Metal Powder for Welding
Table of Contents
Overview of Metal Powder for Welding
Welding is an essential process in various industries, from automotive to aerospace, requiring precise materials for optimal performance. metal powder for welding used in welding are finely ground metallic particles that enhance the welding process by providing better control over the welding arc and reducing defects. This comprehensive guide delves into the various types of metal powders used in welding, their applications, advantages, and limitations, providing a detailed analysis for professionals and enthusiasts alike.
Understanding Metal Powder for Welding
Metal powder welding involves using finely powdered metals as a filler material in various welding processes, including powder welding, thermal spraying, and laser cladding. The choice of metal powder can significantly affect the quality, strength, and durability of the weld.
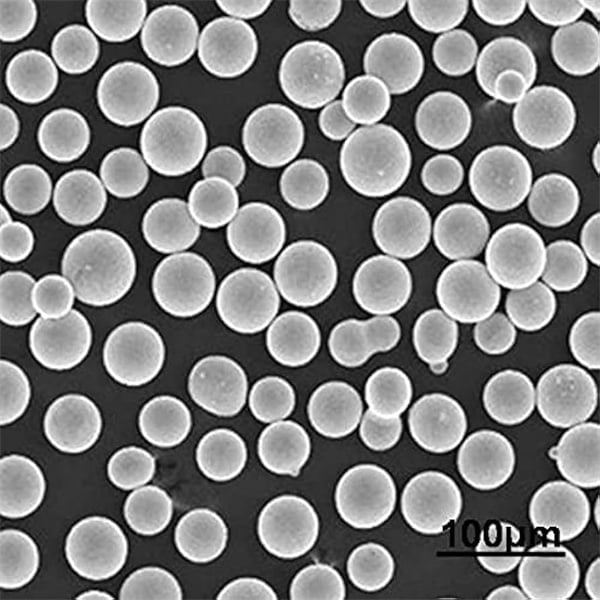
Types and Composition of Metal Powders
Below is a table summarizing different types of metal powders commonly used in welding, their composition, and properties.
Type of Metal Powder | Composition | Properties | Characteristics |
---|---|---|---|
Iron Powder | Pure iron | High strength, magnetic properties | Cost-effective, versatile |
Aluminum Powder | Pure aluminum | Lightweight, corrosion-resistant | High thermal conductivity |
Copper Powder | Pure copper | Excellent electrical conductivity | High thermal conductivity |
Nickel Powder | Pure nickel | High corrosion resistance | Good high-temperature strength |
Stainless Steel Powder | Fe-Cr-Ni alloy | Corrosion-resistant, strong | Durable, versatile |
Titanium Powder | Pure titanium | Lightweight, high strength | Excellent corrosion resistance |
Cobalt Powder | Pure cobalt | High wear resistance | Excellent high-temperature performance |
Tungsten Powder | Pure tungsten | High melting point, dense | Very strong, wear-resistant |
Molybdenum Powder | Pure molybdenum | High melting point, tough | Good high-temperature strength |
Zinc Powder | Pure zinc | Corrosion-resistant, ductile | Good for galvanizing |
Applications of Metal Powder for Welding
Metal powders are used in various welding applications, each offering unique benefits. Here’s a detailed table showcasing their uses:
Application | Type of Metal Powder | Benefits |
---|---|---|
Thermal Spraying | Nickel, Stainless Steel | High corrosion resistance |
Laser Cladding | Cobalt, Titanium | Enhanced surface properties |
Powder Welding | Iron, Copper | Improved weld strength |
Additive Manufacturing | Aluminum, Titanium | Lightweight, high strength |
Repair Welding | Tungsten, Molybdenum | High durability, wear resistance |
Surface Coating | Zinc, Copper | Improved surface protection |
Brazing | Nickel, Copper | Strong, durable joints |
Specifications, Sizes, Grades, and Standards
For an effective welding process, choosing the correct specifications, sizes, grades, and standards of metal powders is crucial. Below is a table detailing these aspects.
Metal Powder | Specifications | Sizes (µm) | Grades | Standards |
---|---|---|---|---|
Iron Powder | ASTM A95 | 45-150 | High Purity | ISO 4497, ASTM B214 |
Aluminum Powder | ASTM B928 | 20-100 | High Purity | ASTM B928 |
Copper Powder | ASTM B170 | 45-150 | High Purity | ASTM B170 |
Nickel Powder | ASTM B330 | 20-100 | High Purity | ISO 4497, ASTM B330 |
Stainless Steel Powder | ASTM A131 | 20-150 | Various | ASTM A131 |
Titanium Powder | ASTM B348 | 20-100 | Grade 1-5 | ASTM B348 |
Cobalt Powder | ASTM F75 | 20-150 | Various | ASTM F75 |
Tungsten Powder | ASTM B777 | 20-100 | High Purity | ASTM B777 |
Molybdenum Powder | ASTM B387 | 20-150 | High Purity | ASTM B387 |
Zinc Powder | ASTM B328 | 20-100 | High Purity | ASTM B328 |
Suppliers and Pricing Details
Choosing the right supplier is crucial for acquiring high-quality metal powders. Here’s a table listing some reputable suppliers along with pricing details.
