Complete gids voor waterverstuiving voor 3D printen van metaalpoeders
Inhoudsopgave
Stel je voor dat je laag voor laag ingewikkelde metalen voorwerpen beeldhouwt en ze vanaf de grond opbouwt met de precisie van een digitale kunstenaar. Dit is de magie van Metaalpoeders voor 3D printenen in het hart van deze revolutionaire technologie ligt een cruciaal ingrediënt: metaalpoeder. Maar hoe transformeren we massief metaal in het fijne, vloeibaar poeder dat nodig is voor 3D printen? Kijk op waterverstuivingEen krachtige en veelzijdige techniek die centraal staat in deze gids.
De magie onthullen: wat is waterverstuiving?
Zie waterverneveling als de kunst om gesmolten metaal om te zetten in een fijne nevel van kleine druppeltjes. Dit ogenschijnlijk eenvoudige proces heeft echter een immense kracht. Zo werkt het:
- Het metaal smelten: De reis begint met het gekozen metaal dat in een oven wordt verhit tot gesmolten toestand. Stel je een vurige smeltkroes voor, gloeiend van gesmolten metaal, klaar om getransformeerd te worden.
- H2O onder hoge druk: Vervolgens wordt er een waterstraal onder hoge druk op de stroom gesmolten metaal losgelaten. Deze krachtige straal, verwant aan een brandweerslang op steroïden, breekt het vloeibare metaal in een fijne nevel van kleine druppeltjes.
- Snelle stolling: Terwijl de metaaldruppels zich verspreiden, koelen ze snel af en stollen ze in de lucht, waarbij ze individuele metaalpoederdeeltjes vormen. Stel je kleine metalen regendruppels voor die stollen nog voor ze de grond raken.
- Verzameling en verwerking: Het nieuw gevormde metaalpoeder wordt verzameld, gedroogd en gezeefd om de gewenste deeltjesgrootte en -distributie te verkrijgen. Dit zorgt voor consistentie en optimale prestaties voor 3D printtoepassingen.
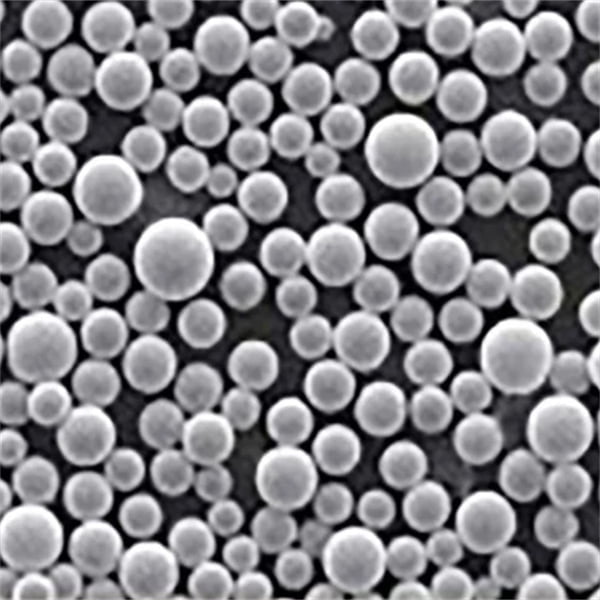
Metaalpoeders voor 3D printen: Waarom deze methode kiezen?
