Powder Bed Fusion
Table of Contents
Overview
Powder bed fusion is an additive manufacturing process that uses thermal energy to selectively fuse regions of a powder bed layer by layer to build up parts. It is one of the most commonly used metal 3D printing technologies today for production applications.
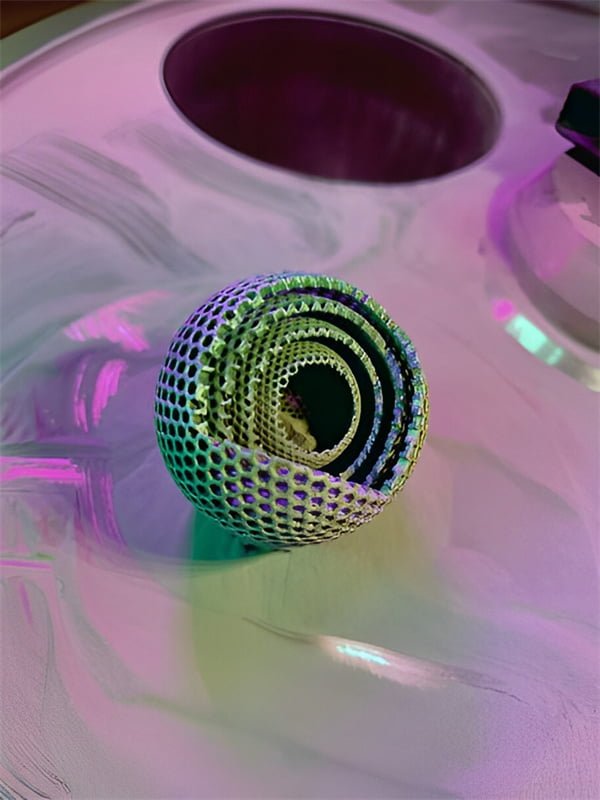
Some key details about powder bed fusion:
- It belongs to the vat photopolymerization family of additive manufacturing.
- A thermal energy source like a laser or electron beam is used to melt and fuse material powder together.
- The powders used are typically metals like stainless steel, titanium, aluminum, nickel alloys, and cobalt-chrome. Polymers and ceramics can also be used in some processes.
- Powder bed fusion can create fully dense metal parts with mechanical properties comparable to traditional manufacturing.
- It enables complex geometries not possible with conventional subtractive techniques.
- Applications span aerospace, medical, dental, automotive, and general industrial uses.
- Popular powder bed technologies include selective laser melting (SLM), direct metal laser sintering (DMLS), electron beam melting (EBM), and binder jetting.
Powder Bed Fusion Processes
There are several different powder bed fusion technologies that have been developed. The main ones are:
Process | Description |
---|---|
Selective Laser Melting (SLM) | Uses a high power laser to fully melt and fuse metallic powder in the bed. |
Direct Metal Laser Sintering (DMLS) | Similar to SLM but aimed at sintering powders vs full melting. |
Electron Beam Melting (EBM) | Uses an electron beam as energy source to melt the powder. Done in vacuum. |
Multi Jet Fusion (MJF) | Inkjet printing of a fusing agent onto a polymer powder bed before sintering with an energy source. |
Binder Jetting | Liquid binding agent selectively deposited to bind powder material followed by sintering. |
Selective laser melting (SLM) is the most common powder bed fusion technology used today. A high power laser (e.g. fiber, CO2, YAG) is focused onto a powder bed to create melt pools and fuse material. The powder bed lowers after each layer and new powder is spread over it. SLM uses full melting so fully dense parts can be built. Materials like stainless steel, titanium, aluminum, Inconel are commonly used.
Direct metal laser sintering (DMLS) operates similarly but aims to only partially melt the powder to form necks between particles to produce a solid part. DMLS has lower requirements for laser power compared to SLM.
Electron beam melting (EBM) uses an electron beam as the energy source focused under vacuum to melt the metallic powders layer by layer. EBM allows higher build rates than laser-based processes since the beam can scan faster. EBM is mostly used with titanium alloys in aerospace applications.
Multi jet fusion (MJF) uses inkjet printing heads to selectively deposit fusing agent onto a polymer powder bed which is then sintered by an energy source. MJF allows high-speed sintering of thermoplastics.
