2024 proszki metali dla metalurgii
Spis treści
Rok 2024 zapowiada się jako kluczowy dla metalurgii proszków (PM), techniki produkcji, która wykorzystuje proszki metali do tworzenia złożonych elementów o kształcie zbliżonym do ostatecznego. U podstaw tego postępu leży moc samych proszków metali. Podobnie jak składniki w przepisie, konkretny rodzaj użytego proszku metalu znacząco wpływa na ostateczne właściwości i wydajność części PM. Ten artykuł zagłębia się w ekscytujący świat 2024 proszki metali, badając ich składy, właściwości, zastosowania i unikalne zalety, jakie oferują producentom PM.
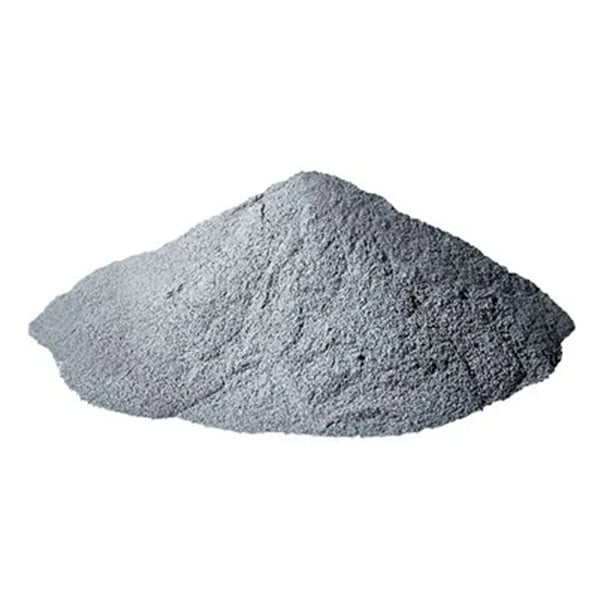
10 Przekonujących Proszków Metali na 2024 rok
Krajobraz proszków metali dla PM jest rozległy i stale ewoluuje. Tutaj przyjrzymy się 10 przekonującym opcjom proszków metali, które mają wywrzeć znaczący wpływ w 2024 roku:
1. Proszki żelaza atomizowane gazem:
- Skład: Głównie żelazo (Fe) z różną zawartością węgla (C).
- Właściwości: Doskonała obrabialność, dobra formowalność, wysoka przenikalność magnetyczna dla niektórych gatunków.
- Zastosowania: Koła zębate, koła łańcuchowe, łożyska, elementy elektryczne.
- Specyfikacje i rozmiary: Dostępne w szerokim zakresie rozmiarów (10-150 mikronów) i zawartości węgla (0,02-4,0 % wag.).
- Dostawcy i ceny: Szeroko dostępne od licznych globalnych dostawców. Ceny różnią się w zależności od rozmiaru, gatunku i ilości.
- Plusy i minusy: Przystępne cenowo, łatwo dostępne, dobre do zastosowań o niskim naprężeniu. Niższa wytrzymałość w porównaniu z niektórymi innymi opcjami.
2. Proszki żelaza karbonylowego:
- Skład: Żelazo o wysokiej czystości (Fe) o sferycznej morfologii.
- Właściwości: Doskonała ściśliwość, wysoka czystość, dobra obrabialność.
- Zastosowania: Miękkie elementy magnetyczne, elementy elektroniczne, filtry.
- Specyfikacje i rozmiary: Dostępne w drobniejszych rozmiarach (3-20 mikronów) w porównaniu z proszkami atomizowanymi gazem.
- Dostawcy i ceny: Ograniczona liczba dostawców, zazwyczaj wyższy koszt niż proszki atomizowane gazem.
- Plusy i minusy: Wyjątkowa czystość, idealna do zastosowań o wysokiej wydajności. Ograniczona dostępność i wyższy koszt mogą być wadami.