Functie | Voordeel | Uitleg |
---|---|---|
Ontwerpvrijheid | Zeer complexe geometrieën | In tegenstelling tot traditionele methoden zoals bewerken of gieten die afhankelijk zijn van subtractieve of formatieve technieken, bouwt 3D-printen met metaalpoeders onderdelen laag voor laag rechtstreeks op basis van een digitaal model. Dit maakt het mogelijk om ingewikkelde interne kenmerken, kanalen en roosterstructuren te creëren die onmogelijk of zeer onpraktisch zouden zijn met andere methoden. |
Materiaal veelzijdigheid | Breed scala aan metalen | Metaalpoeders zijn verkrijgbaar in een breed scala aan opties, van gangbare metalen zoals titanium en aluminium tot meer exotische materialen zoals Inconel en edelmetalen zoals goud. Hierdoor kunnen ingenieurs het perfecte materiaal kiezen voor de specifieke toepassing, rekening houdend met factoren zoals sterkte, gewicht, corrosiebestendigheid en biocompatibiliteit. |
Snelle prototypering | Snellere ontwerpiteratie | De digitale aard van 3D-printen maakt snelle en eenvoudige ontwerpwijzigingen mogelijk. Er kunnen wijzigingen worden aangebracht in het CAD-model en binnen een kort tijdsbestek kan een nieuw prototype worden geprint. Dit vermindert de ontwikkelingstijd en -kosten aanzienlijk in vergelijking met traditionele prototypingmethoden. |
Lichtgewicht | Ontwerp voor efficiëntie | Het vermogen om complexe interne structuren te creëren met 3D-geprinte metaalpoeders zorgt ervoor dat onderdelen licht van gewicht zijn en toch hun sterkte behouden. Dit is cruciaal in toepassingen zoals de lucht- en ruimtevaart en de automobielindustrie, waar gewichtsvermindering zich vertaalt in verbeterde brandstofefficiëntie en prestaties. |
Productie op aanvraag | Verminderde voorraadbehoeften | 3D-printen met metaalpoeders maakt het mogelijk om onderdelen te produceren wanneer nodig, waardoor de noodzaak voor grote productieruns en opslag van afgewerkte producten vervalt. Dit is met name gunstig voor productie in kleine volumes of reserveonderdelen die mogelijk niet direct beschikbaar zijn via traditionele kanalen. |
Minimaal materiaalverlies | Duurzame productie | Metaal 3D-printen gebruikt alleen het materiaal dat nodig is om het onderdeel te bouwen, in tegenstelling tot traditionele methoden die aanzienlijk afvalmateriaal genereren. Dit vermindert afval en verlaagt de milieu-impact van het productieproces. |
Maatwerk | Gepersonaliseerde producten | De mogelijkheid om complexe geometrieën te creëren met 3D-geprinte metaalpoeders maakt de productie van zeer aangepaste onderdelen mogelijk. Dit is gunstig voor toepassingen zoals medische implantaten, protheses en tandkronen die een perfecte pasvorm voor elk individu vereisen. |
Consolidatie van onderdelen | Verminderde assemblagecomplexiteit | De ontwerpvrijheid die 3D-geprinte metaalpoeders bieden, maakt het mogelijk om complexe onderdelen te creëren die de functionaliteit van meerdere componenten integreren. Dit vermindert de complexiteit van de assemblage, verlaagt de productiekosten en verbetert de algehele prestatie van het product. |
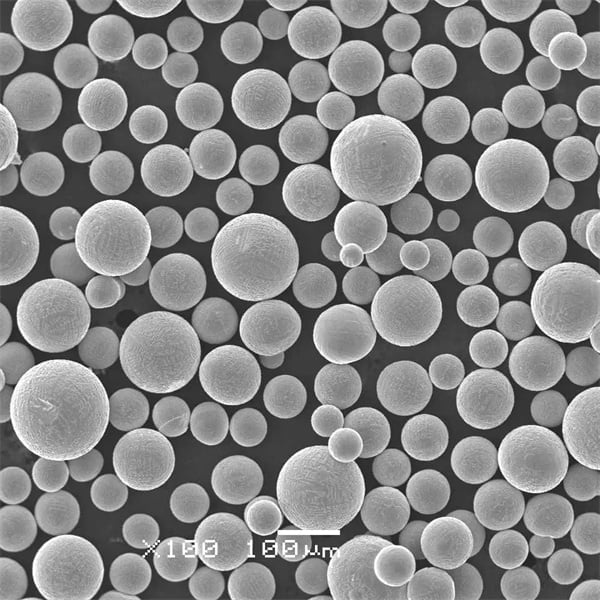
