Aerospace-Grade Niobium Additive Manufacturing in France: A Comprehensive Guide for B2B Buyers
Table of Contents
1. Introduction: The Role of Niobium in Aerospace Additive Manufacturing
Niobium (Nb) is a highly sought-after refractory metal in the aerospace industry due to its high melting point, exceptional strength, and corrosion resistance. These properties make niobium an ideal material for additive manufacturing (AM), particularly for producing components that must withstand extreme temperatures and pressures.
Why Niobium is Critical for Aerospace 3D Printing
- High-Performance Alloys: Niobium is often alloyed with titanium, hafnium, and zirconium to improve mechanical properties.
- Superior Heat Resistance: Its high melting point (~2,477°C) makes it ideal for aerospace engine components.
- Corrosion and Oxidation Resistance: Ensures longevity and durability in harsh aerospace environments.
- Lightweight Strength: Niobium alloys provide a high strength-to-weight ratio, crucial for aircraft and space applications.
Applications of Niobium in Aerospace 3D Printing
Application | Benefits |
---|---|
Rocket Nozzles | High-temperature resistance, durability |
Turbine Blades | Increased strength, reduced weight |
Heat Shields | Protection against thermal fatigue |
Structural Components | High strength-to-weight ratio |
With the rise of additive manufacturing, aerospace manufacturers in France are increasingly adopting niobium powders for selective electron beam melting (SEBM) and laser powder bed fusion (LPBF) processes.
2. Market Trends and Growth Potential for Niobium 3D Printing in France
The aerospace industry in France is one of the most advanced in the world, with key players such as Airbus and Safran investing heavily in additive manufacturing. The demand for high-performance materials like niobium is rising due to:
Key Market Trends
- Growing Adoption of Metal Additive Manufacturing: French aerospace companies are leveraging 3D printing for rapid prototyping and production.
- Increased Demand for Lightweight Materials: Niobium’s strength-to-weight ratio makes it a preferred choice.
- Sustainability and Material Efficiency: Additive manufacturing reduces waste and optimizes material usage.
- Technological Advancements in AM Equipment: Companies like Metal3DP are developing high-precision 3D printers for aerospace applications.
Growth Potential in the French Market
Factor | Impact on Niobium AM |
---|---|
Aerospace Expansion | Increased demand for advanced materials |
Government Support for AM | Funding for research and development |
R&D in High-Performance Alloys | Enhanced niobium-based materials for aviation |
Supply Chain Localization | Reduced dependence on foreign suppliers |
With France positioning itself as a leader in aerospace innovation, the demand for niobium-based additive manufacturing is expected to grow significantly over the next decade.
3. Key Factors to Consider When Choosing a Niobium Powder Supplier
Selecting the right supplier for aerospace-grade niobium powder is critical to ensuring quality, consistency, and performance. Here are the essential factors to consider:
1. Powder Quality and Purity
- Ensure the supplier provides high-purity niobium powder (>99.9%).
- Verify the particle size distribution (PSD) for optimal flowability and packing density.
2. Production Technology
- Gas Atomization: Produces spherical, high-quality niobium powders with minimal contamination.
- PREP (Plasma Rotating Electrode Process): Ensures excellent powder uniformity and low oxygen content.
3. Certifications and Compliance
- Look for suppliers that adhere to aerospace standards such as AS9100, ISO 9001, and ASTM F3055.
- Ensure compliance with REACH and RoHS regulations in the European Union.
4. Consistency and Batch Traceability
- Reliable suppliers provide batch traceability for quality control.
- Consistent powder properties ensure repeatable AM results.
5. Delivery and Supply Chain Reliability
- Opt for suppliers with a strong logistical network in France.
- Consider lead times and availability to avoid production delays.
Comparison of Niobium Powder Suppliers
Supplier | Production Method | Certifications | Supply Chain Strength |
---|---|---|---|
Metal3DP | Gas Atomization, PREP | AS9100, ISO 9001 | Strong global network |
Supplier A | Gas Atomization | ISO 9001 | Moderate |
Supplier B | Water Atomization | No AS9100 | Limited |
Why Choose Metal3DP for Niobium Powder?
