The Transformative Power of MIM Technology in Medical Devices
Table of Contents
Imagine a world where intricate, high-performance medical devices can be mass-produced with unparalleled precision and consistency. This is the reality ushered in by Metal Injection Molding (MIM), a revolutionary manufacturing process poised to redefine the landscape of medical technology.
What is MIM and How Does it Work?
Think of MIM as a marriage between the best aspects of plastic injection molding and traditional metalworking. Here’s a breakdown of the magic behind MIM:
- Powder Power: The process begins with a meticulously formulated metal powder, meticulously chosen based on the desired properties of the final product. We’ll delve deeper into specific metal powder options later.
- Binder Magic: This metal powder is then meticulously mixed with a binder, a polymer that acts as a glue, holding the individual metal particles together. The resulting mixture, called feedstock, has a consistency similar to playdough, allowing for precise shaping.
- Molding Marvel: The feedstock is then injected into a precisely designed mold cavity under high pressure, mimicking the process used for plastic injection molding. This incredible precision allows for the creation of complex geometries with intricate details.
- Debinding Drama: Once the molding is complete, the binder is meticulously removed through a thermal debinding process. This involves carefully heating the molded part in a controlled atmosphere, allowing the binder to volatilize (turn into gas) and escape, leaving behind a fragile metal skeleton.
- Sintering Symphony: The final step is a high-temperature sintering process. Here, the metal particles are heated to a temperature just below their melting point, causing them to fuse together and gain strength. This transforms the fragile metal skeleton into a robust, near-net-shape final product.
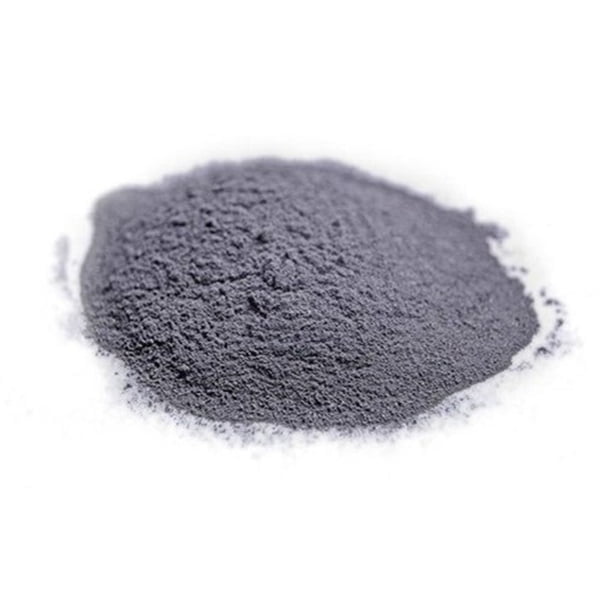
Choosing the Right Tool for the Job
The heart of MIM lies in the selection of the metal powder. Different metal powders offer a unique blend of properties, making them ideal for specific applications in medical devices. Here’s a glimpse into some of the most commonly used metal powders in MIM:
Common Metal Powders Used in MIM for Medical Devices
Metal Powder | Composition | Properties | Applications in Medical Devices |
---|---|---|---|
316L Stainless Steel | Fe (Iron), Cr (Chromium), Ni (Nickel), Mo (Molybdenum) | Excellent corrosion resistance, biocompatible, high strength | Bone screws, dental implants, surgical instruments |
17-4 PH Stainless Steel | Fe (Iron), Cr (Chromium), Ni (Nickel), Cu (Copper) | High strength, good ductility, good corrosion resistance | Springs, clips, gears, housings for implantable devices |
CoCrMo Alloy | Co (Cobalt), Cr (Chromium), Mo (Molybdenum) | Exceptional wear resistance, biocompatible | Hip and knee implant components |
Titanium (Ti) | Ti (Titanium) | Lightweight, high strength-to-weight ratio, excellent biocompatibility | Dental implants, bone screws, fracture fixation devices |
MP35N (Nitronic 60) | Fe (Iron), Cr (Chromium), Ni (Nickel), Mo (Molybdenum), N (Nitrogen) | High strength, excellent wear resistance, good corrosion resistance | Surgical instruments, bone fixation devices |
C40 (Carbon Steel) | Fe (Iron), C (Carbon) | Low cost, good machinability | Non-implantable medical device components, housings |
304L Stainless Steel | Fe (Iron), Cr (Chromium), Ni (Nickel) | Good corrosion resistance, biocompatible | Housings, connectors for medical devices |
Inconel 625 | Ni (Nickel), Cr (Chromium), Mo (Molybdenum), Fe (Iron) | Exceptional high-temperature performance, good corrosion resistance | Components for implantable devices exposed to high temperatures |