Binder jetting first deposits a liquid binding agent in selected areas to bind the powder material followed by sintering to densify the part. It can be used with metals, ceramics and polymers.
Powder Bed Fusion Materials
A range of materials can be used with powder bed fusion additive manufacturing. The most common are:
Material | Processes | Applications |
---|---|---|
Stainless steel | SLM, DMLS, Binder jetting | Medical implants, tooling, general engineering |
Titanium alloys | SLM, EBM | Aerospace and medical implants |
Aluminum alloys | SLM, EBM | Automotive and aerospace lightweighting |
Nickel superalloys | SLM, EBM | Turbine blades, rocket nozzles for extreme environments |
Cobalt-chrome | SLM, DMLS | Dental implants and prosthetics |
Polymers | MJF, Binder jetting | Prototyping and end-use plastic parts |
Ceramics | Binder jetting | Medical implants, aerospace |
The most widely used are stainless steels, which offer good corrosion resistance and mechanical properties. Titanium alloys like Ti6Al4V are popular in aerospace for weight savings over steel and nickel alloys. Aluminum alloys enable lightweight parts for automotive and aerospace.
Nickel superalloys like Inconel are used for high temperature turbine blades and rocket nozzles. Cobalt-chrome alloys are biocompatible and widely used in dental restorations. Polymers like nylons, PEEK, and polyamides can be sintered for plastic parts. Ceramics like zirconia and alumina have applications in medical implants.
The particle size distribution, flowability, packed density, and melting point are key powder material properties that determine processability and final part properties.
Powder Bed Fusion Applications
Powder bed fusion additive manufacturing is used across aerospace, medical, dental, automotive, and general engineering industries. Typical applications include:
Industry | Applications |
---|---|
Aerospace | Turbine blades, rocket nozzles, airfoils, satellites, drones |
Medical | Orthopedic and dental implants, prosthetics, surgical instruments |
Automotive | Lightweighting prototypes, custom tooling |
Industrial | Metal tooling, mining equipment, liquid handling |
Architecture | Decorative features, facades, lighting, furniture |
In aerospace, powder bed fusion is ideal for one-off components like satellites and UAVs. It is used for lightweight titanium and nickel alloy parts including turbines, nozzles, airframes.
For medical, customized titanium and cobalt chrome implants and prosthetics are a major application area. It also enables personalized surgical tools.
In automotive, powder bed is used for lightweight prototypes and custom tooling and fixtures like jigs. For industrial equipment, it enables specialized tooling, jigs, and end-use metal parts.
In architecture, powder bed fusion facilitates unique geometries for decorative and functional elements in buildings and furniture.
Advantages of Powder Bed Fusion
Some key advantages of powder bed fusion technologies include:
- Complex geometries – intricate internal features and lattices are possible.
- Customization – parts can be tailored to fit individual applications.
- Lightweighting – reducing component weight by optimizing designs.
- Consolidation – combining assemblies into single parts.
- High strength – fully dense metals comparable to wrought material strength.
- Shorter lead times – rapid turnaround from digital file to part.
- Mass customization – combining economies of scale with part customization.
- Sustainability – less waste compared to subtractive processes.
The ability to produce dense metal parts with custom complex geometries makes powder bed fusion ideal for lightweight, high performance components across industries. The technology enables consolidation of assemblies into single parts, reducing manufacturing and inventory costs. The use of additive manufacturing also results in significantly less material waste than traditional subtractive methods like CNC machining.
Limitations of Powder Bed Fusion
Some current limitations include:
- Size constraints – build volumes are typically less than 1 cubic meter.
- Surface finish – stair-stepping effect requiring post-processing.
- Build speed – slower than high volume manufacturing methods.
- Anisotropic properties – directional variations in material properties.
- Standards – lack of codes and specifications for qualifying parts.
- Software – design rules and file preparation complexities.
- Costs – equipment and material costs still relatively high.
The maximum component size is restricted by the build volume of the machines, which is improving but still usually less than 1 cubic meter. The layer-by-layer process can result in poor surface finish that requires smoothing and polishing.
Overall build speeds are slower compared high volume production technologies like injection molding. Parts can also exhibit anisotropic properties depending on build orientation. Lack of standards and specifications for qualifying printed parts is also a constraint across heavily regulated industries like aerospace and medical. Designing optimal parts and preprocessing files requires advanced software expertise.
