Molten Metal Deposition (MMD)
Table of Contents
Molten Metal Deposition (MMD) is a fascinating and innovative process revolutionizing the world of manufacturing and materials science. Whether you’re a seasoned engineer, an aspiring inventor, or simply curious about the latest technological advancements, this guide will take you through everything you need to know about MMD. From the basics to specific metal powder models, applications, and more, let’s dive into the molten world of metal deposition.
Overview of Molten Metal Deposition (MMD)
Molten Metal Deposition (MMD) is an additive manufacturing process that involves the precise deposition of molten metal onto a substrate to create intricate and high-strength components. This technology is gaining traction due to its ability to produce complex geometries, reduce material waste, and enhance the mechanical properties of the final product. MMD is utilized in various industries, including aerospace, automotive, and medical devices, due to its versatility and efficiency.
Types, Composition, Properties, and Characteristics of Metal Powders for MMD
Understanding the different types of metal powders used in MMD is crucial for selecting the right material for your project. Here’s a detailed look at some specific metal powder models, their composition, properties, and characteristics:
Metal Powder Model | Composition | Properties | Characteristics |
---|---|---|---|
Inconel 718 | Nickel, Chromium, Iron | High strength, Corrosion-resistant | Ideal for high-temperature applications |
Stainless Steel 316L | Iron, Chromium, Nickel, Molybdenum | Excellent corrosion resistance, High ductility | Widely used in medical and marine applications |
Aluminum 6061 | Aluminum, Magnesium, Silicon | Lightweight, High strength-to-weight ratio | Common in aerospace and automotive industries |
Titanium Ti-6Al-4V | Titanium, Aluminum, Vanadium | Exceptional strength, Low density | Perfect for aerospace and biomedical implants |
Copper C18150 | Copper, Chromium | High electrical and thermal conductivity | Used in electrical components and heat exchangers |
Cobalt-Chrome (CoCr) | Cobalt, Chromium, Molybdenum | High wear resistance, Biocompatible | Ideal for dental and orthopedic implants |
Tool Steel H13 | Iron, Carbon, Chromium, Vanadium | High hardness, Thermal fatigue resistance | Suitable for die-casting and extrusion dies |
Nickel Alloy 625 | Nickel, Chromium, Molybdenum, Niobium | High corrosion and oxidation resistance | Used in marine and chemical processing |
Maraging Steel (18Ni300) | Iron, Nickel, Cobalt, Molybdenum | High tensile strength, Easy to machine | Utilized in aerospace and tooling applications |
Bronze Alloy (CuSn12) | Copper, Tin | Good machinability, High wear resistance | Common in bearings and bushings |
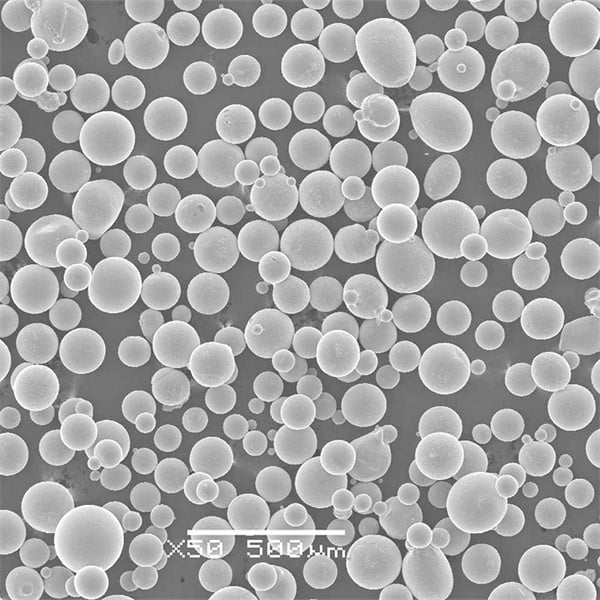
Applications of Molten Metal Deposition (MMD)
Molten Metal Deposition has a wide range of applications due to its flexibility and capability to create complex structures. Let’s explore some of the key areas where MMD is making a significant impact:
Industry | Application | Benefits |
---|---|---|
Aerospace | Turbine blades, structural components | High strength, lightweight, complex geometries |
Automotive | Engine parts, exhaust systems, chassis | Reduced weight, improved performance |
Medical Devices | Orthopedic implants, dental restorations | Biocompatibility, customized fit |
Electronics | Heat sinks, connectors, circuit boards | Enhanced thermal management, precision |
Oil and Gas | Drilling tools, valves, pump components | Corrosion resistance, durability |
Construction | Structural elements, customized fittings | Strength, adaptability to design changes |
Jewelry | Intricate designs, customized pieces | High detail, material versatility |
Energy | Turbine components, solar panel frames | Efficiency, resilience in harsh conditions |
Defense | Lightweight armor, weapon components | High strength, reliability |
Marine | Propellers, hull components, underwater equipment | Corrosion resistance, longevity |
Specifications, Sizes, Grades, and Standards of Metal Powders
