3D Printed Dental Bridge Frameworks: Precision and Efficiency for Modern Dentistry
Spis treści
Introduction: The Evolution of Dental Restorations with 3D Printed Frameworks
The field of dentistry is constantly evolving, with innovations in materials and techniques driving significant improvements in patient care and treatment outcomes. Among these advancements, the integration of metal Drukowanie 3D, also known as metal additive manufacturing, stands out as a transformative force, particularly in the fabrication of dental bridge frameworks. Traditionally, dental restorations like bridges involved labor-intensive processes, often relying on casting techniques that could introduce variability and limitations in design complexity. Today, 3D printed dental bridge frameworks are revolutionizing dental laboratories and clinics by offering unparalleled precision, design flexibility, and material efficiency. This shift towards digital dentistry not only enhances the quality of restorations but also streamlines workflows, reduces lead times, and opens up new possibilities for customized patient solutions.
Przy Metal3DP Technology Co., LTD, headquartered in Qingdao, China, we are at the forefront of this revolution, providing industry-leading additive manufacturing solutions tailored for the demanding requirements of dental applications. Our expertise in both 3D printing equipment and high-performance metal powders enables dental professionals to produce dense, high-quality metal parts with superior mechanical properties. We understand the critical nature of dental restorations and are committed to delivering solutions that meet the highest standards of accuracy and reliability. To learn more about our comprehensive approach to metal 3D printing, visit our Druk 3D w metalu strona.
What are 3D Printed Dental Bridge Frameworks Used For? Enhancing Patient Care and Workflow
Dental bridge frameworks serve as the foundational structure for fixed dental prostheses designed to replace one or more missing teeth. These frameworks are meticulously crafted to fit precisely onto the abutment teeth (the natural teeth adjacent to the gap) or dental implants, providing support and retention for the artificial replacement teeth, known as pontics. The primary function of a dental bridge is to restore the patient’s smile, chewing ability, and speech, while also preventing the adjacent teeth from shifting into the empty space.
The advent of 3D printed dental bridge frameworks has significantly enhanced the capabilities of dental laboratories and clinics in achieving these objectives. By leveraging additive manufacturing, dental professionals can create frameworks with intricate designs that precisely match the patient’s unique oral anatomy. This leads to several key benefits:
- Improved Fit and Comfort: The high accuracy of 3D printing ensures a snug and comfortable fit, minimizing the need for adjustments and enhancing patient satisfaction.
- Zwiększona estetyka: 3D printing allows for the creation of frameworks that can be designed to seamlessly integrate with the patient’s natural teeth, contributing to a more natural-looking restoration.
- Increased Efficiency: Digital workflows associated with 3D printing can significantly reduce the time required for framework fabrication compared to traditional methods, leading to faster turnaround times for patients.
- Optymalizacja materiałów: Additive manufacturing allows for precise material deposition, minimizing waste and potentially reducing material costs.
- Złożone projekty: 3D printing enables the creation of complex geometries that might be challenging or impossible to achieve with traditional casting techniques, offering greater flexibility in addressing individual patient needs.
Dental laboratories and clinics can utilize 3D printed bridge frameworks for a wide range of restorative cases, from single-unit bridges to more complex multi-unit restorations. The versatility and precision offered by this technology make it an indispensable tool for modern dentistry. At Metal3DP, our industry-leading print volume and accuracy ensure that dental professionals can rely on our solutions for even the most demanding cases. Explore our range of Produkty to discover how our technology can elevate your dental practice.
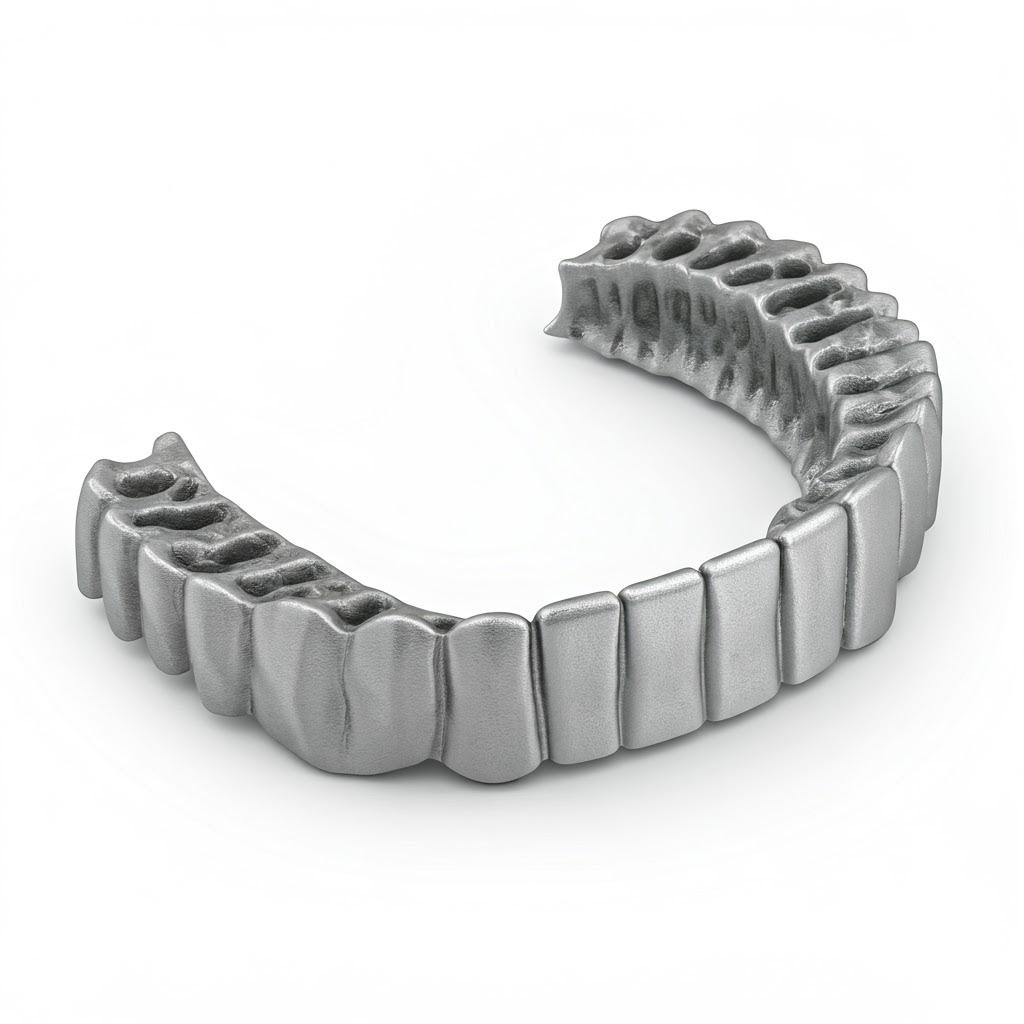
Why Choose Metal 3D Printing for Dental Bridge Frameworks? Advantages Over Traditional Methods
