Poeders voor 3D afdrukken
Inhoudsopgave
3D printen, ook bekend als additive manufacturing (AM), maakt gebruik van gespecialiseerde poeders om driedimensionale onderdelen te construeren in opeenvolgende lagen. Deze gids is een diepgaand naslagwerk over poeders voor 3D printen - met informatie over types, eigenschappen, specificaties, productiemethoden, belangrijkste leveranciers en prijzen, toepassingen in verschillende sectoren, vergelijkingen met alternatieven, veelgestelde vragen en nog veel meer.
Overzicht van Poeders voor 3D afdrukken
3D-printpoeders zijn grondstoffen voor de productie van additieve onderdelen in kunststof, metaal en keramiek. Belangrijkste kenmerken:
- Staat: Ultrafijne deeltjespoeders
- Groottebereik: Gewoonlijk 10-150 micron
- Morfologie: Meestal bolvormige deeltjesvorm
- Samenstelling: Polymeer, metaallegering, keramiek, zandsteenmengsels
- Belangrijkste eigenschappen: Ontwikkelde deeltjesgrootteverdeling, stroombaarheid, verpakkingsdichtheid en microstructuur
Door de fysische eigenschappen van het poeder en de interacties met thermische/kinetische printprocessen onder controle te houden, maken 3D-printpoeders ingewikkelde onderdeelgeometrieën en gradiënten in materiaalsamenstelling mogelijk die anders niet haalbaar zijn.
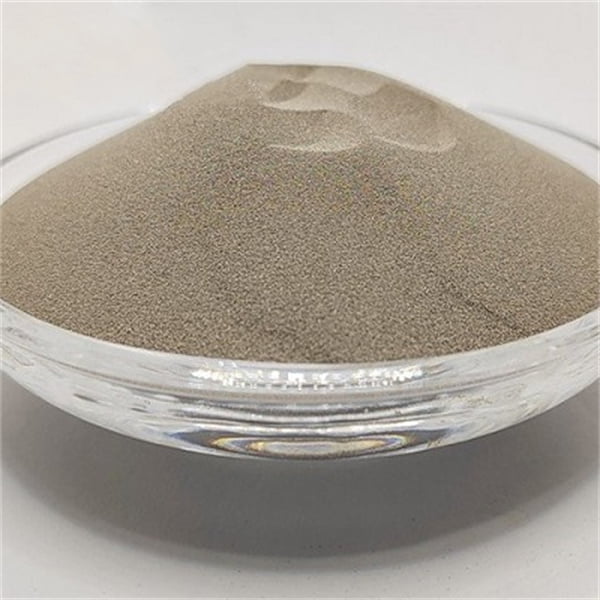
Soorten 3D Printing poeders
Categorie | Materialen | Afdrukmethode |
---|---|---|
Kunststoffen | Nylons, ABS, TPU, PEKK, PEEK ... | Selectief lasersinteren (SLS) |
Metalen | Roestvrij staal, gereedschapsstaal, titanium & legeringen, superlegeringen ... | Direct metaallasersinteren (DMLS) |
Keramiek | Aluminiumoxide, zirkoniumoxide, siliciumcarbide | Binder jetting, gesmolten afzetting modelleren |
Composieten | Metaal/kunststofmengsels, zandsteenmengsels | Meerstraalsfusie (MJF), gebonden metaalafzetting |
Biocompatibel | PEEK, PLGA, TCP... | Selectief lasersmelten (SLM) |
Tafel 1: Belangrijkste categorieën, materialen en bijbehorende printplatforms voor commerciële 3D-printpoeders
Polymeer-, metaal-, keramiek- en composietpoeders ondersteunen de productie van onderdelen voor eindgebruik in de lucht- en ruimtevaart, de auto-industrie, de medische, tandheelkundige en industriële markten.
