The Future of High-Temperature Nickel Alloy Parts: 3D Printing in Seoul
Table of Contents
1. Introduction: The Rise of 3D Printing for High-Temperature Nickel Alloy Parts
The demand for high-temperature nickel alloy parts has surged in industries such as aerospace, energy, and automotive due to their exceptional resistance to extreme temperatures and corrosion. Traditionally, these components were manufactured using casting or CNC machining, but 3D printing has revolutionized the production process, offering greater design flexibility, reduced material waste, and faster lead times.
Seoul is emerging as a leading hub for metal additive manufacturing, with companies investing in cutting-edge 3D printing solutions to meet the growing demand for high-performance metal parts. Manufacturers in South Korea are leveraging Selective Electron Beam Melting (SEBM) and laser-based powder bed fusion (LPBF) to fabricate intricate nickel alloy components with superior mechanical properties.
2. Market Trends & Growth Potential of Nickel Alloy 3D Printing
Global and South Korean Market Insights
Market Segment | Growth Potential |
---|---|
Aerospace & Defense | High demand for lightweight, heat-resistant components |
Power Generation | Nickel alloys used in turbines and heat exchangers |
Medical Implants | Biocompatible nickel alloys for surgical implants |
Automotive & EV | High-performance engine and exhaust components |
- The global 3D printing metals market is projected to grow at a CAGR of 25% from 2023 to 2030, with nickel superalloys playing a crucial role in this expansion.
- South Korea is rapidly adopting metal 3D printing, supported by government initiatives and investments in smart manufacturing technologies.
Industries Adopting Nickel Alloy 3D Printing
- Aerospace: Jet engine components, turbine blades, heat shields
- Energy: Gas turbines, nuclear reactor components
- Medical: Orthopedic and dental implants
- Automotive: Turbochargers, exhaust systems, high-stress components
3. Key Factors to Consider When Choosing a Nickel Alloy 3D Printing Supplier
When selecting a high-temperature nickel alloy 3D printing supplier, businesses must evaluate several critical factors:
1. Material Quality & Consistency
- The sphericity and purity of metal powders determine the final part’s strength and durability.
- Metal3DP uses gas atomization and PREP technologies to ensure highly spherical, flowable powders for superior print quality.
2. Print Volume, Precision & Reliability
- Large-scale industrial 3D printers should offer high build volumes to produce bulk components efficiently.
- Metal3DP’s SEBM and LPBF printers deliver industry-leading accuracy and repeatability.
3. Supplier Expertise & Technical Support
- Manufacturers should partner with suppliers offering comprehensive technical support and material consultation.
- Metal3DP provides end-to-end additive manufacturing solutions, from material selection to final part optimization.
For more details on nickel alloy 3D printing and metal additive technologies, visit Metal3DP’s Metal 3D Printing page.
4. Top 5 Suppliers of High-Temperature Nickel Alloy 3D Printing in Seoul
Seoul is home to several leading metal additive manufacturing companies specializing in high-temperature nickel alloy parts. Below are five top suppliers that provide advanced 3D printing solutions:
1. Metal3DP Technology Co., Ltd.
- Specialty: High-performance nickel alloy powders and industrial-grade 3D printers
- Technologies Used: SEBM (Selective Electron Beam Melting), LPBF (Laser Powder Bed Fusion)
- Key Advantage: Industry-leading print accuracy and advanced powder-making technologies
- Why Choose Metal3DP?
- High-purity metal powders produced using gas atomization and PREP technologies
- Large-scale industrial 3D printers with superior mechanical properties
- Expert consultation for customized additive manufacturing solutions
2. Korea Institute of Industrial Technology (KITECH)
- Specialty: Research-driven 3D printing solutions for aerospace and medical applications
- Technologies Used: Laser-based PBF, DED (Directed Energy Deposition)