Hastelloy C-276 | Ni (Nickel), Mo (Molybdenum), Cr (Chromium), W (Tungsten) | Excellent corrosion resistance to a wide range of chemicals | Components for medical devices exposed to harsh chemical environments |
Tungsten (W) | W (Tungsten) | High density, exceptional X-ray opacity | Radiation shielding components in medical imaging equipment |
MIM’s Marvelous Advantages
MIM technology offers a compelling set of advantages that are revolutionizing the medical device industry:
- Unmatched Precision and Complexity: MIM allows for the creation of intricate geometries with tight tolerances that would be incredibly challenging or cost-prohibitive using traditional machining techniques. Imagine tiny gears, delicate lattice structures, and intricate internal channels – all achievable with MIM.
- Mass Production Prowess: Unlike traditional methods like machining, MIM excels at high-volume production. This translates to cost-effective manufacturing of complex medical devices, making them more accessible to patients.
- Material Magic: MIM offers a vast selection of metal powders, allowing for the creation of medical devices with precisely tailored properties. Need a biocompatible implant? 316L stainless steel or titanium might be your heroes. High wear resistance for a joint replacement? CoCrMo takes the stage. MIM puts the power of material selection at your fingertips.
- Design Freedom Unleashed: Gone are the limitations of traditional manufacturing. MIM’s ability to produce complex shapes unlocks a world of design possibilities for medical devices. Imagine lighter, more ergonomic surgical instruments or implants that mimic natural bone structures – all thanks to the design freedom offered by MIM.
- Strength in Small Packages: MIM excels at producing small, high-strength components. This makes it ideal for delicate medical devices like microfluidics for drug delivery or intricate components in pacemakers. Think of it as crafting robust parts in miniature, perfect for the intricate world of medical technology.
- Waste Not, Want Not: MIM is a remarkably efficient process, minimizing material waste compared to traditional machining techniques. This translates to cost savings and a more environmentally friendly manufacturing process, a win-win for both manufacturers and the environment.
MIM’s Considerations and Limitations
While MIM boasts a remarkable array of advantages, it’s important to acknowledge its limitations:
- Material Limitations: Not all metals are well-suited for MIM. Metals with high melting points or those that oxidize readily can be challenging to process using MIM.
- Surface Roughness: MIM-produced parts can have a slightly rougher surface finish compared to machined parts. This might not be ideal for applications requiring a perfectly smooth surface. However, post-processing techniques like polishing can help mitigate this limitation.
- Part Size Constraints: There are limitations on the size of parts that can be effectively produced using MIM. Very large or very small parts might be better suited for other manufacturing techniques.
- ** upfront Costs:** The initial setup costs for MIM can be higher compared to some traditional methods. However, these costs are often offset by the efficiency and cost-effectiveness of high-volume production using MIM.
MIM in Action: A Tour de Force in Medical Devices
MIM’s impact on the medical device industry is nothing short of transformative. Here are some captivating examples of how MIM is making a difference:
- Implants Taking Root: From biocompatible bone screws and dental implants to intricate components in knee and hip replacements, MIM is enabling the creation of longer-lasting, more durable implants that integrate seamlessly with the human body.