Productiemethoden
Methode | Beschrijving | Geschiktheid materiaal | Voordelen | Nadelen |
---|---|---|---|---|
Verneveling | Deze overkoepelende term omvat verschillende technieken die gesmolten metaal afbreken tot fijne deeltjes. Het gesmolten metaal wordt door een mondstuk in een gas- of waterstroom onder hoge druk geperst, waardoor de druppels snel stollen tot bolvormige deeltjes. | Metalen (ijzer, aluminium, titaniumlegeringen) | - Hoge productiesnelheid - Consistente deeltjesgrootte en -vorm - Goede poederstroombaarheid | - Vereist hoge energie-input - Kans op oxidevorming op deeltjes - Beperkt tot bepaalde materialen |
Gasverstuiving | De meest gebruikte verstuivingsmethode, waarbij een inert gas (meestal stikstof) wordt gebruikt om het gesmolten metaal op te breken. | Vergelijkbaar met verstuiving, maar over het algemeen betere oppervlaktekwaliteit en betere controle over de deeltjesgrootte. | - Superieure poederkwaliteit in vergelijking met andere verstuivingsmethoden - Geschikt voor reactieve metalen | Vergelijkbaar met verstuiving, maar hogere materiaalkosten |
Waterverneveling | Gebruikt een waterstraal onder hoge druk om het gesmolten metaal te fragmenteren. Dit is kosteneffectiever dan gasverstuiving, maar produceert minder bolvormige deeltjes. | Sommige metalen (ijzer, koper) en sommige polymeren | - Lagere kosten dan gasverstuiving - Zeer geschikt voor vochtgevoelige materialen | - Lagere poederkwaliteit (onregelmatige vormen) - Mogelijk niet ideaal voor toepassingen met hoge prestaties |
Plasma-verneveling | Een vlamboog verhit het basismateriaal (metaaldraad of poeder) tot een gesmolten toestand. Het gesmolten metaal wordt dan door een mondstuk uitgeworpen en geatomiseerd met behulp van een plasmatoorts. | Breed scala aan materialen (metalen, legeringen, keramiek) | - Kan materialen met een hoog smeltpunt verwerken - Geschikt voor het maken van samengestelde poeders | - Complex en duur proces - Vereist strenge veiligheidsmaatregelen |
Mechanische vergruizing | Een fysisch proces dat bulkmateriaal vermaalt of maalt tot fijn poeder. | Brosse materialen (keramiek, sommige polymeren) | - Eenvoudigere en goedkopere opstelling vergeleken met andere methoden | - Beperkte controle over deeltjesgrootte en morfologie - Kan onzuiverheden introduceren tijdens het malen |
Chemische dampdepositie (CVD) | Een chemisch proces waarbij gasvormige precursoren reageren om een vaste afzetting te vormen op een zaaddeeltje. | Metalen, keramiek en sommige geavanceerde materialen | - Hoge zuiverheid en nauwkeurige controle over deeltjescompositie - Kan complexe geometrieën creëren | - Langzaam proces met beperkte productiesnelheid - Hoge kapitaalinvestering |
Elektrolytische verstuiving | Een elektrolytische cel wordt gebruikt om een metalen anode te ontbinden in ionen. De ionen combineren dan met elektronen aan de kathode om metaaldeeltjes te vormen. | Metalen | - Milieuvriendelijk proces (vermijdt hoge temperaturen) - Geschikt voor vochtgevoelige materialen | - Lagere productiesnelheid dan verstuivingsmethoden - Beperkt tot bepaalde elektrolyten en anodematerialen |
Sferoïdie | Een aanvullend proces dat wordt gebruikt om de vorm te verbeteren van onregelmatig gevormde poeders die met andere methoden zijn geproduceerd. Het omvat een warmtebehandeling of chemische processen om de samenklontering van de deeltjes tot bolletjes te bevorderen. | Meeste soorten poeder (metalen, polymeren, keramiek) | - Verbetert de vloeibaarheid van poeder en verpakkingsdichtheid - Verbetert de printbaarheid | - Voegt een extra verwerkingsstap toe - Mogelijk niet nodig voor alle toepassingen |
Eigenschappen van Poeders voor 3D afdrukken
Eigendom | Beschrijving | Belang voor 3D printen | Voorbeelden en overwegingen |
---|---|---|---|
