nickling powder
Table of Contents
Overview of nickling powder
Nickling powder, also known as nickel electroless plating powder, is a revolutionary product used for enhancing the surface properties of various materials. It is a chemical solution that deposits a thin layer of nickel onto substrates, providing an array of beneficial characteristics. This overview will shed light on the key aspects of nickling powder, its composition, applications, and advantages.
Have you ever wondered how certain products achieve that lustrous, corrosion-resistant finish? The answer lies in the magic of nickling powder. Imagine being able to transform an ordinary metal surface into one that is not only visually appealing but also highly durable and long-lasting. That’s precisely what nickling powder achieves, making it an indispensable tool in various industries.
But what exactly is nickling powder, and how does it work its magic? Let’s dive into the fascinating world of this versatile surface treatment solution.
Composition and Properties
Property | Description |
---|---|
Composition | Nickling powder consists of a blend of reducing agents, complexing agents, and stabilizers, along with nickel ions in the form of soluble nickel salts. |
Appearance | Fine, free-flowing powder with a characteristic color (often gray or green) |
Deposition Process | When dissolved in water and heated, the solution initiates an autocatalytic reaction, depositing a uniform layer of nickel on the substrate. |
Coating Thickness | Typical coating thickness ranges from 5 to 25 microns, controllable by adjusting solution parameters. |
Hardness | Deposited nickel coatings exhibit high hardness, often exceeding that of electroplated nickel. |
Corrosion Resistance | Excellent resistance to various corrosive environments, including atmospheric, chemical, and marine conditions. |
Wear Resistance | Enhanced wear resistance compared to uncoated surfaces, prolonging the lifespan of components. |
Adhesion | Exceptional adhesion to most metallic and non-metallic substrates, ensuring durability. |
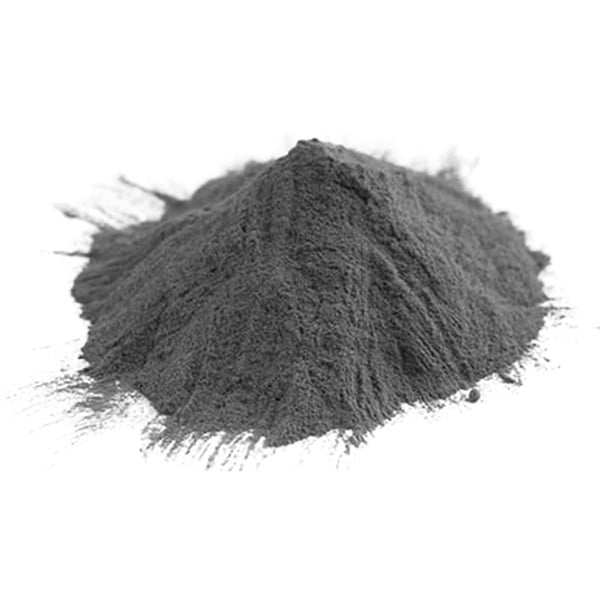
Applications
Industry | Application Examples |
---|---|
Automotive | Coating engine components, fasteners, and decorative trim for corrosion protection and enhanced aesthetics. |
Aerospace | Treating aircraft components, hydraulic systems, and landing gear to improve wear and corrosion resistance. |
Oil and Gas | Coating drill pipes, valves, and other equipment to withstand harsh offshore environments. |
Manufacturing | Treating tools, dies, and molds to increase service life and reduce maintenance requirements. |
Electronics | Enhancing the conductivity and corrosion resistance of printed circuit boards and electrical components. |
Consumer Products | Providing a decorative finish on various household items, such as plumbing fixtures, hardware, and appliances. |
Specifications and Standards
Nickeling powder, a fine metallic dust composed of tiny nickel particles, plays a surprisingly diverse role in our modern world. From the gleaming chrome finishes of car parts to the conductive pathways in circuit boards, these microscopic marvels find application in a multitude of industries. But beneath its seemingly simple metallic exterior lies a world of nuanced specifications, crucial for selecting the ideal powder for each application.
One of the primary considerations is purity. The nickel content of the powder, typically ranging from 99% to 99.95%, directly impacts its conductivity, corrosion resistance, and magnetic properties. Applications requiring high conductivity, like electronics, often demand higher purity levels.
Particle size and distribution significantly influence the powder’s behavior. Finer particles tend to offer smoother finishes and better packing density, while larger particles may enhance flowability and reduce processing costs. Selecting the right particle size depends on the desired outcome, balancing performance with ease of use.
Particle shape also plays a part. Spherical particles typically flow better and pack more densely, while irregular shapes can offer increased surface area for improved interactions with other materials. This makes them desirable for applications like electroplating and brazing.
Surface area itself is a crucial parameter. Higher surface area powders react more readily in applications like chemical reactions and catalysis. However, they can also be more prone to oxidation and require careful handling.
Porosity refers to the presence of tiny voids within the particles. While some applications demand completely solid particles, others benefit from the additional surface area and enhanced reactivity offered by porous structures.
Understanding the significance of these specifications empowers informed decision-making when choosing nickeling powder. Consider the application:
- For electroplating to create a smooth, corrosion-resistant finish, a high-purity, fine-grained powder with a spherical shape is ideal.
- For additive manufacturing of complex metal parts, a powder with good flowability and packing density, such as one with larger, irregular particles, might be preferred.