The transition from traditional methods of fabricating dental bridge frameworks, primarily involving lost-wax casting, to metal 3D printing offers a multitude of compelling advantages for dental laboratories, clinicians, and ultimately, patients. Here’s a detailed look at the key benefits of adopting metal additive manufacturing for this critical application:
Cecha | Odlew tradycyjny | Druk 3D w metalu | Przewaga |
---|---|---|---|
Precyzja i dokładność | Potential for shrinkage and distortion during casting | High accuracy and repeatability, minimal distortion | Superior fit, reduced adjustments, consistent results |
Elastyczność projektowania | Limitations in complex geometries | Enables intricate and customized designs | Better adaptation to patient anatomy, enhanced aesthetics and function |
Wydajność materiałowa | Significant material waste in sprueing and casting | Precise material deposition, minimal waste | Cost savings, reduced material consumption |
Workflow Efficiency | Multiple manual steps, longer lead times | Streamlined digital workflow, faster production times | Reduced labor, quicker turnaround for patients |
Spójność | Variability due to manual processes | Consistent quality and dimensional accuracy | Predictable outcomes, reduced remakes |
Personalizacja | More challenging to achieve highly individualized designs | Facilitates patient-specific designs with ease | Tailored solutions for optimal patient outcomes |
Właściwości materiału | Potential for porosity and inclusions | Dense, high-quality parts with superior mechanical properties | Stronger and more durable restorations |
Eksport do arkuszy
As a leading provider of additive manufacturing solutions, Metal3DP understands these advantages firsthand. Our Selective Electron Beam Melting (SEBM) printers, for example, are engineered to deliver industry-leading accuracy and reliability, ensuring the production of dental bridge frameworks that meet the stringent demands of the dental industry. We also offer advanced metal powders, such as those based on CoCrMo and CoCrW alloys, specifically optimized for dental applications, guaranteeing biocompatibility and excellent mechanical properties. Discover more about our printing methods on our Metody drukowania strona.
Recommended Materials: CoCrMo and CoCrW Powders for High-Performance Dental Frameworks
The selection of appropriate materials is paramount in the fabrication of dental bridge frameworks, as these restorations must exhibit excellent biocompatibility, mechanical strength, corrosion resistance, and aesthetic properties. Among the various metallic materials available for 3D printing, Cobalt-Chromium-Molybdenum (CoCrMo) and Cobalt-Chromium-Tungsten (CoCrW) alloys have emerged as the preferred choices due to their exceptional performance characteristics in the oral environment.
Kobalt-chrom-molibden (CoCrMo)
CoCrMo alloys have a long and successful history in dental applications, renowned for their:
- Wysoka biokompatybilność: These alloys exhibit excellent tissue compatibility, minimizing the risk of allergic reactions or adverse tissue responses in patients.
- Superior Mechanical Strength: CoCrMo frameworks possess high tensile strength, yield strength, and hardness, ensuring the durability and longevity of the dental restoration under masticatory forces.
- Doskonała odporność na korozję: The oral environment is highly corrosive due to variations in pH, temperature, and the presence of saliva and food particles. CoCrMo alloys demonstrate exceptional resistance to corrosion and tarnish, maintaining their structural integrity and aesthetic appearance over time.
- High Stiffness: The high modulus of elasticity of CoCrMo alloys provides the necessary rigidity for bridge frameworks, ensuring stability and preventing flexure under load.
Cobalt-Chromium-Tungsten (CoCrW)
Similar to CoCrMo, CoCrW alloys offer a compelling combination of properties suitable for dental applications:
- Biokompatybilność: CoCrW alloys are also well-tolerated by oral tissues, making them a safe choice for dental restorations.
- Good Mechanical Properties: These alloys provide adequate strength and hardness for dental frameworks, ensuring their ability to withstand the stresses of chewing and biting.
- Odporność na korozję: CoCrW alloys exhibit good resistance to corrosion in the oral environment, contributing to the long-term stability of the restoration.