3. Proszki stali wstępnie stopionej:
- Skład: Baza żelaza (Fe) z określonymi pierwiastkami stopowymi, takimi jak nikiel (Ni), chrom (Cr), molibden (Mo), w zależności od pożądanego gatunku stali.
- Właściwości: Dostosowane właściwości w oparciu o pierwiastki stopowe, oferujące wyższą wytrzymałość, odporność na zużycie lub odporność na korozję w porównaniu z proszkami żelaza.
- Zastosowania: Koła zębate, koła łańcuchowe, narzędzia, elementy samochodowe.
- Specyfikacje i rozmiary: Dostępne w różnych gatunkach o określonych składach chemicznych. Zakres rozmiarów podobny do proszków żelaza atomizowanych gazem.
- Dostawcy i ceny: Oferowane przez kilku producentów proszków stalowych. Ceny odzwierciedlają złożoność składu stopu.
- Plusy i minusy: Szeroki zakres osiągalnych właściwości, doskonały do wymagających zastosowań. Wyższy koszt i potencjalne wyzwania w osiągnięciu spójnych właściwości w porównaniu z proszkami czystego żelaza.
4. Atomizowane proszki stali nierdzewnej:
- Skład: Baza żelaza (Fe) z chromem (Cr) i innymi pierwiastkami, takimi jak nikiel (Ni) i molibden (Mo), w zależności od konkretnego gatunku stali nierdzewnej.
- Właściwości: Doskonała odporność na korozję, dobra wytrzymałość, biokompatybilność dla niektórych gatunków.
- Zastosowania: Implanty medyczne, pompy, zawory, urządzenia do przetwarzania chemicznego.
- Specyfikacje i rozmiary: Oferowane w różnych gatunkach stali nierdzewnej o określonych składach. Zakres rozmiarów jest zgodny z proszkami żelaza atomizowanymi gazem.
- Dostawcy i ceny: Dostępne od kilku producentów proszków stali nierdzewnej. Ceny różnią się w zależności od konkretnego gatunku.
- Plusy i minusy: Niezrównana odporność na korozję w wielu zastosowaniach. Wyższy koszt w porównaniu z proszkami żelaza i potencjał większych trudności w przetwarzaniu.
5. Proszki niklu:
- Skład: Głównie nikiel (Ni) z możliwymi pierwiastkami śladowymi w zależności od metody produkcji.
- Właściwości: Doskonała odporność na korozję, wysoka przewodność elektryczna, dobre właściwości lutownicze.
- Zastosowania: Elementy elektroniczne, elektrody, filtry, materiały lutownicze.
- Specyfikacje i rozmiary: Dostępne w różnych rozmiarach (10-150 mikronów) i czystościach.
- Dostawcy i ceny: Oferowane przez kilku producentów specjalnych proszków metali. Ceny odzwierciedlają czystość i metodę przetwarzania.
- Plusy i minusy: Bardzo poszukiwane właściwości do określonych zastosowań. Wyższy koszt w porównaniu z proszkami żelaza i potencjał utleniania podczas przetwarzania.
6. Proszki miedzi:
- Skład: Głównie miedź (Cu) z możliwymi pierwiastkami śladowymi w zależności od metody produkcji.
- Właściwości: Doskonała przewodność elektryczna i cieplna,
- Zastosowania: Elementy elektryczne, radiatory, elementy zarządzania termicznego.
- Specyfikacje i rozmiary: Oferowane w różnych rozmiarach (10-150 mikronów) i czystościach.
- Dostawcy i ceny: Szeroko dostępne od licznych producentów proszków miedzi. Ceny różnią się w zależności od rozmiaru, czystości i ilości.
- Plusy i minusy: Doskonałe do zastosowań wymagających wysokiej przewodności. Mogą być podatne na utlenianie podczas przetwarzania i mogą wymagać specjalnego obchodzenia się.
7. Proszki aluminium:
- Skład: Głównie aluminium (Al) z możliwymi pierwiastkami stopowymi, takimi jak krzem (Si) lub magnez (Mg), w zależności od pożądanych właściwości.
