Metal Powders for Aviation
Table of Contents
Welcome to the fascinating world of metal powders for aviation! Whether you’re an aviation enthusiast, an industry professional, or just curious about this niche field, you’re in the right place. In this article, we’ll explore the various types of metal powders used in aviation, their applications, advantages, disadvantages, and much more. Buckle up, and let’s dive into the specifics!
Overview of Metal Powder for Aviation
Metal powders are finely divided metals used extensively in various industrial processes, including aviation. In aviation, metal powders are crucial for manufacturing components through techniques like additive manufacturing (3D printing), which allows for the creation of complex and lightweight parts essential for modern aircraft. These powders are typically produced by atomizing molten metal into tiny droplets that solidify into fine particles.
Key Points:
- Types of Metal Powders: Various metals and alloys such as titanium, aluminum, nickel, and cobalt.
- Applications: Additive manufacturing, repair, and coating of aviation components.
- Benefits: Lightweight, high strength, corrosion resistance, and design flexibility.
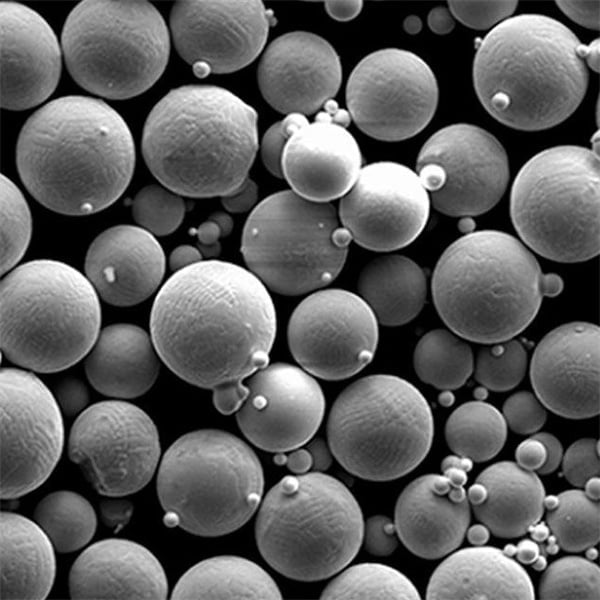
Types and Characteristics of Metal Powders
The type of metal powder used in aviation depends on the specific requirements of the component being manufactured. Let’s break down some of the most commonly used metal powders and their properties.
Metal Powder | Composition | Properties | Characteristics |
---|---|---|---|
Titanium Alloy (Ti6Al4V) | 90% Titanium, 6% Aluminum, 4% Vanadium | High strength-to-weight ratio, corrosion resistance | Widely used in structural components, biocompatible |
Aluminum Alloy (AlSi10Mg) | 90% Aluminum, 10% Silicon, <1% Magnesium | Lightweight, good thermal properties | Ideal for heat exchangers, brackets |
Nickel Alloy (Inconel 718) | 50-55% Nickel, 17-21% Chromium, 4.75-5.5% Niobium | High temperature resistance, excellent mechanical properties | Used in turbine blades, engine components |
Cobalt Chrome (CoCrMo) | 60% Cobalt, 28-30% Chromium, 5-7% Molybdenum | Wear resistance, biocompatibility | Used in medical implants, aerospace components |
Stainless Steel (316L) | 16-18% Chromium, 10-14% Nickel, 2-3% Molybdenum | Corrosion resistance, good mechanical properties | Suitable for brackets, structural parts |
Maraging Steel (MS1) | 18-19% Nickel, 8-10% Cobalt, 4-5% Molybdenum | High strength, toughness | Ideal for tooling, molds |
Copper Alloy (CuCrZr) | 99% Copper, 0.8-1.2% Chromium, 0.1-0.2% Zirconium | High thermal and electrical conductivity | Used in heat sinks, electrical components |
Tungsten (W) | 99.95% Tungsten | High density, high melting point | Suitable for counterweights, radiation shielding |
Magnesium Alloy (AZ91D) | 90% Magnesium, 9% Aluminum, 1% Zinc | Ultra-lightweight, good machinability | Used in lightweight structural components |
Hastelloy X | 47% Nickel, 22% Chromium, 18.5% Iron | Oxidation resistance, high-temperature strength | Used in combustion chambers, afterburners |
Applications of Metal Powder for Aviation
Metal powders have revolutionized the aviation industry by enabling the production of complex, lightweight, and high-performance components. Here are some of the key applications:
Applications Table
Application | Description | Examples |
---|---|---|
Additive Manufacturing | Creating intricate components layer by layer using 3D printing technologies | Engine parts, structural components |
Repair and Maintenance | Repairing worn-out or damaged parts by adding material to the existing component | Turbine blades, exhaust nozzles |
Surface Coating | Enhancing surface properties such as wear resistance and thermal protection | Protective coatings for turbine engines |
Prototyping | Rapid production of prototype parts to test fit, form, and function | Prototype brackets, housings |
Lightweight Structures | Manufacturing lightweight components to improve fuel efficiency and reduce overall weight of aircraft | Airframe components, seats |
Heat Exchangers | Producing components with complex internal structures for efficient heat transfer | Aircraft heat exchangers, cooling ducts |
Electrical Components | Creating parts with excellent electrical conductivity for various aviation systems | Electrical connectors, heat sinks |
