Water Atomization Transforming Molten Metal into Metal Powders
Table of Contents
Imagine a sculptor, not wielding a chisel and stone, but wielding the power of water to break down molten metal into tiny, individual particles. This is the essence of water atomization, a remarkable process that transforms various metals into metal powders with unique properties and diverse applications.
the Process: from Molten Metal to Microscopic Powder
The water atomization process is a fascinating dance between intense heat, high pressure, and the cooling power of water. Here’s a glimpse into its steps:
- Melting the Metal: The metal of choice is heated to its molten state in a furnace, reaching temperatures exceeding thousands of degrees Fahrenheit.
- Atomization Chamber: The molten metal is then transferred to an atomization chamber, where it encounters the magic ingredient – high-pressure water jets.
- Fragmentation: These water jets, at pressures exceeding 50 MPa (equivalent to the pressure at the bottom of the Mariana Trench!), collide with the molten metal, causing it to fragment into tiny droplets.
- Rapid Cooling: As these droplets fall through a cooling tower, they rapidly solidify due to the surrounding air and water, forming the desired metal powder.
- Classification and Packaging: The metal powder is then sieved and classified according to desired particle size and packaged for various industrial applications.
This seemingly simple process unlocks a world of possibilities, allowing us to create metal powders with specific characteristics, tailored for various purposes.
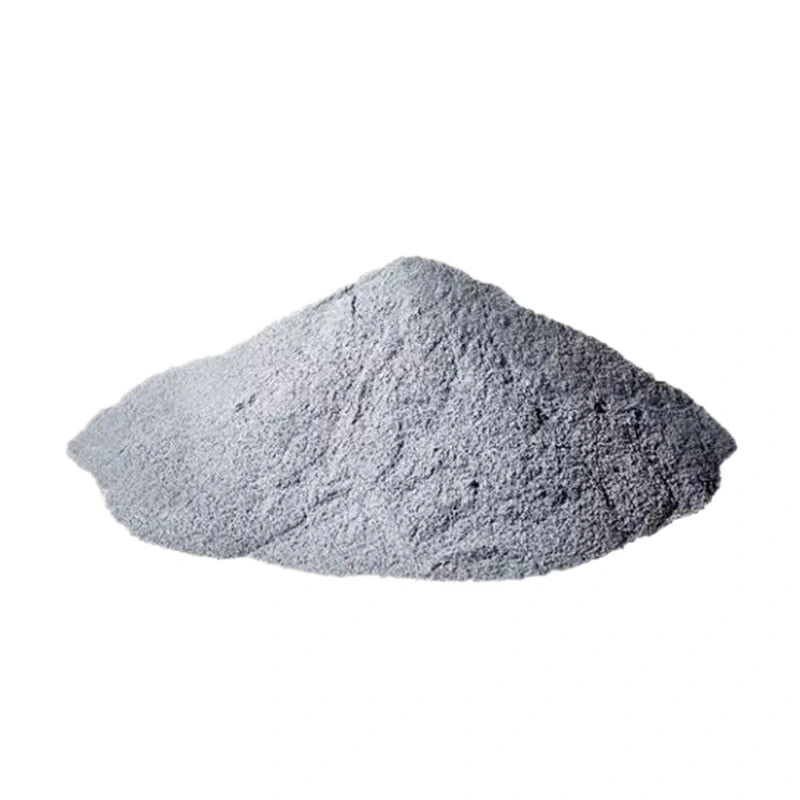
A Spectrum of Metal Powders: Unveiling the Diversity
Water atomization offers a diverse range of metal powders, each boasting unique properties and applications. Here are ten prominent examples:
1. Stainless Steel Powders: Renowned for their corrosion resistance and high strength, these powders find their way into diverse applications, from medical implants and automotive components to household appliances and aerospace parts.
2. Tool Steel Powders: Offering exceptional hardness and wear resistance, tool steel powders are instrumental in creating cutting tools, dies, and molds that can withstand demanding industrial environments.
3. Low-Alloy Steel Powders: These versatile powders, known for their affordability and good balance of strength and formability, are widely used in the production of structural components, gears, and machine parts.
4. Nickel Powders: Highly sought-after for their excellent corrosion resistance and electrical conductivity, nickel powders are crucial for manufacturing electrodes, catalysts, and electronic components.
5. Copper Powders: Renowned for their superior thermal and electrical conductivity, copper powders are utilized in various applications, including heat sinks, electrical contacts, and bearings.
6. Aluminum Powders: Offering an enticing combination of lightweight properties and good formability, aluminum powders are employed in diverse applications, from pyrotechnics and paints to additive manufacturing and automotive components.
7. Titanium Powders: Valued for their high strength-to-weight ratio and excellent corrosion resistance, titanium powders are employed in demanding applications, such as aerospace components, medical implants, and high-performance sporting goods.
