temperatures and stress. This makes it ideal for engine components like pistons and valves that operate in scorching environments.
- Copper: Believe it or not, even copper finds its place in the motorsport AM world. Its excellent thermal conductivity allows for the creation of intricate heat sinks and cooling components, helping manage scorching engine temperatures.
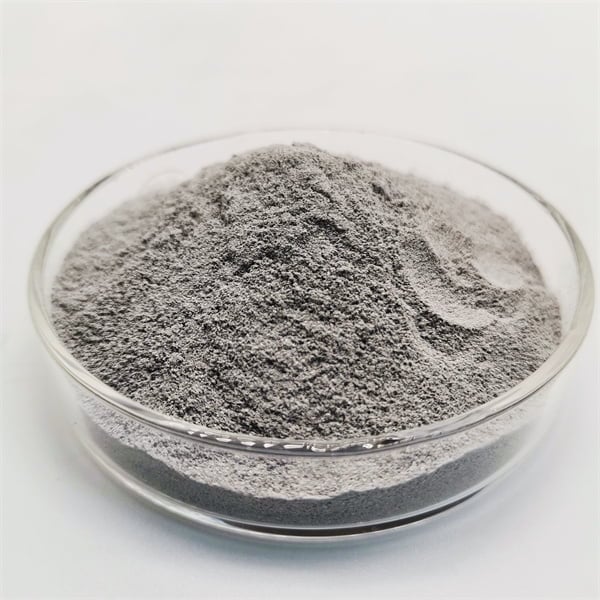
Key Properties of metal powder for motorsport
When choosing the right metal powder for a specific application, several factors come into play. Here’s a table outlining some of the key properties to consider:
Property | Description | Importance in Motorsport |
---|---|---|
Density | How much mass is packed into a given volume | Directly impacts weight. Lower density translates to lighter components, crucial for speed and performance. |
Strength | The material’s ability to resist deformation under stress | Critical for components that experience high loads, like suspension parts and engine components. |
Fatigue Strength | The material’s ability to withstand repeated stress without breaking | Essential for parts that endure continuous vibrations and cyclic loads, such as crankshafts and connecting rods. |
Melting Point | The temperature at which the material transitions from solid to liquid | Highly relevant for components exposed to extreme heat, like exhaust parts and turbochargers. |
Corrosion Resistance | The material’s ability to resist degradation from elements like moisture and chemicals | Important for parts exposed to harsh weather conditions and corrosive fluids. |
Thermal Conductivity | The material’s ability to transfer heat | Crucial for components that need efficient heat dissipation, like engine blocks and cylinder heads. |
Applications of metal powder for motorsport
Metal powders are revolutionizing the way race cars are built, enabling the creation of components that were previously impossible to manufacture using traditional techniques. Here’s a glimpse into the exciting applications of these innovative materials:
Lightweighting for Peak Performance:
- Shedding Pounds: The holy grail of motorsport is shaving off weight without compromising strength. Metal powders, particularly titanium and aluminum alloys, excel in this arena. Imagine intricate suspension arms and lightweight engine components – all contributing to a car that accelerates faster, corners sharper, and ultimately, crosses the finish line first.
- Intricate Designs, Unleashing Potential: Traditional manufacturing methods often struggle with complex geometries. Metal AM, however, thrives on intricate designs. Think of internal channels within components for improved fluid flow or lightweight lattice structures that offer exceptional strength-to-weight ratios. These design freedoms allow engineers to unlock new levels of performance.
Enhanced Functionality and Durability:
- Pushing Heat Boundaries: Motorsport is a battle against heat. Metal powders like Inconel 625 can withstand scorching temperatures, making them ideal for exhaust components and turbocharger housings. This allows for more efficient engine operation and potentially, even higher power outputs.
- Components that Endure: Parts like gears and bearings experience immense wear and tear. Metal powders like Cobalt Chrome offer exceptional abrasion resistance, extending the lifespan of critical components and reducing the need for frequent replacements.