Biocompatible Implants | Producing biocompatible implants for medical applications within aviation settings | Joint replacements, dental implants |
Tooling and Molds | Manufacturing durable and precise molds and tooling for component production | Injection molds, casting dies |
Counterweights | Producing high-density components used for balance and stability | Counterweights for control surfaces |
Detailed Applications:
- Additive Manufacturing: One of the most significant uses of metal powders in aviation is 3D printing, allowing for the creation of complex geometries that traditional manufacturing methods cannot achieve. This is particularly beneficial for components such as fuel nozzles and engine parts that require intricate internal features.
- Repair and Maintenance: Metal powders are also used in repair technologies like laser cladding, which can restore the dimensions and properties of worn-out parts, extending their service life.
- Surface Coating: Protective coatings using metal powders can enhance the durability and performance of critical components exposed to harsh environments, such as turbine blades.
Advantages of Metal Powder for Aviation
Using metal powders in aviation brings several advantages. Let’s delve into the key benefits that make metal powders indispensable in the aviation industry.
Advantages Table
Advantage | Description |
---|---|
Lightweight | Metal powders enable the production of lightweight components, reducing overall aircraft weight. |
High Strength | Components made from metal powders exhibit high strength and durability, essential for aviation safety. |
Design Flexibility | Additive manufacturing allows for complex and customized designs that traditional methods can’t achieve. |
Material Efficiency | Metal powder processes produce less waste compared to subtractive manufacturing methods. |
Reduced Lead Time | Faster production times, especially for complex parts and prototypes. |
Cost-Effective Repairs | Repairs using metal powders can be more economical than replacing entire components. |
Enhanced Performance | Improved material properties such as wear resistance and thermal stability. |
Sustainability | More efficient material usage and potential for recycling powder materials contribute to sustainability. |
Exploring the Benefits:
- Lightweight: Every ounce counts in aviation. Metal powders enable the creation of lightweight components without compromising strength, leading to fuel savings and increased payload capacity.
- Design Flexibility: Imagine creating a part with intricate internal channels or unique shapes that improve performance—this is possible with metal powders and 3D printing.
- Reduced Lead Time: Rapid prototyping and manufacturing mean that new designs and repairs can be implemented quickly, keeping aircraft in service longer.
Disadvantages of Metal Powder for Aviation
While there are many advantages, it’s also important to consider the potential drawbacks of using metal powders in aviation.
Disadvantages Table
Disadvantage | Description |
---|---|
High Cost | Some metal powders, especially high-performance alloys, can be expensive. |
Complex Process Control | Manufacturing with metal powders requires precise control of process parameters. |
Limited Material Variety | Not all metals and alloys are available or suitable for powder production and additive manufacturing. |
Quality Assurance | Ensuring consistent quality and properties of metal powder components can be challenging. |
Health and Safety Risks | Handling fine metal powders requires stringent safety measures to prevent inhalation and explosion hazards. |
Surface Finish | The surface finish of additively manufactured parts may require post-processing to meet standards. |
Addressing the Drawbacks:
- High Cost: While the initial cost of metal powders can be high, the overall savings from reduced waste and efficient manufacturing can offset these costs over time.
- Complex Process Control: Advanced technologies and precise control systems are necessary to maintain quality, but these can also drive innovation and improvements in manufacturing processes.
Specifications, Sizes, Grades, and Standards
Understanding the specifications, sizes, grades, and standards of metal powders is crucial for selecting the right material for specific aviation applications.
