Next-Gen Additive Manufacturing in San Francisco: A Complete Guide for Industrial Buyers, Distributors & Suppliers
Table of Contents
1. Introduction: Why San Francisco is Emerging as a Hub for Next-Gen Additive Manufacturing
San Francisco, long recognized as a global center for technology, innovation, and venture capital, is quickly becoming a major player in the next generation of industrial manufacturing—specifically, additive manufacturing (AM), commonly referred to as 3D printing.
While traditionally known for its dominance in software and digital technologies, the Bay Area is now leveraging its ecosystem of startups, research institutions, and advanced manufacturing labs to pioneer breakthroughs in metal 3D printing, bioprinting, and high-performance additive materials. This shift has profound implications for B2B buyers, industrial distributors, aerospace contractors, and medical device manufacturers looking for reliable AM solutions.
Why San Francisco?
Here are some of the key reasons why San Francisco is becoming a critical hub for next-gen additive manufacturing:
Factor | Description |
---|---|
Tech Ecosystem | Home to world-class research institutions like Stanford, UC Berkeley, and Lawrence Livermore National Lab, which drive innovation in AM materials and hardware. |
Venture Capital Access | Startups working on novel AM technologies easily attract funding from top-tier VC firms in Silicon Valley. |
Talent Pool | A highly-skilled workforce with expertise in robotics, AI, materials science, and advanced manufacturing. |
Sustainability Focus | Strong emphasis on sustainable manufacturing practices, including the use of recyclable metal powders and zero-waste production methods. |
Advanced Manufacturing Labs | Facilities such as Autodesk’s Pier 9 and the Digital Manufacturing Lab foster experimentation and prototyping. |
Why Additive Manufacturing Matters for B2B Buyers
For B2B stakeholders—especially procurement managers, supply chain directors, and OEM partners—additive manufacturing delivers:
- Rapid Prototyping: Faster product development cycles
- Customization at Scale: Ability to produce one-off or low-volume parts cost-effectively
- Material Efficiency: Less waste compared to subtractive manufacturing
- Onshore & Offshore Flexibility: Access to both local and global suppliers for strategic sourcing
As global supply chains continue to evolve, many businesses are reevaluating their sourcing strategies. Additive manufacturing provides a powerful tool to localize production, reduce lead times, and improve part performance.
2. Market Trends: Growth of Additive Manufacturing in San Francisco and the Bay Area
The additive manufacturing market in San Francisco is seeing exponential growth, driven by high-tech industries and new materials innovations. As of 2024, the global AM market is valued at over $25 billion, with the Bay Area contributing significantly thanks to its heavy concentration of biotech, aerospace, and electronics companies.
Key Growth Drivers in San Francisco:
1. Aerospace & Defense
San Francisco and the broader Bay Area are home to aerospace innovators like SpaceX, Rocket Lab, and Planet Labs. These companies rely on metal 3D printing for lightweight, heat-resistant components.
Use Cases:
- Turbine blades
- Engine brackets
- Heat exchangers
- Satellite parts
2. Medical Devices
With companies like Stryker, Medtronic, and startups in bioengineering, additive manufacturing is used for:
- Custom orthopedic implants
- Surgical tools
- Dental prosthetics
- Bone scaffolds
3. Semiconductor & Electronics
Additive manufacturing is being used in microelectronics for:
- Heat sinks
- EMI shielding
- Custom enclosures
- Conformal cooling channels
4. Automotive & EV Innovation
Electric vehicle startups and autonomous driving R&D facilities in the Bay Area are turning to AM for rapid prototyping and lightweight structural parts.