8. Cobalt Powders: Known for their magnetic properties and high melting point, cobalt powders are essential for creating permanent magnets, cutting tools, and wear-resistant coatings.
9. Tungsten Powders: These dense and high-melting point powders are crucial for producing various industrial components, including welding electrodes, armor-piercing ammunition, and heating elements.
10. Molybdenum Powders: Offering excellent high-temperature strength and resistance to corrosion, molybdenum powders are utilized in diverse applications, from filaments in light bulbs and heating elements to rocket nozzles and refractory crucibles.
This list merely scratches the surface of the vast array of metal powders available through water atomization. Each powder offers a unique set of properties, making them
A Universe of Applications: Where Metal Powders Shine
Metal powders, born from the transformative power of water atomization, find their way into a multitude of applications across various industries. Here’s a glimpse into their diverse uses:
Industry | Applications |
---|---|
Metal Additive Manufacturing (AM): | 3D printing of complex metal parts, offering design freedom and weight reduction. |
Powder Metallurgy (PM): | Pressing and sintering metal powders into desired shapes, enabling mass production of complex parts. |
Thermal Spraying: | Coating surfaces with metal powders to enhance properties like wear resistance, corrosion resistance, and thermal conductivity. |
Brazing and Welding: | Joining metal components using metal powders melted with heat or pressure. |
Friction Materials: | Manufacturing brake pads, clutches, and other components that utilize friction for function. |
Electrical & Electronics: | Creating conductive components, electrodes, and catalysts. |
Chemical & Medical Industries: | Manufacturing catalysts, pigments, and even some medical implants. |
Beyond the ten aforementioned metal powders, water atomization unlocks a vast array of possibilities. Here are some additional examples:
- Iron Powders: These workhorses of the metal powder industry find applications in diverse sectors, including automotive components, electrical components, and magnetic cores for transformers and inductors.
- Bronze Powders: Combining the strength of copper with the tin’s corrosion resistance, bronze powders are employed in bearings, bushings, and electrical contacts.
- Brass Powders: Offering good machinability and corrosion resistance, brass powders are utilized in plumbing fixtures, hardware components, and decorative applications.
- Spherical Metal Powders: These unique powders, boasting near-perfect spherical shapes, offer superior flowability and packing density, making them ideal for metal additive manufacturing and specific applications in thermal spraying and brazing.
- Metal Alloys: Water atomization isn’t limited to single metals; it can also create intricate metal alloys by atomizing a blend of molten metals. This opens doors to even more diverse properties and applications.
The applications of metal powders continue to expand at a rapid pace, driven by advancements in technology and the ingenuity of engineers and scientists. Here are some additional noteworthy examples:
- Biomedical Implants: Metal powders, particularly titanium and tantalum, are being increasingly utilized in the creation of biocompatible implants, such as hip and knee replacements, due to their excellent strength-to-weight ratio and biocompatibility.
- Energy Storage: Metal powders play a crucial role in the development of next-generation batteries, acting as key components in electrodes and other vital parts.
- Aerospace & Defense: The high strength-to-weight ratio and unique properties of metal powders make them ideal for creating lightweight and high-performance aerospace components, such as engine parts and airframes.
- Catalysis: Metal powders, due to their large surface area and specific properties, are used as catalysts in various chemical reactions, accelerating reaction rates and improving process efficiency.
The future of metal powders is undoubtedly bright, with continuous advancements in water atomization technology and the discovery of new applications across diverse industries. As research and development efforts continue, we can expect even more innovative and groundbreaking applications to emerge, further solidifying the role of metal powders in shaping the world around us.
Unveiling the Nuances: A Multifaceted Look at Metal Powders
Choosing the right metal powder for a specific application requires careful consideration of various factors. Here’s a breakdown of some key aspects to ponder:
1. Material Properties:
- Composition: The type of metal or alloy used in the powder significantly impacts its properties, such as strength, corrosion resistance, and electrical conductivity.
- Particle Size and Distribution: The size and distribution of the powder particles influence aspects like flowability, packing density, and surface area, all crucial factors in various applications.
- Morphology: The shape of the powder particles, whether spherical, irregular, or flaky, can impact aspects like packing density, flowability, and even the final properties of the finished product.
2. Application-Specific Requirements:
- The intended use of the metal powder significantly dictates the selection process. For instance, powders for additive manufacturing require high flowability and good packing density, while powders for thermal spraying might prioritize specific melting points and particle size distribution.
3. Cost and Availability:
- The cost of the metal powder plays a vital role in the selection process, especially for large-scale applications. Additionally, the availability of specific powders in desired quantities and specifications needs to be considered.