Deeltjesgrootte en -verdeling | Verwijst naar de variatie in grootte van individuele poederdeeltjes en de algemene spreiding over verschillende groottebereiken. Gemeten in micrometers (µm). | Speelt een cruciale rol in de printbaarheid, resolutie en dichtheid van het uiteindelijke onderdeel. – Te groot: belemmerde vloeibaarheid, ongelijkmatige verspreiding en kans op harkfouten. – Te klein: Een groter oppervlak kan leiden tot aankoeken en slechte verpakking, wat de sterkte beïnvloedt. | – SLS (Selective Laser Sintering): Geeft over het algemeen de voorkeur aan fijnere poeders (20-80 µm) voor gedetailleerde vormen. – MJF (Multi Jet Fusion): Iets grotere deeltjes (50-100 µm) kunnen worden gebruikt dankzij het vermogen van inkjettechnologie om stroombeperkingen te overwinnen. – Metaalpoeders: Een strakke verdeling (smal bereik) is ideaal voor een goede verpakkingsdichtheid en minimale porositeit in het uiteindelijke onderdeel. |
Deeltjesmorfologie | De vorm van individuele poederdeeltjes. | Heeft invloed op hoe goed de deeltjes samenpakken, de vloeibaarheid en de oppervlakteafwerking van het uiteindelijke onderdeel. - Bolvormig: Bieden de beste verpakkingsdichtheid en vloeibaarheid, wat leidt tot sterke en uniforme onderdelen. - Onregelmatige vormen: Kan openingen en inconsistenties creëren, wat de sterkte en oppervlaktekwaliteit kan aantasten. | – Plastic poeders: Over het algemeen bolvormig of bijna-bolvormig voor optimale bedrukbaarheid. - Metaalpoeders: Kan variëren afhankelijk van het metaal en de productiemethode. Sferische morfologieën hebben de voorkeur, maar kunnen worden bereikt door nabewerkingstechnieken zoals verstuiving. |
Vloeibaarheid | Het gemak waarmee poeder vloeit onder zijn eigen gewicht of met minimale schuifkracht. | Essentieel voor consistente materiaalafzetting en gelijkmatige laagvorming tijdens het printen. - Goede vloeibaarheid: Zorgt voor een soepele verspreiding en minimaliseert het risico op laagdefecten. - Slechte vloeibaarheid: Kan leiden tot ongelijkmatige afzetting, inconsistenties en mogelijke drukproblemen. | – Poeders met een smalle deeltjesgrootteverdeling hebben de neiging om beter te stromen door minder interferentie met de deeltjesgrootte. - Additieven en oppervlaktebehandelingen kan worden gebruikt om de vloeibaarheid te verbeteren door de wrijving tussen de deeltjes te verminderen. |
Verpakkingsdichtheid | De maat voor hoe dicht poederdeeltjes samengepakt kunnen worden. Uitgedrukt als een percentage van het totale volume dat door het poeder wordt ingenomen. | Beïnvloedt de uiteindelijke dichtheid, sterkte en maatnauwkeurigheid van het geprinte onderdeel. - Hoge verpakkingsdichtheid: Leidt tot dichtere onderdelen met betere mechanische eigenschappen en maatnauwkeurigheid. - Lage verpakkingsdichtheid: Resulteert in onderdelen met een hogere porositeit, mogelijk zwakker en minder maatvast. | – Deeltjesvorm speelt een belangrijke rol. Bolvormige deeltjes pakken efficiënter in dan onregelmatige vormen. - Processen zoals Binder Jetting kunnen baat hebben bij een iets lagere verpakkingsdichtheid om een goede infiltratie van het bindmiddel mogelijk te maken. |
Sinterbaarheid | Het vermogen van poederdeeltjes om samen te smelten of te hechten tijdens het 3D printproces, meestal door hitte of laserenergie. | Essentieel voor het maken van sterke en functionele geprinte onderdelen. - Goede sinterbaarheid: Maakt een sterke interdeeltjesbinding mogelijk, wat leidt tot robuuste en functionele onderdelen. - Slechte sinterbaarheid: Kan leiden tot zwakke verbindingen en mogelijk falen van onderdelen onder spanning. | – Materiaalsamenstelling: Metalen hebben over het algemeen een goede sinterbaarheid door hun inherente vermogen om sterke bindingen te vormen bij hoge temperaturen. - Polymeerpoeders vereisen vaak specifieke additieven of nabewerkingsstappen (bijvoorbeeld sinterovens) om de hechting te verbeteren. |
