Overview of Electron Beam Melting Technology
Table of Contents
Electron beam melting (EBM) is an additive manufacturing technology commonly used for metal 3D printing. EBM uses a powerful electron beam as the heat source to selectively melt and fuse metallic powders layer-by-layer to build up fully dense parts directly from CAD data.
Compared to other metal 3D printing methods like laser-based processes, EBM offers some unique advantages in terms of build rate, material properties, quality, and cost-effectiveness. However it also has some limitations in resolution, surface finish, and material options.
This guide provides a detailed overview of electron beam melting technology, including:
- How EBM works
- Equipment types and main components
- Materials and applications
- Design considerations
- Process parameters
- Advantages and limitations
- Supplier comparison
- Operating guidelines
- Cost analysis
- Choosing the right EBM system
How Electron Beam Melting Works
The EBM process takes place in a high vacuum chamber filled with inert argon gas. Metallic powder is spread in thin layers across a build platform using rakes. An electron beam from an electron gun is used to selectively melt and fuse regions of each powder layer according to slice data from a CAD model.
The build platform lowers incrementally with each new layer. Parts are built directly on the platform without need for support structures due to the geometry-independent nature of powder bed fusion. After completion, excess powder is removed to reveal the solid 3D printed part.
The high energy density of the electron beam results in rapid melting and solidification, enabling high build rates. The EBM process takes place at elevated temperatures up to 1000°C, which reduces residual stresses and distortation.
Parts printed with EBM achieve over 99% density, with material properties comparable or superior to traditional manufacturing.
EBM Equipment Types and Components
EBM systems contain the following main components:
Electron gun – generates a focused beam of high energy electrons
Beam control – electromagnets guide and deflect the electron beam
High voltage power supply – accelerates electrons up to 60kV
Vacuum chamber – provides high vacuum environment
Powder dispensing – deposits and spreads metallic powder layers
Powder cassettes/hoppers – store and deliver powder
Build platform – lowers progressively as layers are built
Heating coils – preheats powder bed up to 1000°C
Control console – computer and software to operate system
There are a few variations of commercial EBM machines:
EBM System | Build Envelope | Beam Power | Layer Thickness |
---|---|---|---|
Arcam A2X | 200 x 200 x 380 mm | 3kW | 50-200 microns |
Arcam Q10plus | 350 x 350 x 380 mm | 5.4kW | 50-200 microns |
Arcam Q20plus | 500 x 500 x 400 mm | 7kW | 50-200 microns |
Arcam Spectra L | 275 x 275 x 380 mm | 1kW | 50-200 microns |
Sciaky EBAM | 1500 x 1500 x 1200 mm | 15-60kW | 200 microns |
Larger build envelopes and higher beam power enable faster builds, larger parts, and higher productivity. Smaller machines tend to have finer resolution and surface finishes.
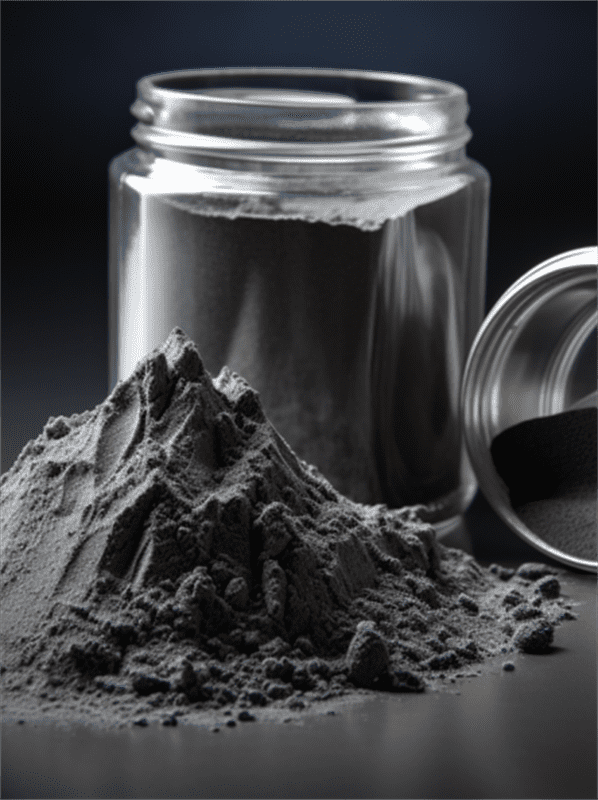
EBM Materials and Applications
The most common materials used in EBM are:
- Titanium alloys like Ti-6Al-4V
- Nickel-base superalloys like Inconel 718, Inconel 625
- Cobalt-chrome alloys
- Tool steels like H13, maraging steel
- Aluminum alloys
- Copper alloys
- Stainless steels like 17-4PH, 316L
Key applications of EBM include:
- Aerospace – turbine blades, impellers, structural brackets
- Medical – orthopedic implants, prosthetics
- Automotive – motor sports components, tooling
- Industrial – fluid handling parts, heat exchangers
- Tooling – injection molds, die casting, extrusion dies
Benefits of EBM for these applications include:
- High strength and fatigue resistance
- Complex geometries with lattices and internal channels
- Short lead times for metal parts
- Consolidation of assemblies into one piece
- Lightweighting and design optimization
- Part customization and personalization
EBM Design Considerations
EBM imposes some design restrictions:
- Minimum wall thickness of 0.8-1mm to prevent collapse
- No undercuts or horizontal overhangs
- 45° max unsupported overhangs
- Open internal channels minimum 1mm diameter
- Fine features limited to 0.5-1mm resolution
Designs should avoid steep thermal gradients to minimize residual stress:
- Uniform wall thickness
- Gradual transitions in section thickness
- Interior supports and lattices for large volumes
Post-processing like machining, drilling and polishing can improve surface finish.