4. Environmental and Sustainability Concerns:
- The environmental impact of the entire production process, including energy consumption and potential waste generation, should be factored into the selection process. Additionally, the sustainability of the metal source and its potential for recycling can be crucial considerations for responsible manufacturing.
By carefully considering these factors, engineers and manufacturers can make informed decisions when choosing the most suitable metal powder for their specific needs.
Beyond the Basics: Exploring Advanced Concepts
As the world of metal powders continues to evolve, several exciting advancements are worth exploring:
- Nanopowders: Metal powders with particle sizes in the nanometer range offer unique properties and hold immense potential in various applications, including catalysts, sensors, and drug delivery systems.
- Composites and Functionally Graded Materials: Combining different types of metal powders or even integrating them with non-metallic materials opens doors to the creation of novel materials with tailored properties for specific applications.
- Sustainability and Environmentally Friendly Processes: Developments in water atomization technology are focusing on reducing energy consumption, minimizing waste generation, and utilizing recycled materials, contributing to a more sustainable future for metal powder production.
Metal Powder Suppliers, Pricing, and Comparisons
With the diverse landscape of metal powders and their ever-expanding applications, navigating the world of suppliers and pricing can be a complex task. Here’s a comprehensive guide to equip you with the knowledge needed to make informed decisions:
Metal Powder Suppliers:
The global market for metal powders boasts a wide range of established and emerging players, each offering diverse powders with varying specifications and capabilities. Here are some prominent suppliers to consider:
- Höganäs AB: A leading global producer of metal powders, offering a vast portfolio encompassing various types, sizes, and alloys.
- AP Powder Company: Renowned for its high-quality metal powders for additive manufacturing and other applications.
- AMETEK SMP: A trusted supplier of specialty metal powders, catering to diverse industries like aerospace and electronics.
- Carpenter Additive Manufacturing: Provides metal powders specifically optimized for additive manufacturing applications.
- SLM Solutions GmbH: Offers metal powders tailored for their laser additive manufacturing machines.
It’s crucial to note that this list is not exhaustive, and numerous other reputable suppliers exist worldwide. When choosing a supplier, consider factors like:
- Product portfolio: Ensure they offer the specific metal powder type, size, and grade required for your application.
- Quality and consistency: Opt for suppliers with a proven track record of delivering high-quality powders with consistent properties.
- Technical expertise: Choose a supplier with knowledgeable personnel who can provide technical support and guidance throughout the selection process.
- Pricing and lead times: Compare pricing and lead times from different suppliers to find the most suitable option for your budget and project timeline.
Metal Powder Pricing:
The cost of metal powders can vary significantly depending on several factors, including:
- The type of metal or alloy: Precious metals like gold or platinum naturally command higher prices compared to common metals like iron or aluminum.
- Particle size and distribution: Finer powders with specific size distributions generally demand a premium due to the increased processing complexity.
- Purity and grade: High-purity and specialty grades typically come at a higher cost compared to standard grades.
- Volume and demand: Larger order quantities often benefit from economies of scale, leading to lower per-unit pricing.
It’s essential to remember that the price shouldn’t be the sole deciding factor when choosing a metal powder. Consider the overall value proposition, including factors like quality, consistency, technical support, and long-term reliability, before making a final decision.
Metal Powder Comparisons:
Comparing different metal powders requires careful consideration of various properties and application-specific requirements. Here’s a breakdown of some key parameters to compare:
- Mechanical properties: This includes aspects like tensile strength, yield strength, and elongation, which are crucial for applications requiring structural integrity.
- Physical properties: Factors like density, melting point, and thermal conductivity play a significant role in various applications, such as thermal spraying or additive manufacturing.
- Chemical properties: Corrosion resistance, oxidation resistance, and biocompatibility are essential considerations for applications where the powder interacts with specific environments or needs to meet biocompatibility standards.
By thoroughly comparing these properties and considering the specific needs of your application, you can make an informed decision and select the most suitable metal powder for your project.
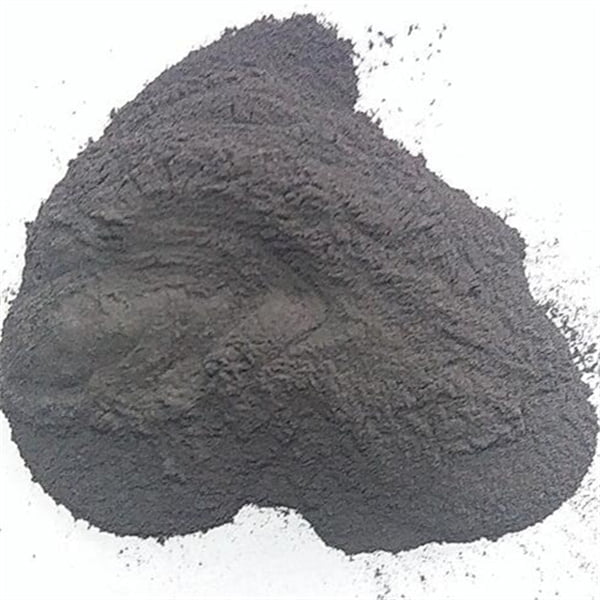
the Advantages and Limitations: A Balanced Perspective
Metal powders, born from the innovative process of water atomization, offer a multitude of advantages:
- Versatility: The diverse range of available metal powders, coupled with their tailorable properties, caters to a vast array of applications across various industries.
