Molybdenum Powder
Table of Contents
Molybdenum powder, a fine and versatile material, plays a crucial role in shaping the world around us. Imagine the searing heat in a jet engine or the pressure within a deep-sea oil rig. Molybdenum powder is there, standing strong and resilient in these extreme environments. But what exactly is molybdenum powder, and how does it achieve such remarkable feats? Buckle up, because we’re diving deep into the fascinating world of this metallic marvel.
An Overview of Molybdenum Powder
Molybdenum powder is a finely divided form of the element molybdenum (Mo). It’s like taking a lump of molybdenum and grinding it down into microscopic particles, each boasting a vast surface area. This increased surface area unlocks a treasure trove of properties that make molybdenum powder invaluable in various industrial applications.
Molybdenum itself is a transition metal renowned for its exceptional strength, high melting point, and impressive resistance to corrosion. When transformed into a powder, these properties are amplified, making it a perfect candidate for applications requiring these characteristics.
Here’s a quick peek at what makes molybdenum powder so special:
- High Melting Point: Molybdenum powder boasts a melting point exceeding 2623°C (4753°F), allowing it to withstand extreme temperatures encountered in furnaces, rocket engines, and other high-heat environments.
- Superior Strength: Even in finely divided form, molybdenum powder retains its remarkable strength. This makes it ideal for strengthening alloys and composite materials.
- Excellent Corrosion Resistance: Molybdenum powder is a champion against corrosion, especially at high temperatures. This property makes it perfect for protecting critical components in harsh environments like chemical plants and seawater applications.
- High Electrical Conductivity: Molybdenum powder conducts electricity efficiently, making it a valuable player in electronic applications.
These are just a few of the key characteristics that make molybdenum powder an irreplaceable material in various industries. But to truly understand its power, we need to delve deeper and explore the different types available.
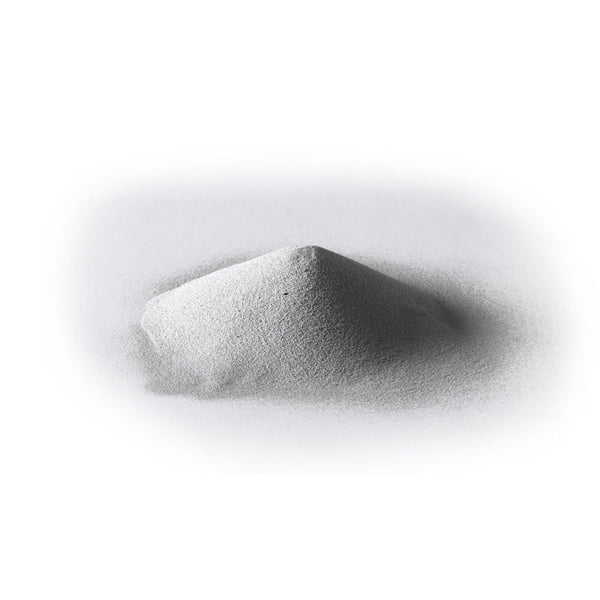
the Diverse Landscape of Molybdenum Powders
The world of molybdenum powder isn’t a one-size-fits-all situation. Manufacturers offer a variety of types, each tailored for specific applications. Here’s a closer look at ten prominent molybdenum powder models:
- Reduced Ammonium Paramolybdate (RAP) Powder: This widely used type is produced by reducing ammonium paramolybdate with hydrogen. RAP powder offers a high degree of purity (often exceeding 99.5%) and boasts a fine particle size, making it ideal for powder metallurgy applications and electronic components.
- Hydrogen Reduced Molybdenum Oxide (H-MoO2) Powder: This powder is obtained by reducing molybdenum trioxide (MoO3) with hydrogen. H-MoO2 powder offers excellent electrical conductivity and high surface area, making it perfect for electrical contacts and applications requiring good sinterability (the ability to form a solid mass during heating).
