plasam atomization
Table of Contents
Imagine a sculptor, not wielding a chisel and hammer, but wielding a high-tech torch that breaks down molten metal into perfectly spherical particles. That’s the essence of plasam atomization, a transformative technology that’s revolutionizing the way we create advanced materials.
What is plasam atomization?
Plasma atomization utilizes the intense heat and power of plasma, a state of matter even hotter than gas, to melt and atomize metal feedstock (usually wire) into a fine powder. This powder, with its near-perfect spherical shape and exceptional purity, becomes the building block for a wide range of cutting-edge applications.
The Power of Plasma: A Closer Look
The process starts with feeding a continuous stream of metal wire into a high-temperature plasma torch. This torch generates a concentrated beam of ionized gas, reaching temperatures exceeding 15,000°C (27,000°F). At such extreme temperatures, the metal wire instantly melts, transforming into a molten droplet. But the journey doesn’t end there.
The next step involves rapid atomization. The molten droplet is subjected to a high-velocity gas stream, typically argon, which breaks it down into tiny droplets. This rapid cooling and forceful shearing create the characteristic spherical shape of the metal powder particles. Finally, the powder is collected and classified according to size and other desired properties.
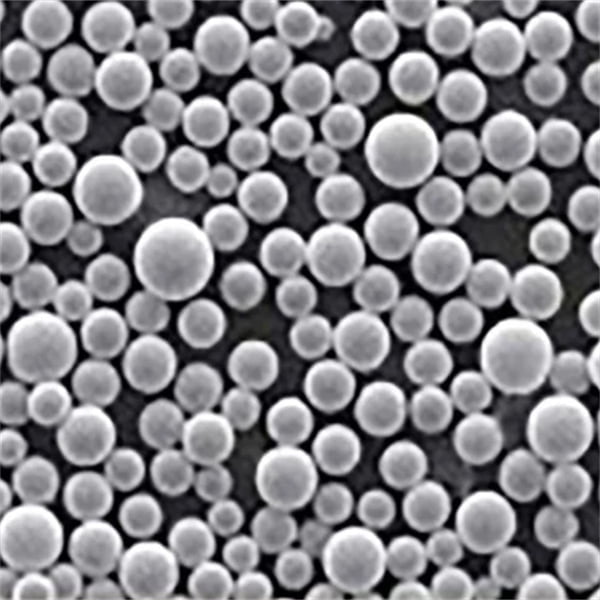
Metal Marvels: A Gallery of Powders
Plasma atomization isn’t a one-size-fits-all process. By tweaking various parameters like feedstock material, plasma temperature, and atomizing gas pressure, manufacturers can create a diverse range of metal powders with specific properties. Here’s a glimpse into the fascinating world of plasma-atomized metal powders:
1. Titanium Powders: The workhorse of the aerospace and medical industries, titanium powders come in various grades, including commercially pure (CP) and titanium alloys like Ti-6Al-4V. CP titanium powder offers excellent corrosion resistance and biocompatibility, making it ideal for prosthetics and implants. Ti-6Al-4V powder, known for its high strength-to-weight ratio, finds its place in aircraft components and jet engine parts.
2. Nickel Powders: Nickel powders, both pure and alloyed, play a crucial role in various applications. Pure nickel powder boasts high electrical conductivity and magnetic permeability, making it perfect for electronics and battery components. Nickel-based superalloy powders, on the other hand, offer exceptional heat resistance and mechanical strength, crucial for parts operating under extreme conditions like turbine blades and rocket engines.
3. Cobalt Powders: A key element in many hard-wearing alloys, cobalt powders find use in applications like wear-resistant coatings, dental implants, and cutting tools.
4. Stainless Steel Powders: From kitchenware to medical instruments, stainless steel is a ubiquitous material. Plasma atomization allows for the creation of various stainless steel powder grades, each with its unique combination of corrosion resistance and mechanical properties.
5. Aluminum Powders: Lightweight and versatile, aluminum powders produced through plasma atomization offer several advantages. Compared to traditionally produced powders, they boast superior flowability and packing density, making them ideal for additive manufacturing processes like metal 3D printing.
6. Copper Powders: Highly conductive and malleable, copper powders find application in various electrical and thermal management applications. Plasma-atomized copper powders offer exceptional purity and consistent particle size distribution, crucial for achieving optimal electrical performance.
