The Application of MIM Technology in the Aerospace Industry
Table of Contents
Imagine a world where crafting intricate, high-performance parts for airplanes wasn’t a race against weight and complexity. A world where near-net-shape manufacturing delivered the strength of metal with the precision of plastic. Enter Metal Injection Molding (MIM), a technological marvel quietly transforming the aerospace industry.
MIM Technology: A Bird’s-Eye View
MIM is a game-changer for aerospace manufacturers seeking a balance between lightweight design and unwavering strength. Think of it like baking a complex metal cake. Here’s the gist:
- Mixing the Batter: Metal powders, typically super alloys and stainless steels, are meticulously blended with a binder to create a feedstock with moldable properties.
- Shaping the Dough: The feedstock is injected into a precisely designed mold under high pressure, mimicking the intricate details of the desired part.
- Baking and Rising: The binder is removed through a thermal debinding process, leaving behind a fragile metal replica.
- Sintering for Strength: The remaining metal structure undergoes high-temperature sintering, transforming it into a robust and near-final shape.
Metal Powders: The Building Blocks of Flight
The success of MIM hinges on the type of metal powder used. Here’s a glimpse into some of the key players:
Stainless Steel Powders:
- 316L: The workhorse of stainless steels, offering excellent corrosion resistance and good formability (perfect for intricate parts).
- 17-4 PH: Boasts superior strength and hardness compared to standard stainless steels, ideal for parts enduring high stress.
Superalloy Powders:
- Inconel 625: Renowned for its exceptional resistance to high temperatures and harsh environments, making it a prime choice for jet engine components.
- Hastelloy X: Another champion in the fight against heat and corrosion, well-suited for parts exposed to extreme conditions.
- Nimonic 90: This nickel-chromium alloy shines in high-temperature applications due to its remarkable creep resistance (the ability to resist deformation under stress).
Titanium Powders:
- Grade 2: The go-to titanium powder for outstanding strength-to-weight ratio and good corrosion resistance, ideal for lightweight airframe components.
- Grade 6: Offers an enticing combination of strength, ductility (the ability to deform without breaking), and excellent corrosion resistance, making it versatile for various aerospace applications.
Other Notable Powders:
- Aluminum Alloys: These lightweight contenders bring significant weight savings, particularly beneficial for non-critical components.
- Tool Steels: Known for their exceptional wear resistance, these powders are used for molds and tooling within the MIM process itself.
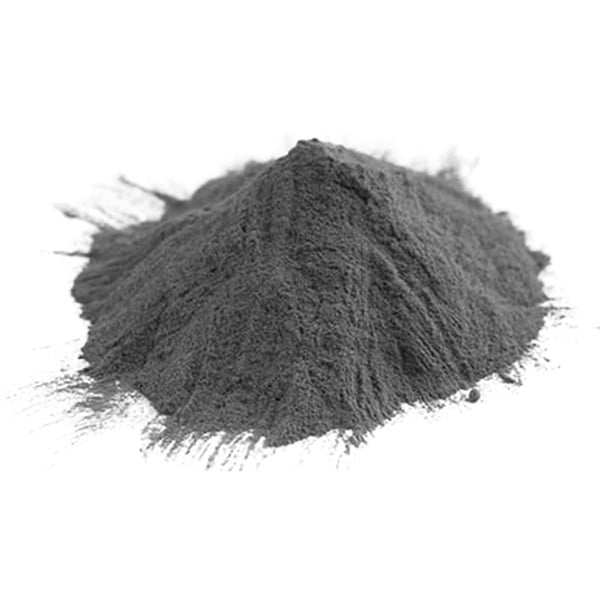
The Arsenal of MIM: A Look at Applications
MIM technology isn’t just about fancy materials; it’s about crafting crucial components that keep planes soaring. Here’s a peek at how MIM parts take flight:
Application | Benefits of Using MIM | Examples |
---|---|---|
Engine Components | MIM delivers intricate details and high-temperature resistance for parts like: | * Turbine blades * Guides * Nozzles * Combustor liners |
Fuel Systems | MIM ensures precision and leak-proof performance in components like: | * Injectors * Filters * Valves |
Landing Gear Systems | MIM offers lightweight and robust solutions for parts like: | * Actuator components * Bearings * Seals |
Flight Control Systems | MIM guarantees precise and reliable operation in parts like: | * Levers * Gears * Pulleys |
Other Applications | MIM’s versatility extends to: | * Fasteners (screws, nuts, bolts) * Housings * Brackets |
MIM vs. Traditional Manufacturing
The Battle for Lightweight Champions
When it comes to crafting intricate, high-performance parts for airplanes, both Metal Injection Molding (MIM) and traditional manufacturing methods like machining and casting vie for dominance. But which one reigns supreme? Here’s a quick breakdown to help you decide:
MIM: The Soaring Star
- Strengths:
- Complexity King: MIM excels at producing intricate shapes with minimal post-processing, ideal for lightweight, complex aerospace components.