Waterverstuivingstoepassingen bij 3D printen: Metaal tot leven brengen
Proces | Beschrijving | Voordelen | Nadelen |
---|---|---|---|
Waterverneveling | Gesmolten metaal wordt via een meerstappenproces omgezet in een fijn poeder. Eerst wordt het metaal gesmolten in een oven. Vervolgens dwingt een hogedrukspuit het vloeibare metaal in een dunne stroom. Deze stroom wordt door een hogesnelheidswaterstraal in kleine druppeltjes gebroken. Ten slotte stollen de snel afgekoelde druppeltjes tot afzonderlijke poederdeeltjes, die worden verzameld, gedroogd en gezeefd om een specifieke grootte en verdeling te bereiken. | – Kosteneffectief: Waterverneveling biedt een relatief goedkope methode voor het produceren van grote hoeveelheden metaalpoeder in vergelijking met andere technieken. – Brede materiaalcompatibiliteit: Deze methode kan een breed spectrum aan metalen aan, van gangbare soorten zoals staal en aluminium tot meer gespecialiseerde opties. | – Deeltjesvorm: Water-geatomiseerde poeders zijn doorgaans minder bolvormig dan die welke met andere methoden worden geproduceerd. Dit kan de vloeibaarheid van het poeder en de pakkingsdichtheid in het 3D-printbed beïnvloeden, wat mogelijk de oppervlaktekwaliteit van het uiteindelijke geprinte onderdeel beïnvloedt. |
Selectief lasersmelten (SLM) | Een 3D-printtechniek die gebruikmaakt van een krachtige laser om metaalpoederdeeltjes selectief te smelten en te fuseren, laag voor laag. De laserstraal volgt een digitaal ontwerp en bouwt het gewenste 3D-object op. | – Hoge precisie en nauwkeurigheid: SLM maakt het mogelijk om complexe geometrieën met nauwe toleranties te creëren, waardoor het ideaal is voor ingewikkelde metalen onderdelen. – Ontwerpvrijheid: In tegenstelling tot traditionele productiemethoden biedt SLM een aanzienlijke ontwerpvrijheid, waardoor de productie van onderdelen met interne kanalen, roosters en andere unieke kenmerken mogelijk is. | – Beperkt bouwvolume: huidige SLM-machines hebben doorgaans een beperkt bouwvolume, waardoor de grootte van afdrukbare objecten beperkt is. – Oppervlakteruwheid: Door de laag-voor-laag-aard van SLM kan het oppervlak van de geprinte onderdelen licht ruw zijn, wat extra nabewerking vereist. |
Elektronenbundelsmelten (EBM) | Vergelijkbaar met SLM gebruikt EBM een krachtige bundel, maar in dit geval werkt een elektronenbundel in een vacuümomgeving. De elektronenbundel smelt de metaalpoederdeeltjes en smelt ze samen om het gewenste 3D-object te vormen. | – Superieure mechanische eigenschappen: EBM produceert onderdelen met uitstekende mechanische eigenschappen, waaronder hoge sterkte en goede vermoeidheidsweerstand. Dit komt door de vacuümomgeving, die oxidatie minimaliseert en materiaaleigenschappen verbetert. – Bredere materiaalcompatibiliteit: Vergeleken met SLM biedt EBM compatibiliteit met een breder scala aan metalen, waaronder reactieve materialen zoals titanium. | – Hogere kosten: EBM-systemen zijn over het algemeen duurder dan SLM-machines, wat van invloed is op de totale productiekosten. – Vacuümvereiste: De noodzaak van een vacuümomgeving voegt complexiteit toe aan het EBM-proces en kan de toegankelijkheid ervan in bepaalde omgevingen beperken. |