Market Statistics (2023–2024):
Market Segment | CAGR (Compound Annual Growth Rate) | Adoption Level |
---|---|---|
Aerospace AM | 22% | High |
Medical AM | 18% | High |
Electronics AM | 15% | Moderate |
Automotive AM | 20% | Moderate |
Venture Capital Impact
In 2023 alone, more than $1.2 billion in VC funding was invested in Bay Area AM startups, such as:
- Carbon – known for its Digital Light Synthesis (DLS)
- Mantle – focusing on precision metal 3D printing
- Seurat Technologies – developing Area Printing for high-volume manufacturing
This influx of capital is accelerating R&D and commercialization of next-gen AM technologies that appeal to industrial buyers and distributors.
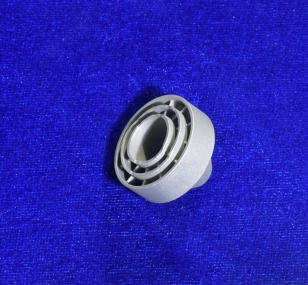
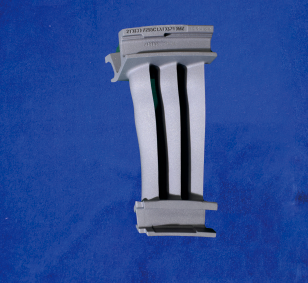
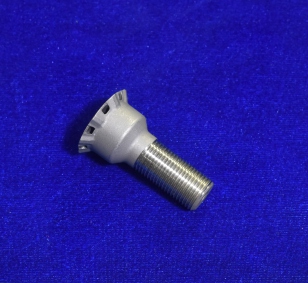
3. Key Considerations When Choosing a Metal 3D Printing Supplier in San Francisco
For industrial buyers and B2B procurement managers, selecting the right additive manufacturing supplier is mission-critical. The quality of your parts, the reliability of your supply chain, and the scalability of production all depend on making informed decisions.
Here are the most important criteria to evaluate:
1. Technical Capabilities
Ask the following questions:
- Do they offer powder bed fusion (PBF), directed energy deposition (DED), or electron beam melting (EBM)?
- Can they handle large build volumes and complex geometries?
- What metals and alloys are supported—stainless steel, titanium, cobalt-chrome, etc.?
2. Certification & Compliance
Look for:
- ISO 9001 or AS9100 certified facilities
- FDA compliance for medical applications
- Testing protocols: CT scanning, tensile testing, metallography
3. Material Quality
Quality of input materials directly impacts part performance. Ensure suppliers use:
- High-purity, spherical metal powders
- Consistent particle size distribution
- Verified powder reuse protocols
This is where global suppliers like Metal3DP stand out. They offer high-performance metal powders manufactured using advanced gas atomization and PREP technology, ensuring excellent sphericity and flowability.
4. Turnaround Time
B2B buyers need predictable timelines. Ask:
- What is the average lead time for prototyping vs. production?
- Do they offer in-house post-processing (e.g., heat treatment, CNC finishing)?
- Can they meet urgent orders or scale for large-volume production?
5. Scalability
Consider future growth:
- Can the supplier handle hundreds-to-thousands of parts/month?
- Are they using industrial-grade printers or desktop units?
- Do they offer production-level capacity for aerospace or automotive tier-1 suppliers?
6. Support & Engineering Services
The best AM partners do more than print parts. Evaluate:
- In-house design for additive manufacturing (DfAM) support
- Simulation and topology optimization services
- Material selection and application consulting
Supplier Evaluation Checklist
Criteria | Must-Have | Nice-to-Have |
---|---|---|
ISO/AS Certification | ✅ | |
In-House Post-Processing | ✅ | |
DfAM Engineering Support | ✅ | |
High-Quality Metal Powders | ✅ | |
Global Shipping | ✅ | |
Custom Alloy Development | ✅ | |
Tooling & Fixturing Capabilities | ✅ |
Internal Link Example:
If you’re looking to understand the fundamental printing technologies used in next-gen AM, check out this guide on Printing Methods used by Metal3DP to support industries like aerospace, medical, and energy.