- Carbonyl Molybdenum Powder (CM Powder): This unique type is produced by the decomposition of molybdenum carbonyl. CM powder boasts a spherical shape and exceptional purity, making it ideal for high-performance applications like filaments in lighting and heating elements. Imagine the tiny filaments glowing brightly in your halogen lamps – that could very well be CM powder at work!
- Atomized Molybdenum Powder: This type is created by rapidly melting molybdenum and then atomizing the molten metal with a high-pressure gas stream. The resulting powder boasts a spherical shape and a broad particle size distribution, making it suitable for various applications like thermal spraying (coating surfaces for protection) and additive manufacturing (creating 3D objects layer by layer).
- Electrolytic Molybdenum Powder: This variety is produced by electrolyzing molybdenum salts. Electrolytic molybdenum powder offers a high degree of purity and a controlled particle size distribution, making it perfect for electronic applications and friction materials (materials used in brakes and clutches).
- Molybdenum Carbide Powder (Mo2C) Powder: This type is a combination of molybdenum and carbon. Mo2C powder offers exceptional hardness and wear resistance, making it ideal for cutting tools and wear parts. Think of those drill bits biting through tough materials – Mo2C powder could be the secret ingredient behind their impressive performance.
- Molybdenum Disilicide Powder (MoSi2) Powder: This powder combines molybdenum and silicon. MoSi2 powder boasts excellent high-temperature strength and oxidation resistance, making it a valuable material for heating elements and furnace components.
- Nickel-Molybdenum (NiMo) Powder: This blend combines molybdenum with nickel. NiMo powder offers a good balance of strength and ductility (the ability to deform without breaking), making it perfect for high-temperature applications like gas turbine blades.
- Copper-Molybdenum (CuMo) Powder: This type mixes molybdenum with copper. CuMo powder offers improved thermal conductivity (the ability to transfer heat) compared to pure molybdenum powder, making it ideal for heat sinks and electronic packaging applications. Imagine those sleek heat sinks on your computer – CuMo powder could be helping keep things cool!
Table 1: Key Characteristics of Molybdenum Powder Models
Molybdenum Powder Model | Production Method | Key Characteristics | Typical Applications |
---|---|---|---|
Reduced Ammonium Paramolybdate (RAP) Powder | Reduction of Ammonium Paramolybdate with Hydrogen | High Purity, Fine Particle Size | Powder Metallurgy, Electronic Components |
Hydrogen Reduced Molybdenum Oxide (H-MoO2) Powder | Reduction of Molybdenum Trioxide with Hydrogen | Excellent Electrical Conductivity, High Surface Area | Electrical Contacts, Sintering Applications |
Carbonyl Molybdenum Powder (CM Powder) | Decomposition of Molybdenum Carbonyl | Spherical Shape, Exceptional Purity | High-Performance Filaments, Lighting Elements |
Atomized Molybdenum Powder | Rapid Melting and Gas Atomization | Spherical Shape, Broad Particle Size Distribution | Thermal Spraying, Additive Manufacturing |
Electrolytic Molybdenum Powder | Electrolysis of Molybdenum Salts | High Purity, Controlled Particle Size Distribution | Electronic Applications, Friction Materials |
Molybdenum Carbide Powder (Mo2C) Powder | Combination of Molybdenum and Carbon | Exceptional Hardness, Wear Resistance | Cutting Tools, Wear Parts |
Molybdenum Disilicide Powder (MoSi2) Powder | Combination of Molybdenum and Silicon | High-Temperature Strength, Oxidation Resistance | Heating Elements, Furnace Components |
Nickel-Molybdenum (NiMo) Powder | Blend of Molybdenum and Nickel | Balanced Strength and Ductility | Gas Turbine Blades, High-Temperature Applications |
Copper-Molybdenum (CuMo) Powder | Blend of Molybdenum and Copper | Improved Thermal Conductivity | Heat Sinks, Electronic Packaging |
Understanding the Nuances: A Look at Properties and Applications
Now that we’ve explored the different types of molybdenum powder, let’s delve deeper into their properties and applications. Here’s a breakdown to shed light on how these versatile powders are utilized across various industries:
Table 2: Properties and Applications of Molybdenum Powder
Property | Description | Example Applications |
---|---|---|
High Melting Point | Withstands extreme temperatures | Furnace Linings, Rocket Engine Components |
Superior Strength | Enhances the strength of materials | Alloying Agent in Steels, Superalloys |
Excellent Corrosion Resistance | Protects against degradation | Chemical Processing Equipment, Marine Applications |
High Electrical Conductivity | Efficiently conducts electricity | Electrical Contacts, Heat Sinks |
Fine Particle Size | Offers a large surface area | Catalyst Supports, Powder Metallurgy Processes |
Spherical Shape | Enables good flowability | Thermal Spraying Powders, Additive Manufacturing Feedstock |
This table provides a glimpse into the diverse applications of molybdenum powder. From the fiery depths of furnaces to the intricate world of electronics, molybdenum powder plays a crucial role in shaping our technological landscape.