Binder Jetting (BJ) | Een 3D-printmethode die gebruikmaakt van een vloeibaar bindmiddel om selectief metaalpoederdeeltjes op een printplatform te inkjeten. De lagen worden vervolgens uitgehard om een solide structuur te creëren. | – Groot bouwvolume: Binder jetting biedt een groter bouwvolume vergeleken met SLM en EBM, waardoor de productie van grotere metalen onderdelen mogelijk is. – Potentieel voor full-colour bedrukking: Binder jetting-technieken die gekleurde bindmiddelen bevatten, zijn in ontwikkeling en bieden mogelijkheden voor het creëren van functionele en visueel aantrekkelijke metalen onderdelen. | – Lagere onderdeelsterkte: onderdelen die zijn geproduceerd via binder jetting vertonen doorgaans een lagere sterkte vergeleken met onderdelen die zijn gemaakt met SLM of EBM. Dit kan extra nabewerkingsstappen, zoals infiltratie, noodzakelijk maken om de gewenste mechanische eigenschappen te bereiken. – Beperkte materiaalopties: Binder Jetting heeft momenteel een beperkter aanbod aan compatibele metaalmaterialen vergeleken met andere 3D-printmethoden. |
Het kiezen van het juiste watervernevelde metaalpoeder
Factor | Beschrijving | Impact op het additieve productieproces en het laatste onderdeel |
---|---|---|
Materiaaleigenschappen | Het specifieke metaal of de legering die wordt gekozen, bepaalt de uiteindelijke eigenschappen van het 3D-geprinte onderdeel. | • Sterkte en duurzaamheid: Denk aan toepassingen die een hoge sterkte-gewichtsverhouding vereisen, zoals componenten voor de lucht- en ruimtevaart. Nikkellegeringen of titaniumpoeders excelleren hier. • Corrosieweerstand: Onderdelen die worden blootgesteld aan zware omstandigheden kunnen baat hebben bij roestvrij staal of koperlegeringen. • Thermische geleidbaarheid en elektrische geleidbaarheid: Koellichamen of elektrische geleiders kunnen aluminium- of koperpoeders gebruiken voor optimale prestaties. |
Deeltjesgrootte en -verdeling | De grootte en variatie in grootte van de poederdeeltjes hebben een grote invloed op de printbaarheid en de eigenschappen van het uiteindelijke onderdeel. | • Vloeibaarheid: Uniforme, bolvormige deeltjes stromen gemakkelijker, wat leidt tot een consistente laagvorming tijdens het printen. • Verpakkingsdichtheid: De ideale poederverpakkingsdichtheid zorgt voor een maximale benutting van het materiaal en een goede versmelting tussen de lagen. • Afwerking oppervlak: Fijnere poeders zorgen over het algemeen voor een gladder oppervlak op het uiteindelijke onderdeel. • Mechanische eigenschappen: De deeltjesgrootte en -verdeling kunnen van invloed zijn op de sterkte, porositeit en ductiliteit van het uiteindelijke onderdeel. |
Deeltjesmorfologie | De vorm van de poederdeeltjes beïnvloedt hun pakkingsgedrag en vloeibaarheid. | • Sfericiteit: Zeer bolvormige deeltjes bieden een superieure vloeibaarheid en pakkingsdichtheid, wat leidt tot een betere bedrukbaarheid. • Satellieten en satellietdeeltjes: Dit zijn kleinere deeltjes die aan grotere deeltjes vastzitten. Overmatige satellieten kunnen de vloeibaarheid belemmeren en leiden tot inconsistenties in het geprinte onderdeel. • Holle deeltjes: Holle deeltjes zorgen weliswaar voor gewichtsvermindering, maar ze kunnen ook interne holtes in het uiteindelijke onderdeel creëren, waardoor de mechanische sterkte wordt beïnvloed. |
