Formowanie wtryskowe metali (MIM)
Spis treści
Wyobraź sobie proces produkcyjny, który łączy skomplikowane szczegóły i swobodę projektowania formowania wtryskowego tworzyw sztucznych z niezrównaną wytrzymałością i trwałością metalu. To właśnie magia Formowanie wtryskowe metali (MIM), zmieniający zasady gry w świecie obróbki metali.
Czym jest formowanie wtryskowe metalu (MIM)?
MIM to technika produkcji w kształcie zbliżonym do siatki, która wykorzystuje unikalną mieszankę proszku metalowego i spoiwa polimerowego. Ta kombinacja, znana jako surowiec, zachowuje się podobnie jak pasta do formowania. Proces MIM strategicznie wstrzykuje ten surowiec do gniazda formy pod wysokim ciśnieniem, replikując pożądaną skomplikowaną geometrię. Oto podział procesu MIM na kluczowe etapy:
- Przygotowanie surowca: Drobno sproszkowany metal, zwykle stal nierdzewna, stopy stali, a nawet egzotyczne materiały, takie jak węglik wolframu, jest skrupulatnie mieszany z systemem spoiwa. Spoiwo to zapewnia płynność mieszanki podczas formowania wtryskowego.
- Formowanie: Przygotowany surowiec jest wtryskiwany pod wysokim ciśnieniem do precyzyjnie zaprojektowanej wnęki formy. Replikuje to skomplikowany kształt zbliżony do siatki pożądanego elementu metalowego.
- Debinding: Po formowaniu spoiwo musi zostać usunięte z uformowanej części. Ten delikatny proces, często nazywany usuwaniem spoiwa, może obejmować techniki termiczne (ogrzewanie) lub usuwanie spoiwa rozpuszczalnikiem, w zależności od wybranego systemu spoiwa.
- Spiekanie: Odtłuszczona część, będąca teraz kruchą strukturą proszku metalowego, poddawana jest procesowi spiekania w wysokiej temperaturze w kontrolowanej atmosferze. Ten kluczowy etap łączy ze sobą cząsteczki metalu, osiągając pożądaną wytrzymałość i gęstość końcowego komponentu.
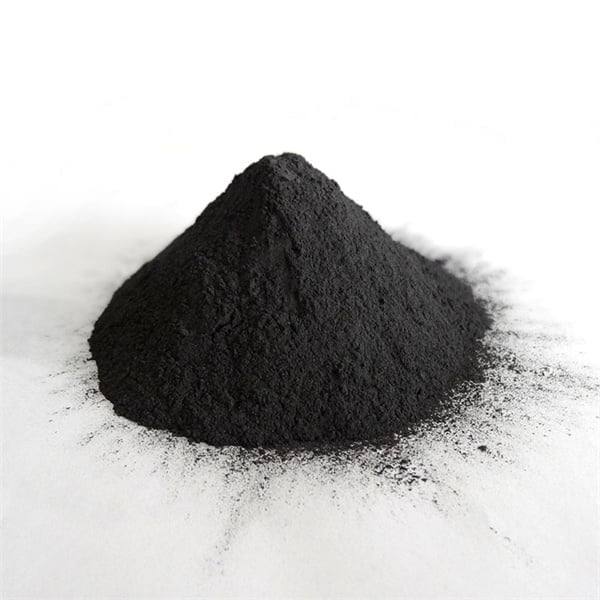
Zalety Formowanie wtryskowe metali (MIM)
MIM oferuje przekonujący zestaw zalet, które sprawiają, że jest to bardzo pożądany proces w różnych branżach:
- Geometrie złożone: W przeciwieństwie do tradycyjnych technik obróbki skrawaniem, które mogą zmagać się ze skomplikowanymi kształtami, MIM wyróżnia się w produkcji komponentów o złożonych cechach, wąskich tolerancjach i cienkich ściankach. Otwiera to drzwi dla innowacyjnych projektów, które wcześniej były trudne lub niemożliwe do osiągnięcia konwencjonalnymi metodami.
- Wysoka precyzja i powtarzalność: MIM wykorzystuje precyzję formowania wtryskowego, co skutkuje wysoce spójnymi częściami o minimalnych różnicach wymiarowych. Przekłada się to na niezawodną wydajność i mniejsze zapotrzebowanie na obróbkę końcową.
- Produkcja masowa: MIM to proces dobrze nadający się do produkcji wielkoseryjnej. Po skonfigurowaniu formy, MIM może wydajnie produkować dużą liczbę identycznych części, dzięki czemu idealnie nadaje się do zastosowań wymagających stałej jakości i dużych ilości.