Metal3DP offers high-quality gas atomized and PREP niobium powders with exceptional spherical morphology, flowability, and purity—ideal for aerospace additive manufacturing.
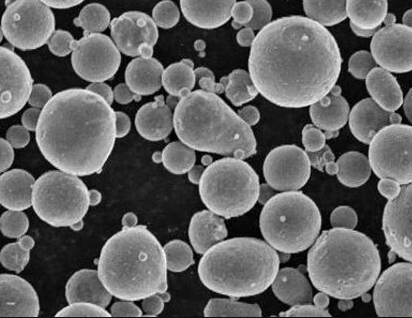
4. Top Niobium Powder Suppliers for Additive Manufacturing in France
Sourcing high-quality niobium powder for additive manufacturing in France requires working with reliable suppliers who adhere to strict aerospace standards. Below is a list of top suppliers offering aerospace-grade niobium powders for 3D printing applications.
Key Criteria for Selecting Niobium Powder Suppliers
- Powder Production Method: Gas atomization and PREP ensure high sphericity and flowability.
- Certifications: AS9100, ISO 9001, ASTM F3055 compliance for aerospace applications.
- Supply Chain Presence in France: Reliable local distribution and logistics.
Top Niobium Powder Suppliers in France
Supplier Name | Production Method | Certifications | Market Coverage |
---|---|---|---|
Metal3DP | Gas Atomization, PREP | AS9100, ISO 9001 | Global network, strong in France |
Aubert & Duval | Gas Atomization | ISO 9001, AS9100 | Strong French presence |
Eramet | Water Atomization | ISO 9001 | Moderate aerospace focus |
AMG Superalloys | PREP | AS9100, ISO 9001 | Limited in France |
Among these, Metal3DP stands out as a global leader in additive manufacturing powders, offering high-purity, aerospace-grade niobium powders optimized for laser powder bed fusion (LPBF) and electron beam melting (EBM) processes.
5. Why More Aerospace Companies Are Choosing Niobium for 3D Printing
The adoption of niobium in aerospace 3D printing is growing rapidly due to its superior material properties and cost-effectiveness in advanced manufacturing processes.
Key Benefits of Niobium in Aerospace Additive Manufacturing
- Superior Heat Resistance
- With a melting point of 2,477°C, niobium is ideal for high-temperature aerospace applications such as rocket nozzles and turbine blades.
- High Strength-to-Weight Ratio
- Niobium alloys offer lightweight structural integrity, making them perfect for reducing aircraft weight while maintaining durability.
- Excellent Oxidation and Corrosion Resistance
- Niobium-based components can withstand extreme environmental conditions, including oxidation and stress-induced corrosion.
- Improved Design Flexibility with Additive Manufacturing
- 3D printing allows for complex geometries and weight optimization, enabling the production of high-performance aerospace components.
Case Study: Niobium in Rocket Engine Components
Several leading aerospace manufacturers, including SpaceX and ArianeGroup, are integrating niobium-based superalloys into their rocket engines due to the metal’s ability to resist extreme heat and mechanical stress.
Aerospace Application | Niobium Benefits |
---|---|
Rocket Nozzles | High-temperature stability, durability |
Turbine Blades | Increased efficiency, reduced weight |
Heat Shields | Thermal fatigue resistance |
Engine Mounts | Lightweight and strong |
In France, aerospace giants such as Airbus and Safran are investing in niobium-based additive manufacturing to enhance aircraft performance and reduce production costs.
6. Why Choose Metal3DP for Your Aerospace-Grade Niobium Needs
When selecting a supplier for aerospace-grade niobium powders, it is essential to work with an experienced provider who offers high-purity materials, advanced manufacturing techniques, and reliable support.
Metal3DP: A Leader in Aerospace Additive Manufacturing
Metal3DP is a global expert in metal additive manufacturing, specializing in high-quality powders and 3D printing solutions for aerospace applications.