Chemische samenstelling en poederzuiverheid | De aanwezigheid van onzuiverheden of afwijkingen van de gewenste chemische samenstelling kunnen van invloed zijn op het printproces en de uiteindelijke kwaliteit van het onderdeel. | • Zuurstofinhoud: Te veel zuurstof kan leiden tot een hogere porositeit en verminderde mechanische eigenschappen. • Vochtgehalte: Vocht kan tijdens het drukproces spatten veroorzaken en tot oppervlaktedefecten leiden. • Sporenelementen: De aanwezigheid van onbedoelde elementen kan de eigenschappen en bedrukbaarheid van het materiaal beïnvloeden. Betrouwbare leveranciers leveren gedetailleerde chemische analyserapporten om naleving van materiaalspecificaties te garanderen. |
Poeder vloeibaarheid | Het gemak waarmee het poeder stroomt, is cruciaal voor een consistente laagvorming in additieve productieprocessen. | Een slechte vloeibaarheid kan leiden tot: • Inconsistente laagdikte • Scheiding van deeltjes in het poederbed • Moeilijkheden met materiaalverspreidingsmechanismen Al deze zaken kunnen een negatieve invloed hebben op de kwaliteit en maatnauwkeurigheid van het eindproduct. |
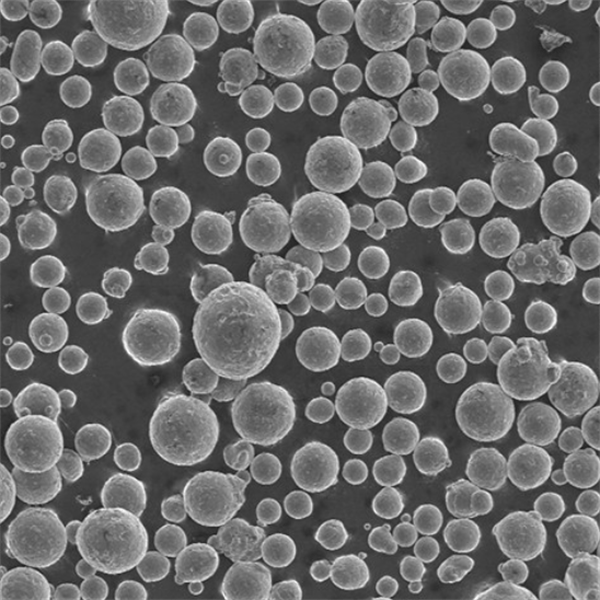
Geavanceerde overwegingen voor wateratomisatie
Factor | Beschrijving | Impact op het proces | Matigingsstrategieën |
---|---|---|---|
Meercomponenten grondstof | Bij het atomiseren van legeringen of slurries met meerdere componenten zijn factoren als deeltjesgrootteverdeling en uniformiteit van de samenstelling van cruciaal belang. | Tijdens de atomisering kan er scheiding van componenten optreden, waardoor er variaties in de eigenschappen van het eindproduct ontstaan. | – Gecontroleerd mengen: Door gebruik te maken van high-shear mengers of inline homogenisatoren kan een gelijkmatige verdeling van componenten in de grondstof worden gegarandeerd. – Co-atomisatie: Door gelijktijdige verneveling van afzonderlijke elementen kan een nauwkeurige controle over de uiteindelijke samenstelling worden verkregen. – Monitoring- en feedbacksystemen: Dankzij realtimebewaking van de deeltjesgrootte en -samenstelling kunt u de atomiseringsparameters aanpassen voor een consistente productkwaliteit. |
Deeltjesmorfologie | De vorm en oppervlakte-eigenschappen van de vernevelde deeltjes hebben een grote invloed op de verdere processen, zoals poederverwerking, sinteren en de prestaties van het eindproduct. | Onregelmatige deeltjesvormen kunnen leiden tot problemen met de pakkingsdichtheid, vloeibaarheid en sintergedrag. | – Vernevelingsdruk en spuitmondontwerp: Door deze parameters te optimaliseren, kunt u de mate van druppelafbraak en stolling beïnvloeden, wat leidt tot meer bolvormige deeltjes. – Selectie oppervlakteactieve stof: Er kunnen specifieke oppervlakteactieve stoffen aan de waterstroom worden toegevoegd om de oppervlaktespanning te wijzigen en een uniformere deeltjesmorfologie te bevorderen. – Snelle stolling: Technieken zoals hogedrukverneveling of snel blussen kunnen de deeltjesgroei minimaliseren en meer bolvormige vormen bevorderen. |