- Wszechstronność materiału: MIM oferuje szeroką gamę kompatybilnych materiałów, od zwykłych stali nierdzewnych i narzędziowych po egzotyczne opcje, takie jak tytan i inconel. Pozwala to na wybór optymalnego materiału w oparciu o określoną wytrzymałość, odporność na korozję lub inne wymagania dotyczące wydajności aplikacji.
- Efektywność kosztowa: W porównaniu z tradycyjnymi technikami obróbki, zwłaszcza w przypadku złożonych geometrii, MIM może zaoferować znaczne oszczędności kosztów. Możliwość uzyskania kształtu zbliżonego do siatki minimalizuje straty materiału i zmniejsza zapotrzebowanie na rozległe operacje obróbki skrawaniem.
Zastosowania formowania wtryskowego metali (MIM)
Różnorodne zalety MIM sprawiły, że jest to popularny wybór w szerokim spektrum branż. Oto kilka znaczących przykładów:
- Motoryzacja: Technologia MIM doskonale sprawdza się w przemyśle motoryzacyjnym, produkując skomplikowane komponenty, takie jak koła zębate, zębatki, elementy zaworów i części układu paliwowego, znane ze swojej trwałości i dokładności wymiarowej.
- Urządzenia medyczne: Biokompatybilność niektórych materiałów MIM sprawia, że są one idealne do zastosowań medycznych. MIM jest wykorzystywany do tworzenia skomplikowanych narzędzi chirurgicznych, implantów i komponentów do różnych urządzeń medycznych.
- Elektronika użytkowa: Zdolność do produkcji małych, złożonych części z wysoką precyzją sprawia, że MIM jest idealnym rozwiązaniem dla branży elektroniki użytkowej. MIM znajduje zastosowanie w złączach, obudowach i wewnętrznych komponentach różnych urządzeń elektronicznych.
- Przemysł lotniczy i obronny: Wysokie wymagania sektora lotniczego i obronnego są dobrze dostosowane do MIM. MIM produkuje wysokowytrzymałe, lekkie komponenty do samolotów, statków kosmicznych i systemów uzbrojenia.
Więcej niż korzyści: Rozważania na temat MIM
Chociaż MIM oferuje mnóstwo zalet, przed wybraniem go do konkretnego zastosowania należy wziąć pod uwagę kilka czynników:
- Ograniczenia rozmiaru części: MIM ma obecnie ograniczenia dotyczące maksymalnego rozmiaru części, które może produkować. Części przekraczające określoną objętość mogą być lepiej dostosowane do tradycyjnych technik obróbki metalu.
- Istotne ograniczenia: Chociaż MIM oferuje szeroką gamę materiałów, niektóre egzotyczne lub specjalistyczne stopy mogą nie być łatwo dostępne lub opłacalne dzięki MIM.
- Koszty rozwoju: Konfiguracja procesu MIM dla nowego komponentu wymaga początkowych inwestycji w rozwój formy i optymalizację procesu. Ten czynnik kosztowy należy zestawić z potencjalną wielkością produkcji i długoterminowymi korzyściami.
Zrozumienie MIM: dogłębna analiza techniczna
Dla tych, którzy są zainteresowani technicznymi zawiłościami MIM, oto bliższe spojrzenie na niektóre kluczowe aspekty:
Wybór surowców: Wybór odpowiedniego surowca ma kluczowe znaczenie dla powodzenia procesu MIM. Oto kilka kluczowych aspektów, które należy wziąć pod uwagę:
- Metalowy proszek:
- Rozmiar i rozkład cząstek: Rozmiar i dystrybucja proszku metalowego znacząco wpływają na końcowe właściwości części. Drobniejsze proszki generalnie zapewniają ściślejsze tolerancje i gładsze wykończenia, ale mogą być również trudniejsze w obróbce ze względu na problemy z płynnością. Często preferowany jest dobrze zrównoważony rozkład wielkości cząstek.
- Morfologia proszku: Kształt cząstek metalu również odgrywa rolę. Sferyczne proszki mają tendencję do lepszego płynięcia i gęstszego upakowania, co prowadzi do poprawy wytrzymałości i dokładności wymiarowej.
- System spoiwa: System wiążący działa jak tymczasowy klej, utrzymując proszek metalowy razem podczas formowania i usuwania lepiszcza. Różne systemy wiążące oferują różne właściwości, takie jak stabilność termiczna, zachowanie podczas usuwania lepiszcza i kompatybilność z wybranym procesem usuwania lepiszcza.