- Key Advantage: Strong R&D capabilities and government-backed initiatives
3. Insstek Inc.
- Specialty: Direct Metal Deposition (DMD) for high-strength alloy parts
- Technologies Used: DED, Hybrid AM solutions
- Key Advantage: Focus on repairing and reinforcing high-performance metal parts
4. EOS Korea
- Specialty: High-precision metal printing solutions for industrial applications
- Technologies Used: LPBF
- Key Advantage: Global leader in metal AM, offering highly optimized process parameters
5. 3D Systems Korea
- Specialty: Advanced metal 3D printing for aerospace and medical industries
- Technologies Used: DMP (Direct Metal Printing)
- Key Advantage: High-volume production capabilities for complex, high-temperature metal parts
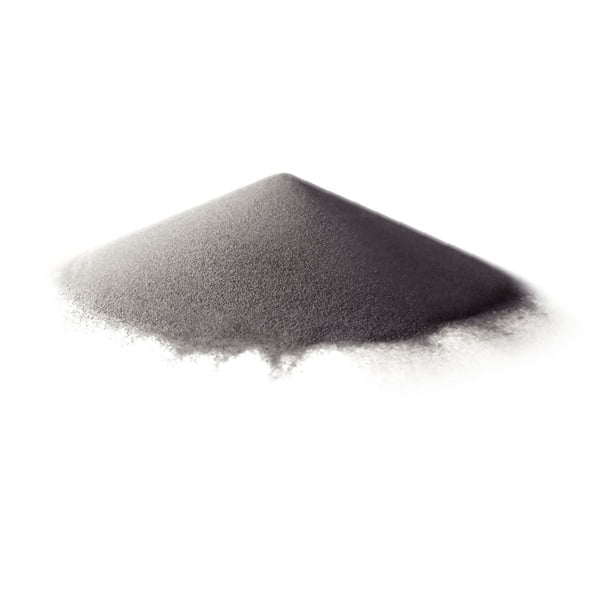
5. Why More Manufacturers Are Turning to Metal 3D Printing for High-Temperature Parts
Traditional manufacturing methods for high-temperature nickel alloy components, such as casting and CNC machining, often result in material waste, long lead times, and design limitations. Metal 3D printing is rapidly becoming the preferred alternative due to its numerous advantages:
Key Benefits of Metal 3D Printing for Nickel Alloy Parts
Benefit | How It Helps Manufacturers |
---|---|
Design Freedom | Enables complex geometries that are impossible with traditional machining |
Material Efficiency | Reduces waste by using only the necessary powder for each part |
Faster Lead Times | Eliminates the need for tooling, speeding up production |
Superior Mechanical Properties | Produces dense, high-strength metal parts with optimized microstructures |
Cost Savings | Reduces reliance on expensive materials and post-processing |
Real-World Applications of Nickel Alloy 3D Printing
- Aerospace: Lightweight, high-temperature turbine blades
- Energy Sector: Heat exchangers and gas turbine components
- Medical Industry: Biocompatible implants with customized geometries
- Automotive: High-performance exhaust systems and turbocharger housings
6. Why Choose Metal3DP for High-Performance Nickel Alloy 3D Printing?
1. Advanced Powder-Making Systems
Metal3DP employs industry-leading gas atomization and PREP technologies to manufacture high-purity, spherical nickel alloy powders. These powders ensure excellent flowability and printability, resulting in stronger, more reliable components.
2. Industry-Leading Print Volume & Accuracy
- Our SEBM and LPBF printers offer high-volume production with exceptional precision.
- Supports mission-critical applications in aerospace, automotive, and medical industries.
3. Wide Range of High-Performance Metal Powders
Metal3DP offers an extensive portfolio of nickel-based superalloys, including:
- Inconel 625 & 718 (high corrosion resistance)
- Hastelloy X (ideal for extreme thermal environments)
- Custom nickel alloys for specialized industrial applications
4. Expert Consultation & End-to-End Solutions
From material selection to final post-processing, Metal3DP provides comprehensive additive manufacturing services to support businesses in achieving high-performance, cost-effective production.
For more information about our 3D printing technologies and metal powders, visit our Product Page.
7. How to Order Custom Nickel Alloy 3D Printed Parts in Seoul
For businesses looking to source high-temperature nickel alloy parts through 3D printing, understanding the ordering process is crucial. Below is a step-by-step guide to ensure a seamless experience when working with Metal3DP or other suppliers in Seoul.
Step-by-Step Ordering Process
Step | Details |
---|---|
Step 1: Define Your Requirements | Identify the part specifications, including dimensions, material type, and mechanical properties required. |
Step 2: Select the Right Nickel Alloy | Choose from Inconel 625, Inconel 718, Hastelloy X, or custom nickel-based alloys based on temperature resistance and corrosion properties. |
Step 3: Submit Your 3D Model | Provide a CAD file (.STL, .STEP, or .IGES) of your design for evaluation. |
Step 4: Receive a Manufacturing Consultation | Metal3DP experts will review print feasibility, material selection, and production timeline. |
Step 5: Get a Quote & Confirm Order | Receive a detailed cost estimate based on print volume, material cost, and post-processing needs. |
Step 6: Production & Quality Inspection | The part is 3D printed using SEBM or LPBF, followed by quality control checks to ensure dimensional accuracy. |
Step 7: Post-Processing & Finishing | Additional treatments such as heat treatment, surface polishing, or CNC machining can be applied. |
Step 8: Shipping & Delivery | Once the part passes final inspection, it is securely packaged and shipped to your location. |
For businesses interested in bulk orders or custom metal additive manufacturing solutions, visit our About Us Page to learn more about Metal3DP’s capabilities.