7. Tungsten Powders: Renowned for its high melting point and density, tungsten finds use in a variety of demanding applications. Plasma-atomized tungsten powders offer exceptional purity and controlled particle size distribution, making them ideal for applications like tungsten inert gas (TIG) welding electrodes and armor-piercing projectiles.
8. Tantalum Powders: A rare and valuable metal prized for its exceptional corrosion resistance, tantalum powders find use in capacitors, surgical implants, and chemical processing equipment.
9. Molybdenum Powders: Offering high melting point and good thermal conductivity, molybdenum powders are used in applications like heating elements, electrodes, and rocket engine nozzles.
10. Inconel Powders: A family of nickel-chromium superalloys known for their exceptional heat and corrosion resistance, Inconel powders are used in demanding applications like gas turbine components and heat exchangers.
These are just a few examples, and the possibilities with plasma atomization are truly endless. With its ability to produce high-purity, spherical powders from a wide range of materials, this technology is paving the way for advancements in various sectors, including:
- Aerospace: Lighter, stronger aircraft components with improved fuel efficiency.
- Medical: Biocompatible implants and prosthetics that last longer and integrate better with the body. Imagine a world where hip replacements become routine procedures, and artificial joints function seamlessly for decades. Plasma atomization is making such advancements a reality by enabling the creation of customized implants with improved biocompatibility and osseointegration (the ability to bond with bone).
- Electronics: Smaller, more efficient electronic components. The ever-shrinking size of electronic devices demands high-performance materials with precise properties. Plasma atomization allows for the creation of metal powders with exceptional purity and consistent particle size, crucial for producing miniaturized electronic components with superior performance.
- Automotive: Lighter, stronger car parts that improve fuel efficiency and performance. As the automotive industry strives for sustainability and performance, plasma atomization comes into play. This technology enables the creation of lighter yet stronger metal powders for components like pistons and connecting rods, leading to lighter vehicles with improved fuel economy and handling.
- Additive Manufacturing (3D Printing): The foundation for printing complex metal parts. Additive manufacturing, or 3D printing, is revolutionizing how we create complex metal parts. Plasma atomization plays a critical role in this process by providing high-quality, flowable metal powders that can be precisely deposited layer by layer to create intricate structures.
Beyond these core applications, plasma atomization has the potential to impact a vast array of industries, including:
- Energy: Development of more efficient and sustainable energy technologies.
- Construction: Creation of stronger, lighter building materials with improved durability.
- Consumer Goods: Production of high-performance sporting goods and other consumer products.
The Future of plasam atomization
Plasma atomization is a rapidly evolving technology, with ongoing research and development pushing the boundaries of what’s possible. Here are some exciting trends to watch for:
- Multi-material Powders: The creation of powders with a blend of different materials, offering unique combinations of properties. This opens doors for the development of novel materials with tailor-made functionalities.
- Nano Powders: Production of ultra-fine metal powders in the nanoscale range, enabling the creation of advanced materials with unique properties. Imagine materials with enhanced strength, conductivity, or catalytic activity.
- Sustainable Practices: Development of environmentally friendly processes for plasma atomization, minimizing energy consumption and waste generation.
Plasma atomization is more than just a technology; it’s a catalyst for innovation. By unlocking the potential of metal powders, it’s paving the way for a future filled with lighter, stronger, and more functional materials that will shape the world around us.
Advantages and Limitations of Plasma Atomization
Advantages:
- High Purity: Plasma atomization produces exceptionally pure metal powders with minimal contamination. This is crucial for applications demanding high performance and biocompatibility.
- Spherical Shape: The near-perfect spherical shape of plasma-atomized powders offers several advantages. It improves flowability, leading to better packing density and efficient handling during processing. Additionally, spherical particles minimize stress concentrations, leading to stronger and more durable final products.
- Fine Particle Size: Plasma atomization allows for the production of fine metal powders, enabling the creation of intricate structures and components with superior surface finishes.
- Wide Range of Materials: This technology is adaptable to a vast array of materials, from common metals like aluminum and titanium to more exotic materials like tantalum and molybdenum.
Limitations:
- High Cost: Plasma atomization equipment and processes can be expensive to set up and maintain. This translates to a higher cost for the resulting metal powders compared to some conventional methods.
- Energy Consumption: The high temperatures involved in the process can lead to significant energy consumption. However, ongoing research is focused on developing more energy-efficient methods.