- Material Marvel: Offers a vast array of metal powders, allowing parts to withstand extreme temperatures and harsh environments.
- Mass Production Powerhouse: Efficient for high-volume production, ensuring a steady supply of vital aircraft parts.
- Weaknesses:
- Cost Factor: Setting up an MIM line requires a high initial investment, impacting low-volume production costs.
- Material Matchmaker: Not all metals can be MIM-ed. Exotic alloys might require traditional methods.
- Size Constraints: Current limitations exist for part size, though technology is constantly evolving.
Traditional Manufacturing: The Established Fleet
- Strengths:
- Time-Tested Methods: Traditional methods like machining and casting have a long history of success in various applications.
- Material Flexibility: Can handle a wider range of materials compared to MIM.
- Economical for Small Batches: Often the more cost-effective option for low-volume or simple part production.
- Weaknesses:
- Complexity Challenge: Traditional methods struggle with intricate shapes, often requiring extensive machining, increasing cost and lead time.
- Material Waste: Significant material removal during machining leads to higher waste and potentially higher costs.
- Production Speed: Can be slower for complex parts compared to the high-volume efficiency of MIM.
The Verdict: It Depends on Your Flight Path
MIM shines for high-volume production of complex, lightweight parts where material properties are crucial. Traditional methods remain a strong choice for low-volume or simpler geometries and a wider range of materials. Ultimately, the best choice depends on your specific needs – part complexity, production volume, and material requirements.
The Advantages and Trade-offs of MIM: A Pilot’s Perspective
MIM’s impact on the aerospace industry soars high, but like any technology, it has its own flight pattern. Let’s delve into the compelling advantages and acknowledge the potential drawbacks to consider:
Soaring High with MIM: The Advantages
- Lightweight Champion: MIM parts boast exceptional strength-to-weight ratios, a crucial factor for fuel efficiency and overall aircraft performance. Imagine an airplane shedding pounds without sacrificing an ounce of strength – that’s the magic of MIM.
- Near-Net-Shape Prowess: MIM produces parts close to their final form, minimizing the need for extensive machining. This translates to faster production times, reduced material waste, and lower overall costs – a win-win for manufacturers and the environment.
- Design Freedom: MIM’s ability to handle complex geometries unlocks new design possibilities. Think intricate cooling channels in engine components or lightweight, high-strength brackets – MIM lets engineers push the boundaries of design without compromising functionality.
- Mass Production Powerhouse: For high-volume components, MIM shines. The streamlined process allows for rapid and consistent production, ensuring a steady supply of vital parts for aircraft assembly.
- Material Marvel: The vast array of metal powders available with MIM caters to a wide range of aerospace applications. Need a part that withstands scorching temperatures? Superalloy powders have you covered. Looking for lightweight efficiency? Aluminum alloys come to the rescue. MIM offers the perfect material match for each crucial component.
Turbulence Ahead: Considerations for MIM
- Material Limitations: While MIM boasts a diverse selection of metal powders, it can’t handle every material under the sun. Some exotic alloys or those with extremely high melting points might not be suitable for the MIM process.
- Upfront Investment: Setting up an MIM production line requires a significant initial investment. However, for high-volume production, the long-term cost savings often outweigh the upfront cost.
- Part Size Constraints: There are limitations to the size of parts that can be effectively produced using MIM. While the technology is constantly evolving, very large or very small parts might be better suited for traditional manufacturing methods.
