Plasma Atomization
Table of Contents
Welcome to our extensive guide on plasma atomization. Whether you’re a curious novice or an industry expert, this comprehensive article will provide you with a detailed understanding of plasma atomization, its applications, and its role in the production of high-quality metal powders. We’ll cover everything from the basics to the specifics, including different metal powder models and their properties. Let’s dive in!
Overview of Plasma Atomization
Plasma atomization is a process used to produce fine, spherical metal powders with a high degree of purity. This method involves the use of a plasma torch to melt a metal feedstock, which is then atomized into fine droplets and solidified into powder form. The resulting powders are characterized by their uniform particle size distribution and excellent flowability, making them ideal for various high-tech applications.
Key Points:
- What is Plasma Atomization? A process using a plasma torch to produce fine metal powders.
- Why Use Plasma Atomization? It ensures high purity, uniform particle size, and excellent flowability.
- Applications: Widely used in additive manufacturing, metal injection molding, and thermal spray coatings.
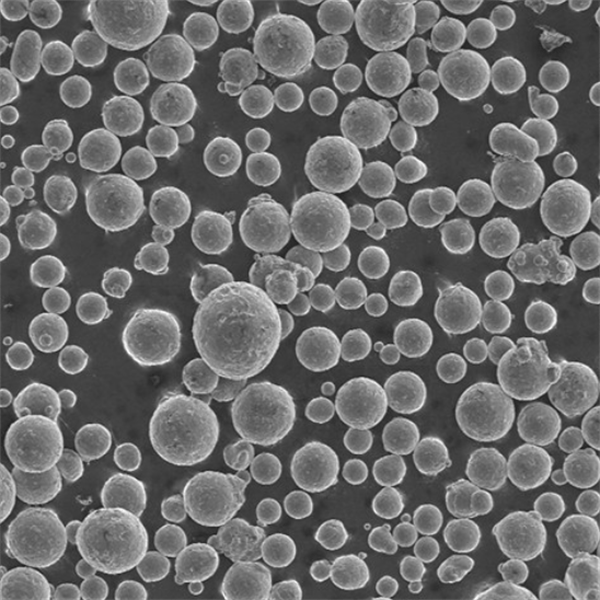
Types of Metal Powders Produced by Plasma Atomization
The plasma atomization process can produce a variety of metal powders, each with specific properties and applications. Here, we list and describe some of the most commonly produced metal powders:
Metal Powder | Composition | Properties | Applications |
---|---|---|---|
Titanium (Ti) | Pure Titanium | High strength-to-weight ratio, corrosion resistance | Aerospace, biomedical implants, automotive |
Titanium Alloys | Ti-6Al-4V, Ti-6Al-2Sn-4Zr | Enhanced mechanical properties, high temperature performance | Aerospace, military applications |
Nickel (Ni) | Pure Nickel | High melting point, excellent corrosion resistance | Electronics, aerospace, chemical processing |
Nickel Alloys | Inconel 718, Hastelloy X | High strength, oxidation resistance | Turbine engines, nuclear reactors, chemical plants |
Stainless Steel | 316L, 304L | Corrosion resistance, good mechanical properties | Medical devices, food processing, marine applications |
Aluminum (Al) | Pure Aluminum, AlSi10Mg | Lightweight, good thermal conductivity | Automotive, aerospace, packaging |
Cobalt-Chromium (CoCr) | CoCrMo | High wear resistance, biocompatibility | Orthopedic implants, dental prosthetics |
Copper (Cu) | Pure Copper, CuNi2SiCr | Excellent electrical conductivity, antimicrobial properties | Electrical components, medical devices |
Iron (Fe) | Pure Iron | Good magnetic properties, high strength | Magnets, heavy machinery, construction |
Magnesium (Mg) | Pure Magnesium | Lightweight, good mechanical properties | Aerospace, automotive, electronics |
Applications of Plasma Atomization
Plasma atomization has revolutionized various industries by providing high-quality metal powders. Here’s a detailed look at where and how these powders are used:
Additive Manufacturing (3D Printing)
Additive manufacturing relies heavily on the precision and quality of metal powders produced through plasma atomization. The uniform particle size and purity ensure consistent layer formation and optimal mechanical properties in 3D-printed components.
Metal Injection Molding (MIM)
Metal powders are mixed with a binder to form a feedstock for injection molding. Plasma-atomized powders are preferred due to their high purity and flowability, which are crucial for producing intricate shapes and maintaining structural integrity.
Thermal Spray Coatings
In thermal spray processes, metal powders are melted and sprayed onto surfaces to form coatings. Plasma-atomized powders provide excellent adhesion and coating properties, enhancing wear resistance and corrosion protection.
Biomedical Applications
High-purity titanium and cobalt-chromium powders are used to manufacture implants and prosthetics. The biocompatibility and mechanical properties of these powders make them ideal for medical applications.