- Process Complexity: Plasma atomization involves a complex interplay of various parameters like feedstock material, plasma temperature, and atomizing gas pressure. Optimizing these parameters for a specific material requires expertise and experience.
Choosing the Right Technology: Plasma Atomization vs. Other Powder Production Methods
Plasma atomization isn’t the only game in town when it comes to metal powder production. Here’s a quick comparison with some other common methods:
- Gas Atomization: Similar to plasma atomization, gas atomization uses a high-velocity gas stream to break down molten metal into droplets. However, gas atomization typically uses lower temperatures, resulting in powders with a broader size distribution and less spherical morphology compared to plasma atomization.
- Water Atomization: A more cost-effective method, water atomization utilizes a high-pressure water jet to break down molten metal.
- Electrolytic Deposition: This method involves electrodeposition of metal ions onto a cathode to create a metal powder. While offering good control over particle size, electrolytic deposition is limited in terms of the materials it can produce and the production rate.
Ultimately, the choice of powder production method depends on several factors, including:
- Desired powder properties: Purity, particle size, and shape are crucial considerations.
- Material compatibility: Not all methods are suitable for all materials.
- Cost and production volume: Plasma atomization might be overkill for low-volume applications.
Plasma atomization stands out for its ability to produce high-purity, spherical powders from a wide range of materials. However, its higher cost and energy consumption need to be weighed against the benefits it offers.
Specifications, Sizes, Grades, and Standards for Plasma-Atomized Powders
As with any manufactured product, plasma-atomized metal powders come in various specifications, sizes, grades, and adhere to specific standards. Here’s a breakdown of these factors:
Specifications:
- Chemical Composition: The exact chemical composition of the powder, including the main element and any trace elements present. This information is crucial for ensuring the powder meets the desired material properties.
- Particle Size Distribution (PSD): This refers to the range of particle sizes present in the powder, typically expressed as a statistical distribution. A narrow PSD is often preferred for applications demanding consistent material properties.
- Apparent Density: The bulk density of the powder, which is a measure of how much powder occupies a given volume. Flowability and packing characteristics are often dependent on apparent density.
- Flowability: This refers to the ease with which the powder flows and how well it fills a mold or container. Good flowability is essential for efficient processing, particularly in additive manufacturing.
- Surface Morphology: The shape and texture of the powder particles. Plasma-atomized powders are known for their near-perfect spherical shape, but surface roughness can also be a factor depending on the application.
Sizes:
Plasma-atomized metal powders come in a wide range of sizes, typically ranging from a few microns (micrometers) to several hundred microns. The specific size range will depend on the desired application. For instance, finer powders are better suited for additive manufacturing processes like metal 3D printing, while coarser powders might be used for applications like thermal spraying.
Grades:
Metal powders can be classified into different grades based on their chemical composition, particle size distribution, and other properties. Common grades include:
- Commercially Pure (CP): A basic grade with minimal alloying elements.
- Alloy Grades: Powders containing specific combinations of elements to achieve desired properties like strength, corrosion resistance, or high-temperature performance.
- Medical Grades: Powders meeting stringent biocompatibility requirements for use in medical implants and prosthetics.
Standards:
There are various industry standards that govern the production and quality of plasma-atomized metal powders. Some of the prominent standards include:
- ASTM International (ASTM): A global standards organization that publishes various standards for metal powders, including specifications for particle size, chemical composition, and flowability.
- American Society for Materials and Testing (ASM International): Another leading organization that sets standards for materials, including metal powders.
- International Organization for Standardization (ISO): This international organization publishes a range of standards related to metal powders, covering aspects like terminology, classification, and testing methods.
By adhering to these standards, manufacturers ensure that plasma-atomized metal powders meet consistent quality levels and are suitable for their intended applications.