Specifications Table
Metal Powder | Available Sizes (μm) | Grades | Standards |
Titanium Alloy (Ti6Al4V) | 15-45, 45-90 | Grade 5, Grade 23 | ASTM F2924, AMS 4998 |
Aluminum Alloy (AlSi10Mg) | 20-63, 63-106 | 1.4301, 1.4307 | ISO 9001, AMS 4288 |
Nickel Alloy (Inconel 718) | 15-53, 53-150 | AMS 5662, AMS 5663 | ASTM F3055, AMS 5664 |
Cobalt Chrome (CoCrMo) | 10-45, 45-90 | ASTM F75, ASTM F1537 | ISO 5832-12, ASTM F799 |
Stainless Steel (316L) | 15-45, 45-105 | 1.4404, 1.4435 | ASTM F138, ASTM F139 |
Maraging Steel (MS1) | 10-45, 45-90 | 18Ni (300), Maraging 250 | AMS 6521, ASTM A538 |
Copper Alloy (CuCrZr) | 15-63, 63-150 | C18150, C18200 | ASTM B152, AMS 4596 |
Tungsten (W) | 10-50, 50-150 | W-1, W-2 | ASTM B777, ASTM F288 |
Magnesium Alloy (AZ91D) | 20-63, 63-150 | ASTM B93/B93M | ASTM B661 |
Hastelloy X | 15-45, 45-90 | AMS 5754, AMS 5587 | ASTM B435, ASTM B572 |
Key Insights:
- Standards: Adhering to recognized standards such as ASTM and AMS ensures the reliability and quality of metal powder components.
- Grades and Sizes: Different applications require specific powder sizes and grades to achieve optimal performance.
Suppliers and Pricing Details
Selecting the right supplier is crucial for obtaining high-quality metal powders. Here are some of the leading suppliers and an overview of pricing details.
Suppliers and Pricing Table
Supplier | Metal Powders Offered | Pricing (per kg) | Notes |
---|---|---|---|
Carpenter Technology | Titanium, Nickel, Cobalt, Stainless Steel | $200 – $500 | High-quality powders, extensive certification |
GKN Additive | Titanium, Aluminum, Stainless Steel | $150 – $400 | Innovative solutions, global supplier |
Höganäs AB | Stainless Steel, Copper, Cobalt | $100 – $350 | Leader in metal powder production, broad range |
LPW Technology | Titanium, Nickel, Aluminum | $250 – $600 | Specializes in additive manufacturing powders |
Sandvik Materials Technology | Stainless Steel, Nickel, Copper | $180 – $450 | High-performance materials, extensive R&D |
Tekna | Titanium, Aluminum, Nickel | $220 – $550 | Advanced plasma atomization technology |
Arcam AB (GE Additive) | Titanium, Cobalt, Nickel | $230 – $580 | Pioneer in electron beam melting technology |
Erasteel | Maraging Steel, Stainless Steel | $190 – $480 | Focus on high-performance steels |
Praxair Surface Technologies | Nickel, Cobalt, Stainless Steel | $210 – $500 | Comprehensive range of powder solutions |
Aubert & Duval | Nickel, Titanium, Aluminum | $240 – $620 | Premium powders for aerospace applications |
Supplier Insights:
- Carpenter Technology: Known for their high-quality powders and extensive certification, ensuring compliance with stringent aviation standards.
- GKN Additive: Offers innovative solutions and a broad range of metal powders suitable for various aviation applications.
Pros and Cons Comparison
When choosing metal powders for aviation, it’s essential to weigh the pros and cons of each option. Here’s a comparative analysis of some popular choices.
Pros and Cons Table
Metal Powder | Advantages | Disadvantages |
---|---|---|
Titanium Alloy (Ti6Al4V) | High strength-to-weight ratio, corrosion resistance | High cost, complex process control |
Aluminum Alloy (AlSi10Mg) | Lightweight, good thermal properties | Lower strength compared to other alloys |
Nickel Alloy (Inconel 718) | High temperature resistance, mechanical properties | Expensive, difficult to machine |
Cobalt Chrome (CoCrMo) | Wear resistance, biocompatibility | High cost, brittle |
Stainless Steel (316L) | Corrosion resistance, mechanical properties | Heavier than other options, moderate strength |
Maraging Steel (MS1) | High strength, toughness | Expensive, limited availability |
Copper Alloy (CuCrZr) | High thermal/electrical conductivity | Soft, prone to deformation |
Tungsten (W) | High density, melting point | Very heavy, difficult to process |
Magnesium Alloy (AZ91D) | Ultra-lightweight, machinability | Corrosion-prone, lower strength |
Hastelloy X | Oxidation resistance, high-temp strength | Very expensive, challenging to work with |
Insights from the Comparison:
- Titanium Alloys: Offer unmatched strength and corrosion resistance but come at a higher cost and require precise process control.