Aerospace and Automotive
Lightweight and high-strength metal powders such as titanium and aluminum alloys are used to produce critical components in aerospace and automotive industries. Plasma atomization ensures the quality and performance required for these demanding applications.
Electronics
Nickel and copper powders are essential in the production of electronic components due to their excellent electrical and thermal conductivity. Plasma-atomized powders help in achieving the necessary precision and reliability in these applications.
Energy Sector
Nickel alloys and stainless steel powders are used in the energy sector for manufacturing components exposed to high temperatures and corrosive environments, such as in turbines and reactors.
Characteristics and Properties of Plasma-Atomized Powders
The quality of metal powders produced by plasma atomization is defined by several key characteristics:
Characteristic | Description |
---|---|
Particle Size Distribution | Narrow and uniform, ensuring consistent performance in applications. |
Purity | High purity levels due to the inert atmosphere during production, minimizing contamination. |
Sphericity | High sphericity enhances flowability and packing density, critical for additive manufacturing and MIM. |
Flowability | Excellent flowability ensures efficient processing and handling in various applications. |
Density | High apparent and tap density, leading to better mechanical properties in finished products. |
Surface Morphology | Smooth surfaces, reducing friction and wear during processing and application. |
Advantages of Plasma Atomization
Plasma atomization offers several benefits over other powder production methods:
High Purity
The use of an inert gas plasma torch ensures that the metal powders produced are of high purity, free from oxidation and contamination.
Uniform Particle Size
The process results in powders with a narrow particle size distribution, which is crucial for consistent performance in additive manufacturing and other applications.
Excellent Flowability
The spherical shape of the particles enhances flowability, making the powders easy to handle and process.
Versatility
Plasma atomization can produce powders from a wide range of metals and alloys, offering flexibility for different industrial needs.
Disadvantages of Plasma Atomization
Despite its many advantages, plasma atomization also has some limitations:
High Cost
The equipment and energy required for plasma atomization are expensive, making the process cost-prohibitive for some applications.
Complexity
The process involves complex machinery and requires skilled operators, adding to the operational costs.
Limited Material Range
While versatile, not all metals and alloys can be easily processed using plasma atomization, limiting its application scope.
Specifications, Sizes, and Standards of Plasma-Atomized Powders
To meet the diverse needs of various industries, plasma-atomized powders are available in different specifications and sizes. Here’s a breakdown:
Metal Powder | Particle Size Range (μm) | Common Standards |
---|---|---|
Titanium (Ti) | 15-45, 45-106 | ASTM F1580, ASTM B348 |
Nickel (Ni) | 15-45, 45-106 | ASTM B330, AMS 4777 |
Stainless Steel | 15-45, 45-106 | ASTM A564, ASTM A479 |
Aluminum (Al) | 15-45, 45-106 | ASTM B211, AMS 4078 |
Cobalt-Chromium (CoCr) | 15-45, 45-106 | ASTM F75, ISO 5832-4 |
Copper (Cu) | 15-45, 45-106 | ASTM B187, ASTM B152 |
Iron (Fe) | 15-45, 45-106 | ASTM A848, ASTM A510 |
Magnesium (Mg) | 15-45, 45-106 | ASTM B107, AMS 4377 |
Suppliers and Pricing Details of Plasma-Atomized Powders
Finding the right supplier for plasma-atomized powders is crucial for ensuring quality and consistency. Here are some of the leading suppliers along with their pricing details:
Supplier | Metal Powders | Price Range (per kg) | Notes |
---|---|---|---|
AP&C (a GE Additive company) | Titanium, Nickel, Aluminum | $200 – $500 | High-quality, widely used in aerospace |
Praxair Surface Technologies | Stainless Steel, Cobalt-Chromium | $150 – $400 | Known for consistent quality |
Tekna Plasma Systems | Titanium, Nickel, Magnesium | $250 – $600 | Innovative production techniques |
Sandvik Osprey | Stainless Steel, Copper, Iron | $100 – $300 | Established supplier with broad range |
Höganäs AB | Nickel, Cobalt-Chromium, Aluminum | $180 – $450 | Specializes in high-performance powders |
Carpenter Additive | Titanium, Stainless Steel, Aluminum | $220 – $500 | Focus on additive manufacturing |