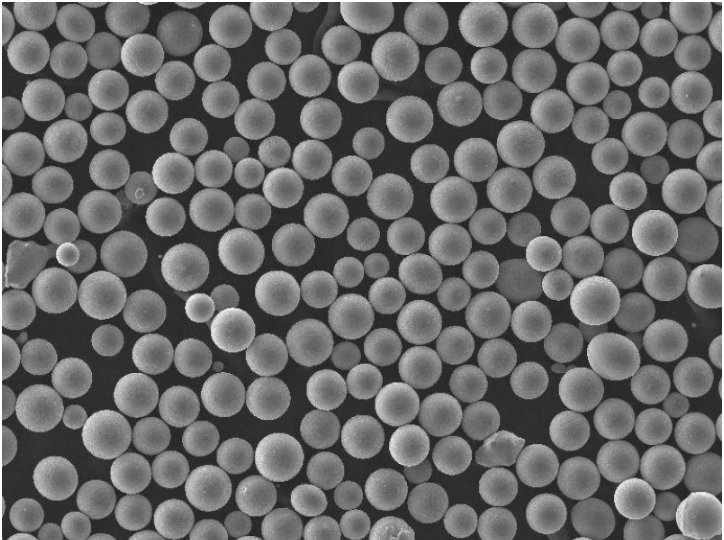
4. Top 5 Additive Manufacturing Suppliers in San Francisco for Industrial Buyers
The San Francisco Bay Area boasts a growing list of additive manufacturing service providers that cater to industrial clients across aerospace, medical, automotive, and electronics sectors. Below is a curated list of the top 5 AM suppliers based on their capabilities, certifications, material offerings, and relevance to B2B buyers.
Comparison Table: Leading AM Providers in San Francisco
Company | Technologies Offered | Materials Supported | Certifications | Specialization |
---|---|---|---|---|
Carbon (Redwood City) | Digital Light Synthesis (DLS) | Photopolymers, resins | ISO 13485 | Medical, dental, consumer goods |
Mantle (San Francisco) | TrueShape Metal AM | Tool steel, stainless | ISO 9001 | Tooling, injection mold inserts |
Seurat Technologies (Hayward) | Area Printing™ (Laser PBF) | Metal alloys | In development | High-volume industrial parts |
Fathom (Oakland) | SLS, SLA, FDM, DMLS | Plastic, metal | ISO 9001 | Rapid prototyping, low-volume |
3DEO (Los Angeles, serves SF) | Intelligent Layering (metal AM) | Stainless steel | ISO 9001, AS9100 | Aerospace, defense, medical |
Key Takeaways for B2B Buyers
- Carbon is ideal for medical device manufacturers looking for fast prototyping and production of biocompatible components.
- Mantle offers a cost-effective solution for tooling applications—particularly valuable to automotive and consumer electronics OEMs.
- Seurat is promising for large-scale production, although still in commercialization phase.
- Fathom is a full-service bureau offering both plastic and metal AM, suitable for distributors and design firms.
- 3DEO specializes in high-volume, precision metal components with tight tolerances, ideal for aerospace and defense contractors.
Questions to Ask When Contacting These Suppliers
- Can you meet our monthly volume and lead time requirements?
- What industries do you specialize in?
- Can you provide sample parts or case studies?
- Do you offer design support or just part production?
5. Why More Buyers Are Choosing Offshore Suppliers Like Metal3DP for Cost-Effective Additive Manufacturing
While San Francisco offers cutting-edge AM capabilities, many industrial buyers and sourcing managers in the U.S. are increasingly turning to offshore partners—especially those in China—for scalable, cost-effective solutions without compromising on quality.