EBM Process Parameters
Key EBM process parameters:
- Electron beam – Beam current, focus, speed, pattern
- Powder – Material, layer thickness, particle size
- Temperature – Preheat, build temp, scanning strategy
- Speed – Point distance, contour speed, hatch speed
These parameters control properties like density, precision, surface finish, microstructure:
Parameter | Typical Range | Effect on Part Properties |
---|---|---|
Beam Current | 5-40mA | Energy input, melt pool size |
Beam Speed | 104-107 mm/s | Energy density, cooling rate |
Layer Thickness | 50-200μm | Resolution, surface roughness |
Build Temperature | 650-1000°C | Residual stress, distortion |
Scan Speed | 500-10,000 mm/s | Surface finish, porosity |
Scan Pattern | Chessboard, unidirectional | Anisotropy, density |
Precise tuning of these parameters is required to achieve optimal material properties and accuracy for each alloy.
Advantages of Electron Beam Melting
Key benefits of EBM include:
- High build rate – up to 80 cm3/hr possible
- Fully dense parts – over 99% density achieved
- Excellent mechanical properties – strength, hardness, fatigue resistance
- High accuracy and repeatability – ±0.2mm precision
- Minimal supports needed – reduces post-processing
- High temperature builds – reduces residual stress
- Low contamination – high purity vacuum environment
The fast scan speeds result in rapid melting and solidification cycles, creating fine grained microstructures. The layerwise building method produces parts comparable to wrought properties.
Limitations of Electron Beam Melting
Drawbacks of EBM include:
- Limited resolution – minimum feature size ~0.8mm
- Rough surface finish – stair-stepping effect, requires finishing
- Restricted materials – mainly Ti alloys, Ni alloys, CoCr currently
- High equipment cost – $350,000 to $1 million+ for machine
- Slow preheat times – 1-2 hours to reach build temperature
- Contamination risk – zirconium can contaminate reactive alloys
- Powder management – recycling, handling of fine powders
- Line of sight requirements – horizontal overhangs not possible
The anisotropic layered build pattern and “stair-step” effect from sintered powder layers creates visible striations on upward facing surfaces. The electron beam can only fuse material in direct line of sight.
EBM Machine Suppliers
The major EBM equipment manufacturers include:
Supplier | Models | Materials | Beam Power | Price Range |
---|---|---|---|---|
Arcam EBM (GE) | A2X, Q10plus, Q20plus | Ti, Ni, CoCr alloys | 3-7kW | $350,000-$800,000 |
Sciaky | EBAM 300, 500 Series | Ti, Al, Inconel, steels | 15-60kW | $500,000-$1.5 million |
slaM | slm280 | Al, Ti, CoCr, tool steels | 5kW | $500,000-800,000 |
JEOL | JEM-ARM200F | Ni alloys, steels, Ti | 3kW | $700,000-900,000 |
Arcam EBM systems have the widest material capabilities while Sciaky offers large-scale production solutions. SLM Solutions and JEOL also provide EBM technology focused on metals.
Operating EBM Systems
To operate an EBM machine:
- Install EBM equipment with proper power, cooling, inert gas, and exhaust ventilation.
- Load CAD data and input build parameters into EBM software
- Sieve and load metallic powder into cassettes
- Pre-heat powder bed to process temperature
- Calibrate electron beam focus and power
- Begin layered build as beam scans and melts powder
- Allow parts to cool slowly before removing from machine
- Remove excess powder using vacuum cleaning
- Cut parts from build plate and conduct post-processing
Proper powder handling and storage is critical to avoid contamination which can cause defects. Regular maintenance of the beam filament, powder filters, and vacuum system is also essential.