- Właściwości: Lekkie, dobra przewodność elektryczna, wysoka refleksyjność dla niektórych gatunków.
- Zastosowania: Radiatory, elementy elektryczne, reflektory.
- Specyfikacje i rozmiary: Oferowane w różnych gatunkach aluminium o określonych składach. Zakres rozmiarów jest zgodny z proszkami żelaza atomizowanymi gazem.
- Dostawcy i ceny: Szeroko dostępne od licznych producentów proszków aluminiowych. Ceny różnią się w zależności od gatunku i ilości.
- Plusy i minusy: Lekka opcja o dobrej przewodności. Może wymagać ostrożnego obchodzenia się ze względu na reaktywność i potencjał zapłonu w postaci proszku.
8. Proszki tytanowe:
- Skład: Głównie tytan (Ti) z możliwymi pierwiastkami śladowymi w zależności od metody produkcji.
- Właściwości: Wysoki stosunek wytrzymałości do masy, doskonała odporność na korozję, biokompatybilność dla niektórych gatunków.
- Zastosowania: Elementy lotnicze, implanty medyczne, sprzęt sportowy.
- Specyfikacje i rozmiary: Oferowane w różnych gatunkach o określonych właściwościach. Zakres rozmiarów zwykle drobniejszy niż proszki żelaza atomizowane gazem.
- Dostawcy i ceny: Ograniczona liczba dostawców, zazwyczaj wyższy koszt w porównaniu z wieloma innymi opcjami ze względu na wyzwania związane z przetwarzaniem.
- Plusy i minusy: Wyjątkowy stosunek wytrzymałości do masy i biokompatybilność dla określonych zastosowań. Wysoki koszt, potencjał trudności w przetwarzaniu i wrażliwość na zanieczyszczenia są wadami.
9. Proszki superstopów na bazie niklu:
- Skład: Złożone stopy na bazie niklu (Ni) z pierwiastkami takimi jak chrom (Cr), kobalt (Co), molibden (Mo) i innymi, w zależności od konkretnego stopu.
- Właściwości: Wyjątkowa wytrzymałość w wysokich temperaturach, odporność na utlenianie, odporność na pełzanie.
- Zastosowania: Łopatki turbin, elementy silników odrzutowych, wysokowydajne elementy złączne.
- Specyfikacje i rozmiary: Oferowane w różnych gatunkach superstopów o określonych składach. Zakres rozmiarów zwykle drobniejszy niż proszki żelaza atomizowane gazem.
- Dostawcy i ceny: Ograniczona liczba dostawców ze względu na złożoność stopów. Bardzo wysoki koszt w porównaniu z większością innych opcji.
- Plusy i minusy: Niezrównane właściwości do zastosowań w wysokich temperaturach. Niezwykle wysoki koszt, złożone wymagania dotyczące przetwarzania i ograniczona dostępność to znaczące wady.
10. Proszki do formowania wtryskowego metali (MIM):
- Skład: Połączenie drobnych proszków metali (<20 mikronów) z polimerowym systemem wiążącym.
- Właściwości: Umożliwia produkcję o kształcie zbliżonym do ostatecznego o złożonych kształtach z dobrą dokładnością wymiarową.
- Zastosowania: Koła zębate, koła łańcuchowe, obudowy, skomplikowane elementy elektroniczne.
- Specyfikacje i rozmiary: Oferowane w różnych kompozycjach metalowych (stal, stal nierdzewna itp.) z określonymi systemami wiążącymi.
- Dostawcy i ceny: Dostępne od kilku producentów wsadu MIM. Ceny różnią się w zależności od składu metalu i złożoności systemu wiążącego.
- Plusy i minusy: Umożliwia skomplikowane geometrie części o dobrych właściwościach mechanicznych. Wyższa złożoność przetwarzania i potencjał wyższych kosztów w porównaniu z konwencjonalnymi technikami PM.
