plasma quality powder
Table of Contents
Imagine a world where complex metal parts are crafted not through traditional subtractive manufacturing, but through additive manufacturing, where objects are built layer by layer with incredible precision. This revolutionary technology, also known as 3D printing, relies on a crucial ingredient: plasma quality powders.
These fine, metallic granules hold the key to creating intricate structures with superior properties. But what exactly are plasma quality powders, and how do they transform industries? Buckle up, because we’re diving deep into the fascinating world of these microscopic marvels.
What are Plasma Quality Powders?
Plasma quality powders are meticulously crafted metallic particles produced through a process called plasma atomization. This technique utilizes high-intensity plasma, a superheated, ionized gas, to melt and rapidly solidify molten metal into a fine powder. Imagine a miniature, supercharged blowtorch disintegrating a stream of molten metal into a blizzard of tiny, perfectly round particles.
Key Characteristics of Plasma Quality Powders:
- Spherical Shape: Unlike irregularly shaped powders, plasma-atomized powders boast a near-perfect spherical form. This uniformity translates to superior flow characteristics, allowing for smoother and more consistent deposition during 3D printing.
- Fine Particle Size: These powders come in a range of sizes, often microns in diameter, enabling the creation of intricate features with exceptional detail.
- High Purity: Plasma atomization minimizes contamination, resulting in powders with exceptional chemical consistency, crucial for achieving desired mechanical properties in the final product.
- Tailored Properties: By tweaking the plasma atomization process, manufacturers can fine-tune the properties of the powder, such as grain size and morphology, to meet specific application requirements.
Plasma Atomization Process:
- Feedstock Preparation: The chosen metal is carefully prepared and fed into the system.
- Plasma Generation: High-temperature plasma is created using an inert gas like argon.
- Metal Melting: The molten metal stream is injected into the plasma torch.
- Atomization: The intense heat rapidly disintegrates the molten metal into a fine mist of droplets.
- Solidification: As the droplets rapidly cool, they solidify into spherical particles.
- Classification and Collection: The powder is classified by size and collected for further processing.
This intricate dance between heat, pressure, and rapid cooling yields a versatile material with the potential to revolutionize various industries.
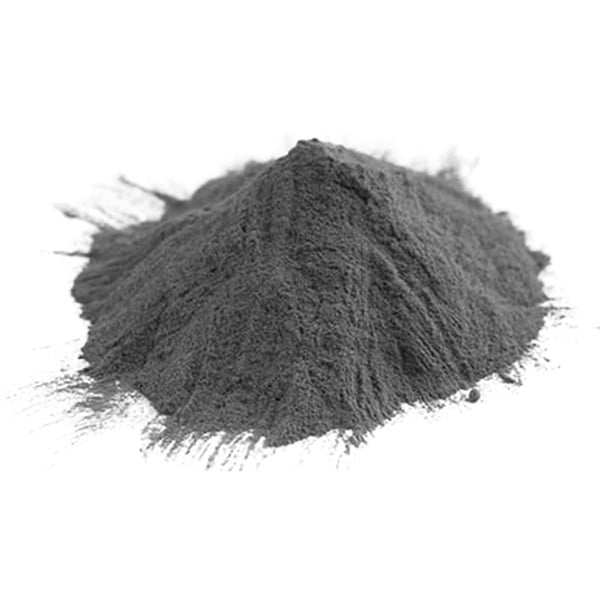
Popular Plasma Quality Powder Types
With a vast array of metals and alloys amenable to plasma atomization, the possibilities for creating unique materials are endless. Here’s a glimpse into some of the most sought-after plasma quality powder types:
1. Titanium Powders (Ti):
- Applications: Aerospace, biomedical implants, sporting goods
- Properties: Lightweight, high strength-to-weight ratio, excellent biocompatibility
- Advantages: Titanium’s low density makes it ideal for aerospace applications where weight reduction is paramount. Its exceptional biocompatibility makes it a top choice for implants like knee replacements.
- Disadvantages: Compared to some other options, titanium can be more expensive.
2. Titanium Alloys (Ti6Al4V):
- Applications: Aerospace components, prosthetics, dental implants
- Properties: Excellent strength-to-weight ratio, good corrosion resistance
- Advantages: Titanium alloys offer enhanced strength compared to pure titanium, making them suitable for demanding applications.
- Disadvantages: Slightly more complex to process compared to pure titanium, potentially impacting cost.
3. Stainless Steel Powders (316L):
- Applications: Medical devices, chemical processing equipment, marine components
- Properties: Corrosion resistant, biocompatible, good mechanical properties
- Advantages: The versatility of 316L stainless steel makes it a popular choice across various industries. Its resistance to corrosion allows it to withstand harsh environments.
- Disadvantages: Compared to lighter options like titanium, stainless steel has a higher density.