- High-performance characteristics: Metal powders can offer exceptional strength-to-weight ratios, high conductivity, and unique properties not achievable with traditional manufacturing methods.
- Design freedom: Metal powders, particularly when utilized in additive manufacturing, enable the creation of complex geometries and intricate designs, pushing the boundaries of conventional manufacturing.
- Near-net shape manufacturing: Metal powders allow for the production of parts closer to their final shape, minimizing material waste and reducing machining requirements.
- Potential for mass production: Powder metallurgy techniques, utilizing metal powders, enable mass production of complex parts with good consistency and repeatability.
However, it’s essential to acknowledge that metal powders also come with certain limitations:
- Cost: Depending on the specific metal, size, and grade, metal powders can be more expensive compared to some conventional materials.
- Storage and handling: Metal powders can be susceptible to moisture and oxidation, requiring careful storage and handling procedures to maintain their properties.
- Safety considerations: Metal powders can pose safety hazards, such as inhalation risks or flammability concerns, necessitating proper handling and safety protocols.
By understanding both the advantages and limitations of metal powders, you can make informed decisions about their suitability for your specific application and implement appropriate measures to mitigate any potential drawbacks.
FAQ
1. What are the advantages of water atomization over other metal powder production methods?
Water atomization offers several advantages compared to other methods like gas atomization or atomized shot:
- Cost-effective: Water is readily available and significantly less expensive than the inert gases used in gas atomization.
- Environmentally Friendly: Water atomization generally has a lower environmental footprint compared to gas atomization, which can generate greenhouse gas emissions.
- Broader range of materials: Water atomization can effectively process a wider range of metal types and alloys compared to some other methods.
2. How are metal powders used in 3D printing?
Metal powders are the primary building material for metal additive manufacturing (AM) techniques like Selective Laser Melting (SLM) and Electron Beam Melting (EBM). The powder is fed into the 3D printer layer by layer, where a laser or electron beam melts the powder, fusing it to create the desired 3D object.
3. What are some safety precautions to take when handling metal powders?
Metal powders can pose various safety risks, including:
- Inhalation: Fine metal particles can be inhaled and cause respiratory irritation or even lung damage.
- Fire and explosion: Some metal powders, particularly those with high surface area like magnesium powders, can be flammable and pose a fire or explosion risk.
- Skin and eye irritation: Direct contact with metal powders can irritate the skin and eyes.
4. What are some future trends in the metal powder industry?
The metal powder industry is expected to witness significant growth in the coming years, driven by several factors:
- Advancements in additive manufacturing: As metal AM technologies continue to evolve, the demand for high-quality metal powders for 3D printing is expected to rise significantly.
- Development of novel materials: Research focusing on creating metal powders with unique properties, such as nanopowders or functionally graded materials, is expected to unlock new applications and possibilities.
- Focus on sustainability: Advancements in water atomization technology are likely to focus on reducing energy consumption, minimizing waste generation, and utilizing recycled materials, contributing to a more sustainable future for metal powder production.
5. Where can I find more information about specific metal powders and their suppliers?
Several resources can help you learn more about specific metal powders and their suppliers:
- Metal powder supplier websites: Most reputable suppliers have detailed information about their product offerings, specifications, and technical data on their websites.
- Industry publications and trade shows: Industry publications and trade shows related to metal powders, additive manufacturing, or specific application areas can provide valuable insights and connect you with potential suppliers.
- Scientific research papers and online databases: Research papers and online databases focused on material science and engineering can offer in-depth information about the properties and applications of various metal powders.
Share On
MET3DP Technology Co., LTD is a leading provider of additive manufacturing solutions headquartered in Qingdao, China. Our company specializes in 3D printing equipment and high-performance metal powders for industrial applications.
Inquiry to get best price and customized Solution for your business!
Related Articles
About Met3DP
Recent Update
Our Product
CONTACT US
Any questions? Send us message now! We’ll serve your request with a whole team after receiving your message.
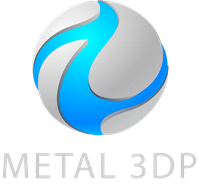
Metal Powders for 3D Printing and Additive Manufacturing