8. FAQs: Common Questions About High-Temperature Nickel Alloy 3D Printing
Q1: What are the advantages of using nickel alloys in 3D printing?
Nickel-based alloys offer exceptional heat resistance, corrosion resistance, and mechanical strength, making them ideal for aerospace, power generation, and high-stress applications.
Q2: How strong are 3D-printed nickel alloy parts compared to traditionally manufactured parts?
With advanced powder bed fusion (PBF) technologies, 3D-printed nickel alloy parts can achieve similar or superior mechanical properties compared to cast or machined parts, thanks to optimized microstructures.
Q3: What is the lead time for ordering a custom nickel alloy 3D-printed part?
Production times depend on part complexity, material selection, and post-processing needs. On average:
- Small parts: 5-7 business days
- Large or complex parts: 10-20 business days
Q4: Can Metal3DP print large-scale nickel alloy components?
Yes! Metal3DP’s industrial-grade SEBM and LPBF printers support large-format metal printing for aerospace and heavy industry applications.
Q5: How does the cost of 3D printing nickel alloys compare to traditional methods?
While initial costs may be higher, metal 3D printing reduces material waste and eliminates tooling expenses, leading to long-term cost savings.
For more information on 3D printing methods and technologies, check out our Printing Methods Page.
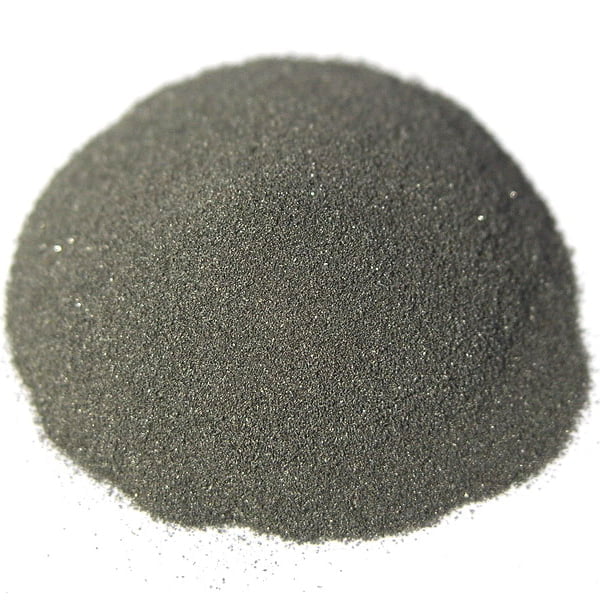
9. Conclusion & Next Steps
High-temperature nickel alloy 3D printing is transforming industries by enabling the production of complex, high-performance components with unmatched efficiency. Seoul is at the forefront of this revolution, with companies like Metal3DP offering cutting-edge additive manufacturing solutions.
Why Choose Metal3DP?
✔ Industry-leading nickel alloy powders with precise sphericity and purity
✔ Advanced SEBM and LPBF 3D printing technologies for superior mechanical properties
✔ Expert consultation & customized manufacturing solutions
✔ Fast production timelines to meet industrial demands
If you’re looking to source high-quality 3D-printed nickel alloy parts, Metal3DP is your trusted partner.
📩 Get in touch today! Visit our Contact Page to request a quote and explore how Metal3DP can optimize your metal additive manufacturing needs.
Stay ahead in the metal additive manufacturing industry by leveraging advanced 3D printing solutions!
Share On
MET3DP Technology Co., LTD is a leading provider of additive manufacturing solutions headquartered in Qingdao, China. Our company specializes in 3D printing equipment and high-performance metal powders for industrial applications.
Inquiry to get best price and customized Solution for your business!
Related Articles
About Met3DP
Recent Update
Our Product
CONTACT US
Any questions? Send us message now! We’ll serve your request with a whole team after receiving your message.
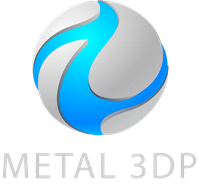
Metal Powders for 3D Printing and Additive Manufacturing