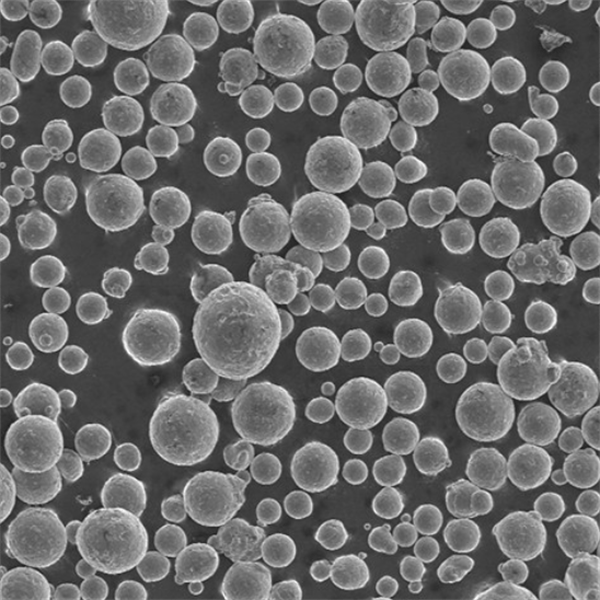
Suppliers and Pricing of Plasma-Atomized Powders
The global market for plasma-atomized metal powders is experiencing steady growth, driven by increasing demand from various industries. Several leading manufacturers offer a wide range of metal powders produced through plasma atomization. Here’s a glimpse into some of the key players:
- APEX Materials: A global supplier of metal powders, including a wide variety of plasma-atomized powders for aerospace, medical, and other applications.
- Höganäs AB: A Swedish manufacturer specializing in metal powders, offering plasma-atomized powders for additive manufacturing and other processes.
- AMETEK SMP: A leading provider of metal powders for additive manufacturing, including plasma-atomized powders for various materials.
- SLM Solutions: A prominent player in the metal 3D printing industry, also offering a range of plasma-atomized metal powders compatible with their 3D printing systems.
Pricing for plasma-atomized metal powders can vary depending on several factors, including:
- Material: Exotic or rare earth metals will typically command a higher price than common metals.
- Powder Grade: High-purity or medical-grade powders will be more expensive than commercially pure grades.
- Particle Size Distribution: Powders with a narrow PSD typically require more precise processing and may be priced higher.
- Quantity: Bulk purchases often attract discounts compared to smaller quantities.
As a general estimate, the price for plasma-atomized metal powders can range from tens of dollars per kilogram for common materials like aluminum to several hundred dollars per kilogram for high-purity or exotic materials. It’s important to consult with specific suppliers for current pricing information based on your desired material, grade, and quantity.
FAQ
1. What are the advantages of using plasma atomization over other powder production methods?
Plasma atomization offers several advantages, including:
- High purity: Minimal contamination for superior performance and biocompatibility.
- Spherical shape: Improved flowability, packing density, and stronger final products.
- Fine particle size: Enables creation of intricate structures and components.
- Wide range of materials: Applicable to various metals, from common to exotic.
2. What are the limitations of plasma atomization?
The limitations include:
- High cost: Setting up and maintaining equipment can be expensive, leading to higher powder costs.
- Energy consumption: The high temperatures involved require significant energy input.
- Process complexity: Optimizing parameters for specific materials requires expertise.
3. How does plasma atomization compare to gas atomization?
Both methods use a high-velocity gas stream to break down molten metal. However, plasma atomization uses higher temperatures, resulting in:
- Purer powders: Plasma offers a cleaner environment with less contamination.
- More spherical shapes: Plasma-atomized powders are closer to perfect spheres.
- Finer particle size: Plasma allows for creation of finer powders.
4. What are some of the applications of plasma-atomized metal powders?
These powders find use in a wide range of industries, including:
- Aerospace: Lighter, stronger aircraft components for improved fuel efficiency.
- Medical: Biocompatible implants and prosthetics with better integration with the body.
- Electronics: Smaller, more efficient electronic components with precise properties.
- Automotive: Lighter, stronger car parts for better fuel economy and performance.
- Additive Manufacturing (3D Printing): The foundation for printing complex metal parts.
5. What are the future trends in plasma atomization?
Exciting developments include:
- Multi-material powders: Blending different materials for unique property combinations.
- Nano powders: Ultra-fine powders for advanced materials with enhanced properties.
- Sustainable practices: More energy-efficient and environmentally friendly processes.
know more 3D printing processes
Share On
MET3DP Technology Co., LTD is a leading provider of additive manufacturing solutions headquartered in Qingdao, China. Our company specializes in 3D printing equipment and high-performance metal powders for industrial applications.
Inquiry to get best price and customized Solution for your business!
Related Articles
About Met3DP
Recent Update
Our Product
CONTACT US
Any questions? Send us message now! We’ll serve your request with a whole team after receiving your message.
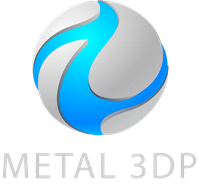
Metal Powders for 3D Printing and Additive Manufacturing