Wybór odpowiedniego proszku metalowego
Wybór optymalnego proszku metalu dla Twojej aplikacji PM jest podobny do znalezienia idealnego partnera przez wykwalifikowanego swatkę. Tak jak zgodność jest kluczowa w związkach, odpowiedni proszek musi posiadać właściwości, które pasują do pożądanej wydajności części. Rozważ te kluczowe czynniki przy dokonywaniu wyboru:
- Wymagane właściwości: Zidentyfikuj niezbędne właściwości dla swojej aplikacji, takie jak wytrzymałość, odporność na korozję, przewodność elektryczna lub obrabialność.
- Uwagi dotyczące przetwarzania: Oceń zgodność proszku z wybraną techniką PM (zagęszczanie, spiekanie) i możliwościami sprzętu.
- Efektywność kosztowa: Zrównoważ koszt proszku z całkowitym kosztem przetwarzania i propozycją wartości ostatecznej części.
Przyszłość proszków metali: Innowacja bierze górę
Przyszłość proszków metali dla PM jest pełna ekscytujących możliwości. Oto kilka trendów, na które warto zwrócić uwagę:
- Rozwój nowych stopów: Naukowcy nieustannie opracowują nowe stopy proszków metali o dostosowanych właściwościach do określonych zastosowań.
- Zaawansowane techniki produkcji proszków: Nowe technologie, takie jak produkcja addytywna (AM), torują drogę do produkcji proszków o unikalnej morfologii i właściwościach.
Zastosowania Proszki metali 2024
Wszechstronność proszków metali 2024 rozciąga się daleko i szeroko, napędzając innowacje w wielu branżach. Tutaj zagłębiamy się w niektóre z kluczowych obszarów zastosowań, w których te niezwykłe materiały mają znaczący wpływ:
Przemysł motoryzacyjny:
- Koła zębate i koła łańcuchowe: Proszki metali, takie jak żelazo atomizowane gazem i stale wstępnie stopione, są coraz częściej wykorzystywane do produkcji precyzyjnych, zbliżonych do kształtu końcowego kół zębatych i kół łańcuchowych do skrzyń biegów i innych elementów układu napędowego. Te części PM oferują korzyści, takie jak redukcja masy, poprawa efektywności paliwowej i elastyczność projektowania w porównaniu z tradycyjnie obrabianymi elementami.
- Komponenty silnika: Proszki superstopów na bazie niklu znajdują swoje zastosowanie w produkcji wysokowydajnych elementów silników, takich jak łopatki turbin i tarcze silników odrzutowych. Ich wyjątkowa wytrzymałość w wysokich temperaturach i odporność na pełzanie pozwalają im wytrzymać wymagające warunki w silniku.
- Wysiłki związane z odchudzaniem: Proszki aluminiowe i tytanowe są wykorzystywane do tworzenia lekkich komponentów konstrukcyjnych dla pojazdów. To skupienie się na redukcji masy przekłada się na poprawę oszczędności paliwa i ogólnej wydajności pojazdu.
Przemysł lotniczy i kosmiczny:
- Elementy konstrukcyjne: Proszki superstopów na bazie tytanu i niklu są wykorzystywane do produkcji wytrzymałych, lekkich komponentów dla samolotów i statków kosmicznych. Te części PM przyczyniają się do ogólnej redukcji masy pojazdów kosmicznych, co ma kluczowe znaczenie dla efektywności paliwowej i nośności.
- Produkcja addytywna (AM): Proszki metali odgrywają kluczową rolę w technikach AM, takich jak spiekanie laserowe i topienie wiązką elektronów, wykorzystywanych do tworzenia złożonych, bliskich kształtów netto komponentów lotniczych o skomplikowanych geometriach.
Urządzenia medyczne:
- Biokompatybilne implanty: Proszki stali nierdzewnej i tytanu o właściwościach biokompatybilnych są wykorzystywane do produkcji implantów ortopedycznych, takich jak wymiany bioder i kolan. Te implanty PM oferują doskonałą odporność na korozję, biokompatybilność i mogą być dostosowane do naśladowania właściwości mechanicznych kości.