Beyond Weight Reduction: Exploring Other Advantages
Metal AM with powders isn’t just about shaving off pounds. Here are some additional benefits it brings to the table:
- Rapid Prototyping and Customization: Imagine creating a custom-designed component overnight! Metal AM allows for rapid prototyping, enabling engineers to test and iterate on designs quickly. This accelerates development cycles and paves the way for highly customized race car parts.
- Reduced Material Waste: Traditional manufacturing often generates significant scrap metal. Metal AM, however, uses a more targeted approach, minimizing material waste. This translates to a more environmentally friendly production process.
Challenges and Considerations: Not a Silver Bullet
While metal AM with powders offers incredible advantages, it’s not without its challenges. Here are some factors to consider:
- Cost: Metal AM technology and powders can be expensive compared to traditional manufacturing methods. However, the performance gains and weight reduction can often justify the initial investment, especially in high-performance racing applications.
- Surface Finish: Metal AM components may require additional post-processing for a smooth surface finish. This adds to the overall production time and cost.
- Limited Build Size: Current AM machines have limitations on the size of components they can produce. This might restrict the use of metal AM for certain large-scale parts in race cars.
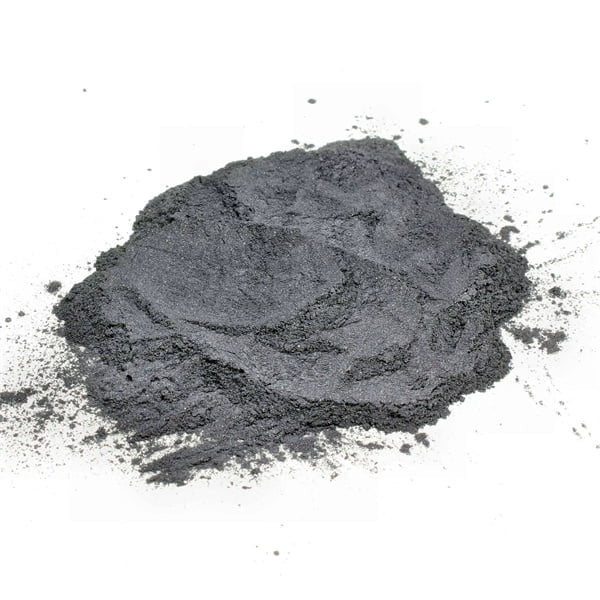
Supplier of metal powder for motorsport
Here’s a table showcasing some prominent suppliers of metal powders for motorsport applications:
Supplier | Notable Products | Areas of Expertise |
---|---|---|
Aubert & Duval | Titanium alloys (Ti-6Al-4V, Ti-6Al-4ELI) | High-performance metal powders for demanding motorsport applications. |
Höganäs | Aluminum alloys (AlSi10Mg), Stainless steel powders (316L) | Offering a wide range of metal powders for various motorsport components. |
AP Powder | Nickel alloys (Inconel 625, Nickel Alloy 718) | Specializes in high-performance powders for components exposed to extreme temperatures and harsh environments. |
Carpenter Additive | Cobalt Chrome (CoCr), Scalmalloy | Providing metal powders for applications demanding exceptional wear resistance and high strength. |
ExOne | Copper | Offering copper powders for creating intricate heat sinks and cooling components. |
Pricing and Availability: A Glimpse into the Market
The pricing of metal powders varies depending on the specific material, particle size, and desired purity. Here’s a general idea:
- Titanium powders: These are among the most expensive metal powders, typically ranging from $50 to $200 per kilogram.
- Aluminum powders: Generally more affordable than titanium, with prices starting around $20 per kilogram.
- Nickel alloys: These high-performance powders can range from $75 to $150 per kilogram.
It’s important to note that these are just indicative prices, and the actual cost can vary depending on the supplier and specific requirements.