- Nickel Alloys: Excel in high-temperature environments but can be challenging and costly to machine.
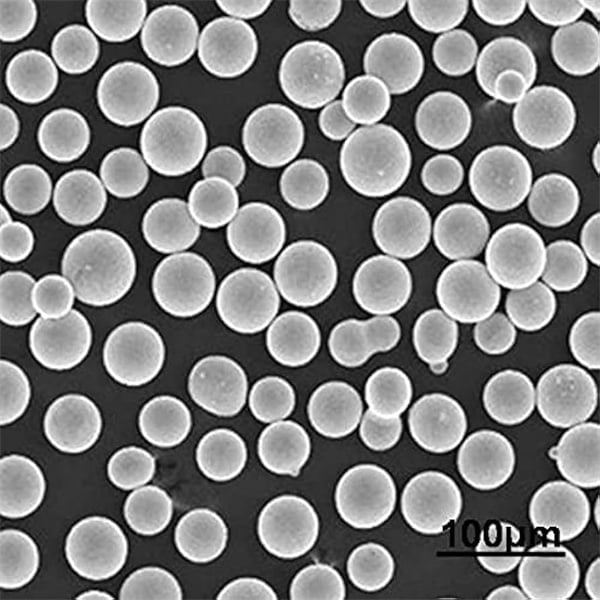
FAQ
To wrap things up, let’s address some common questions about metal powders for aviation.
Question | Answer |
---|---|
What are metal powders used for in aviation? | Metal powders are used for additive manufacturing, repairs, surface coatings, prototyping, and lightweight structures. |
Why are titanium alloys popular in aviation? | Titanium alloys offer a high strength-to-weight ratio and excellent corrosion resistance, making them ideal for structural components. |
What is additive manufacturing? | Additive manufacturing, or 3D printing, is a process of creating parts layer by layer using digital models, allowing for complex designs and material efficiency. |
Are metal powders safe to handle? | While metal powders can pose health and safety risks, proper handling and safety measures can mitigate these hazards. |
How does metal powder repair work? | Metal powder repair involves adding material to worn-out or damaged parts through techniques like laser cladding, extending the life of the components. |
What are the cost considerations for metal powders? | The cost of metal powders varies based on the material, production method, and quality. High-performance alloys tend to be more expensive. |
Can all metals be made into powders for aviation use? | Not all metals are suitable for powder production or aviation applications due to limitations in properties or manufacturing capabilities. |
What standards govern the use of metal powders in aviation? | Standards such as ASTM and AMS provide guidelines to ensure the quality and reliability of metal powder components used in aviation. |
What are the benefits of using metal powders for prototyping? | Metal powders enable rapid prototyping, allowing for quick testing of new designs and modifications without the need for traditional tooling. |
How do metal powders contribute to sustainability in aviation? | Metal powders reduce material waste, enable lightweight structures that save fuel, and can be recycled, contributing to a more sustainable aviation industry. |
Conclusion
Metal powders are transforming the aviation industry by enabling innovative manufacturing techniques, improving performance, and enhancing sustainability. From titanium alloys to nickel superalloys, each type of metal powder offers unique advantages and challenges. By understanding the properties, applications, and considerations of these materials, the aviation industry can continue to soar to new heights.
Share On
MET3DP Technology Co., LTD is a leading provider of additive manufacturing solutions headquartered in Qingdao, China. Our company specializes in 3D printing equipment and high-performance metal powders for industrial applications.
Inquiry to get best price and customized Solution for your business!
Related Articles
About Met3DP
Recent Update
Our Product
CONTACT US
Any questions? Send us message now! We’ll serve your request with a whole team after receiving your message.
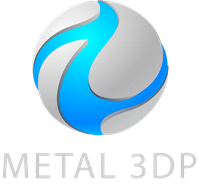
Metal Powders for 3D Printing and Additive Manufacturing