- Fine Grain Structure: 3D printing with CoCrW powders can result in a fine grain structure, which can further enhance the mechanical properties and surface finish of the framework.
Przy Metal3DP, we recognize the importance of high-quality metal powders in achieving optimal results in dental 3D printing. Our advanced powder making system, utilizing industry-leading gas atomization technology, ensures that our CoCrMo and CoCrW powders exhibit high sphericity and excellent flowability, which are crucial for the precision and density of 3D printed dental frameworks. We are committed to researching and manufacturing high-performance metal powders that meet the specific needs of the dental industry, enabling our customers to produce superior dental restorations. For more information about our high-quality metal powders, please visit our product strona.
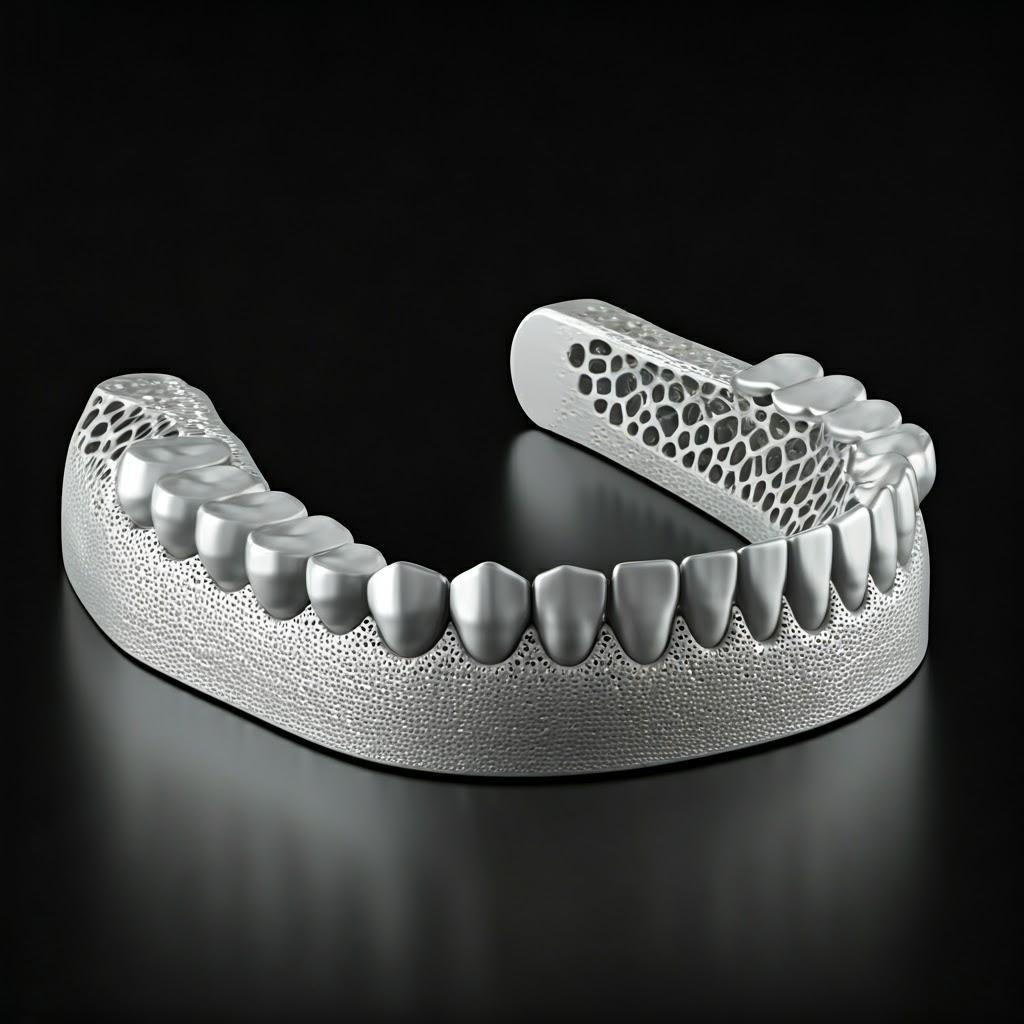
Design Considerations for Additive Manufacturing of Dental Bridges: Optimizing for Functionality and Fit
Designing dental bridge frameworks for additive manufacturing requires a different mindset compared to traditional subtractive or casting methods. To fully leverage the capabilities of metal 3D printing and ensure optimal functionality, fit, and aesthetics, several key design considerations must be taken into account:
- Minimalna grubość ścianki: While 3D printing allows for intricate geometries, it’s crucial to adhere to minimum wall thickness requirements for the chosen material to ensure structural integrity and prevent collapse during printing and in service. The optimal thickness will depend on the specific alloy (e.g., CoCrMo, CoCrW) and the size and load-bearing requirements of the bridge.
- Struktury wsparcia: Overhanging features and complex geometries often necessitate the use of support structures during the printing process. These supports provide stability and prevent distortion. Careful consideration should be given to the placement and design of supports to minimize material usage and facilitate easy removal post-printing without damaging the framework’s surface.
- Orientation on the Build Platform: The orientation of the dental bridge framework on the printer’s build platform can significantly impact the surface finish, dimensional accuracy, and the need for support structures. Optimal orientation should aim to minimize the number of downward-facing surfaces and maximize self-supporting angles.
