MS1(1.2709) Metal Powder
Table of Contents
Metal injection molding (MIM) has revolutionized the manufacturing industry, enabling the creation of complex, near-net-shape metal parts with exceptional precision and detail. But this transformative technology relies heavily on a crucial ingredient: metal powder. And when it comes to MIM, MS1(1.2709) Metal Powder stands out as a champion, offering a unique blend of properties that elevate the MIM process to new heights.
Understanding MS1(1.2709) Metal Powder
MS1(1.2709) powder is a gas-atomized, low-alloy steel powder specifically designed for MIM applications. It boasts a chemical composition of approximately 0.10% carbon (C), 0.40% manganese (Mn), 1.00% molybdenum (Mo), and 0.04% sulfur (S), with the balance being iron (Fe). This specific composition grants MS1(2.709) a remarkable set of characteristics that make it a perfect partner for MIM.
Properties and Benefits of MS1(1.2709) Powder for MIM
Property | Benefit for MIM |
---|---|
Fine Particle Size and Spherical Morphology | Excellent flowability for uniform feedstock |
High Powder Packing Density | Minimizes shrinkage and distortion during sintering |
Controlled Chemistry | Consistent material properties in final parts |
Good Sintering Response | Achieves high strength and density after sintering |
Excellent Machinability | Enables post-processing for tight tolerances |
Let’s delve deeper into how these properties translate to advantages in the MIM process.
- Flawless Flowability: MS1(1.2709) powder boasts a fine particle size and a near-spherical morphology. This translates to exceptional flowability, ensuring a smooth and consistent feedstock during injection molding. Imagine pouring honey – that’s the kind of flow you want in your MIM feedstock. Smooth flow guarantees uniform filling of the mold cavity, minimizing defects and inconsistencies in the final part.
- Packing Powerhouse: High packing density is another key benefit of MS1(1.2709) powder. During MIM, the powder particles pack tightly together, minimizing the amount of empty space within the mold cavity. This dense packing reduces shrinkage and distortion during the high-temperature sintering stage, leading to dimensionally accurate and predictable final parts. Think of it like packing suitcases for a trip – you want to maximize the space used to minimize wasted volume. In MIM, dense packing translates to less shrinkage and more precise parts.
- Chemistry in Control: The controlled chemistry of MS1(1.2709) powder ensures consistent material properties in the final MIM parts. This means you can predict and rely on the mechanical performance of your components with confidence. Imagine baking a cake – a precisely measured recipe guarantees consistent results every time. Similarly, the controlled chemistry of MS1(1.2709) ensures predictable and reliable performance in your MIM parts.
- Sintering Strength: MS1(1.2709) powder exhibits an excellent response to the sintering process. Sintering is the high-temperature stage where the powder particles bond together to form a solid metal structure. MS1(1.2709) sinters effectively, achieving high strength and density in the final part. Imagine building a house of cards – with weak materials, the structure crumbles easily. But strong, well-bonded powder particles, like those in MS1(1.2709), create a robust and dependable final product.
- Machinability Magic: After sintering, MS1(1.2709) parts boast excellent machinability. This allows for precise post-processing to achieve tight tolerances and intricate features. Think of shaping clay on a potter’s wheel – the excellent machinability of MS1(2.709) allows for similar shaping and refinement of the MIM parts.
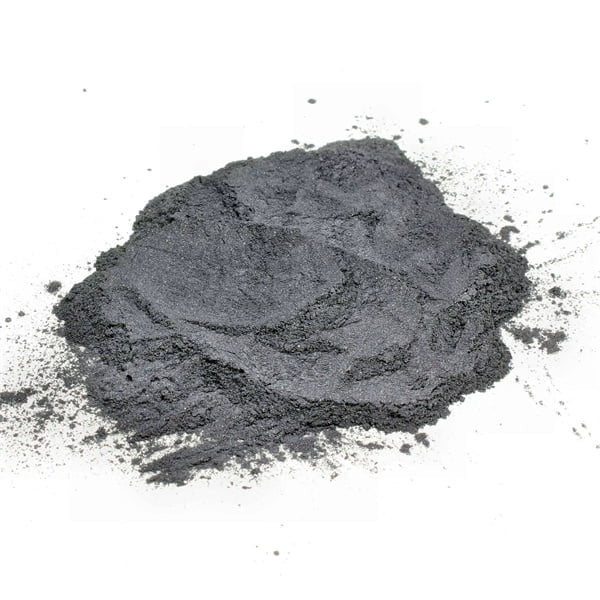
Metal Powder Options for MIM
While MS1(1.2709) shines as a versatile and high-performing metal powder for MIM, it’s not the only player in the game. Here’s a glimpse into a wider selection of metal powders used in MIM, each with its own strengths and applications:
- 316L Stainless Steel: A popular choice for applications requiring corrosion resistance, 316L stainless steel powder offers excellent biocompatibility, making it ideal for medical implants.