Projektowanie form dla MIM:
Formy MIM wykazują podobieństwa do form wtryskowych z tworzyw sztucznych, ale wymagają szczególnych rozważań dotyczących zachowania proszku metalowego:
- Konstrukcja bramy: Konstrukcja wlewów, które są punktami wejścia materiału wsadowego do gniazda formy, musi zapewniać prawidłowy przepływ i minimalizować turbulencje, które mogą prowadzić do wad.
- Wentylacja: Kanały odpowietrzające mają kluczowe znaczenie dla umożliwienia ucieczki uwięzionego powietrza podczas wtrysku, zapobiegając powstawaniu pustych przestrzeni i zapewniając całkowite wypełnienie części.
- Draft Angles: Kąty zanurzenia na ściankach formy są niezbędne, aby ułatwić wyjmowanie uformowanej części po schłodzeniu.
Techniki odwijania w MIM:
Jak wspomniano wcześniej, usuwanie spoiwa jest krytycznym etapem usuwania spoiwa z uformowanej części. Oto zestawienie dwóch podstawowych technik usuwania spoiwa:
- Odszranianie termiczne: Metoda ta polega na stopniowym podgrzewaniu formowanej części w kontrolowanej atmosferze. Wraz ze wzrostem temperatury spoiwo ulega degradacji i rozkładowi, pozostawiając strukturę proszku metalu. Profil ogrzewania musi być starannie zaprojektowany, aby zapewnić całkowite usunięcie spoiwa bez uszkodzenia delikatnej struktury metalu.
- Odwiązywanie rozpuszczalnikiem: Technika ta wykorzystuje rozpuszczalnik, który selektywnie rozpuszcza system wiążący. Formowana część jest zanurzana w rozpuszczalniku, co pozwala na wypłukanie spoiwa, podczas gdy proszek metalowy pozostaje nienaruszony. Usuwanie lepiszcza za pomocą rozpuszczalnika może być szybsze niż usuwanie lepiszcza metodą termiczną, ale może wymagać specjalnej obsługi i utylizacji zużytego rozpuszczalnika.
Spiekanie w technologii MIM:
Spiekanie to ostatni etap procesu MIM, w którym proszek metalu przekształca się w stały, funkcjonalny komponent. Podczas spiekania część jest wystawiana na działanie wysokich temperatur (zazwyczaj w zakresie od 1/2 do 2/3 temperatury topnienia metalu) w kontrolowanej atmosferze. Ta wysoka temperatura sprzyja wiązaniu dyfuzyjnemu między cząstkami metalu, powodując zagęszczenie i znaczną poprawę wytrzymałości i innych właściwości mechanicznych.
Kontrola jakości w MIM:
Utrzymanie stałej jakości jest najważniejsze w produkcji MIM. Oto kilka podstawowych środków kontroli jakości:
- Charakterystyka surowców: Regularne testowanie właściwości surowca, takich jak rozkład wielkości proszku metalu i zawartość spoiwa, zapewnia spójne zachowanie materiału podczas przetwarzania.
- Kontrola wymiarów: Wymiary formowanych części są skrupulatnie sprawdzane, aby zapewnić ich zgodność ze specyfikacjami projektowymi i zachowanie wąskich tolerancji.
- Pomiar gęstości: Gęstość spiekanych części jest krytycznym wskaźnikiem ich wytrzymałości i wydajności. Do pomiaru gęstości można wykorzystać różne techniki, takie jak zasada Archimedesa lub piknometria.
- Analiza mikrostruktury: Badanie mikroskopowe mikrostruktury spiekanej części ujawnia informacje o wielkości ziarna, porowatości i potencjalnych wadach.
Przyszłość Formowanie wtryskowe metali
MIM jest stale rozwijającą się technologią, której badania i rozwój koncentrują się na:
- Rozszerzający się zakres materiałów: Poszukiwanie nowych materiałów i systemów spoiw kompatybilnych z MIM poszerza możliwości zastosowania tego wszechstronnego procesu.
- Zwiększona wydajność procesu: Badania mają na celu optymalizację etapów usuwania lepiszcza i spiekania, aby skrócić czas cyklu i zwiększyć ogólną wydajność produkcji.
- Zaawansowana złożoność części: Rozwój w dziedzinie projektowania form i materiałoznawstwa przesuwa granice osiągalnej złożoności części dzięki MIM.