- Surgical Instruments with Finesse: Imagine delicate surgical instruments with intricate features, crafted for unparalleled precision and control. MIM makes this a reality, allowing surgeons to operate with unmatched dexterity and minimal invasiveness.
- The Heart of the Matter: MIM plays a vital role in the production of components for pacemakers, defibrillators, and other cardiac devices. Its ability to create miniature, high-precision parts is crucial for these life-saving technologies.
- A Brighter Future for Diagnostics: MIM is making waves in the world of medical diagnostics. Intricate microfluidic components for drug delivery systems and lab-on-a-chip devices are just a few examples of how MIM is driving innovation in diagnostics.
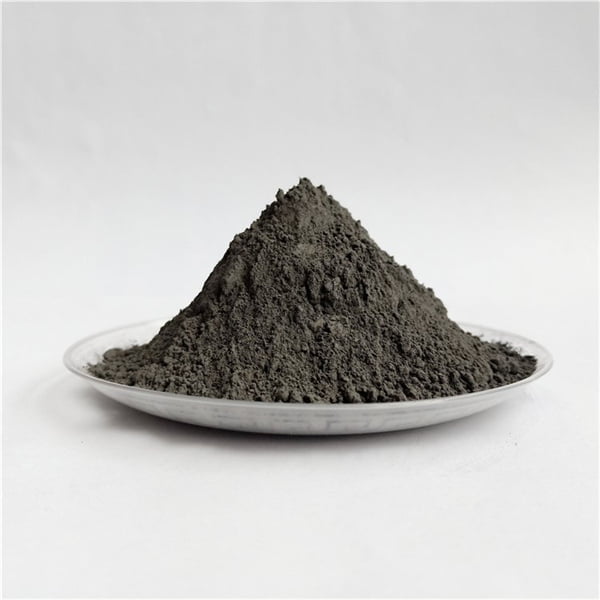
FAQ
Here are some of the most frequently asked questions about MIM technology:
Q: Is MIM safe for medical devices?
A: When used with appropriate biocompatible metal powders, MIM is perfectly safe for medical devices. The selection of the right metal powder is crucial, and rigorous testing ensures the safety and biocompatibility of MIM-produced medical devices.
Q: How strong are MIM parts?
A: MIM parts can be incredibly strong, depending on the chosen metal powder and the sintering process. MIM can achieve strength levels comparable to those of traditionally machined parts.
Q: What are the cost implications of MIM?
A: While upfront costs can be higher, MIM offers significant cost advantages in high-volume production. The efficiency of the process and minimal material waste contribute to its cost-effectiveness for mass-produced medical devices.
Q: Is MIM suitable for all medical devices?
A: MIM is best suited for small to medium-sized, complex medical devices requiring high precision and intricate geometries. For very large or very small parts, or those requiring an ultra-smooth surface finish, other manufacturing techniques might be more appropriate.
The Future of Medical Devices: Shaped by MIM
MIM technology is poised to play an even greater role in the future of medical devices. As the technology continues to evolve, we can expect to see even more intricate and sophisticated medical devices produced using MIM. This will lead to enhanced functionality, improved patient outcomes, and a new era of innovation in the medical device industry.
Share On
MET3DP Technology Co., LTD is a leading provider of additive manufacturing solutions headquartered in Qingdao, China. Our company specializes in 3D printing equipment and high-performance metal powders for industrial applications.
Inquiry to get best price and customized Solution for your business!
Related Articles
About Met3DP
Recent Update
Our Product
CONTACT US
Any questions? Send us message now! We’ll serve your request with a whole team after receiving your message.
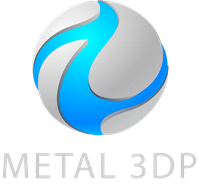
Metal Powders for 3D Printing and Additive Manufacturing