- 17-4 PH Stainless Steel: Known for its high strength and good machinability, 17-4 PH stainless steel powder is often used in aerospace and automotive components.
- Inconel 625: Offering exceptional heat and corrosion resistance, Inconel 625 powder is a go-to choice for high-temperature applications like jet engine components.
- Titanium Grade 2: For applications demanding a lightweight yet strong material, titanium grade 2 powder is a prime candidate. It’s particularly valuable in aerospace and biomedical engineering.
- AMS 316L Stainless Steel: Meeting the stringent aerospace material standards, AMS 316L stainless steel powder ensures the highest quality and consistency for critical aerospace parts.
- Nitronic 60: This precipitation-hardening stainless steel powder boasts exceptional strength and wear resistance, making it ideal for gears, bearings, and other demanding applications.
- Carpenter 4140: Offering a good balance of strength, toughness, and machinability, Carpenter 4140 powder is a versatile choice for general engineering components.
- Kovar: Known for its excellent thermal expansion coefficient match to glass, Kovar powder is widely used for metal-to-glass sealing applications in electronics and optoelectronics.
- Invar 36: With its ultra-low coefficient of thermal expansion, Invar 36 powder is crucial for components requiring dimensional stability over a wide temperature range, such as scientific instruments and electronic packages.
Applications of MS1(1.2709) Metal Powder
The exceptional properties of MS1(1.2709) powder make it suitable for a wide range of MIM applications across various industries. Here are some prime examples:
- Automotive: Complex gears, transmission components, and lightweight engine parts can all benefit from the strength, precision, and machinability of MS1(1.2709) MIM parts.
- Consumer Electronics: Miniaturized connectors, housings, and intricate components for electronic devices can be effectively produced using MS1(1.2709) powder in MIM.
- Medical Devices: Surgical instruments, bone screws, and other non-implantable medical devices can leverage the biocompatible nature and good mechanical properties of MS1(1.2709) MIM parts.
- Firearms: Components requiring high strength and tight tolerances, such as triggers, sears, and safety levers, can be precisely manufactured using MS1(1.2709) MIM technology.
- Aerospace: Certain non-critical aerospace components, such as brackets, housings, and spacers, can benefit from the cost-effective and high-precision production offered by MS1(1.2709) MIM.
Advantages and Limitations of MS1(1.2709) Metal Powder
MS1(1.2709) powder is a compelling choice for MIM, but like any material, it has its own set of advantages and limitations to consider.
Advantages:
- Versatility: MS1(1.2709) powder is suitable for a broad range of applications due to its well-balanced properties.
- Cost-Effectiveness: Compared to some specialty metal powders, MS1(1.2709) offers a more economical option for MIM production.
- High-Quality Parts: The combination of good flowability, packing density, and sintering response allows for the creation of high-quality MIM parts with good dimensional accuracy and mechanical properties.
- Excellent Machinability: MS1(1.2709) parts can be readily machined to achieve tight tolerances and intricate features.
Limitations:
- Strength Limitations: Compared to some high-alloy or tool steel powders, MS1(1.2709) might not be suitable for applications demanding exceptional strength.
- Corrosion Resistance: While decent, the corrosion resistance of MS1(1.2709) might not be sufficient for highly corrosive environments. For such applications, stainless steel or specialty alloy powders might be a better choice.
Finding the Perfect Match: Selecting the Right Metal Powder for Your MIM Needs
The ideal metal powder for your MIM project depends on your specific requirements. Here are some key factors to consider when making your selection:
- Application Requirements: The intended use of the MIM part will dictate the necessary properties, such as strength, corrosion resistance, machinability, and weight.
- Part Geometry: Complex geometries might require a powder with excellent flowability for uniform filling of the mold cavity.