Meeting Specific Needs: Specifications, Sizes, and Grades
The world of molybdenum powder isn’t a one-size-fits-all situation. To cater to specific needs, manufacturers offer various specifications, sizes, and grades. Here’s a breakdown to help you navigate this aspect:
Table 3: Specifications, Sizes, and Grades of Molybdenum Powder
Specification | Description | Importance |
---|---|---|
Purity | Percentage of Molybdenum in the Powder | Affects performance in applications like electrical conductivity |
Particle Size | Measured in microns (µm) or mesh size | Fine powders offer a larger surface area for reactions, while coarser powders are better for thermal spraying |
Apparent Density | The bulk density of the powder | Impacts how much powder can be packed into a specific volume |
Flowability | How easily the powder flows | Critical for efficient use in automated processes |
Oxygen Content | The amount of oxygen present in the powder | Affects the mechanical properties and sinterability of the powder |
Finding the Right Supplier: A Look at Options and Pricing
With a plethora of molybdenum powder manufacturers and suppliers, choosing the right one can be daunting. Here are some key factors to consider:
Factor | Description | Importance |
---|---|---|
Reputation | The supplier’s track record for quality and consistency | Ensures you receive reliable and high-performance powder |
Product Range | The variety of molybdenum powder types offered | Provides options to meet specific application needs |
Customization Options | The ability to tailor powder properties to specific requirements | Allows for fine-tuning performance for optimal results |
Pricing | The cost of the molybdenum powder | Consider cost in relation to quality and desired performance |
Delivery Times | The timeframe for receiving the powder | Impacts production schedules and project timelines |
Minimum Order Quantities | The minimum amount of powder that can be purchased | May influence purchasing decisions for smaller projects |
Beyond the Basics: Advantages and Limitations
Molybdenum powder boasts a treasure trove of advantages that make it a highly sought-after material. Here’s a closer look:
Table 5: Advantages of Molybdenum Powder
Advantage | Description | Benefit |
---|---|---|
Exceptional Strength | Offers superior strength even in fine particle form | Strengthens alloys and composites |
High Melting Point | Can withstand extreme temperatures | Ideal for high-heat environments like furnaces and rocket engines |
Excellent Corrosion Resistance | Resists degradation at high temperatures | Protects critical components in harsh environments |
High Electrical Conductivity | Conducts electricity efficiently | Valuable for electrical applications |
Fine Particle Size | Provides a large surface area | Enhances performance in applications like catalysis |
Spheroidal Shape (for specific types) | Improves flowability and packing density | Benefits thermal spraying and additive manufacturing processes |
However, like any material, molybdenum powder also has limitations to consider:
Table 6: Limitations of Molybdenum Powder
Limitation | Description | Impact |
---|---|---|
Relatively High Cost | Can be more expensive compared to some other metal powders | May influence cost-sensitive applications |
Oxidation Potential | Can oxidize at high temperatures | May require use in controlled atmospheres or coatings for high-temperature applications |
Brittleness (for some types) | Certain types may be brittle | May not be suitable for applications requiring high ductility |
By understanding both the advantages and limitations of molybdenum powder, you can make informed decisions about its suitability for your specific needs.