Supplier | Metal Powder | Price (per kg) | Location | Contact Details |
---|---|---|---|---|
American Elements | Iron, Aluminum | $50 – $150 | USA | [email protected] |
Höganäs AB | Iron, Stainless Steel | $100 – $300 | Sweden | [email protected] |
Advanced Metal Powders | Copper, Nickel | $150 – $350 | UK | [email protected] |
Tekna Plasma Systems | Titanium, Cobalt | $200 – $500 | Canada | [email protected] |
Global Tungsten & Powders | Tungsten, Molybdenum | $250 – $600 | Germany | [email protected] |
Belmont Metals | Zinc, Aluminum | $80 – $200 | USA | [email protected] |
Comparing Pros and Cons: Advantages and Limitations
Each type of metal powder has its advantages and limitations. Understanding these can help in making an informed decision. Here’s a comparative table.
Metal Powder | Advantages | Limitations |
---|---|---|
Iron Powder | Cost-effective, strong | Susceptible to rust |
Aluminum Powder | Lightweight, corrosion-resistant | Lower strength compared to others |
Copper Powder | Excellent conductivity, thermal properties | Expensive, not as strong |
Nickel Powder | High corrosion resistance, durable | Expensive |
Stainless Steel Powder | Corrosion-resistant, versatile | Costly, may require specialized handling |
Titanium Powder | High strength, lightweight | Very expensive, reactive |
Cobalt Powder | High wear resistance, durable at high temps | High cost |
Tungsten Powder | Very strong, wear-resistant | Extremely heavy, difficult to work with |
Molybdenum Powder | High melting point, tough | Expensive, limited availability |
Zinc Powder | Cost-effective, corrosion-resistant | Lower strength, limited high-temperature use |
Detailed Analysis of Specific Metal Powder Models
Here’s an in-depth look at ten specific metal powder models, highlighting their unique features and applications.
- Fe-Powder X100
- Composition: Pure iron
- Properties: High strength, magnetic
- Applications: General welding, automotive parts
- Pros: Cost-effective, widely available
- Cons: Prone to rust
- Al-Powder A200
- Composition: Pure aluminum
- Properties: Lightweight, excellent thermal conductivity
- Applications: Aerospace, automotive
- Pros: Corrosion-resistant, lightweight
- Cons: Lower tensile strength
- Cu-Powder C300
- Composition: Pure copper
- Properties: Excellent electrical conductivity
- Applications: Electrical components, thermal management
- Pros: High thermal and electrical conductivity
- Cons: Expensive, soft
- Ni-Powder N400
- Composition: Pure nickel
- Properties: High corrosion resistance, durable
- Applications: Marine, chemical processing
- Pros: Long-lasting, durable
- Cons: High cost
- SS-Powder S500
- Composition: Fe-Cr-Ni alloy
- Properties: Corrosion-resistant, strong
- Applications: Medical devices, food processing
- Pros: Versatile, strong
- Cons: Expensive
- Ti-Powder T600
- Composition: Pure titanium
- Properties: Lightweight, high strength
- Applications: Aerospace, medical implants
- Pros: High strength-to-weight ratio
- Cons: Very expensive
- Co-Powder C700
- Composition: Pure cobalt
- Properties: High wear resistance
- Applications: Turbine blades, cutting tools
- Pros: Excellent high-temperature performance
- Cons: High cost
- W-Powder W800
- Composition: Pure tungsten
- Properties: High melting point, dense
- Applications: Radiation shielding, high-temperature components
- Pros: Very strong, durable
- Cons: Extremely heavy, difficult to process
- Mo-Powder M900
- Composition: Pure molybdenum
- Properties: High melting point, tough
- Applications: Aerospace, electronics
- Pros: Good high-temperature strength
- Cons: Expensive
- Zn-Powder Z1000
- Composition: Pure zinc
- – Properties: Corrosion-resistant, ductile
- – Applications: Galvanizing, battery manufacturing
- – Pros: Cost-effective, versatile
- – Cons: Lower strength, limited high-temperature use
Advantages of Metal Powder for Welding
Metal powders offer several advantages over traditional welding materials. Here are some key benefits:
Enhanced Control
Using metal powders allows for better control over the welding process. The fine particles can be precisely fed into the weld pool, ensuring a more consistent and high-quality weld.
Improved Mechanical Properties
Metal powders can significantly enhance the mechanical properties of the weld. For instance, using titanium powder can result in a lightweight yet strong weld, ideal for aerospace applications.
Versatility
Different metal powders can be used for various applications, from repairing worn-out components to manufacturing new parts with complex geometries. This versatility makes metal powders a valuable resource in multiple industries.