Chemische samenstelling | De elementaire samenstelling van het poedermateriaal. | Bepaalt de uiteindelijke eigenschappen van het geprinte onderdeel, zoals sterkte, hittebestendigheid en biocompatibiliteit. - Materiaalkeuze is cruciaal op basis van de gewenste toepassing en functionele vereisten. - Poeders kunnen worden gemengd om specifieke eigenschappen te verkrijgen (bijvoorbeeld het combineren van metalen voor een betere sterkte-gewichtsverhouding). | – Metaalpoeders kunnen variëren van pure metalen zoals titanium tot complexe legeringen met op maat gemaakte eigenschappen. - Polymeerpoeders kunnen nylons, polyamiden en biocompatibele materialen voor medische toepassingen zijn. |
Thermische eigenschappen | Het gedrag van het poedermateriaal onder verschillende temperaturen, inclusief smeltpunt, thermische geleidbaarheid en thermische uitzettingscoëfficiënt. | Invloedsfactoren zoals maatvastheid, kromtrekken en warmtevervorming tijdens het printen en de nabewerking. - Gecontroleerde verwarming is essentieel om te voorkomen dat de thermische grenzen van het materiaal worden overschreden en er defecten aan het onderdeel ontstaan. - Thermische eigenschappen van poeder en bouwplatform op elkaar afstemmen minimaliseert kromtrekken en garandeert maatnauwkeurigheid. | – Metaalpoeders hebben vaak een hoog smeltpunt en vereisen een nauwkeurige temperatuurregeling tijdens lasergebaseerde processen zoals SLM (Selective Laser Melting). - Polymeerpoeders kan zacht worden of smelten bij lagere temperaturen, |
3D-Printpoeder Specificaties
Eigendom | Beschrijving | Invloed op printbaarheid en productkwaliteit | Materiaal Voorbeelden |
---|---|---|---|
Deeltjesgrootte en -verdeling | Verwijst naar de individuele deeltjesdiameters en de variatie binnen het poeder. Gemeten in micron (µm). | Fijne poeders ( 100 µm) verbeteren de vloeibaarheid, maar kunnen de detaillering beperken en de oppervlakteruwheid verhogen. Een smalle grootteverdeling zorgt voor een consistente verpakking en printgedrag. | Polymeren: Nylon (15-75 µm), polypropyleen (40-100 µm) |
Deeltjesmorfologie | De vorm van individuele poederdeeltjes. | Bolvormige deeltjes vloeien vrij en pakken efficiënt in, wat leidt tot een goede bedrukbaarheid. Onregelmatige vormen kunnen de onderlinge binding tussen de deeltjes verbeteren, maar kunnen stromingsproblemen veroorzaken en specifieke printtechnieken vereisen. | Polymeren: Meestal bolvormig door productieprocessen. |
Schijnbare dichtheid & verpakkingsdichtheid | Schijnbare dichtheid is het gewicht van poeder per volume-eenheid in losse, gegoten toestand. Verpakkingsdichtheid is de maximale dichtheid die kan worden bereikt na kloppen of trillen. | Schijnbare dichtheid beïnvloedt de poederstroom en de verwerking. De verpakkingsdichtheid beïnvloedt de uiteindelijke dichtheid van het geprinte onderdeel en zijn mechanische eigenschappen. Een hogere verpakkingsdichtheid leidt over het algemeen tot sterkere onderdelen. | Polymeren: Schijnbare dichtheid (0,3-0,8 g/cm³), verpakkingsdichtheid (0,5-0,9 g/cm³) |
Vloeibaarheid | Het gemak waarmee poeder stroomt onder zwaartekracht of met minimale agitatie. | Een goede vloeibaarheid is cruciaal voor een gelijkmatige poederverspreiding tijdens het printen. Een slechte vloeibaarheid kan leiden tot ongelijkmatige lagen en drukfouten. | Polymeren: Vloeien meestal vrij door hun bolvormige morfologie. Er kunnen additieven worden gebruikt om de vloeibaarheid te verbeteren. |
Vochtgehalte | De hoeveelheid waterdamp die gevangen zit in de poederdeeltjes. | Overtollig vocht kan problemen veroorzaken tijdens het printen, zoals stoomexplosies of inconsistent smeltgedrag. De meeste poeders vereisen een strikte vochtcontrole. | Polymeren: Typisch zeer laag vochtgehalte (< 0,1 wt%) om hydrolyse te voorkomen en een consistent printgedrag te garanderen. |