- Sprue Design (if applicable): While some direct metal printing processes may not require traditional sprues, others might benefit from strategically placed sprues for efficient heat dissipation and material flow during the build. The design should facilitate easy removal without compromising the framework’s critical areas.
- Connectors and Pontic Design: The design of the connectors between the retainers and the pontic(s) is crucial for the bridge’s strength and longevity. These connectors should be sufficiently thick and appropriately shaped to withstand occlusal forces. The pontic design should consider aesthetics, function, and the need for proper tissue contact.
- Margin Design: Precise margin design is essential for a seamless fit with the abutment teeth or implants. The design should account for the limitations and capabilities of the 3D printing process to ensure accurate reproduction of the prepared margins.
- Hollowing and Lattice Structures: For larger bridges, hollowing out non-critical areas and incorporating lattice structures can reduce material usage and weight without compromising strength. This design approach is often only feasible with additive manufacturing.
Przy Metal3DP, our application development services provide invaluable support to dental laboratories and clinicians in optimizing their designs for metal 3D printing. Our team of experts possesses decades of collective expertise in metal additive manufacturing and can offer guidance on best practices for design, material selection, and process parameters to ensure successful outcomes. We partner with organizations to implement 3D printing and accelerate digital manufacturing transformations in dentistry. Contact Metal3DP to explore how our capabilities can power your organization’s additive manufacturing goals.
Precision and Accuracy in 3D Printed Dental Frameworks: Achieving Optimal Fit and Function
One of the most significant advantages of using metal 3D printing for dental bridge frameworks is the high level of precision and accuracy achievable. This is critical in dentistry, where even微米-level deviations can impact the fit, function, and longevity of the restoration, as well as patient comfort. Several factors contribute to the superior accuracy of 3D printed frameworks:
- Digital Workflow: The entire process, from scanning the patient’s oral anatomy to designing the framework using CAD software and then transferring the digital model directly to the 3D printer, minimizes the potential for errors introduced by manual steps in traditional methods.
- Layer-by-Layer Fabrication: Additive manufacturing builds parts layer by layer based on the digital design. This precise deposition of material ensures that even complex geometries are accurately reproduced.
- Advanced Printer Technology: Technologies like Selective Electron Beam Melting (SEBM), which Metal3DP specializes in, offer high energy input and precise control over the melting and solidification process, resulting in dense, accurate parts with minimal residual stresses and distortion. Our printers deliver industry-leading accuracy and reliability for mission-critical parts in dental applications.
- Wysokiej jakości proszki metali: The quality and consistency of the metal powder used are crucial for achieving high accuracy. Metal3DP employs industry-leading gas atomization and PREP technologies to research and manufacture high-quality 3D printing metallic powders 1 with high sphericity and good flowability, ensuring consistent and accurate printing. 1. met3dp.sg met3dp.sg
- Calibration and Process Control: Regular calibration of the 3D printer and stringent control over process parameters, such as laser power (in SLM/DMLS) or electron beam parameters (in SEBM), build speed, and temperature, are essential for maintaining accuracy.
The high precision of 3D printed dental bridge frameworks translates directly into several benefits for dental professionals and patients:
- Optimal Fit: Accurate frameworks require minimal adjustments during the fitting process, saving chair time and improving patient comfort.
- Enhanced Stability and Retention: A precise fit ensures proper seating on the abutment teeth or implants, leading to a stable and retentive bridge.
- Improved Marginal Integrity: Accurate margins are crucial for preventing microleakage, which can lead to secondary caries and other complications.
- Predictable Outcomes: The consistency and accuracy of 3D printing contribute to more predictable treatment outcomes.
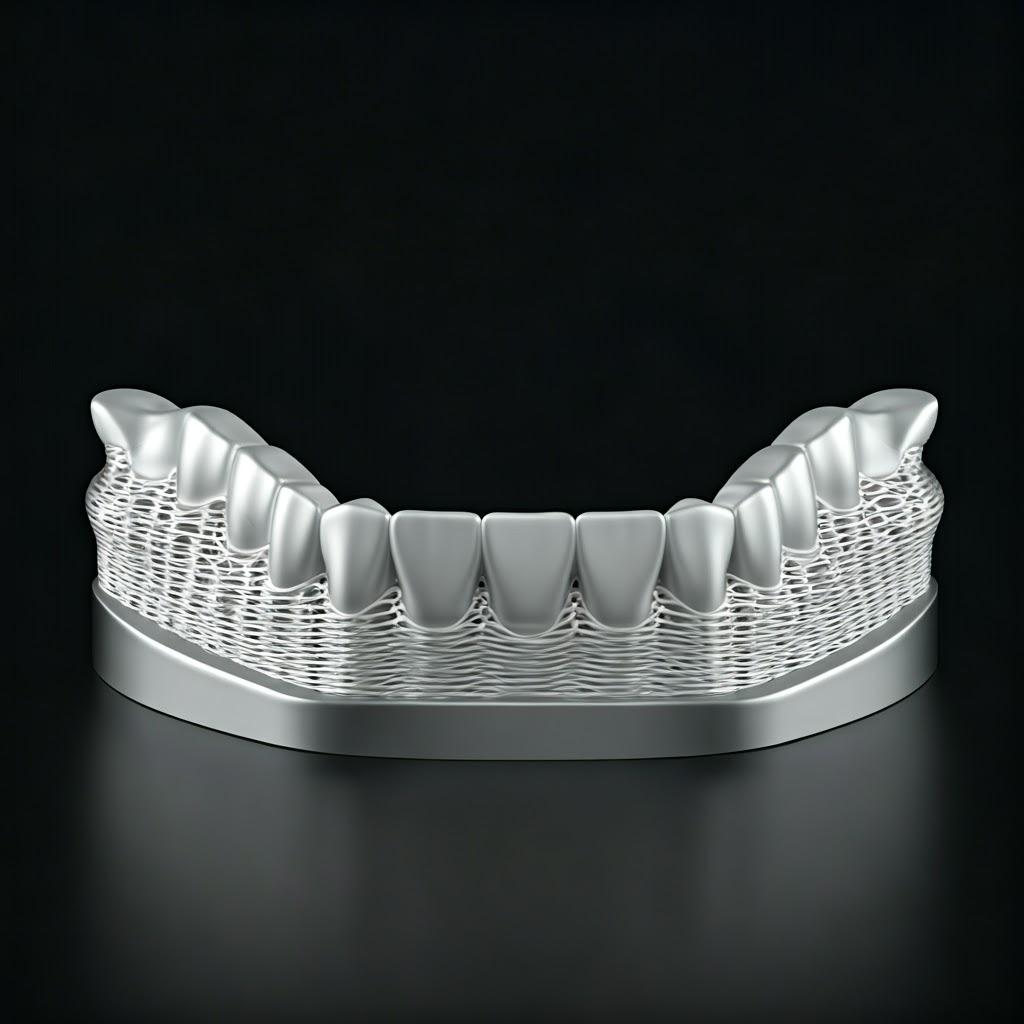
Post-Processing of 3D Printed Dental Bridges: Ensuring Biocompatibility and Aesthetics