LPW Technology (a Carpenter company) | Titanium, Nickel, Aluminum | $210 – $490 | High-end powders for critical applications |
GKN Hoeganaes | Iron, Copper, Nickel | $120 – $350 | Leading supplier with extensive portfolio |
AMETEK Specialty Metal Products | Titanium, Nickel, Stainless Steel | $200 – $480 | High-quality powders for diverse uses |
Renishaw | Stainless Steel, Cobalt-Chromium, Aluminum | $180 – $470 | Advanced manufacturing capabilities |
Comparing Plasma Atomization with Other Powder Production Methods
When considering the production of metal powders, it’s important to compare plasma atomization with other methods to understand its relative advantages and limitations:
Method | Advantages | Disadvantages |
---|---|---|
Plasma Atomization | High purity, uniform particle size, excellent flowability | High cost, complex process |
Gas Atomization | Good sphericity, suitable for many metals | Lower purity, less control over particle size |
Water Atomization | Cost-effective, suitable for large-scale production | Irregular particle shapes, limited to certain metals |
Mechanical Milling | Low cost, simple process | Broad particle size distribution, contamination |
Electrolysis | High purity, precise control over composition | Limited to certain metals, slower process |
Advantages and Limitations of Different Metal Powders
Here’s a comparative look at the advantages and limitations of various metal powders produced by plasma atomization:
Metal Powder | Advantages | Limitations |
---|---|---|
Titanium (Ti) | High strength-to-weight ratio, corrosion resistance | High cost, difficult to process |
Nickel (Ni) | High melting point, excellent corrosion resistance | High cost, challenging to machine |
Stainless Steel | Corrosion resistance, good mechanical properties | Heavier than some alternatives, costlier than regular steel |
Aluminum (Al) | Lightweight, good thermal conductivity | Lower strength compared to some other metals |
Cobalt-Chromium (CoCr) | High wear resistance, biocompatibility | High cost, difficult to machine |
Copper (Cu) | Excellent electrical conductivity, antimicrobial properties | Susceptible to oxidation, relatively heavy |
Iron (Fe) | Good magnetic properties, high strength | Prone to rusting, heavy |
Magnesium (Mg) | Lightweight, good mechanical properties | Highly reactive, flammable in powdered form |
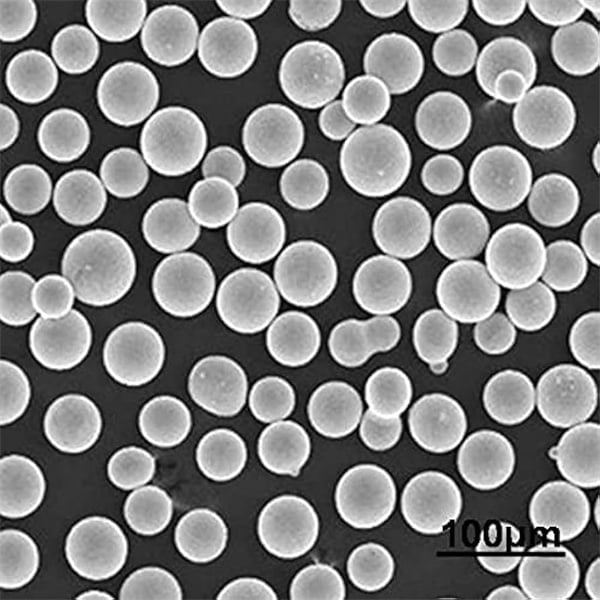
FAQ
Question | Answer |
---|---|
What is plasma atomization? | Plasma atomization is a process that uses a plasma torch to melt and atomize metal feedstock into fine powders. |
Why is plasma atomization used? | It is used to produce high-purity, spherical metal powders with uniform particle size distribution. |
What metals can be atomized using plasma? | Commonly atomized metals include titanium, nickel, stainless steel, aluminum, cobalt-chromium, copper, iron, and magnesium. |
What are the applications of plasma-atomized powders? | They are used in additive manufacturing, metal injection molding, thermal spray coatings, and various other high-tech industries. |
How does plasma atomization compare to other methods? | It offers higher purity and better particle size control but is more expensive and complex than other methods. |
Conclusion
Plasma atomization stands out as a cutting-edge technology for producing high-quality metal powders. Its ability to create uniform, pure, and spherical powders makes it indispensable for various advanced manufacturing processes. Although it comes with high costs and complexity, the benefits often outweigh these drawbacks, especially in high-performance applications.
Whether you’re involved in aerospace, biomedical, or any other industry requiring top-notch metal powders, understanding plasma atomization and its offerings can significantly impact your material choices and, ultimately, your product’s performance.
Share On
MET3DP Technology Co., LTD is a leading provider of additive manufacturing solutions headquartered in Qingdao, China. Our company specializes in 3D printing equipment and high-performance metal powders for industrial applications.
Inquiry to get best price and customized Solution for your business!
Related Articles
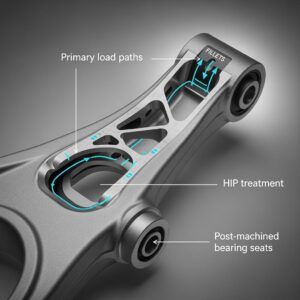
Metal 3D Printing for U.S. Automotive Lightweight Structural Brackets and Suspension Components
Read More »About Met3DP
Recent Update
Our Product
CONTACT US
Any questions? Send us message now! We’ll serve your request with a whole team after receiving your message.