powder for multi-laser printing
Table of Contents
Multi-laser printing, a revolutionary additive manufacturing (AM) technique, has captured the imagination of engineers and designers alike. Imagine creating complex objects layer-by-layer using beams of light and a unique material – powder. But what kind of powder exactly? Buckle up, because we’re about to delve into the fascinating world of powders specifically designed for multi-laser printing.
Composition and Properties of powder for multi-laser printing
Compositional Delights:
Unlike your average beach sand, powders for multi-laser printing are meticulously crafted from various metals. Here’s a sneak peek at some of the most popular players:
- Stainless Steel Powders (316L, 17-4PH): These versatile workhorses offer excellent corrosion resistance, making them ideal for applications like medical implants and marine components.
- Titanium Powders (Ti-6Al-4V, Grade 2): Renowned for their high strength-to-weight ratio and biocompatibility, titanium powders are perfect for aerospace parts and prosthetics.
- Nickel-based Alloy Powders (Inconel 625, Inconel 718): These champions boast exceptional heat resistance and resistance to harsh environments, making them prime candidates for jet engine components and chemical processing equipment.
- Aluminum Powders (AlSi10Mg, AlSi7Mg0.3): Lightweight and readily available, aluminum powders are popular for prototyping and applications where weight reduction is crucial.
- Cobalt Chrome Powders (CoCrMo): Offering a unique combination of strength, wear resistance, and biocompatibility, cobalt chrome powders shine in the production of joint replacements and cutting tools.
A Symphony of Properties:
The magic of these powders lies not just in their composition, but also in their meticulously controlled properties:
- Particle Size and Distribution: Uniform, spherical particles are crucial for smooth powder flow and optimal laser interaction during the printing process. Imagine tiny marbles versus a bag of pebbles – you want a smooth flow!
- Flowability: The ability of the powder to flow freely is essential for even layer deposition. Think of pouring sand versus flour – the smoother, the better for multi-laser printing.
- Meltability: Powders need to melt readily at the laser’s heat to form a strong bond with the underlying layer. Picture butter melting on a hot pan – that’s the kind of meltability we’re looking for.
- Sinterability: The ability of the melted powder particles to fuse together during the printing process, creating a solid and robust object. Imagine tiny grains of sand sticking together to form a strong castle – that’s the essence of sinterability.
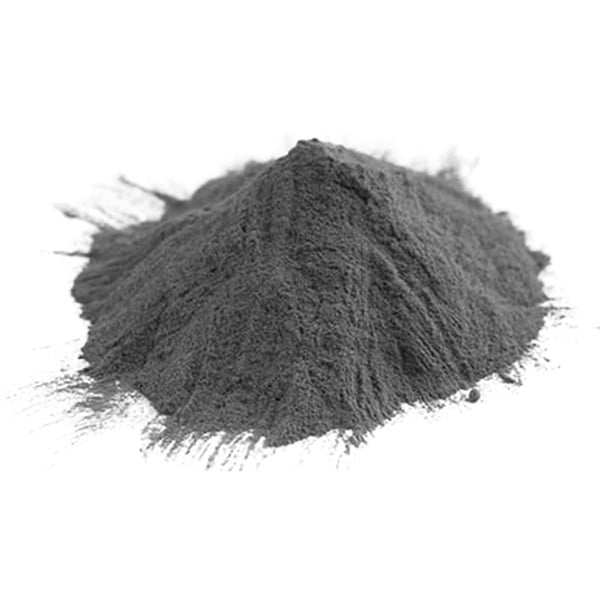
10 Metal Powder Models
The world of multi-laser printing powders boasts a diverse cast of characters. Here are 10 specific models to whet your appetite:
Metal Powder Model | Composition | Key Properties | Applications |
---|---|---|---|
Höganäs AM 316L | Stainless Steel 316L | High corrosion resistance, good ductility | Medical implants, marine components |
EOS Titanium Ti64 | Titanium Ti-6Al-4V | High strength-to-weight ratio, biocompatible | Aerospace parts, prosthetics |
SLM Solutions Inconel 625 | Nickel-based alloy | Exceptional heat resistance, corrosion resistant | Jet engine components, chemical processing equipment |
ExOne AlSi10Mg | Aluminum alloy | Lightweight, good machinability | Prototyping, automotive components |
Carpenter Additive Manufacturing Cobalt Chrome (CoCrMo) | Cobalt chrome alloy | High strength, wear resistance, biocompatible | Joint replacements, cutting tools |
LPW PM2000 | Stainless Steel 17-4PH | High strength, good ductility at high temperatures | Automotive parts, molds and dies |
AMPro Metal Powder | Titanium Grade 2 | Excellent biocompatibility, good strength | Dental implants, surgical instruments |
Matermind AlSi7Mg0.3 | Aluminum alloy | Lightweight, good corrosion resistance | Electronic enclosures, heat sinks |
Renishaw Invar 36 | Nickel-iron alloy | Low thermal expansion coefficient | Optical components, precision instruments |
Sandvik Osprey Hastelloy C-276 | Nickel-molybdenum-chromium alloy | Exceptional corrosion resistance at high temperatures | Chemical processing equipment, heat exchangers |
Please note: This table is not exhaustive, and new powder models are constantly being developed.
Applications of Powders in Multi-Laser Printing
Powders for multi-laser printing aren’t just fancy dust – they’re the building blocks for a revolution in manufacturing. Let’s explore the diverse applications where these powders shine:
- Aerospace and Defense: The need for lightweight, high-strength components is paramount in the aerospace industry. Titanium and aluminum powders are used to create intricate aircraft parts, missile components, and even spacecraft structures. Their ability to withstand extreme temperatures and stresses makes them ideal for these demanding applications.