When it comes to MMD, having detailed information on the specifications, sizes, grades, and standards of metal powders is essential for achieving optimal results. Here’s a comprehensive table to guide you:
Metal Powder | Particle Size Range (µm) | Grade | Standard |
---|---|---|---|
Inconel 718 | 15-45 | Aerospace Grade | ASTM B637 |
Stainless Steel 316L | 20-50 | Medical Grade | ASTM F138, F139 |
Aluminum 6061 | 15-63 | Industrial Grade | ASTM B209 |
Titanium Ti-6Al-4V | 15-45 | Medical/Aerospace Grade | ASTM F1472, F2924 |
Copper C18150 | 20-60 | Electrical Grade | ASTM B224 |
Cobalt-Chrome (CoCr) | 10-45 | Medical Grade | ASTM F75, F1537 |
Tool Steel H13 | 20-53 | Tooling Grade | ASTM A681 |
Nickel Alloy 625 | 15-45 | Marine/Industrial Grade | ASTM B443 |
Maraging Steel (18Ni300) | 10-45 | Aerospace Grade | AMS 6521 |
Bronze Alloy (CuSn12) | 20-60 | Industrial Grade | ASTM B427 |
Suppliers and Pricing Details of Metal Powders for MMD
Finding reliable suppliers and understanding the pricing of metal powders is crucial for budgeting and planning your MMD projects. Here’s a table to help you get started:
Supplier | Metal Powder | Price per kg (USD) | Location | Website |
---|---|---|---|---|
Höganäs | Inconel 718 | $80-$100 | Sweden | www.hoganas.com |
Carpenter | Stainless Steel 316L | $50-$70 | USA | www.carpentertechnology.com |
AP&C | Aluminum 6061 | $30-$50 | Canada | www.advancedpowders.com |
TLS Technik | Titanium Ti-6Al-4V | $200-$300 | Germany | www.tls-technik.de |
GKN Additive | Copper C18150 | $20-$40 | UK | www.gknadditive.com |
Sandvik Osprey | Cobalt-Chrome (CoCr) | $150-$250 | Sweden | www.materials.sandvik |
Uddeholm | Tool Steel H13 | $70-$90 | Sweden | www.uddeholm.com |
VDM Metals | Nickel Alloy 625 | $100-$150 | Germany | www.vdm-metals.com |
Kennametal | Maraging Steel (18Ni300) | $120-$160 | USA | www.kennametal.com |
Kymera International | Bronze Alloy (CuSn12) | $25-$45 | USA | www.kymerainternational.com |
Pros and Cons of Molten Metal Deposition (MMD)
As with any technology, MMD has its advantages and limitations. Let’s compare them to give you a balanced perspective:
Advantages | Disadvantages |
---|---|
High Precision: Ability to create complex geometries with high accuracy. | Cost: Initial setup and material costs can be high. |
Material Efficiency: Reduces waste compared to traditional methods. | Speed: Deposition rates can be slower compared to some manufacturing methods. |
Strength and Durability: Produces parts with superior mechanical properties. | Complexity: Requires specialized equipment and expertise. |
Versatility: Can work with a wide range of metal powders. | Post-processing: May require additional finishing processes. |
Customization: Ideal for producing customized and intricate designs. | Size Limitations: Not suitable for extremely large components. |
Application-Specific Insights: MMD in Various Industries
Aerospace Industry
In the aerospace industry, MMD is a game-changer. Turbine blades, structural components, and other critical parts are manufactured with unprecedented precision and strength. The high strength-to-weight ratio of materials like Titanium Ti-6Al-4V and Inconel 718 makes them ideal for aerospace applications. These materials ensure that the components can withstand extreme temperatures and stress while maintaining lightweight properties crucial for flight efficiency.
Automotive Industry
The automotive industry benefits significantly from MMD, particularly in the production of engine parts, exhaust systems, and chassis
components. Aluminum 6061, with its high strength-to-weight ratio and excellent machinability, is frequently used. This not only reduces the weight of the vehicle, improving fuel efficiency, but also enhances the performance and longevity of the parts.
Medical Devices
In the realm of medical devices, the ability to create biocompatible and customized implants is invaluable. Stainless Steel 316L and Cobalt-Chrome are popular choices due to their corrosion resistance and biocompatibility. MMD allows for the production of orthopedic implants and dental restorations tailored to the patient’s anatomy, improving outcomes and reducing recovery times.