EBM Processing Cost Analysis
Cost factors for EBM production:
- Machine depreciation – ~15-20% of total part cost
- Labor – machine operation, post-processing
- Powder – $100-500/kg for titanium alloys
- Power – high electricity use during builds
- Argon – daily purge gas consumption
- Maintenance – beam source, vacuum system, rakes
- Post-processing – support removal, surface finishing
Economies of scale can be achieved by batching smaller parts in a single build. Larger machines produce parts faster and more cost-effectively. The high upfront system cost is spread over more parts.
For low-volume production, outsourcing to a service bureau minimizes equipment overhead.
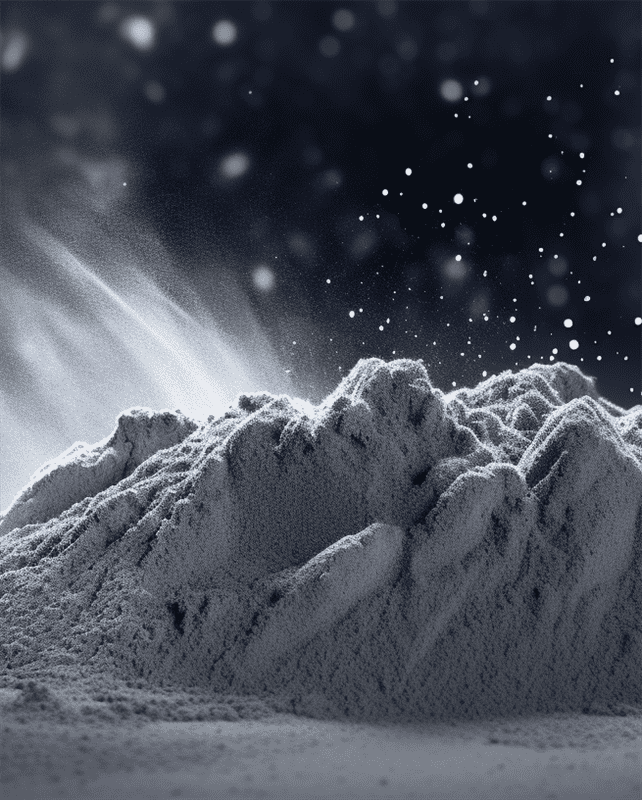
How to Choose an EBM System
Key considerations for selecting an EBM machine:
- Build envelope – match to part size requirements
- Precision – minimum feature size and surface finish needs
- Materials – alloys required for applications
- Throughput – daily/monthly production volume goals
- Power requirements – available electrical supply capacity
- Software – ease of use, flexibility, data formats
- Post-processing – finishing time and costs
- Training and support – installation, operation, maintenance
- Total cost – system price, operating expenses, powder
Conduct test builds of sample parts on different EBM systems to assess actual part quality and economics.
Invest in the largest build envelope that fits budget and space constraints to allow future expansion. Partner with a reputable supplier that can provide continued technical support.
FAQ
Q: How accurate is EBM?
A: Dimensional accuracy and tolerances of ±0.2 mm are typical for EBM parts. Fine features down to 0.3 mm are possible.
Q: What materials can be used in EBM besides metals?
A: EBM is limited to conductive metallic alloys. Photopolymers and ceramics cannot currently be processed due to the electron beam energy source.
Q: Does EBM require any supports?
A: EBM does not require support structures for overhangs less than 45° due to the geometry-independent nature of powder bed fusion. Minimal internal supports may help for large hollow sections.
Q: What is the surface finish?
A: As-built EBM parts have relatively rough surfaces due to powder layers and scan tracks. Various amounts of machining, grinding or polishing is required to improve surface finish.
Q: How expensive is EBM compared to other 3D printing processes?
A: EBM equipment has a higher upfront cost of $350,000 to over $1 million. But the high build speed can offset this by reducing part costs at scale. The process cost per part is competitive with other metal 3D printing methods.
Q: Is any post-processing needed on EBM parts?
A: Most EBM parts will need some post-processing like cutting from the build plate, stress relieving, surface machining, hole drilling, grinding or polishing to achieve the final part finish, tolerance, and appearance. Minimal manual touch-up may be needed to break sharp edges or reduce roughness.
Share On
MET3DP Technology Co., LTD is a leading provider of additive manufacturing solutions headquartered in Qingdao, China. Our company specializes in 3D printing equipment and high-performance metal powders for industrial applications.
Inquiry to get best price and customized Solution for your business!
Related Articles
About Met3DP
Recent Update
Our Product
CONTACT US
Any questions? Send us message now! We’ll serve your request with a whole team after receiving your message.