Formowanie wtryskowe metali oferuje unikalne połączenie swobody projektowania, wszechstronności materiałów i opłacalności dla szerokiego zakresu branż. W miarę dojrzewania tej technologii możemy spodziewać się jeszcze bardziej innowacyjnych zastosowań i postępów w ekscytującym świecie MIM.
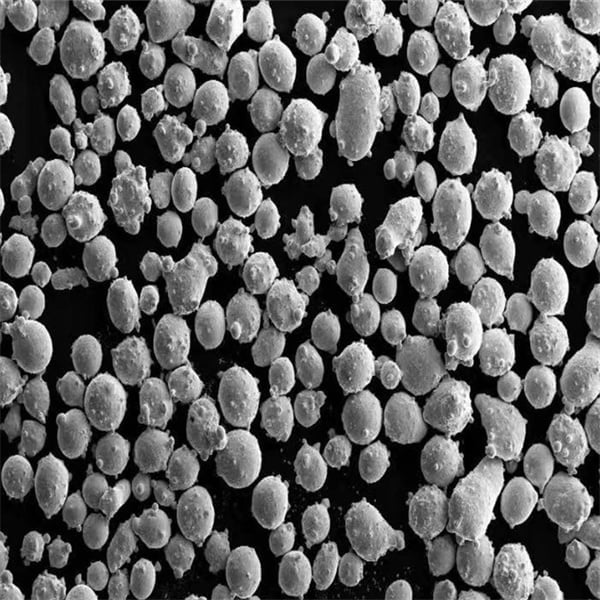
FAQ
Tabela 1: Często zadawane pytania dotyczące formowania wtryskowego metali (MIM)
Pytanie | Odpowiedź |
---|---|
Jakie są typowe ograniczenia rozmiaru części MIM? | Maksymalny rozmiar części MIM jest zazwyczaj ograniczony do kilku cali sześciennych. Ograniczenie to wynika z wyzwań związanych z przepływem surowca i zapewnieniem jednolitego usuwania zadziorów w większych częściach. |
Czy MIM może być używany do prototypowania? | Tak, MIM może być realną opcją do prototypowania złożonych części metalowych, zwłaszcza gdy wymagany jest wysoki stopień dokładności i wierności ostatecznemu projektowi. Należy jednak wziąć pod uwagę początkowy koszt opracowania formy. |
Jakie są zalety MIM w porównaniu do tradycyjnej obróbki skrawaniem? | MIM oferuje kilka zalet w porównaniu z tradycyjną obróbką skrawaniem, w tym Zdolność do wytwarzania złożonych geometrii z wąskimi tolerancjami Większa swoboda projektowania skomplikowanych funkcji Wysoka precyzja i powtarzalność dla spójnych części Wydajność produkcji masowej dla dużych ilości Zmniejszona ilość odpadów materiałowych w porównaniu do technik subtraktywnych |
Jakie są wady MIM w porównaniu do tradycyjnej obróbki skrawaniem? | MIM ma również pewne ograniczenia, które należy wziąć pod uwagę: Ograniczenia rozmiaru części w porównaniu z technikami takimi jak odlewanie lub kucie Ograniczenia materiałowe dla niektórych egzotycznych lub specjalistycznych stopów Wyższe koszty początkowe ze względu na rozwój formy Wykończenie powierzchni może nie pasować do wyjątkowo gładkich wykończeń osiąganych poprzez polerowanie lub szlifowanie. |
Jakie czynniki należy wziąć pod uwagę przy wyborze między MIM a tradycyjną obróbką metali? | Idealny wybór zależy od konkretnego zastosowania. Oto kilka kluczowych czynników, które należy wziąć pod uwagę: Złożoność geometrii części Wymagania dotyczące wielkości produkcji Potrzeby w zakresie wyboru materiałów Rozważania dotyczące kosztów, w tym inwestycji początkowych i potencjalnych oszczędności Wymagania dotyczące wykończenia powierzchni |
Jakie są przyszłe trendy w technologii MIM? | Wysiłki badawczo-rozwojowe w dziedzinie MIM koncentrują się na rozszerzeniu zakresu materiałów, poprawie wydajności procesu w celu skrócenia czasu cyklu i przesunięciu granic możliwej do osiągnięcia złożoności części. |
Jakie są typowe zastosowania MIM? | MIM znajduje zastosowanie w wielu różnych branżach, w tym: Motoryzacja (koła zębate, zębatki, elementy zaworów) Urządzenia medyczne (narzędzia chirurgiczne, implanty) Elektronika użytkowa (złącza, obudowy) Przemysł lotniczy i obronny (wysokowytrzymałe, lekkie komponenty) |
Jakie są różne rodzaje surowców stosowanych w MIM? | Materiał wsadowy MIM zazwyczaj składa się z proszku metalu (np. stali nierdzewnej, stopów stali, tytanu) zmieszanego z polimerowym systemem wiążącym. Konkretny rodzaj proszku metalowego i spoiwa zależy od pożądanych właściwości końcowych części. |
Jakie są różne techniki usuwania izolacji stosowane w MIM? | Istnieją dwie podstawowe techniki usuwania izolacji: Rozdrabnianie termiczne: Stopniowe ogrzewanie w celu usunięcia spoiwa. Usuwanie lepiszcza za pomocą rozpuszczalnika: Użycie rozpuszczalnika do selektywnego rozpuszczenia spoiwa. |
Wybór właściwego procesu: MIM a tradycyjna obróbka metali
Decyzja między MIM a tradycyjnymi technikami obróbki metalu zależy od różnych czynników specyficznych dla danego zastosowania. Oto kilka kluczowych kwestii, którymi należy się kierować przy dokonywaniu wyboru:
- Geometria części: Jeśli komponent ma złożone cechy, wąskie tolerancje i skomplikowane szczegóły, MIM oferuje znaczną przewagę.