- Złożone komponenty: Proszki wsadowe MIM, łączące proszki metali z polimerowym spoiwem, umożliwiają tworzenie złożonych urządzeń medycznych o wysokiej dokładności wymiarowej i skomplikowanych cechach. Technologia ta jest szczególnie cenna dla mikroprzepływów i innych specjalistycznych zastosowań medycznych.
Przemysł elektroniczny:
- Podzespoły elektryczne: Proszki miedzi i niklu są wykorzystywane do produkcji przewodników elektrycznych, złączy i radiatorów w urządzeniach elektronicznych. Ich doskonała przewodność elektryczna i właściwości zarządzania termicznego mają kluczowe znaczenie dla efektywnego rozdziału mocy i rozpraszania ciepła.
- Ekranowanie EMI: Proszki żelaza i aluminium są wykorzystywane do tworzenia komponentów ekranujących przed zakłóceniami elektromagnetycznymi (EMI), które chronią urządzenia elektroniczne przed niepożądanymi zakłóceniami elektromagnetycznymi.
Dobra konsumpcyjne:
- Artykuły sportowe: Proszki tytanu znajdują zastosowanie w produkcji wysokowydajnych artykułów sportowych, takich jak ramy rowerów i kije golfowe. Ich wyjątkowy stosunek wytrzymałości do masy pozwala na tworzenie lekkiego, a zarazem wytrzymałego sprzętu.
- Złożone komponenty: Proszki wsadowe MIM są wykorzystywane do produkcji skomplikowanych komponentów dla dóbr konsumpcyjnych, takich jak koła zębate, obudowy i elementy złączne w urządzeniach elektronicznych, aparatach fotograficznych i innych zastosowaniach.
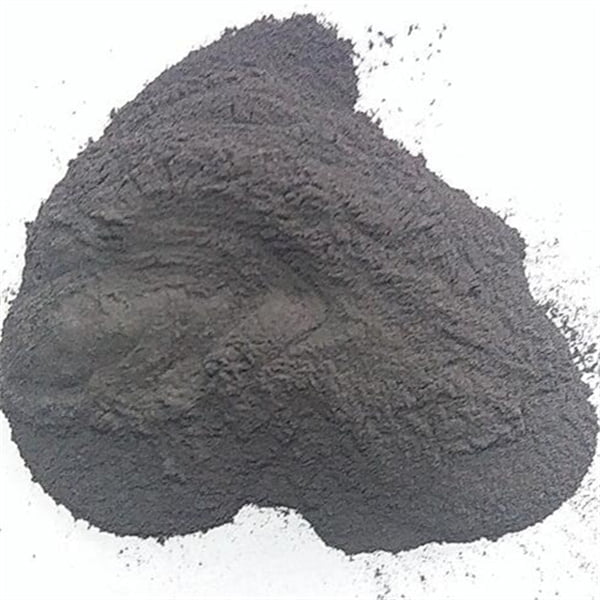
Zalety Proszki metali 2024
Przekonujące właściwości i charakterystyki przetwarzania proszków metali 2024 oferują mnóstwo zalet dla producentów PM. Oto bliższe spojrzenie na niektóre z kluczowych korzyści:
- Near-Net-Shape Manufacturing: Proszki metali umożliwiają tworzenie złożonych komponentów przy minimalnej stracie materiału, zmniejszając koszty produkcji i wpływ na środowisko.
- Elastyczność konstrukcji: Możliwość dostosowywania właściwości proszku i wykorzystywania technik AM otwiera drzwi do innowacyjnych projektów części o skomplikowanych cechach, które są trudne lub niemożliwe do osiągnięcia tradycyjnymi metodami produkcji.
- Wydajność materiałowa: PM pozwala na efektywne wykorzystanie cennych materiałów, minimalizując ilość złomu i przyczyniając się do zrównoważonych praktyk produkcyjnych.
- Masowa personalizacja: Względna łatwość przetwarzania proszków metali sprawia, że nadają się one do masowej kustomizacji, umożliwiając tworzenie części o specyficznych właściwościach dla niszowych zastosowań.