Milieu-impact | Bij waterverstuivingsprocessen kan afvalwater ontstaan dat metaaldeeltjes bevat en een aanzienlijk waterverbruik vereist. | Onbehandelde afvalwaterlozing brengt gevaren voor het milieu met zich mee. Hoog waterverbruik kan de hulpbronnen belasten. | – Waterrecyclingsystemen: Gesloten systemen kunnen worden geïmplementeerd om het vernevelingswater op te vangen en te behandelen, waardoor afval en waterverbruik tot een minimum worden beperkt. – Vlokvorming en bezinking: Deze technieken kunnen worden gebruikt om metaaldeeltjes uit het afvalwater te scheiden voordat het wordt behandeld en afgevoerd. – Geavanceerde filtratiesystemen: Membraanfiltratie of ionenuitwisselingsprocessen kunnen worden gebruikt om verontreinigingen op een zeer efficiënte manier uit afvalwater te verwijderen. |
Procesautomatisering en -controle | Integratie van automatisering en realtime procesbesturing kan de consistentie en efficiëntie aanzienlijk verbeteren. | Handmatige bediening kan leiden tot menselijke fouten en inconsistenties in de productkwaliteit. | – Geautomatiseerde besturingssystemen: Door feedbackloops en geautomatiseerde aanpassingen op basis van sensorgegevens te implementeren, wordt een consistente productkwaliteit gegarandeerd. – Geavanceerde bewakingssystemen: Realtimebewaking van kritische parameters zoals stroomsnelheden, druk en deeltjeseigenschappen maakt proactieve aanpassingen en optimalisaties mogelijk. – Integratie van machinaal leren: Machine learning-algoritmen kunnen historische gegevens en sensormetingen analyseren om mogelijke problemen te voorspellen en procesparameters te optimaliseren voor een betere efficiëntie en opbrengst. |
Veiligheidsoverwegingen | Bij waterverstuivingsprocessen zijn hoge druk, bewegende onderdelen en mogelijke blootstelling aan metaaldeeltjes betrokken. | Onjuiste veiligheidsprocedures kunnen leiden tot ongelukken en verwondingen. | – Juiste training en persoonlijke beschermingsmiddelen (PBM): Een grondige training van operators over veilige bedieningsprocedures en het gebruik van de juiste PBM's is van cruciaal belang. – Regelmatig onderhoud en inspectie: Door preventieve onderhoudsschema's en veiligheidsinspecties te implementeren, minimaliseert u apparatuurstoringen en mogelijke gevaren. – Behuizingsontwerp en ventilatiesystemen: Door hogedrukgebieden af te sluiten en goede ventilatiesystemen te gebruiken, wordt de blootstelling aan zwevende metaaldeeltjes beperkt. |
FAQ
Vraag | Antwoord |
---|---|
Wat zijn de typische deeltjesgroottes van watergeatomiseerde metaalpoeders voor 3D printen? | Het bereik van de deeltjesgrootte valt meestal tussen 10 en 150 micrometer (µm)waarbij het specifieke bereik varieert afhankelijk van het gekozen metaal en de gewenste toepassing. |