Comparing Metal Powders for MMD: Pros and Cons
Each metal powder used in MMD has its own set of pros and cons. Let’s break down some of the key differences:
Metal Powder | Pros | Cons |
---|---|---|
Inconel 718 | High temperature resistance, excellent strength | Expensive, difficult to machine |
Stainless Steel 316L | Excellent corrosion resistance, good ductility | Lower strength compared to other alloys |
Aluminum 6061 | Lightweight, high strength-to-weight ratio | Lower melting point, less wear resistance |
Titanium Ti-6Al-4V | Exceptional strength, low density | Very expensive, challenging to work with |
Copper C18150 | High electrical and thermal conductivity | Lower mechanical strength, prone to oxidation |
Cobalt-Chrome (CoCr) | High wear resistance, biocompatible | High cost, difficult to machine |
Tool Steel H13 | High hardness, thermal fatigue resistance | Prone to corrosion, high cost |
Nickel Alloy 625 | Excellent corrosion and oxidation resistance | Expensive, difficult to machine |
Maraging Steel (18Ni300) | High tensile strength, easy to machine | Expensive, limited availability |
Bronze Alloy (CuSn12) | Good machinability, high wear resistance | Lower strength, not suitable for high-stress applications |
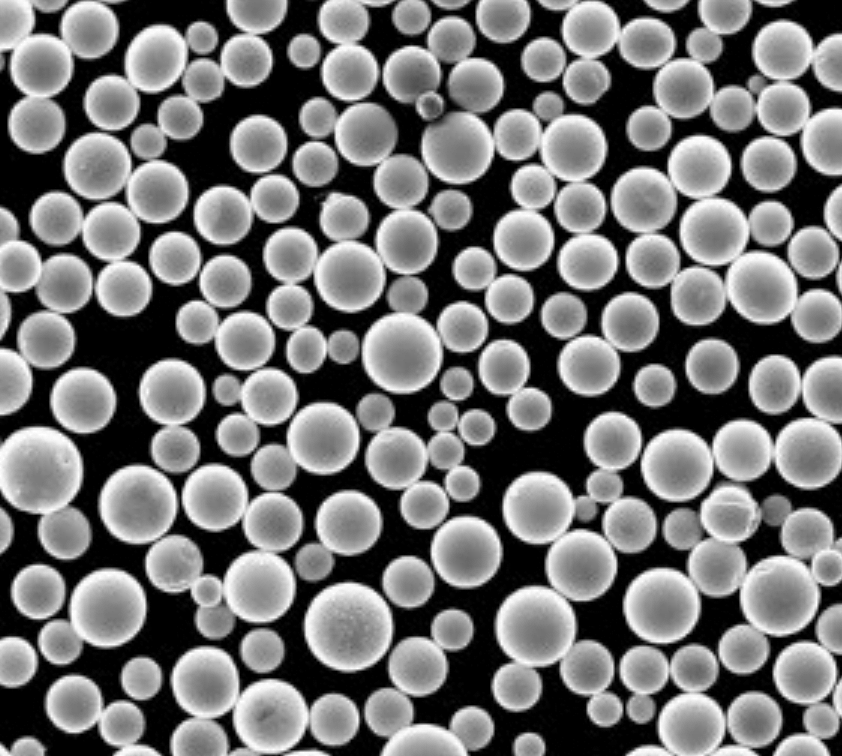
FAQ
Question | Answer |
---|---|
What is Molten Metal Deposition (MMD)? | MMD is an additive manufacturing process that involves depositing molten metal onto a substrate to create complex and high-strength components. |
What metals can be used in MMD? | A wide range of metals can be used, including Inconel 718, Stainless Steel 316L, Aluminum 6061, Titanium Ti-6Al-4V, and more. |
What are the advantages of MMD? | MMD offers high precision, material efficiency, superior mechanical properties, versatility, and the ability to produce customized designs. |
What industries benefit from MMD? | Aerospace, automotive, medical devices, electronics, oil and gas, construction, jewelry, energy, defense, and marine industries all benefit from MMD. |
What are the limitations of MMD? | MMD can be costly, slower than some methods, requires specialized equipment and expertise, may need post-processing, and has size limitations. |
How does MMD compare to other manufacturing methods? | MMD provides higher precision and material efficiency but can be more expensive and slower compared to some traditional manufacturing methods. |
What are the costs associated with MMD? | Costs include the initial setup, material costs, and potential post-processing requirements. Metal powder prices vary depending on the type and supplier. |
Is MMD suitable for large-scale production? | MMD is more suitable for small to medium-sized components and customized production rather than large-scale manufacturing due to size and speed limitations. |
Can MMD be used for prototyping? | Yes, MMD is ideal for prototyping as it allows for the creation of complex and customized designs quickly and efficiently. |
What safety measures are needed for MMD? | Proper ventilation, protective equipment, and training are essential to ensure safety when handling molten metals and operating MMD equipment. |
Conclusion
Molten Metal Deposition (MMD) is a transformative technology that is shaping the future of manufacturing. With its ability to create complex, high-strength components with minimal waste, MMD is revolutionizing various industries. By understanding the types, properties, and applications of different metal powders, you can leverage this technology to its full potential. Whether you’re looking to improve performance, reduce costs, or innovate your products, MMD offers a versatile and efficient solution.
Share On
MET3DP Technology Co., LTD is a leading provider of additive manufacturing solutions headquartered in Qingdao, China. Our company specializes in 3D printing equipment and high-performance metal powders for industrial applications.
Inquiry to get best price and customized Solution for your business!
Related Articles
About Met3DP
Recent Update
Our Product
CONTACT US
Any questions? Send us message now! We’ll serve your request with a whole team after receiving your message.
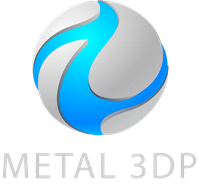
Metal Powders for 3D Printing and Additive Manufacturing