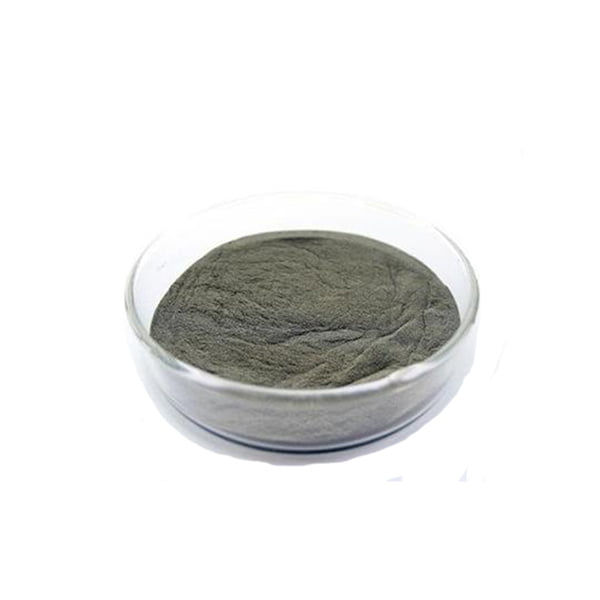
FAQ
Here are some frequently asked questions regarding molybdenum powder, presented in a clear and informative table format:
Table 7: Molybdenum Powder FAQ
Question | Answer |
---|---|
What is molybdenum powder used for? | Molybdenum powder finds applications in various industries, including metallurgy (strengthening alloys), electronics (electrical contacts and heat sinks), high-temperature applications (furnace linings and rocket engine components), and more. |
What are the different types of molybdenum powder? | Several types of molybdenum powder exist, each with unique properties. Common varieties include reduced ammonium paramolybdate (RAP), hydrogen reduced molybdenum oxide (H-MoO2), carbonyl molybdenum powder (CM), and atomized molybdenum powder. |
What are the key factors to consider when choosing molybdenum powder? | Consider factors like purity, particle size, apparent density, flowability, oxygen content, supplier reputation, product range, customization options, pricing, delivery times, and minimum order quantities. |
What are the advantages of molybdenum powder? | Molybdenum powder offers exceptional strength, a high melting point, excellent corrosion resistance, high electrical conductivity, and a large surface area (for fine particle sizes). Spherical shapes (in some types) improve flowability and packing density. |
What are the limitations of molybdenum powder? | Molybdenum powder can be relatively expensive compared to some other metal powders. It can also oxidize at high temperatures and may exhibit brittleness (depending on the type). |
Conclusion: The Mighty Molybdenum Powder
Molybdenum powder, often the unsung hero in the world of materials, plays a crucial role in shaping our technological advancements. From the searing heat of a jet engine to the intricate world of electronics, molybdenum powder quietly stands strong, delivering exceptional performance and resilience. By understanding the different types, properties, applications, and considerations surrounding molybdenum powder, you can leverage its potential to achieve remarkable results in your projects.
Share On
MET3DP Technology Co., LTD is a leading provider of additive manufacturing solutions headquartered in Qingdao, China. Our company specializes in 3D printing equipment and high-performance metal powders for industrial applications.
Inquiry to get best price and customized Solution for your business!
Related Articles
About Met3DP
Recent Update
Our Product
CONTACT US
Any questions? Send us message now! We’ll serve your request with a whole team after receiving your message.
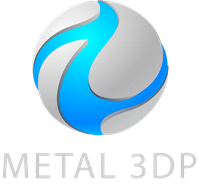
Metal Powders for 3D Printing and Additive Manufacturing