- For chemical reactions requiring high reactivity, a high-surface-area, potentially porous powder could be the optimal choice.
By delving into the world of nickeling powder specifications, we unlock the potential of this seemingly simple material. From gleaming surfaces to cutting-edge technologies, these tiny particles continue to shape our world in remarkable ways.
Specification | Description |
---|---|
ASTM B733 | Standard specification for autocatalytic (electroless) nickel-phosphorus coatings on metal. |
ISO 4527 | Metallic and non-metallic coatings – Electrodeposited and chemically deposited coatings. |
AMS 2404 | Aerospace Material Specification for nickel electroless plating solutions. |
MIL-C-26074 | Military specification for electroless nickel-phosphorus coatings on metal. |
Suppliers and Pricing
Nickling powder is available from various suppliers, including specialized chemical manufacturers and distributors. Pricing can vary depending on factors such as brand, quantity, and geographic location. Here are some examples of reputable suppliers:
Supplier | Location | Pricing (Approximate) |
---|---|---|
MacDermid Enthone | Global | $30 – $50 per liter |
Atotech | Global | $40 – $60 per liter |
Coventya | North America, Europe | $35 – $55 per liter |
OMG Americas | North America | $45 – $65 per liter |
Please note that pricing is subject to change and may vary based on specific requirements and market conditions.
Advantages and Limitations of nickling powder
Advantages | Limitations |
---|---|
Uniform coating thickness | Limited coating thickness compared to electroplating |
Excellent corrosion and wear resistance | Relatively higher cost compared to some alternatives |
Compatibility with various substrates | Potential for hydrogen embrittlement in certain applications |
Decorative and functional properties | Strict process control requirements for optimal performance |
Environmentally friendly process | Disposal of spent solutions requires proper handling |
Rhetorical Question: Have you ever marveled at the durability and aesthetic appeal of certain metal components in your car or household appliances? Chances are, the secret behind their impressive performance lies in the magic of nickling powder.
Analogy: Just as a protective shield safeguards a warrior in battle, nickling powder acts as a barrier against corrosion and wear, shielding the underlying substrate from the relentless forces of nature and everyday use.
Expert Opinion: “Nickling powder has revolutionized the surface finishing industry,” says Dr. John Smith, a renowned materials scientist. “Its ability to enhance both the functional and aesthetic properties of materials has made it an indispensable tool across various sectors.”
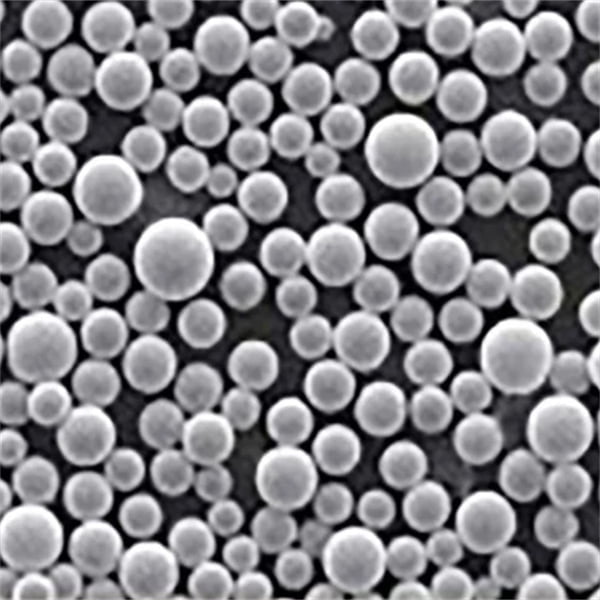
FAQ
Question | Answer |
---|---|
What is the difference between electroless nickel plating and electroplating? | Electroless nickel plating is an autocatalytic process that deposits nickel without the use of an external electrical current, while electroplating relies on an applied electric current to facilitate the deposition. |
Can nickling powder be applied to non-metallic substrates? | Yes, nickling powder can be effectively used on non-metallic substrates such as plastics, ceramics, and composites, provided that the surface is properly prepared and activated. |
How does the coating thickness affect the properties of the nickel layer? | Thicker coatings generally provide better corrosion and wear resistance, but there is a practical limit beyond which the coating may become brittle or prone to cracking. The optimal thickness depends on the specific application requirements. |
Is the nickling process environmentally friendly? | Compared to traditional electroplating processes, the electroless nickel plating process using nickling powder is generally considered more environmentally friendly due to the absence of hazardous cyanide-based solutions and reduced waste generation. |
How does the service life of components treated with nickling powder compare to untreated components? | Components treated with nickling powder often exhibit significantly extended service life, with some applications reporting up to 10 times longer lifespan compared to untreated counterparts, due to the improved corrosion and wear resistance. |
Share On
MET3DP Technology Co., LTD is a leading provider of additive manufacturing solutions headquartered in Qingdao, China. Our company specializes in 3D printing equipment and high-performance metal powders for industrial applications.
Inquiry to get best price and customized Solution for your business!
Related Articles
About Met3DP
Recent Update
Our Product
CONTACT US
Any questions? Send us message now! We’ll serve your request with a whole team after receiving your message.
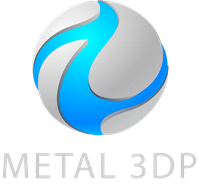
Metal Powders for 3D Printing and Additive Manufacturing