Cost Efficiency
While some metal powders like titanium or cobalt can be expensive, others like iron and zinc are cost-effective. Additionally, the precision and reduced waste associated with powder welding can lead to overall cost savings.
Disadvantages of Metal Powder for Welding
Despite their numerous advantages, metal powders also have some limitations.
Cost
High-quality metal powders, especially those made from rare or complex alloys, can be expensive. This can be a limiting factor for some applications.
Storage and Handling
Metal powders require careful storage and handling to prevent contamination and degradation. This can add to the complexity and cost of using these materials.
Specialized Equipment
Using metal powders often requires specialized equipment, such as laser cladding machines or thermal spray systems. This can be a significant investment for companies looking to adopt this technology.
Choosing the Right Metal Powder
Selecting the right metal powder for your welding needs involves considering various factors, including the specific application, desired properties, and budget. Here are some tips to help you make an informed decision:
Evaluate the Application
Consider what you will be using the metal powder for. Different applications require different properties. For example, if you need a strong, corrosion-resistant weld for marine applications, stainless steel or nickel powder would be a good choice.
Consider the Environment
The environment in which the welded component will be used can significantly affect your choice of metal powder. For high-temperature environments, tungsten or molybdenum powders are ideal due to their high melting points.
Balance Cost and Performance
While it might be tempting to opt for the highest quality metal powder available, it’s essential to balance cost and performance. Sometimes a more affordable option like iron or zinc powder can meet your needs without breaking the bank.
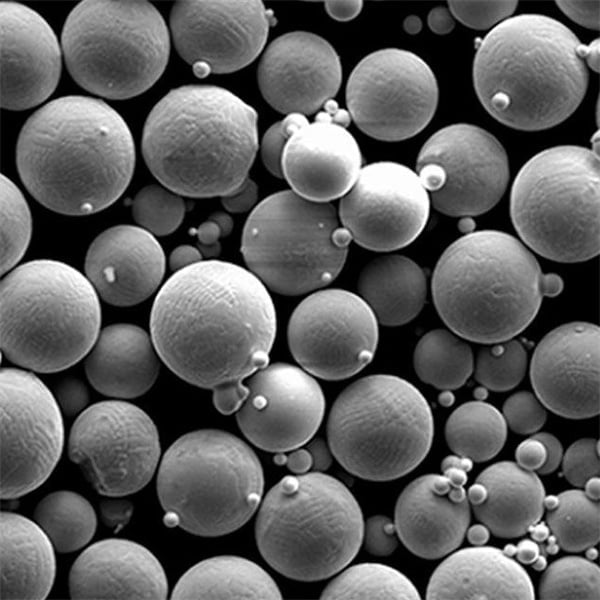
FAQs
Here’s a FAQ section to address common questions about metal powder for welding:
Question | Answer |
---|---|
What is metal powder for welding? | Metal powder for welding is finely ground metallic particles used as filler material in various welding processes to enhance weld quality and performance. |
How is metal powder used in welding? | Metal powders are used in processes like powder welding, thermal spraying, and laser cladding, where they are fed into the weld pool or applied to surfaces. |
What are the benefits of using metal powder? | Benefits include enhanced control, improved mechanical properties, versatility, and cost efficiency. |
What are the drawbacks? | Drawbacks include high cost for some powders, need for careful storage and handling, and requirement for specialized equipment. |
How do I choose the right metal powder? | Consider the specific application, environmental conditions, and balance between cost and performance. Evaluate factors like strength, corrosion resistance, etc. |
Can metal powders be mixed? | Yes, metal powders can be mixed to achieve desired properties, but it requires careful consideration of compatibility and processing techniques. |
Where can I buy metal powder for welding? | Metal powders can be purchased from specialized suppliers such as American Elements, Höganäs AB, and Tekna Plasma Systems. |
Is metal powder welding suitable for DIY? | Metal powder welding typically requires specialized equipment and expertise, making it more suitable for industrial applications rather than DIY projects. |
What safety precautions should be taken? | Proper ventilation, protective gear, and careful handling are essential to prevent inhalation of fine particles and contamination. |
Conclusion
Metal powders for welding offer a versatile, efficient, and high-quality solution for various industrial applications. By understanding the different types of metal powders, their properties, and how to choose the right one for your needs, you can significantly enhance your welding projects. Whether you’re working in aerospace, automotive, or general manufacturing, metal powders can provide the performance and reliability you need to achieve the best results.
Share On
MET3DP Technology Co., LTD is a leading provider of additive manufacturing solutions headquartered in Qingdao, China. Our company specializes in 3D printing equipment and high-performance metal powders for industrial applications.
Inquiry to get best price and customized Solution for your business!
Related Articles
About Met3DP
Recent Update
Our Product
CONTACT US
Any questions? Send us message now! We’ll serve your request with a whole team after receiving your message.
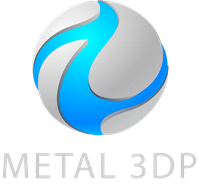
Metal Powders for 3D Printing and Additive Manufacturing