Chemische samenstelling en zuiverheid | De elementaire samenstelling van het poeder en de aanwezigheid van onzuiverheden. | De chemische samenstelling bepaalt de uiteindelijke eigenschappen van het geprinte onderdeel. Onzuiverheden kunnen de printbaarheid, mechanische prestaties en oppervlaktekwaliteit beïnvloeden. | Polymeren: Er wordt materiaal van hoge zuiverheidsgraad gebruikt om consistente eigenschappen en printbaarheid te garanderen. |
Thermische eigenschappen | Smeltpunt, glasovergangstemperatuur (Tg) voor polymeren en thermische geleidbaarheid. | Thermische eigenschappen beïnvloeden de parameters van het printproces en de uiteindelijke microstructuur van het geprinte onderdeel. | Polymeren: Smeltpunt en Tg zijn cruciaal voor het instellen van printparameters zoals laservermogen of bedtemperatuur. |
3D drukpoeder leveranciers
Materiaal | Belangrijkste toepassingen | Representatieve leveranciers | Overwegingen |
---|---|---|---|
Polymeerpoeder | - Prototyping - Functionele onderdelen - Medische apparaten - Consumentengoederen | * Polyamide (nylon): BASF, Evonik, Arkema * Polymelkzuur (PLA): NatureWorks, ExxonMobil Chemical, DuPont * Polypropyleen (PP): Koninklijke DSM, SABIC, Repsol | * De deeltjesgrootte en -distributie beïnvloeden de printbaarheid en de uiteindelijke onderdeeleigenschappen. * Materiaaleigenschappen zoals hittebestendigheid, flexibiliteit en biocompatibiliteit variëren. * Houd rekening met chemische compatibiliteit met nabewerkingstechnieken. |
Metaalpoeders | - Ruimtevaartonderdelen - Auto-onderdelen - Medische implantaten - Gereedschappen en matrijzen | * Titaanlegeringen: AP Poederfabriek, Höganäs, GE Additief * Roestvrij staal: Carpenter Additive Manufacturing, SLM-oplossingen, EOS GmbH * Aluminiumlegeringen: Rio Tinto Alcan, DLP Manufacturing, Exone | * De morfologie (vorm) van het poeder beïnvloedt de vloeibaarheid en verpakkingsdichtheid. * De korrelgrootte beïnvloedt de mechanische eigenschappen van het uiteindelijke onderdeel. * Veiligheidsprotocollen zijn cruciaal bij het werken met reactieve metaalpoeders. |
Samengestelde poeders | - Lichtgewicht structuren met hoge sterkte - Geleidende componenten - Biocompatibele implantaten met verbeterde eigenschappen | * Composieten van polymeer en metaal: LPW Technologie, Markforged, Desktop Metaal * Keramisch-metaalcomposieten: Sandvik Hyperion, Extrude Hone, Plasma Technik * Composieten van polymeer-koolstofvezel: Stratasys, Desktop Metaal, Henkel | * De keuze hangt af van de gewenste combinatie van eigenschappen (sterkte, geleidbaarheid, biocompatibiliteit). * Interface tussen verschillende materialen vereist zorgvuldige aandacht voor optimale prestaties. * De printparameters moeten mogelijk worden aangepast in vergelijking met enkelvoudige poeders. |
Toepassingen van Poeders voor 3D afdrukken
Drukpoeders faciliteren op unieke wijze complexe, op maat gemaakte onderdeelgeometrieën in verschillende industrieën:
Industrie | Voorbeeld Onderdelen | Voordelen |
---|---|---|
Lucht- en ruimtevaart | Turbinebladen, raketstraalpijpen, UAV-chassis | Gewichtsvermindering, prestatieverbetering |
Medisch | Op de patiënt afgestemde implantaten, protheses | Persoonlijke maat, biocompatibiliteit |
Automobiel | Warmtewisselaars, lichtgewicht chassiselementen | Consolidatie van onderdelen, efficiëntie |
Industrieel | Aangepaste productiegereedschappen, mallen | Kortere ontwikkelingstijden |
Tabel 5: Belangrijke toepassingssectoren die profiteren van de mogelijkheden van 3D-printpoeder
De mogelijkheid om ontwerpen snel te herhalen en kleine oplages economisch te printen, maakt innovatie van onderdelen voor eindgebruik mogelijk.