- Cost Considerations: While MS1(1.2709) offers a good balance of performance and cost, other metal powders might be more economical for simpler parts or when large production volumes are involved.
- Post-Processing Needs: If extensive machining is required, a powder with good machinability is crucial.
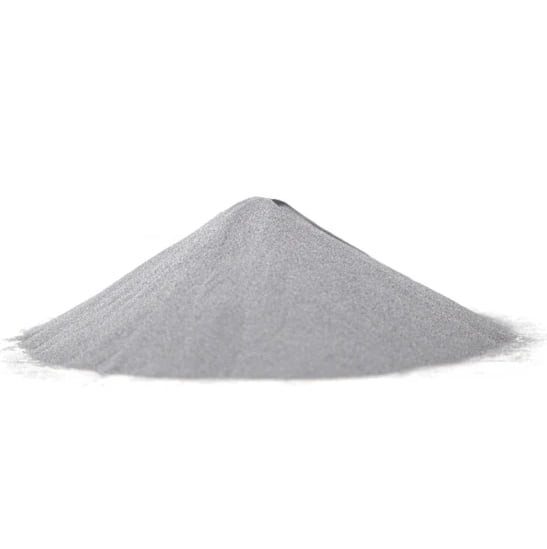
FAQ
Q: What are the main advantages of using MS1(1.2709) powder for MIM?
A: MS1(1.2709) powder offers a compelling combination of benefits for MIM applications:
- Versatility: It boasts a well-balanced set of properties, making it suitable for a wide range of applications.
- Cost-Effectiveness: Compared to some specialty metal powders, MS1(1.2709) is a more economical option.
- High-Quality Parts: The combination of good flowability, packing density, and sintering response allows for the creation of high-quality MIM parts with good dimensional accuracy and mechanical properties.
- Excellent Machinability: MS1(1.2709) parts can be readily machined to achieve tight tolerances and intricate features.
Q: Are there any limitations to consider when using MS1(1.2709) powder?
A: While MS1(1.2709) is a versatile powder, it does have some limitations to keep in mind:
- Strength Limitations: Compared to high-alloy or tool steel powders, MS1(1.2709) might not be ideal for applications demanding exceptional strength.
- Corrosion Resistance: While decent, the corrosion resistance of MS1(1.2709) might not be sufficient for highly corrosive environments. For such applications, stainless steel or specialty alloy powders might be a better choice.
Q: How does MS1(1.2709) powder compare to other popular MIM powders like 316L stainless steel?
A: Here’s a breakdown of the key differences:
- Material Type: MS1(1.2709) is a low-alloy steel, while 316L is a stainless steel.
- Applications: MS1(1.2709) finds use in gears, housings, and consumer electronics, while 316L is preferred for medical devices and chemical processing equipment due to its superior corrosion resistance.
- Cost: MS1(1.2709) is generally more economical than 316L stainless steel powder.
Q: What factors should I consider when selecting a metal powder for my MIM project?
A: Choosing the right metal powder hinges on your specific project requirements. Here are some key considerations:
- Application Requirements: The intended use of the MIM part will dictate the necessary properties, such as strength, corrosion resistance, machinability, and weight.
- Part Geometry: Complex geometries might require a powder with excellent flowability for uniform mold filling.
- Cost Considerations: While MS1(1.2709) offers a good balance of performance and cost, other metal powders might be more economical for simpler parts or large production volumes.
- Post-Processing Needs: If extensive machining is required, a powder with good machinability is crucial.
Q: Where can I find suppliers for MS1(1.2709) powder?
A: Several global and regional metal powder suppliers offer MS1(1.2709) powder. It’s recommended to search online marketplaces or contact metal powder suppliers directly to request quotes and compare pricing and availability.
Share On
MET3DP Technology Co., LTD is a leading provider of additive manufacturing solutions headquartered in Qingdao, China. Our company specializes in 3D printing equipment and high-performance metal powders for industrial applications.
Inquiry to get best price and customized Solution for your business!
Related Articles
About Met3DP
Recent Update
Our Product
CONTACT US
Any questions? Send us message now! We’ll serve your request with a whole team after receiving your message.
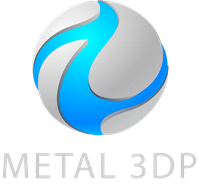
Metal Powders for 3D Printing and Additive Manufacturing