- Surface Finish: MIM parts might require additional finishing processes to achieve a desired surface quality. This can add to the overall production time and cost.
Choosing the Right Path: When is MIM the Ideal Choice?
MIM isn’t a one-size-fits-all solution, but for specific scenarios, it takes flight beautifully. Here are some key factors to consider when deciding if MIM is the right choice for your aerospace application:
- Part Complexity: If your component boasts intricate shapes or internal features, MIM can be a lifesaver.
- Production Volume: For high-volume production runs, MIM’s efficiency and cost-effectiveness shine.
- Material Needs: If a suitable metal powder exists for your application, MIM offers exceptional material properties.
- Weight Constraints: When lightweight design is paramount, MIM’s strength-to-weight ratio is a game-changer.
The Future of Flight: The Sky’s the Limit for MIM
As the aerospace industry continues its relentless pursuit of efficiency and performance, MIM stands poised to play an even greater role. Here’s a glimpse into the exciting possibilities on the horizon:
- Advanced Powders: The development of new metal powders with even more extraordinary properties will push the boundaries of what’s achievable with MIM.
- Larger-Scale Production: Technological advancements promise to overcome current size limitations, allowing MIM to tackle even bigger aerospace components.
- Hybrid Manufacturing: Integrating MIM with other manufacturing processes like 3D printing could unlock entirely new design possibilities and production efficiencies.
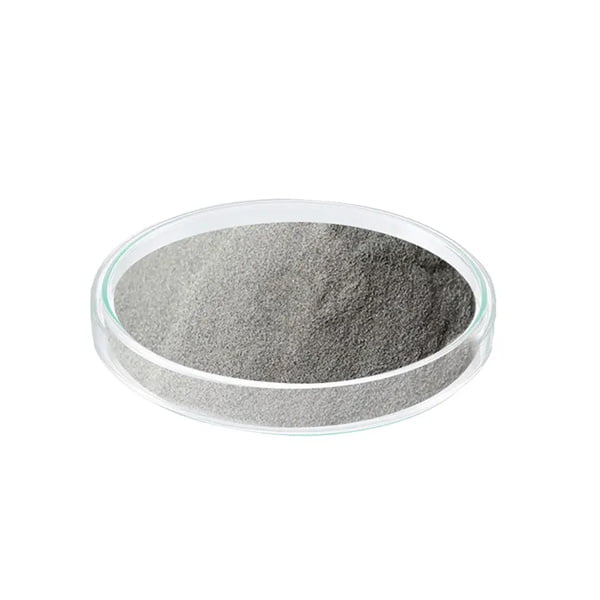
MIM in the Cockpit: A Pilot’s Final Thoughts
Metal Injection Molding isn’t just a fancy technology; it’s a revolution quietly taking place within the heart of the aerospace industry. By offering a unique blend of design freedom, weight savings, and high-performance materials, MIM is helping to build the next generation of lighter, stronger, and more fuel-efficient aircraft. As we continue to explore the potential of MIM, the future of flight looks brighter, lighter, and more innovative than ever before.
FAQ
Question | Answer |
---|---|
What are the size limitations of MIM parts? | Current limitations typically restrict MIM parts to a few centimeters in each dimension. However, advancements are constantly pushing these boundaries. |
Can MIM be used for all metals? | No, MIM is currently limited to specific metal powders with suitable properties for the molding process. |
How does the cost of MIM compare to traditional manufacturing? | The cost of MIM depends on production volume and part complexity. For high-volume, complex parts, MIM is generally more cost-effective than traditional methods due to efficiency and minimal waste. For low-volume, simple parts, traditional methods might be cheaper. |
Share On
MET3DP Technology Co., LTD is a leading provider of additive manufacturing solutions headquartered in Qingdao, China. Our company specializes in 3D printing equipment and high-performance metal powders for industrial applications.
Inquiry to get best price and customized Solution for your business!
Related Articles
About Met3DP
Recent Update
Our Product
CONTACT US
Any questions? Send us message now! We’ll serve your request with a whole team after receiving your message.
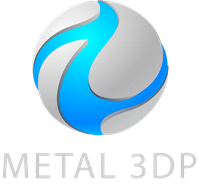
Metal Powders for 3D Printing and Additive Manufacturing