4. Nickel-based Superalloys (Inconel 625):
- Applications: Gas turbine components, rocket engines, heat exchangers
- Properties: Excellent high-temperature strength, oxidation resistance
- Advantages: Inconel 625 thrives in extreme heat environments, making it ideal for jet engines and other high-performance applications.
- Disadvantages: Nickel-based superalloys are generally more expensive than other options due to the complexity of their composition.
5. Cobalt-Chrome Alloys (CoCrMo):
- Applications: Joint replacements, dental implants, wear-resistant components
- Properties: High wear resistance, biocompatible.
6. Aluminum Powders (AlSi10Mg):
- Applications: Automotive components, aerospace structures, heat sinks
- Properties: Lightweight, good thermal conductivity, high strength-to-weight ratio (for certain alloys)
- Advantages: Aluminum’s low weight and excellent thermal properties make it attractive for applications like radiators and lightweight car parts. AlSi10Mg offers a good balance of strength and ductility.
- Disadvantages: Pure aluminum can be relatively soft. Alloying with other elements improves strength but can affect other properties.
7. Copper Powders (Cu):
- Applications: Electrical components, heat exchangers, thermal management systems
- Properties: Excellent electrical conductivity, high thermal conductivity
- Advantages: Copper’s exceptional conductivity makes it the go-to material for electrical wiring and heat sinks.
- Disadvantages: Copper can readily oxidize, requiring careful handling and storage.
8. Tungsten Powders (W):
- Applications: High-speed cutting tools, armor piercing projectiles, electrodes
- Properties: Extremely high melting point, high density, excellent wear resistance
- Advantages: Tungsten’s exceptional hardness makes it ideal for applications requiring extreme wear resistance.
- Disadvantages: Tungsten’s high brittleness necessitates careful handling and processing.
9. Nickel Powders (Ni):
- Applications: Electrical components, battery electrodes, catalysts
- Properties: Good electrical conductivity, excellent corrosion resistance, formable
- Advantages: Nickel’s versatility makes it a valuable material for various applications. Its formability allows for intricate shapes to be created.
- Disadvantages: Pure nickel may not offer the same level of strength or high-temperature performance as some alloys.
10. Molybdenum Powders (Mo):
- Applications: High-temperature components, crucibles, electronics
- Properties: High melting point, good thermal stability, good corrosion resistance
- Advantages: Molybdenum excels in high-temperature environments, making it suitable for furnace components and rocket engine parts.
- Disadvantages: Molybdenum can be susceptible to oxidation at elevated temperatures.
Choosing the Right Plasma Quality Powder
Selecting the ideal plasma quality powder hinges on the specific application’s requirements. Key factors to consider include:
- Desired Properties: What are the crucial mechanical, physical, and chemical properties needed for the final product?
- Processing Compatibility: How will the powder be used in the 3D printing process? Is the powder size and flowability suitable for the chosen technology?
- Cost Considerations: Plasma quality powders can vary significantly in price. Striking a balance between cost and desired properties is essential.
Applications of Plasma Quality Powders
The potential applications of plasma quality powders are vast and constantly evolving. Here’s a glimpse into some of the transformative ways these powders are shaping various industries:
Aerospace: Plasma quality powders are revolutionizing the aerospace industry by enabling the creation of lightweight, high-strength components for aircraft and spacecraft. Imagine 3D-printed rocket engine parts or custom-designed satellite structures – all crafted with these innovative powders.
Biomedical: The biocompatible nature of certain plasma quality powders makes them ideal for creating medical implants. From intricate joint replacements to personalized dental implants, these powders offer the potential for improved patient outcomes and custom-fit solutions.
Automotive: The automotive industry is embracing plasma quality powders to create lighter, stronger car parts. Imagine 3D-printed components that reduce weight, improve fuel efficiency, and push the boundaries of automotive design.
Consumer Goods: The potential for customized and high-performance consumer goods using plasma quality powders is immense. Think of personalized sporting equipment, lightweight and durable electronics, or even intricate jewelry pieces – all crafted layer by layer with these versatile powders.
The Future of Manufacturing:
Plasma quality powders are poised to play a pivotal role in the future of manufacturing. Their ability to create complex structures with exceptional properties opens doors to innovative designs, lighter products, and on-demand manufacturing. As 3D printing technology matures, we can expect to see even wider adoption of these transformative powders across various industries.
Plasma Quality Powders: Pros and Cons
Advantages of Plasma Quality Powders:
- Superior Material Properties: Plasma atomization yields powders with exceptional purity, controlled grain size, and near-perfect spherical shapes. This translates to enhanced mechanical properties, improved performance, and consistent results in the final product.
- Design Freedom: 3D printing with plasma quality powders allows for the creation of intricate geometries and complex internal features, previously impossible with traditional manufacturing techniques.