While the 3D printing process itself creates the basic form of the dental bridge framework, post-processing steps are essential to achieve the final desired properties, biocompatibility, surface finish, and aesthetics. Common post-processing requirements for 3D printed metal dental bridges include:
- Usuwanie wsparcia: If support structures were used during printing, they need to be carefully removed without damaging the delicate features of the framework. This can involve manual breaking, cutting, or the use of specialized tools.
- Czyszczenie: Residual powder particles adhering to the surface of the printed framework must be thoroughly removed using methods such as air blasting, ultrasonic cleaning, or brushing.
- Obróbka cieplna: Depending on the material and the printing process, heat treatment may be necessary to relieve internal stresses, optimize the microstructure, and enhance the mechanical properties of the framework. For CoCrMo and CoCrW alloys, specific annealing or sintering cycles might be required.
- Wykończenie powierzchni: The as-printed surface of a metal 3D printed part can sometimes be rough. Depending on the clinical requirements and aesthetic considerations, various surface finishing techniques may be employed, such as:
- Grinding and Polishing: To achieve a smooth, lustrous surface that is comfortable for the patient and promotes good tissue health.
- Piaskowanie: To create a uniform surface texture, often prior to porcelain veneering.
- Pasywacja: For certain metallic alloys, a passivation process may be required to enhance their corrosion resistance by forming a protective oxide layer on the surface.
- Kontrola jakości i inspekcja: Thorough inspection of the finished framework is crucial to ensure it meets the required dimensional accuracy, surface finish, and overall quality standards. This may involve visual inspection, tactile examination, and the use of metrology equipment.
Metal3DP understands the importance of these post-processing steps in delivering high-quality dental restorations. We can provide guidance and solutions for effective post-processing of 3D printed metal parts, ensuring that the final product meets the stringent requirements of the dental industry. Our expertise extends beyond printing to encompass the entire manufacturing workflow.
Addressing Common Challenges in 3D Printing Dental Frameworks: Solutions for Accuracy and Consistency
While metal 3D printing offers numerous advantages for dental bridge frameworks, certain challenges can arise during the process. Understanding these potential issues and implementing appropriate solutions is crucial for achieving consistent accuracy and high-quality results:
- Wypaczenia i zniekształcenia: Thermal stresses during the printing process can sometimes lead to warping or distortion of the framework, particularly for large or complex designs.
- Solutions: Optimizing part orientation, using appropriate support structures, and carefully controlling the build parameters (e.g., temperature, laser/electron beam power) can minimize these issues. Metal3DP‘s advanced SEBM technology inherently reduces thermal stresses compared to some other powder bed fusion methods.
- Support Removal Damage: Improperly designed or aggressively removed support structures can damage the delicate surfaces of the dental framework.
- Solutions: Designing breakaway supports or using dissolvable support materials can facilitate easier and safer removal. Careful and methodical removal techniques are also essential.
- Porowatość: Insufficient melting or improper process parameters can lead to porosity within the printed part, compromising its mechanical strength and biocompatibility.
- Solutions: Optimizing laser/electron beam power and scanning strategies, ensuring the use of high-quality metal powders with good flowability (as offered by Metal3DP), and employing appropriate heat treatment cycles can minimize porosity.
- Chropowatość powierzchni: The as-printed surface may not be smooth enough for direct clinical use and can affect the fit and comfort of the restoration.
- Solutions: Optimizing build parameters, such as layer thickness and scanning strategies, can improve surface finish. Post-processing techniques like grinding, polishing, and sandblasting are commonly used to achieve the desired smoothness.
- Dimensional Inaccuracies: Deviations from the intended design can occur due to factors like material shrinkage, calibration issues, or improper design compensation.
- Solutions: Accurate calibration of the 3D printer, material-specific shrinkage compensation in the CAD design, and using high-precision printing technologies are crucial. Metal3DP‘s commitment to industry-leading accuracy helps mitigate these issues.