Cost Comparison: Domestic vs. Offshore AM
Item | U.S.-Based Supplier | Metal3DP |
---|---|---|
Titanium Alloy Powder (per kg) | $400–$600 | $180–$260 |
Custom Inconel Part (mid-size) | $500–$800 | $200–$350 |
Lead Time (prototyping) | 5–10 days | 5–7 days |
MOQ (Minimum Order Quantity) | Often 50+ units | Flexible – as low as 1 unit |
Certifications | ISO, AS9100 | ISO 9001, In-house QC standards |
Conclusion: Offshore suppliers can offer up to 50% cost savings, faster lead times, and lower MOQs—especially beneficial for startups or small-batch manufacturers.
Why Metal3DP Is a Preferred Offshore Partner
Metal3DP, headquartered in Qingdao, China, is a global leader in metal additive manufacturing solutions. The company’s competitive edge lies in:
- Advanced Manufacturing Equipment: Metal3DP offers SEBM (Selective Electron Beam Melting), Laser PBF, and other high-precision technologies.
- Superior Metal Powders: Produced using gas atomization and PREP technology, Metal3DP powders offer excellent sphericity and flowability.
- Custom Alloys: The company supports specialized alloys like TiNi, TiAl, CoCrMo, and more, ideal for aerospace and biomedical applications.
- Global Distribution: Metal3DP ships globally, with logistics experience in serving U.S., EU, and APAC clients.
Case Study: U.S. Aerospace Component Supplier
A California-based aerospace component supplier partnered with Metal3DP to procure high-strength titanium parts for jet engine brackets. Key outcomes:
- 35% cost savings over domestic suppliers
- 12-day turnaround for 30 units
- 100% pass rate on X-ray and tensile tests
This example shows how offshore AM sourcing can be both strategic and reliable.
6. Why Choose Metal3DP as Your Additive Manufacturing Partner
Metal3DP isn’t just a supplier—it’s a strategic partner for businesses seeking high-quality metal 3D printing solutions at scale. Whether you’re a B2B distributor, OEM, or supply chain director, here’s why you should consider Metal3DP for your additive manufacturing needs.
1. Industry-Leading Printing Systems
Metal3DP offers a suite of additive manufacturing systems for industrial-scale production:
- SEBM Printers: Ideal for high-density metal parts with intricate geometries
- Laser Powder Bed Fusion: Delivers excellent surface quality for aerospace and medical
- Electron Beam Melting: For parts requiring superior mechanical properties at high temperatures
Visit the Metal 3D Printing Equipment page to explore available systems.
2. High-Performance Metal Powders
Metal3DP’s proprietary metal powders are manufactured in-house using:
- Gas Atomization
- Plasma Rotating Electrode Process (PREP)
This results in:
- Highly spherical particles
- Narrow particle size distribution
- Excellent flowability and packing density
✅ Available Alloys:
Alloy Type | Suitable Industries | Key Properties |
---|---|---|
Ti6Al4V | Aerospace, Medical | Lightweight, corrosion-resistant |
CoCrMo | Dental, Orthopedic | Biocompatible, wear-resistant |
Inconel 718 | Aerospace | High temp strength |
316L Stainless | Industrial, Food | Corrosion-resistant |
TiNbZr | Biomedical | High elasticity, biocompatibility |
Explore the full Product Portfolio of powders and systems.
3. Custom Engineering and Application Support
Metal3DP doesn’t just sell powders and machines—they work with clients to:
- Design for Additive Manufacturing (DfAM)
- Develop custom alloys
- Support regulatory compliance (FDA, ISO)
- Optimize part geometry for performance and printability
This makes them an ideal partner for:
- Medical OEMs
- Aerospace Tier 1 Suppliers
- Industrial Product Designers
- Distributors of 3D printing materials
4. Quality Control & Testing
All parts and powders undergo rigorous quality checks:
- Powder Analysis: Morphology, PSD, flow rate
- Part Testing: Tensile strength, CT scanning, density
- Process Validation: Repeatability, traceability, documentation
5. Global Logistics and U.S. Support
- Metal3DP offers consolidated shipping and customs handling for U.S. buyers
- Dedicated export team ensures on-time delivery with batch traceability
- Remote support and virtual factory tours available for overseas clients
Internal Link Example:
To learn more about how Metal3DP’s advanced systems and powders support mission-critical industries, explore their About Us page showcasing their R&D and quality commitment.