- Ulepszone właściwości mechaniczne: Techniki PM, takie jak prasowanie izostatyczne na gorąco (HIP), mogą być wykorzystywane do tworzenia komponentów o doskonałych właściwościach mechanicznych w porównaniu z tradycyjnymi metodami odlewania lub obróbki skrawaniem.
Wady proszków metali 2024
Chociaż proszki metali oferują liczne zalety, istotne jest uznanie pewnych potencjalnych ograniczeń, aby zapewnić udaną produkcję PM:
- Wyższe koszty początkowe: Same proszki metali mogą być droższe niż materiały masowe, takie jak stal lub aluminium.
- Złożoność przetwarzania: Techniki PM mogą wymagać specjalistycznego sprzętu i wiedzy w porównaniu z tradycyjnymi metodami produkcji.
- Płynność proszku: Zapewnienie spójnego przepływu proszku podczas przetwarzania może być wyzwaniem, szczególnie w przypadku drobniejszych proszków.
- Gęstość części: Osiągnięcie pożądanej gęstości w częściach PM może wymagać specyficznych technik przetwarzania i obróbki końcowej.
Podsumowanie: 2024 i dalej – świetlana przyszłość proszków metali w PM
Rok 2024 stanowi istotny punkt zwrotny dla proszków metali w PM. Dzięki swoim wyjątkowym właściwościom, wszechstronności w różnych branżach i obietnicy ciągłych innowacji, te niezwykłe materiały mają zrewolucjonizować krajobraz produkcyjny. Oto kilka kluczowych wniosków do zapamiętania:
- Wybór optymalnego proszku metalu zależy od pożądanych właściwości części, kompatybilności przetwarzania i opłacalności.
- Od motoryzacji i lotnictwa po urządzenia medyczne i dobra konsumpcyjne, proszki metali 2024 napędzają postęp w różnych branżach.
- Techniki PM oferują wyraźne zalety, takie jak produkcja bliska kształtowi netto, elastyczność projektowania i efektywność materiałowa.
Patrząc w przyszłość, przyszłość proszków metali w PM jest pełna możliwości:
- Opracowywanie nowych stopów: Naukowcy nieustannie przesuwają granice, opracowując nowe stopy proszków metali o właściwościach dostosowanych do konkretnych zastosowań. Ta ciągła innowacja otworzy jeszcze więcej możliwości dla PM.
- Zaawansowana produkcja proszków: Nowe technologie, takie jak produkcja addytywna (AM), torują drogę do produkcji proszków o unikalnych morfologiach i właściwościach. Te postępy jeszcze bardziej rozszerzą możliwości projektowania części PM.
- Koncentracja na zrównoważonym rozwoju: Przemysł PM w coraz większym stopniu stawia na zrównoważony rozwój. Efektywne wykorzystanie materiałów z proszkami metali doskonale wpisuje się w te cele, minimalizując ilość odpadów i wpływ na środowisko.
W miarę jak świat PM ewoluuje, 2024 proszki metali stanowią świadectwo potęgi innowacji. Ich zdolność do tworzenia złożonych, wysokowydajnych części przy minimalnej ilości odpadów pozycjonuje je jako przełom w przemyśle wytwórczym. Wykorzystując ich potencjał i przyjmując ciągłe postępy, producenci PM mogą otworzyć przyszłość pełną ekscytujących możliwości.