- Wielkość produkcji: W przypadku produkcji wielkoseryjnej, wydajność i powtarzalność MIM sprawiają, że jest to atrakcyjna opcja.
- Wybór materiału: Upewnij się, że wymagany materiał jest kompatybilny z MIM. Jeśli potrzebujesz egzotycznego stopu, który nie jest łatwo dostępny w MIM, najlepszym rozwiązaniem może być tradycyjna obróbka metalu.
- Rozważania dotyczące kosztów: Należy wziąć pod uwagę początkowe koszty opracowania formy dla MIM w porównaniu z potencjalnymi stratami materiałowymi i dłuższym czasem produkcji tradycyjnych technik dla złożonych części.
- Wymagania dotyczące wykończenia powierzchni: Jeśli nieskazitelne wykończenie powierzchni jest najważniejsze, konieczne może być zastosowanie tradycyjnych technik, takich jak polerowanie.
Wnioski
Formowanie wtryskowe metali (MIM) jest potężnym i wszechstronnym procesem produkcyjnym, oferującym unikalne połączenie swobody projektowania, opcji materiałowych i opłacalności w szerokim zakresie zastosowań. Rozumiejąc jego zalety, ograniczenia i porównanie z tradycyjnymi technikami obróbki metalu, można podejmować świadome decyzje, aby wykorzystać MIM do konkretnych potrzeb i uwolnić potencjał innowacyjnych i wysokowydajnych komponentów metalowych.
Udostępnij
MET3DP Technology Co., LTD jest wiodącym dostawcą rozwiązań w zakresie produkcji addytywnej z siedzibą w Qingdao w Chinach. Nasza firma specjalizuje się w sprzęcie do druku 3D i wysokowydajnych proszkach metali do zastosowań przemysłowych.
Zapytaj o najlepszą cenę i spersonalizowane rozwiązanie dla Twojej firmy!
Powiązane artykuły
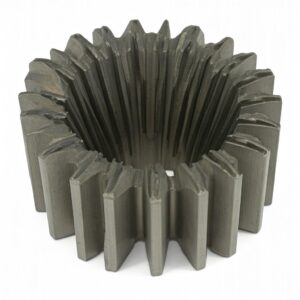
Wysokowydajne segmenty łopatek dysz: Rewolucja w wydajności turbin dzięki drukowi 3D w metalu
Czytaj więcej "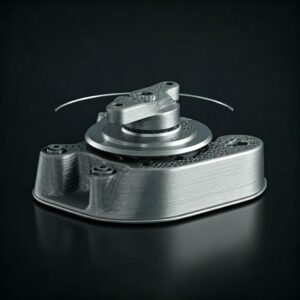
Drukowane w 3D mocowania dla samochodowych czujników radarowych: Precyzja i wydajność
Czytaj więcej "Informacje o Met3DP
Ostatnia aktualizacja
Nasz produkt
KONTAKT
Masz pytania? Wyślij nam wiadomość teraz! Po otrzymaniu wiadomości obsłużymy Twoją prośbę całym zespołem.
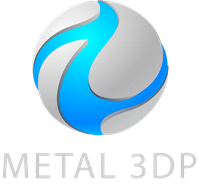
Proszki metali do druku 3D i produkcji addytywnej