Pros and Cons
Pros | Cons |
---|---|
Lightweighting: Significant weight reduction for improved performance. | Cost: Metal AM technology and powders can be expensive. |
Intricate Designs: Unlocks new possibilities for complex geometries and performance optimization. | Surface Finish: May require additional post-processing for a smooth finish, adding to cost and time. |
Enhanced Functionality: Improved heat resistance, wear resistance, and overall component performance. | Limited Build Size: Current technology might restrict the use of metal AM for large-scale parts. |
Rapid Prototyping: Fast turnaround times for creating and testing custom components. | Evolving Technology: Metal AM is a continuously developing field, with ongoing advancements in technology and materials. |
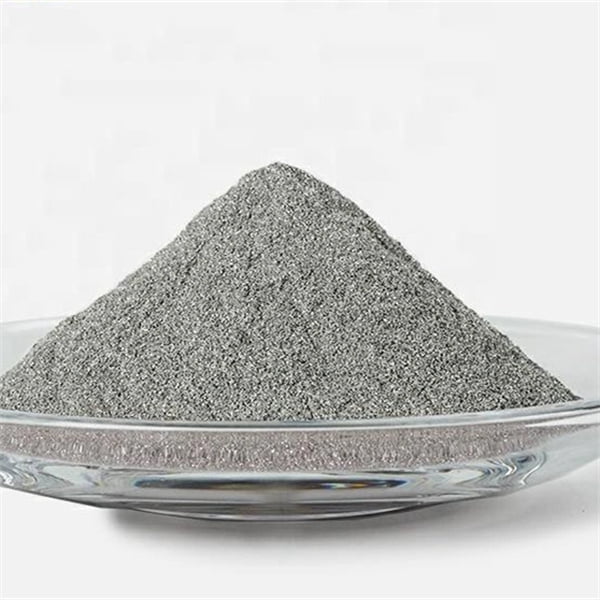
FAQ
Here’s a table addressing some frequently asked questions regarding metal powders in motorsport:
Question | Answer |
---|---|
What are the main benefits of using metal powders in motorsport? | Weight reduction, intricate design possibilities, enhanced component functionality, rapid prototyping, and reduced material waste. |
What are some challenges associated with metal AM using powders? | Cost, surface finish limitations, and restricted build size for certain applications. |
Which metal powders are most commonly used in motorsport? | Titanium alloys (Ti-6Al-4V, Ti-6Al-4ELI) for their exceptional strength-to-weight ratio. Aluminum alloys (AlSi10Mg) for lightweight components. Nickel alloys (Inconel 625) for high-temperature resistance. |
How much do metal powders typically cost? | The price varies depending on the material, particle size, and purity. Titanium powders are generally the most expensive, followed by nickel alloys and then aluminum alloys. |
Is metal AM with powders the future of motorsport manufacturing? | Metal AM holds immense potential for the future of motorsport. As technology advances and costs become more competitive, we can expect to see wider adoption of this revolutionary manufacturing technique. |
Conclusion
Metal powders are revolutionizing the world of motorsport, offering a pathway to lighter, stronger, and more high-performance race cars. From intricate components with optimized designs to enhanced functionality and material efficiency, the possibilities are truly exciting. While challenges like cost and limitations in build size remain, the rapid advancements in metal AM technology suggest a bright future for this innovative approach. As the industry continues to evolve, one thing is certain – metal powders are here to stay, leaving their mark on the ever-competitive world of motorsport.
Share On
MET3DP Technology Co., LTD is a leading provider of additive manufacturing solutions headquartered in Qingdao, China. Our company specializes in 3D printing equipment and high-performance metal powders for industrial applications.
Inquiry to get best price and customized Solution for your business!
Related Articles
About Met3DP
Recent Update
Our Product
CONTACT US
Any questions? Send us message now! We’ll serve your request with a whole team after receiving your message.
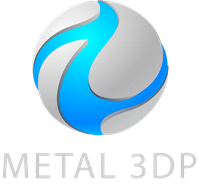
Metal Powders for 3D Printing and Additive Manufacturing