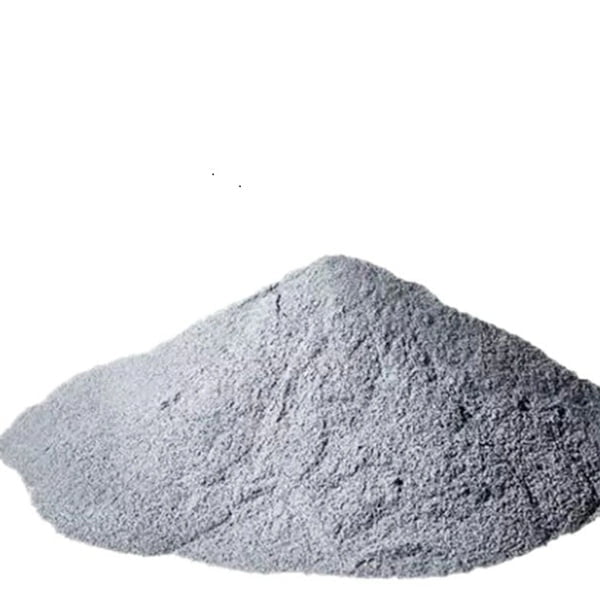
FAQ
P: Jakie są kluczowe czynniki, które należy wziąć pod uwagę przy wyborze proszku metalu dla PM?
O: Proces selekcji powinien uwzględniać wymagane właściwości dla danego zastosowania (wytrzymałość, odporność na korozję itp.), kompatybilność przetwarzania z wybraną techniką PM oraz opłacalność samego proszku i całego procesu.
P: Jakie są niektóre z zalet stosowania proszków metali w PM?
O: PM z proszkami metali oferuje kilka korzyści, w tym produkcję bliską kształtowi netto przy minimalnej ilości odpadów, elastyczność projektowania dla skomplikowanych komponentów, efektywność materiałową i potencjał uzyskania doskonałych właściwości mechanicznych w porównaniu z metodami tradycyjnymi.
P: Czy istnieją jakieś ograniczenia, które należy wziąć pod uwagę przy stosowaniu proszków metali w PM?
O: Chociaż korzystne, proszki metali mogą mieć wyższe koszty początkowe w porównaniu z materiałami masowymi. Same techniki PM mogą być bardziej złożone i wymagać specjalistycznego sprzętu. Zapewnienie spójnego przepływu proszku i osiągnięcie pożądanej gęstości części może również stanowić pewne wyzwania.
P: Jakie są niektóre z pojawiających się trendów w świecie proszków metali dla PM?
O: Opracowywanie nowych stopów o dostosowanych właściwościach, zaawansowane techniki produkcji proszków z wykorzystaniem AM oraz rosnący nacisk na zrównoważony rozwój w przemyśle PM to ekscytujące trendy kształtujące przyszłość proszków metali.
Udostępnij
MET3DP Technology Co., LTD jest wiodącym dostawcą rozwiązań w zakresie produkcji addytywnej z siedzibą w Qingdao w Chinach. Nasza firma specjalizuje się w sprzęcie do druku 3D i wysokowydajnych proszkach metali do zastosowań przemysłowych.
Zapytaj o najlepszą cenę i spersonalizowane rozwiązanie dla Twojej firmy!
Powiązane artykuły
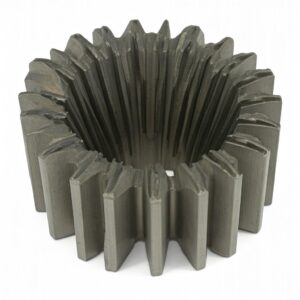
Wysokowydajne segmenty łopatek dysz: Rewolucja w wydajności turbin dzięki drukowi 3D w metalu
Czytaj więcej "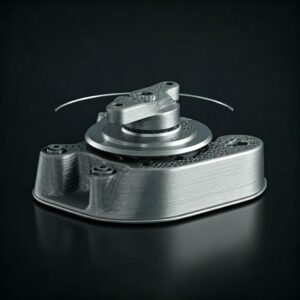
Drukowane w 3D mocowania dla samochodowych czujników radarowych: Precyzja i wydajność
Czytaj więcej "Informacje o Met3DP
Ostatnia aktualizacja
Nasz produkt
KONTAKT
Masz pytania? Wyślij nam wiadomość teraz! Po otrzymaniu wiadomości obsłużymy Twoją prośbę całym zespołem.
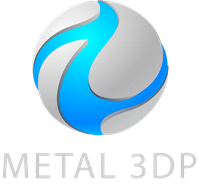
Proszki metali do druku 3D i produkcji addytywnej