Why Metal3DP Stands Out
Feature | Metal3DP Advantage |
---|---|
High-Purity Niobium Powder | Produced using gas atomization and PREP for superior quality. |
Advanced Powder Morphology | Spherical particles ensure optimal flowability and packing density. |
Aerospace-Grade Certifications | Complies with AS9100, ISO 9001, and ASTM F3055. |
Strong Global Supply Chain | Fast delivery to France and other aerospace hubs. |
Support for Laser and Electron Beam Printing | Powders optimized for LPBF and EBM processes. |
Metal3DP’s Powder Production Technologies
Metal3DP employs two advanced production methods for aerospace-grade niobium powders:
- Gas Atomization:
- Produces highly spherical powders with excellent flowability.
- Ensures minimal impurities and consistent particle size.
- PREP (Plasma Rotating Electrode Process):
- Guarantees ultra-high purity with low oxygen content.
- Ideal for high-performance aerospace applications.
Customer Success Stories
Many aerospace companies worldwide trust Metal3DP for their high-performance metal powders. The company’s innovative approach to additive manufacturing enables customers to accelerate production, reduce costs, and improve part performance.
To learn more about Metal3DP’s aerospace solutions, visit the official website: Metal3DP Aerospace 3D Printing.
7. How to Order Aerospace-Grade Niobium Powder for Additive Manufacturing
When sourcing aerospace-grade niobium powder for additive manufacturing, it is crucial to follow a structured procurement process to ensure quality, consistency, and supply chain reliability.
Step-by-Step Guide to Ordering Niobium Powder
Step 1: Determine Your Requirements
Before placing an order, define the specifications that match your additive manufacturing process:
- Powder Particle Size: Choose the appropriate size distribution (e.g., 15-45µm for LPBF, 45-150µm for EBM).
- Purity Levels: Ensure the powder meets aerospace-grade purity standards (>99.9% niobium).
- Batch Volume: Determine the required quantity based on production needs.
Step 2: Select a Certified Supplier
It is essential to work with a trusted supplier who meets aerospace industry standards. Metal3DP is a global leader providing high-quality gas atomized and PREP-produced niobium powders with AS9100 and ISO 9001 certifications.
Step 3: Request a Sample for Testing
Before placing a bulk order, request a sample to:
- Test flowability and packing density.
- Evaluate printability in LPBF or EBM systems.
- Verify mechanical properties after sintering.
Step 4: Confirm Certification and Compliance
Ensure the supplier provides material certification documents, including:
- Chemical Composition Report
- Particle Size Distribution Analysis
- Sphericity and Flowability Data
- Compliance with ASTM F3055 (Niobium Powder Standard for AM)
Step 5: Place an Order and Arrange Logistics
Once the sample meets your requirements:
- Place a bulk order based on production volume.
- Select the most efficient shipping method for France.
- Coordinate with the supplier to ensure timely delivery.
Ordering from Metal3DP
Metal3DP provides a seamless ordering process for aerospace manufacturers in France:
Ordering Step | Metal3DP Advantage |
---|---|
Custom Powder Selection | Wide range of niobium and niobium-based alloys. |
Fast Sample Delivery | Test powder compatibility before bulk ordering. |
Certified Aerospace-Grade Powders | AS9100, ISO 9001, ASTM F3055 compliant. |
Global Logistics Network | Reliable shipping to France and Europe. |
To place an order, visit Metal3DP’s product page and request a quote today.
8. Future Innovations in Niobium Additive Manufacturing
The future of niobium additive manufacturing is shaped by advancements in material science, printing technologies, and aerospace applications.
Key Trends Shaping the Future of Niobium 3D Printing
1. Development of Niobium-Based Superalloys
Researchers are working on new niobium-titanium and niobium-hafnium alloys that offer:
- Higher thermal stability for jet engines.
- Increased oxidation resistance for hypersonic aircraft.
- Improved mechanical properties for space applications.
2. Advancements in Printing Technologies
Emerging laser and electron beam powder bed fusion (LPBF and EBM) techniques are improving:
- Part precision and surface finish.
- Production scalability for aerospace components.
- Reduction in residual stresses and porosity.
3. Sustainability and Recycling in AM
The recycling of niobium powder is becoming a priority to:
- Reduce material waste in additive manufacturing.