- Material Contamination: Impurities in the metal powder or contamination during the printing process can affect the quality and biocompatibility of the framework.
- Solutions: Using high-purity, certified metal powders (like those from Metal3DP) and maintaining a clean printing environment are essential.
By understanding these potential challenges and implementing appropriate strategies, dental laboratories and clinicians can effectively leverage metal 3D printing to produce high-quality, accurate dental bridge frameworks consistently.
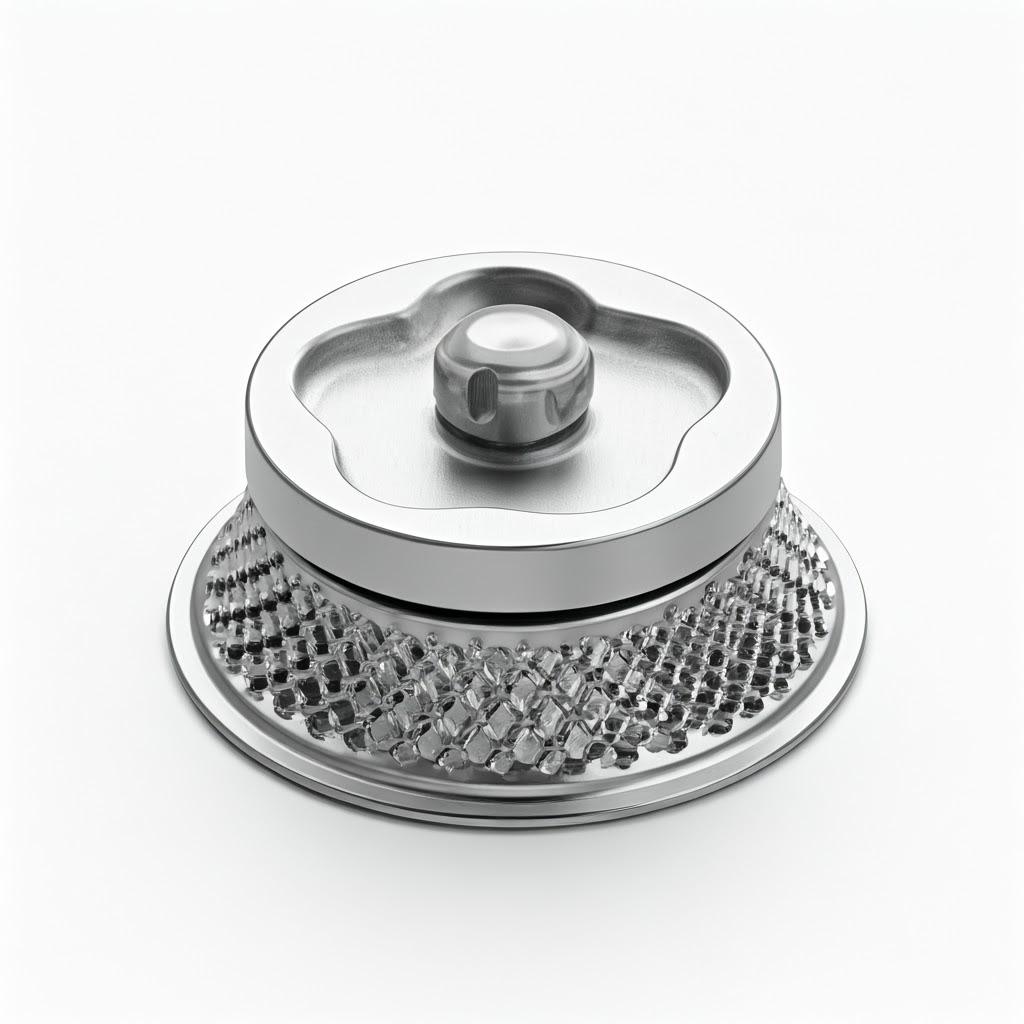
Selecting a Reliable Metal 3D Printing Service for Dental Applications: Key Considerations
Choosing the right metal 3D printing service provider is a critical decision for dental laboratories and clinicians looking to integrate this advanced technology into their workflow without the upfront investment and expertise required for in-house production. A reliable partner can ensure high-quality frameworks, timely delivery, and expert support. Here are key considerations when evaluating potential metal 3D printing service providers for dental applications:
- Material Capabilities: Ensure the service provider offers the specific biocompatible metal alloys required for dental bridge frameworks, such as CoCrMo and CoCrW. Verify the quality and certifications of their metal powders. Metal3DP manufactures a wide range of high-quality metal powders optimized for laser and electron beam powder bed fusion, including innovative alloys suitable for dental applications.
- Printing Technology and Accuracy: Understand the types of metal 3D printing technologies the provider utilizes (e.g., SLM, DMLS, SEBM). Inquire about the accuracy and tolerances they can achieve, as this directly impacts the fit and function of the dental frameworks. Metal3DP‘s SEBM printers deliver industry-leading print volume, accuracy, and reliability, crucial for mission-critical dental parts.
- Quality Control and Certifications: Check if the service provider has robust quality control procedures in place, including material testing, dimensional inspection, and adherence to relevant industry standards and certifications (e.g., ISO 13485 for medical devices).
- Post-Processing Services: Determine if the provider offers the necessary post-processing services, such as support removal, cleaning, heat treatment, surface finishing (polishing, sandblasting), and passivation, as these are crucial for the final quality and biocompatibility of the frameworks.