Kunnen watergeatomiseerde metaalpoeders worden gerecycled? | Ja, met water geatomiseerde metaalpoeders kunnen gerecycleerd door middel van verschillende technieken, zoals hersmelten en heratomiseren. Dit bevordert duurzaamheid en minder afval. |
Hoe verhoudt waterverstuiving zich tot andere productiemethoden voor metaalpoeder? | Hoewel verneveling met water voordelen biedt op het gebied van kosteneffectiviteit en productiesnelheidAndere methoden zoals gasverneveling zou kunnen opleveren meer bolvormige deeltjes en zijn geschikt voor reactieve metalen. De keuze hangt uiteindelijk af van de specifieke toepassing en de gewenste eigenschappen. |
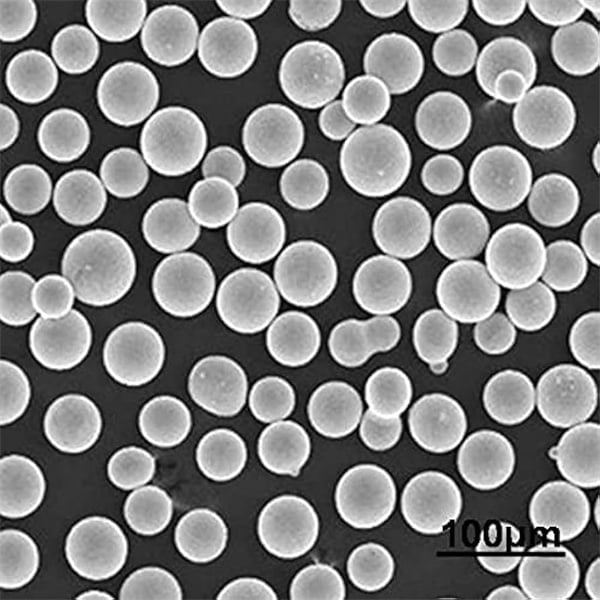
Conclusie: Het potentieel van waterverstuiving omarmen
Terwijl de wereld van 3D printen blijft evolueren, blijft waterverstuiving een hoeksteentechnologie, die een betrouwbaar en kosteneffectief middelen om metaalpoeders voor verschillende toepassingen te produceren. Van complexe lucht- en ruimtevaartonderdelen naar ingewikkelde medische implantatenMet watergeatomiseerde poeders kunnen diverse en functionele 3D-geprinte onderdelen worden gemaakt.
Vooruitkijkend zit de toekomst van waterverneveling boordevol potentieel. Voortdurende vooruitgang in de technologie belooft:
- Verbeterde deeltjesvorm: Via verfijningen in verstuivingstechnieken en de verkenning van innovatieve materialende sfericiteit van watergeatomiseerde poeders kan verder worden verbeterd, mogelijkerwijs overeenkomen met de kwaliteit bereikt met duurdere methoden zoals gasverstuiving.
- Uitgebreide materiaalcompatibiliteit: Onderzoekers onderzoeken actief het potentieel van waterverstuiving voor een breder scala aan metalenwaaronder zeer reactieve materialen die een uitdaging vormen voor conventionele methoden. Dit zou nieuwe wegen kunnen openen voor 3D-printtoepassingen in veeleisende industrieën zoals ruimtevaart en geneeskunde.
- Duurzame vooruitgang: De focus op milieuverantwoordelijkheid is de drijvende kracht achter de ontwikkeling van milieuvriendelijke watervernevelingsprocessen. Dit kan het volgende inhouden gesloten-lussystemen die het waterverbruik en de afvalproductie minimaliseren, wat bijdraagt aan een meer duurzame toekomst voor de productie van metaalpoeder voor 3D-printen.
Door het potentieel van wateratomisatie te omarmen en de grenzen ervan voortdurend te verleggen, kunnen we een toekomst ontsluiten waarin 3D-printen van metaal een nog belangrijkere rol gaat spelen. krachtige en veelzijdige technologieDe wereld om ons heen op innovatieve en transformerende manieren vormgeven.
Delen op
MET3DP Technology Co, LTD is een toonaangevende leverancier van additieve productieoplossingen met hoofdkantoor in Qingdao, China. Ons bedrijf is gespecialiseerd in 3D printapparatuur en hoogwaardige metaalpoeders voor industriële toepassingen.
Onderzoek om de beste prijs en een op maat gemaakte oplossing voor uw bedrijf te krijgen!
gerelateerde artikelen
Over Met3DP
Recente update
Ons product
NEEM CONTACT MET ONS OP
Nog vragen? Stuur ons nu een bericht! Na ontvangst van uw bericht behandelen wij uw verzoek met een heel team.
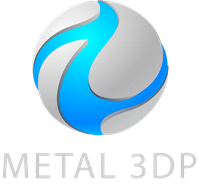
Metaalpoeders voor 3D printen en additieve productie