- Lower production costs for aerospace manufacturers.
- Ensure a more sustainable supply chain.
The Role of Metal3DP in Future Innovations
Metal3DP is continuously investing in advanced powder production techniques, ensuring:
- Higher purity levels for aerospace applications.
- Optimized particle size distribution for better printability.
- Innovative alloy development to meet future aviation needs.
As a leader in metal additive manufacturing, Metal3DP is at the forefront of revolutionizing niobium-based 3D printing for the aerospace industry.
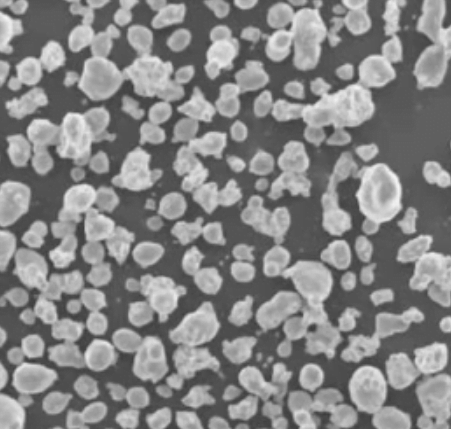
9. FAQs: Common Questions About Niobium Additive Manufacturing
Q1: Why is niobium used in aerospace additive manufacturing?
Niobium is used because of its high melting point, corrosion resistance, and lightweight strength, making it ideal for rocket nozzles, turbine blades, and heat shields.
Q2: How does niobium compare to titanium in 3D printing?
Property | Niobium (Nb) | Titanium (Ti) |
---|---|---|
Melting Point | 2,477°C | 1,668°C |
Corrosion Resistance | Excellent | High |
Weight | Heavier than Ti | Lightweight |
Strength-to-Weight Ratio | High | Very High |
Niobium is generally preferred for high-temperature applications, whereas titanium is favored for lightweight structural parts.
Q3: Can niobium powders be used in both laser and electron beam 3D printing?
Yes, niobium powders are suitable for LPBF and EBM processes, with particle sizes optimized for each method.
Q4: What is the best production method for aerospace-grade niobium powder?
Gas atomization and PREP (Plasma Rotating Electrode Process) produce the highest quality powders, ensuring:
- High sphericity and flowability.
- Minimal oxygen contamination.
- Consistent particle size distribution.
Q5: How can I source aerospace-grade niobium powder in France?
You can source high-quality niobium powder from trusted suppliers like Metal3DP, which offers AS9100-certified powders with global shipping options.
Conclusion: Unlock the Potential of Niobium Additive Manufacturing with Metal3DP
The aerospace industry in France is rapidly embracing niobium additive manufacturing for its high-performance, lightweight, and corrosion-resistant properties. With advancements in 3D printing technologies, niobium is set to play a crucial role in the future of aerospace engineering, hypersonic flight, and space exploration.
Why Choose Metal3DP for Niobium 3D Printing?
✅ High-purity niobium powders optimized for LPBF and EBM.
✅ Advanced powder production using gas atomization and PREP.
✅ Certified aerospace-grade materials (AS9100, ISO 9001, ASTM F3055).
✅ Reliable global supply chain with fast shipping to France.
✅ Innovative R&D in niobium-based superalloys.
Ready to source aerospace-grade niobium powders?
🔗 Request a quote today from Metal3DP!
By partnering with Metal3DP, aerospace manufacturers in France can unlock the full potential of niobium additive manufacturing and stay ahead in next-generation aviation and space technologies.
Share On
MET3DP Technology Co., LTD is a leading provider of additive manufacturing solutions headquartered in Qingdao, China. Our company specializes in 3D printing equipment and high-performance metal powders for industrial applications.
Inquiry to get best price and customized Solution for your business!
Related Articles
About Met3DP
Recent Update
Our Product
CONTACT US
Any questions? Send us message now! We’ll serve your request with a whole team after receiving your message.
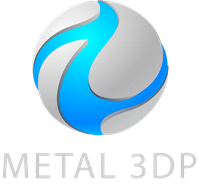
Metal Powders for 3D Printing and Additive Manufacturing