7. How to Order High-Performance Metal Powders and 3D Printing Services from Metal3DP
For industrial buyers, procurement directors, and global distributors, ordering from an international supplier like Metal3DP is easier than ever. With streamlined logistics, engineering consulting, and total transparency, Metal3DP supports both small-batch and large-scale procurement of 3D printing powders and parts.
Step-by-Step Ordering Process
Here’s a breakdown of how to engage with Metal3DP as a B2B buyer:
Step | Description |
---|---|
1. Initial Inquiry | Submit your requirements via their website or email. Include CAD files, part specs, material needs, and volume. |
2. Technical Consultation | Metal3DP’s engineers review your design and offer suggestions on material choice, printing method, and optimization. |
3. Quotation | Receive a detailed quote including unit pricing, shipping, MOQ, lead times, and quality certifications. |
4. Prototype (Optional) | For new projects, a prototype can be manufactured and shipped prior to bulk production. |
5. Production & Testing | Full production begins after approval. All products undergo in-house QA (chemical composition, density, tensile testing, etc.). |
6. Shipping & Delivery | Parts and/or powders are shipped via DHL, FedEx, or sea freight with full customs documentation and tracking. |
7. After-Sales Support | Dedicated support for reorders, revisions, and long-term supply agreements. |
Ordering Metal Powders
Metal3DP offers a wide range of 3D printing powders optimized for PBF and EBM technologies.
Ordering Parameters:
- MOQ: As low as 5 kg for most alloys
- Packaging: Vacuum-sealed, inert gas-packed metal containers
- Delivery Time: 7–10 days to the U.S. (express), 20–25 days (sea)
- Custom Alloys: Available upon request
Popular Metal Powders Available:
Alloy | Use Case | sD50 (µm) | Flowability | Notes |
---|---|---|---|---|
Ti6Al4V | Aerospace, medical implants | 25–45 | Excellent | Biocompatible |
Inconel 718 | Turbines, exhaust systems | 15–53 | Very Good | High-temp resistance |
CoCrMo | Dental, orthopedic | 20–45 | Good | Wear-resistant |
316L Stainless | Food, marine, tooling | 20–50 | Excellent | Corrosion-resistant |
TiAl | Jet engine blades | 30–60 | Good | Lightweight, high strength |
➡️ To view the full list of available powders and printer systems, visit the Products Page.
Ordering Custom 3D Printed Parts
If you need precision metal parts instead of just powders, Metal3DP provides full contract manufacturing services:
- Supported Printing Tech: SEBM, LPBF, EBM
- Max Build Volume: Up to 500 x 500 x 500 mm
- Surface Finish: Ra < 10 µm (with post-processing)
- Tolerances: ±0.05 mm standard, tighter available on request
- Materials: Titanium, Ni-based alloys, CoCr, stainless steel, and more
Optional post-processing services include:
- CNC machining
- HIP (Hot Isostatic Pressing)
- Heat treatment
- Surface polishing
- Coating (TiN, AlTiN)
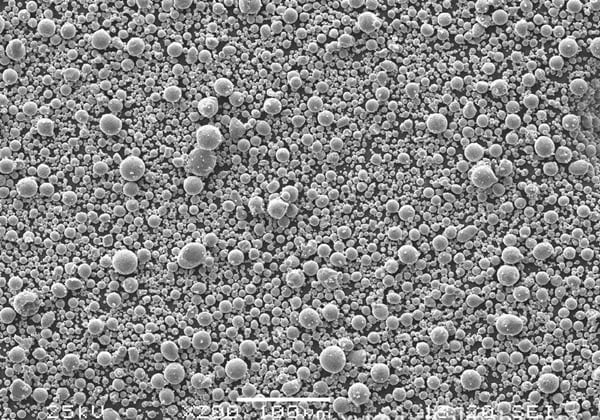
8. FAQs: Common Questions About Sourcing Additive Manufacturing in San Francisco or Overseas
Q1: How do I know if Metal3DP powders are compatible with my printer?