- Design Support and Consultation: A valuable service provider should offer expertise in designing for additive manufacturing, providing guidance on optimizing designs for printability, functionality, and material efficiency. Metal3DP provides comprehensive solutions spanning SEBM printers, advanced metal powders, and application development services, 1 partnering with organizations to implement 3D printing effectively. 1. met3dp.sg met3dp.sg
- Turnaround Time and Scalability: Evaluate the provider’s lead times for production and their capacity to handle your volume requirements, especially as your adoption of 3D printed frameworks grows.
- Communication and Customer Support: Clear communication, responsiveness, and technical support are essential for a smooth and successful partnership.
- Cost Structure: Understand the pricing model, including material costs, printing fees, and any additional charges for design optimization or post-processing. While cost is a factor, prioritize quality and reliability to ensure optimal patient outcomes.
By carefully considering these factors, dental laboratories and clinicians can select a metal 3D printing service provider that aligns with their specific needs and helps them leverage the benefits of this advanced manufacturing technology effectively.
Cost-Effectiveness and Turnaround Time for 3D Printed Dental Bridge Frameworks
The adoption of 3D printed dental bridge frameworks can offer significant advantages in terms of both cost-effectiveness and turnaround time compared to traditional fabrication methods, although these factors can vary depending on the complexity of the design, material used, and the chosen service provider.
Czynniki kosztowe:
- Wydajność materiałowa: Additive manufacturing minimizes material waste as only the necessary material is deposited to create the part. This can lead to cost savings, especially for complex geometries that would generate significant waste with subtractive methods.
- Reduced Labor Costs: The automated nature of the 3D printing process can reduce the labor involved in framework fabrication compared to manual casting techniques, potentially lowering overall production costs.
- Koszty narzędzi: Unlike traditional casting, which often requires the creation of molds and dies, 3D printing eliminates these upfront tooling costs, making it particularly cost-effective for low to medium production volumes and customized designs.
- Koszty przetwarzania końcowego: While some post-processing is required, the overall cost can be competitive, especially when considering the reduced need for extensive manual adjustments often associated with cast frameworks.
- Complexity without Added Cost: 3D printing allows for the creation of intricate designs without significant increases in manufacturing cost, unlike traditional methods where complexity often adds to the price.
Turnaround Time:
- Faster Production Cycles: The digital workflow of 3D printing can significantly reduce the time from design to final part. Once the digital model is finalized, the printing process can run relatively autonomously.
- Elimination of Casting Steps: By bypassing the multiple steps involved in lost-wax casting (wax-up, investing, burnout, casting, divesting), 3D printing can lead to quicker turnaround times.
- Produkcja na żądanie: 3D printing enables on-demand production, reducing the need for large inventories and allowing for faster delivery of customized frameworks.
While the initial cost of investing in in-house 3D printing equipment can be substantial, utilizing a reliable service provider like Metal3DP can offer a cost-effective entry point with predictable pricing structures. Our efficient processes and advanced technology are geared towards providing timely delivery of high-quality dental frameworks. Contact Metal3DP to discuss your specific requirements and receive a customized cost and lead time estimate.
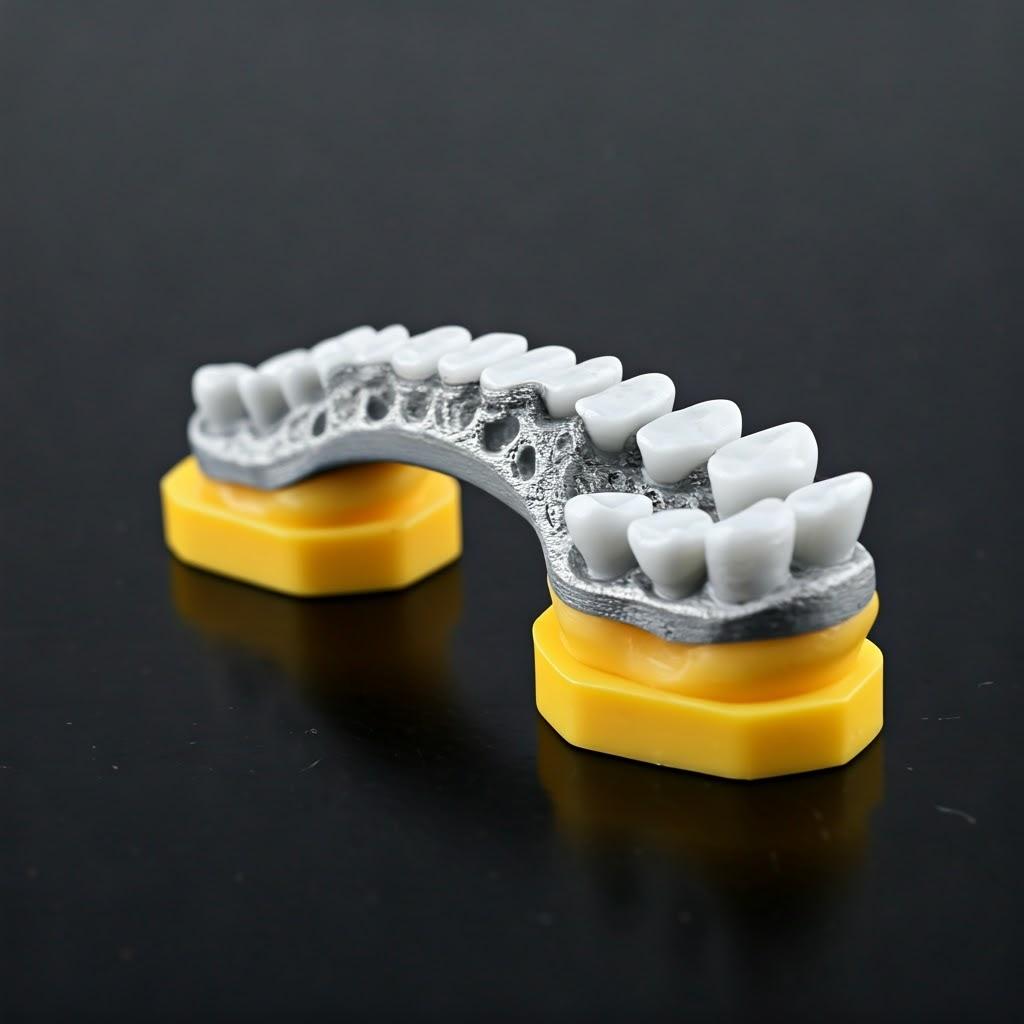
Frequently Asked Questions (FAQ) about 3D Printed Dental Bridge Frameworks