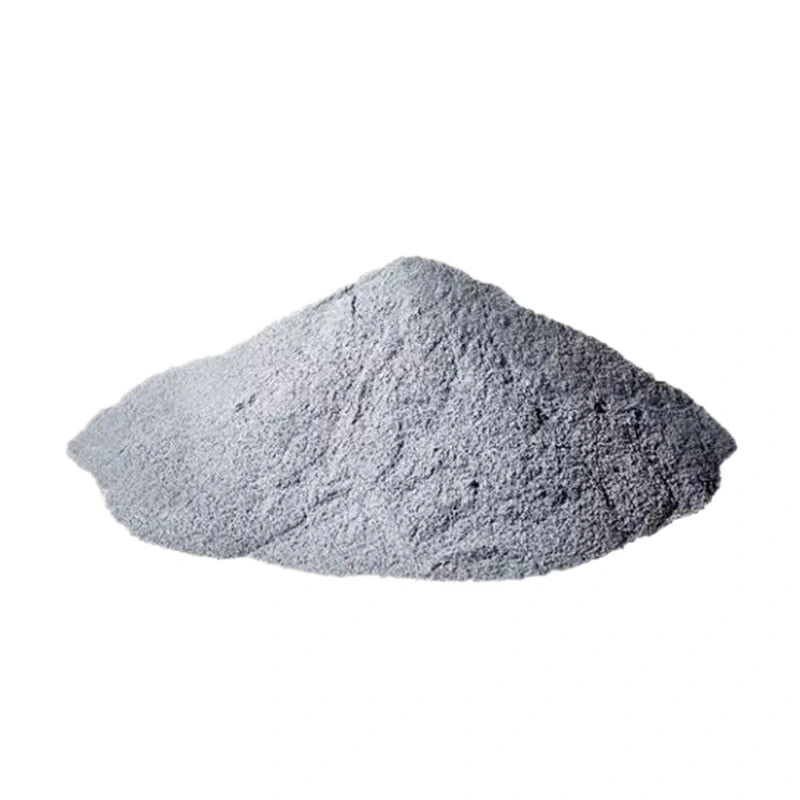
Voor- en nadelen van 3D printen op basis van poeder
Pluspunten | Nadelen |
---|---|
Hoge nauwkeurigheid en resolutie | Behandeling en veiligheid van poeder |
Breed scala aan materialen | Beperkte bouwgrootte |
Minimale ondersteunende structuren | Vereisten voor naverwerking |
Snelle productiesnelheden | Hoge initiële investering |
Veelgestelde vragen
V: Welke deeltjesgrootte werkt het beste voor metalen 3D printpoeders?
A: 10-45 micron vergemakkelijkt een goede verpakking en spreiding terwijl uitdagingen met ultrafijne poeders rond poederbehandeling vermeden worden. De meeste legeringen presteren goed met een verdeling van 30±15 μm.
V: Welk 3D-printproces voor polymeerpoeder biedt de beste mechanische prestaties?
A: Met selectief lasersinteren (SLS) is een uitstekende fusie en productie van fijne onderdelen mogelijk, waardoor hoogwaardige kunststofonderdelen kunnen worden gemaakt die kunnen wedijveren met spuitgietprocessen of deze zelfs overtreffen.
V: Hoe lang kan ongebruikt 3D-printpoeder worden bewaard?
A: Afgedicht met droogmiddel tegen vocht in een koele, droge omgeving - poeders behouden hun vloei-eigenschappen minstens 12 maanden. Zelfs geopende poeders gaan 6+ maanden mee voordat er merkbare degradatie optreedt.
V: Heeft de kwaliteit van het startpoeder een significante invloed op de eigenschappen van geprinte onderdelen?
A: Ja, de zuiverheid van de poedersamenstelling en een adequate controle van de poedereigenschappen bepalen sterk de mechanische eigenschappen, esthetiek, maatnauwkeurigheid en betrouwbaarheid van het eindproduct.
Delen op
MET3DP Technology Co, LTD is een toonaangevende leverancier van additieve productieoplossingen met hoofdkantoor in Qingdao, China. Ons bedrijf is gespecialiseerd in 3D printapparatuur en hoogwaardige metaalpoeders voor industriële toepassingen.
Onderzoek om de beste prijs en een op maat gemaakte oplossing voor uw bedrijf te krijgen!
gerelateerde artikelen
Over Met3DP
Recente update
Ons product
NEEM CONTACT MET ONS OP
Nog vragen? Stuur ons nu een bericht! Na ontvangst van uw bericht behandelen wij uw verzoek met een heel team.
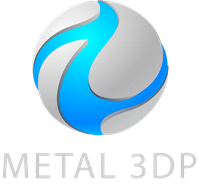
Metaalpoeders voor 3D printen en additieve productie