Metal3DP powders are designed for compatibility with a wide range of systems including EOS, SLM Solutions, Renishaw, Arcam, and Concept Laser. Particle size distribution and flowability are optimized for both laser and electron beam systems.
➡️ For more technical specs, refer to their Printing Methods Guide.
Q2: Can Metal3DP help with FDA or aerospace certification requirements?
Yes. While Metal3DP does not issue final product certifications, they provide:
- Full materials traceability
- Chemical composition reports
- Mechanical property testing
- Powder batch certification
This documentation can be used by your quality team to pursue ISO, AS9100, or FDA compliance.
Q3: What industries does Metal3DP serve?
Metal3DP supports mission-critical industries including:
- Aerospace & Defense
- Medical Devices & Orthopedics
- Automotive & EV
- Energy & Oilfield
- Tooling & Injection Molding
- Research & Development Institutions
Q4: What’s the lead time for a typical order?
- Powders: 5–7 days for most standard alloys
- Printed Parts: 10–15 days depending on complexity and post-processing
- Custom Alloys: 2–3 weeks including lab development
Shipping to the U.S. typically takes 5–10 days via air freight.
Q5: Can I get a sample before bulk ordering?
Yes. Metal3DP encourages new buyers to order samples or prototypes to validate quality. Small powder containers (1–2 kg) and single-part prints are available for evaluation.
Q6: Do they offer support in English?
Absolutely. The international sales and engineering teams at Metal3DP include fluent English speakers who provide:
- Technical advice
- Quotation assistance
- After-sales support
- Documentation and compliance guidance
They are experienced in working with North American and European clients.
9. Conclusion: Embracing the Future of Industrial Manufacturing with Global Additive Solutions
Additive manufacturing is no longer just a prototyping tool—it’s a strategic production asset for industrial buyers, engineers, and procurement leaders across industries. In San Francisco, the AM ecosystem is thriving, supported by innovation, venture capital, and advanced R&D.
However, as global sourcing continues to evolve, companies seeking better cost-performance ratios, custom material solutions, and scalable production are increasingly turning to offshore partners like Metal3DP.
Why Metal3DP Is Your Ideal Additive Manufacturing Partner:
- ✅ In-house production of premium metal powders
- ✅ Cutting-edge SEBM and LPBF printers
- ✅ Custom alloy development and DfAM support
- ✅ Global logistics and low MOQs
- ✅ Trusted by aerospace, medical, and industrial leaders
Whether you’re a U.S.-based distributor sourcing titanium powders, an OEM developing next-gen medical implants, or a research institute experimenting with custom alloys—Metal3DP has the technology, expertise, and global reach to power your additive manufacturing goals.
📩 Ready to start?
Request a quote or speak with an engineer today via the Metal3DP Contact Page.
Share On
MET3DP Technology Co., LTD is a leading provider of additive manufacturing solutions headquartered in Qingdao, China. Our company specializes in 3D printing equipment and high-performance metal powders for industrial applications.
Inquiry to get best price and customized Solution for your business!
Related Articles
About Met3DP
Recent Update
Our Product
CONTACT US
Any questions? Send us message now! We’ll serve your request with a whole team after receiving your message.
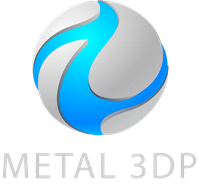
Metal Powders for 3D Printing and Additive Manufacturing
COMPANY
PRODUCT
cONTACT INFO
- Qingdao City, Shandong, China
- [email protected]
- [email protected]
- +86 19116340731