System and material costs are still relatively high compared to traditional manufacturing. However, costs are lowering with increased adoption and many applications can justify the costs due to part performance, customization, and design flexibility.
Post-Processing
Post-processing refers to the steps required after the build process to yield a finished part:
- Powder removal – Parts are separated from unmelted powder using brushes.
- Supports removal – Support structures are cut off and surface cleaned.
- Surface finishing – Sanding, grinding, bead blasting to improve
Process Parameters
There are several key process parameters that can be tuned to optimize properties, performance, and productivity with powder bed fusion:
Parameter | Typical Range | Effect |
---|---|---|
Laser power | 50-500W | Melting rate, melt pool size, depth penetration |
Scan speed | 100-10,000 mm/s | Solidification rate, cooling rate, microstructure |
Hatch spacing | 50-200 μm | Overlapping tracks, density, bond strength |
Layer thickness | 20-100 μm | Resolution, surface roughness, build time |
Scanning strategy | Islands, stripes, chessboard | Residual stresses, distortion, anisotropy |
Process atmosphere | Vacuum, inert gas | Oxidation, contamination, porosity |
Laser power affects the energy input, melting rate, melt pool dimensions and depth penetration. Scan speed controls the solidification rate and cooling rate which influences grain morphology and defect formation.
Hatch spacing sets the spacing betweenscan tracks and affects overlapping, densification, and bonding between layers. Layer thickness determines the resolution, surface roughness and total build time.
Scanning strategy (scan patterns) affects residual stresses, distortion, and anisotropic properties based on print direction. Process atmosphere determines levels of oxidation and contamination.
Powder Recycling
- Unfused powder can be harvested and sieved to remove large particles
- Reused for up to 20 cycles typically
- Reduces powder costs significantly
- Fresh powder added to replenish and maintain chemistry
- Properties monitored for reuse thresholds
Powder bed fusion processes reuse unfused powder for additional builds. After depowdering, the loose powder is harvested, sieved to remove large particles, and blended with fresh powder before reusing.
Typical reuse rates are up to 20 cycles depending on material, particle size changes, and contamination levels. This recycling greatly improves material efficiency and lowers overall part costs. The reused powder ratio and properties are monitored to determine refresh rates.
Quality Control
Some key quality control measures used with powder bed fusion include:
- Chemical analysis of powders
- Particle size distribution analysis
- Powder reuse tracking
- Melt pool monitoring
- Part geometry inspection
- Mechanical property testing
- Non-destructive testing (e.g. X-ray)
- CT scanning for internal defects
- Surface roughness measurement
Input powder chemistry and particle size distribution are analyzed to ensure high quality. Powder refresh rates are tracked. In-process monitoring systems like melt pool monitoring detect defects during builds.
Printed parts are measured for geometric tolerances. Mechanical testing assesses properties based on process parameters and build orientation. Non-destructive and CT scanning identifies internal flaws. Surface finishing is evaluated. All data is analyzed to calibrate and optimize processes.
Cost Analysis
Typical powder bed fusion part costs depend on:
- Machine depreciation
- Material costs
- Labor for preprocessing and postprocessing
- Build time and energy consumption
- Amount of reusable powder
- Buy-to-fly ratio
Machine equipment costs are amortized over expected lifetime based on usage. Material costs are calculated based on part volume and buy-to-fly ratio. Labor includes file preparation, setup, depowdering, and finishing steps.
Energy usage depends on build time and power levels. Reusable powder lowers overall material costs. Buy-to-fly ratios of 3:1 up to 20:1 are common for high value parts.
Suppliers
Some of the major powder bed fusion system suppliers include:
Supplier | Key Technology |
---|---|
EOS | DMLS (Direct Metal Laser Sintering) |
3D Systems | DMP (Direct Metal Printing) |
GE Additive | DMLM (Direct Metal Laser Melting) |
Trumpf | TruPrint metal 3D printers |
Sisma | Laser metal fusion systems |
AddUp | FormUp metal 3D printers |
EOS and 3D Systems were early pioneers in powder bed fusion and remain leaders today. GE Additive acquired Concept Laser and Arcam EBM to offer both laser and electron beam technologies. Trumpf and Sisma also provide industrial SLM systems. AddUp is a joint venture between Michelin and Fives focusing on metal additive manufacturing.