- Reduced Waste: Unlike subtractive manufacturing, which generates significant scrap material, 3D printing with plasma quality powders minimizes waste. This not only reduces environmental impact but also improves production efficiency.
- Mass Customization: The digital nature of 3D printing allows for easy customization of parts using plasma quality powders. This opens doors for personalized products, on-demand manufacturing, and rapid prototyping.
- Lightweighting: The ability to create complex lattice structures with plasma quality powders allows for significant weight reduction in components. This is particularly advantageous in industries like aerospace and automotive, where every gram saved translates to improved performance.
Disadvantages of Plasma Quality Powders
- Cost: Plasma atomization is a complex process, and the powders themselves can be expensive compared to traditional materials. This can be a barrier for some applications, particularly in high-volume production.
- Limited Material Selection: While the range of plasma quality powders is expanding, it’s not as vast as traditionally manufactured materials. New alloys and material compositions are continually being explored for compatibility with plasma atomization.
- Processing Challenges: Working with plasma quality powders requires specialized 3D printing equipment and expertise. The process parameters need to be carefully optimized for each powder type and desired outcome.
- Surface Finish: 3D-printed parts using plasma quality powders may require additional post-processing steps to achieve a desired surface finish. This can add time and cost to the overall production process.
Finding the Right Balance:
The decision to leverage plasma quality powders hinges on carefully weighing the advantages and disadvantages in the context of a specific application. For high-performance applications where weight reduction, design complexity, and exceptional material properties are paramount, the benefits of plasma quality powders can outweigh the initial cost considerations. As 3D printing technology matures and powder production costs become more competitive, we can expect wider adoption of these innovative materials.
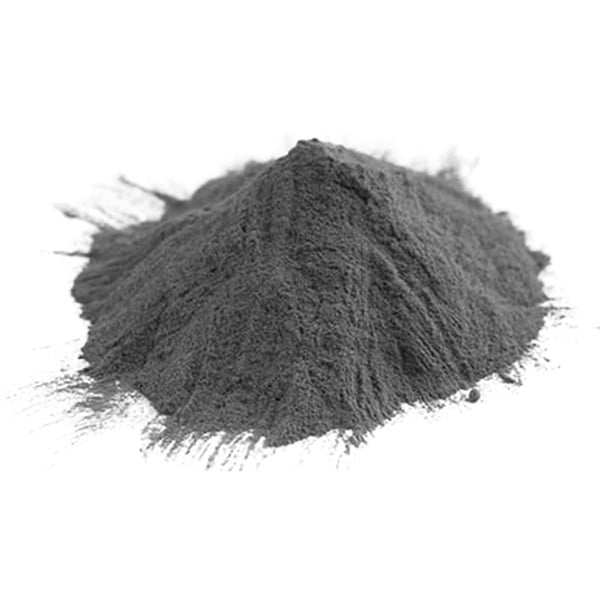
FAQ
Q: What are the different sizes of plasma quality powders available?
A: Plasma quality powders come in a range of sizes, typically measured in microns (µm). The specific size chosen depends on the desired application and the 3D printing technology being used. For instance, finer powders are better suited for creating intricate features, while larger powders may be more efficient for some printing methods.
Q: How are plasma quality powders stored?
A: Due to their susceptibility to moisture and oxidation, plasma quality powders require careful storage in controlled environments. They are typically stored in sealed containers with inert gas to prevent contamination and maintain their optimal properties.
Q: Are plasma quality powders safe to handle?
A: Certain plasma quality powders, particularly those containing reactive metals, may require specific handling precautions to avoid inhalation or skin contact. Always consult the safety data sheet (SDS) for the specific powder being used and follow recommended handling procedures.
Q: What are the future trends for plasma quality powders?
A: The future of plasma quality powders is bright. As 3D printing technology advances, we can expect to see the development of new powder compositions with even more specialized properties. Additionally, research is ongoing to improve the cost-effectiveness of plasma atomization, making these powders more accessible for a wider range of applications.
In Conclusion
Plasma quality powders are revolutionizing the way we think about manufacturing. These versatile materials offer the potential to create complex structures with exceptional properties, pushing the boundaries of design and innovation. As technology continues to evolve and costs become more competitive, plasma quality powders are poised to play a transformative role in shaping the future of various industries.
Share On
MET3DP Technology Co., LTD is a leading provider of additive manufacturing solutions headquartered in Qingdao, China. Our company specializes in 3D printing equipment and high-performance metal powders for industrial applications.
Inquiry to get best price and customized Solution for your business!
Related Articles
About Met3DP
Recent Update
Our Product
CONTACT US
Any questions? Send us message now! We’ll serve your request with a whole team after receiving your message.
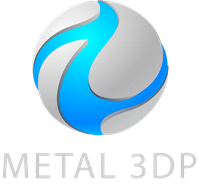
Metal Powders for 3D Printing and Additive Manufacturing