Here are some common questions that dental professionals have regarding 3D printed dental bridge frameworks:
- Are 3D printed metal dental bridges biocompatible? Yes, when manufactured using biocompatible metal powders like CoCrMo and CoCrW that meet relevant medical device standards, 3D printed dental bridges are highly biocompatible and safe for intraoral use. Metal3DP utilizes high-quality, certified metal powders to ensure the biocompatibility of our printed parts.
- What is the typical lifespan of a 3D printed metal dental bridge? The lifespan of a 3D printed metal dental bridge is comparable to that of traditionally fabricated bridges and depends on factors such as the material used, the accuracy of the fit, the patient’s oral hygiene, and the occlusal forces. With proper care, they can last for many years.
- Can 3D printed dental bridges be veneered with porcelain? Yes, 3D printed metal frameworks made from alloys like CoCrMo and CoCrW are fully compatible with conventional porcelain veneering techniques, allowing for the creation of aesthetically pleasing and functional restorations.
- What level of accuracy can be achieved with 3D printed dental frameworks? Metal 3D printing, especially technologies like SEBM used by Metal3DP, can achieve very high levels of accuracy, typically within tens of microns. This precision ensures an excellent fit and reduces the need for extensive adjustments.
- How do I prepare my digital scan for 3D printing of a dental bridge? The digital scan should be converted into an STL or other compatible file format and designed using dental CAD software, taking into account the specific requirements for metal 3D printing, such as minimum wall thickness and support considerations. Collaboration with an experienced 3D printing service provider like Metal3DP can provide valuable guidance on design optimization.
Conclusion: Embracing the Future of Dental Restorations with Metal 3D Printing
Metal 3D printing is revolutionizing the fabrication of dental bridge frameworks, offering significant advantages over traditional methods in terms of precision, design flexibility, material efficiency, and potentially faster turnaround times. By utilizing biocompatible and high-performance metal powders like CoCrMo and CoCrW, dental laboratories and clinicians can create restorations with optimal fit, strength, and aesthetics, ultimately enhancing patient care and satisfaction.
Metal3DP Technology Co., LTD is committed to empowering the dental industry with cutting-edge additive manufacturing solutions. Our industry-leading SEBM printers and high-quality metal powders, coupled with our application development expertise, provide a comprehensive pathway for dental professionals to embrace the future of digital dentistry. We invite you to explore the possibilities of metal 3D printing for your dental restoration needs and encourage you to skontaktuj się z Metal3DP to learn more about how our capabilities can support your practice or laboratory. By partnering with a trusted provider like us, you can confidently navigate the world of metal additive manufacturing and unlock new levels of precision and efficiency in your dental workflows.
Udostępnij
MET3DP Technology Co., LTD jest wiodącym dostawcą rozwiązań w zakresie produkcji addytywnej z siedzibą w Qingdao w Chinach. Nasza firma specjalizuje się w sprzęcie do druku 3D i wysokowydajnych proszkach metali do zastosowań przemysłowych.
Zapytaj o najlepszą cenę i spersonalizowane rozwiązanie dla Twojej firmy!
Powiązane artykuły
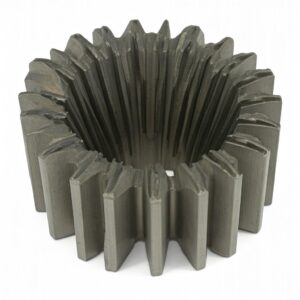
Wysokowydajne segmenty łopatek dysz: Rewolucja w wydajności turbin dzięki drukowi 3D w metalu
Czytaj więcej "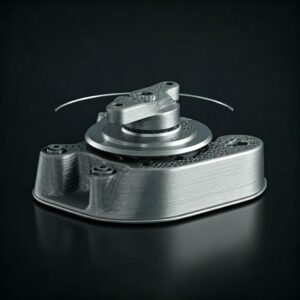
Drukowane w 3D mocowania dla samochodowych czujników radarowych: Precyzja i wydajność
Czytaj więcej "Informacje o Met3DP
Ostatnia aktualizacja
Nasz produkt
KONTAKT
Masz pytania? Wyślij nam wiadomość teraz! Po otrzymaniu wiadomości obsłużymy Twoją prośbę całym zespołem.