There are also many suppliers of materials for powder bed fusion, including Carpenter, Sandvik, Praxair, LPW Technology, and AP&C.
Cost Comparison
Process | Equipment Cost | Material Cost | Speed |
---|---|---|---|
Powder bed fusion | $100K – $1M+ | $100-500/kg | 5-100 cm3/hr |
CNC machining | $50K – $500K | $5-50/kg | 50-500 cm3/hr |
Injection molding | $100K – $1M+ | $2-5/kg | 100-1000 cm3/hr |
Powder bed systems have high equipment costs from $100,000 for industrial printers up to over $1 million for large production systems. Materials range from $100-500/kg. Production speeds vary from 5-100 cm3/hr depending on the technology.
CNC machining has lower equipment costs starting around $50,000. Metal material costs are cheaper at $5-50/kg. Speeds range 50-500 cm3/hr.
Injection molding systems also cost over $100,000. But plastic material is very cheap at $2-5/kg. Speeds are 100-1000 cm3/hr.
So powder bed fusion is only cost effective for lower volume, high value metal parts where performance merits the higher costs.
Powder Bed Fusion vs. Binder Jetting
Powder Bed Fusion | Binder Jetting | |
---|---|---|
Materials | Metals, polymers, ceramics | Metals, polymers, ceramics |
Density | Fully dense parts | Porous parts, infiltration needed |
Accuracy | Medium, ±0.1% with postprocessing | Medium, ±0.2% |
Surface Finish | Moderate, requires finishing | Fair, layered texture remains |
Speed | Slow, depends on energy source | Fast, independent of energy source |
Applications | End-use metal parts | Tooling, casting patterns, prototypes |
- Powder bed fusion can produce fully dense parts while binder jetting parts are porous and require infiltration.
- Binder jetting accuracy is moderate while powder bed fusion can achieve higher accuracies with post-processing.
- Powder bed fusion surface finish requires finishing while binder jetting has a layered, textured finish.
- Binder jetting build speeds are much faster than powder bed processes limited by energy source.
- Powder bed is used more for end-use parts while binder jetting is better for tooling, casting, and concept models.
Powder Bed Fusion vs. Directed Energy Deposition
Powder Bed Fusion | DED | |
---|---|---|
Materials | Primarily metals | Metals, polymers |
Geometry | Complexity enabled | Medium complexity |
Accuracy | Medium to high | Medium |
Surface Finish | Moderate, requires finishing | Rough, more finishing |
Scalability | Small to medium parts | Medium to large parts |
Deposition rate | Low, depends on scan speed | High, increased with larger nozzles |
- Powder bed fusion is mostly used with metals while DED can use metals and polymers.
- Powder bed fusion allows higher complexity than DED which has some geometric constraints.
- Accuracy is higher with powder bed fusion. DED accuracy is medium.
- DED creates rough surfaces requiring more finishing due to additive beads.
- Powder bed fusion builds smaller parts while DED does medium to large near-net shapes.
- DED has much higher deposition rates due to its blown powder approach.
So powder bed fusion generally produces smaller, complex geometries at moderate speeds. DED makes larger simple shapes much faster but with more finishing work.
The Future of Powder Bed Fusion
Some areas of future development for powder bed fusion include:
- Larger build volumes up to several cubic meters
- Faster scanning methods to increase build speeds
- Expanding materials like high temperature alloys, MMCs, polymers
- Hybrid manufacturing integrating powder bed fusion and CNC
- Automated depowdering and postprocessing
- Advanced real-time monitoring and control
- More rigorous qualification and certification procedures
Larger build platforms will enable bigger parts or higher production throughput. New faster scanning technologies can drastically increase build speeds. The material options will continue expanding especially into high performance alloys.
Share On
MET3DP Technology Co., LTD is a leading provider of additive manufacturing solutions headquartered in Qingdao, China. Our company specializes in 3D printing equipment and high-performance metal powders for industrial applications.
Inquiry to get best price and customized Solution for your business!
Related Articles
About Met3DP
Recent Update
Our Product
CONTACT US
Any questions? Send us message now! We’ll serve your request with a whole team after receiving your message.
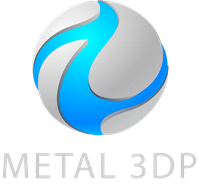
Metal Powders for 3D Printing and Additive Manufacturing