- Medical Implants: The biocompatible nature of certain powders, like titanium and cobalt chrome, has opened doors for creating customized prosthetics, joint replacements, and even dental implants. These printed implants offer a perfect fit for individual patients, leading to faster recovery times and improved quality of life.
- Automotive Industry: The quest for lighter, more fuel-efficient vehicles is driving the use of aluminum powders in multi-laser printing. Prototypes of car parts, complex engine components, and even lightweight wheels can be produced with incredible accuracy and detail.
- Consumer Goods: From customized bike frames to intricate jewelry designs, multi-laser printing with powders is making its way into the consumer market. Imagine designing and printing your own phone case or a one-of-a-kind camera lens mount – the possibilities are endless!
- Tooling and Molds: Creating complex molds and dies traditionally involves intricate machining processes. Multi-laser printing with powders like stainless steel allows for the creation of these tools with intricate channels and shapes, saving time and money in the production process.
- Energy Sector: Components for heat exchangers, reactors, and other demanding applications in the energy sector can be produced using powders with exceptional heat resistance and corrosion resistance, like Inconel and Hastelloy.
Beyond these examples, the potential applications of powders in multi-laser printing are constantly expanding. As technology advances and new powder formulations are developed, we can expect to see even more innovative and groundbreaking applications emerge.
Advantages and Disadvantages of Powders for Multi-Laser Printing
Like any technology, powders for multi-laser printing come with their own set of pros and cons. Let’s take a balanced look:
Advantages:
- Design Freedom: Multi-laser printing allows for the creation of complex geometries that are impossible with traditional manufacturing techniques. Imagine designing a part with internal channels or intricate lattice structures – this becomes a reality with powders.
- Lightweighting: Certain powders, like aluminum and titanium, enable the creation of lightweight components, crucial for applications in aerospace, automotive, and other weight-sensitive industries.
- Customization: Powders can be tailored to meet specific needs. For instance, adding specific elements to a metal powder can enhance its strength, corrosion resistance, or biocompatibility.
- Rapid Prototyping: Multi-laser printing with powders allows for the creation of functional prototypes quickly and efficiently, accelerating the design and development process.
- Reduced Waste: Compared to traditional manufacturing techniques that involve machining away material, multi-laser printing with powders generates minimal waste, making it a more sustainable option.
Disadvantages:
- Cost: The technology and materials involved in multi-laser printing with powders can be expensive. Setting up and maintaining a printing system requires significant investment.
- Surface Finish: The surface finish of parts printed with powders can be rough compared to those produced with traditional techniques. Additional post-processing steps might be needed to achieve a desired finish.
- Material Limitations: While the range of powders available is growing, there are still limitations in terms of the materials that can be effectively used in multi-laser printing.
- Limited Production Volume: Currently, multi-laser printing with powders is better suited for producing small batches or prototypes rather than high-volume production runs.
- Safety Concerns: Handling metal powders can pose health risks, and proper safety protocols need to be followed when working with this technology.
It’s important to weigh the advantages and disadvantages of powders for multi-laser printing carefully to determine if this technology is the right fit for your specific application.
Characteristics of powder for multi-laser printing
Before diving into the nitty-gritty of choosing the perfect powder, let’s explore the key specifications that define a powder’s suitability for multi-laser printing:
- Particle Size and Distribution: As mentioned earlier, uniform, spherical particles are crucial. Ideally, the particle size distribution should be narrow, with most particles falling within a specific size range. This ensures even powder flow, optimal laser interaction, and a smooth surface finish in the final printed part. Imagine using ball bearings versus a mix of pebbles and sand – the ball bearings (uniform particles) will flow smoothly and create a more consistent result.
Here’s a table outlining typical particle size ranges for different multi-laser printing applications:
Application | Typical Particle Size Range (μm) |
---|---|
Aerospace and Defense | 15-45 |
Medical Implants | 20-50 |
Automotive | 40-70 |
Consumer Goods | 25-60 |
Tooling and Molds | 30-60 |
- Flowability: The ability of the powder to flow freely is essential for even layer deposition during the printing process. Powders with good flowability spread evenly across the build platform, ensuring consistent density and minimal defects in the final part. Imagine pouring flour versus wet sand – the flour will flow smoothly, leading to a uniform layer.
- Apparent Density: This refers to the weight of powder per unit volume, taking into account the air spaces between the particles. A higher apparent density generally translates to better packing efficiency and potentially faster printing speeds.
- Laser Absorbency: The powder needs to absorb the laser’s energy efficiently to melt properly and form strong bonds with adjacent layers. The specific laser wavelength used in the printing system plays a role in determining the optimal laser absorbency of the powder.
- Sinterability: As mentioned before, the ability of the melted powder particles to fuse together during printing is crucial. Good sinterability ensures a strong and robust final part.
Additionally, powder suppliers often provide specifications like:
- Chemical Composition: The exact breakdown of elements present in the powder, ensuring it meets the desired material properties.
- Moisture Content: Excess moisture can negatively impact flowability and laser interaction. Powders are typically stored and handled in controlled environments to minimize moisture absorption.
- Oxygen Content: For certain materials like titanium, oxygen content needs to be tightly controlled to avoid defects in the final part.
Understanding these specifications empowers you to make informed decisions when selecting the right powder for your multi-laser printing project.
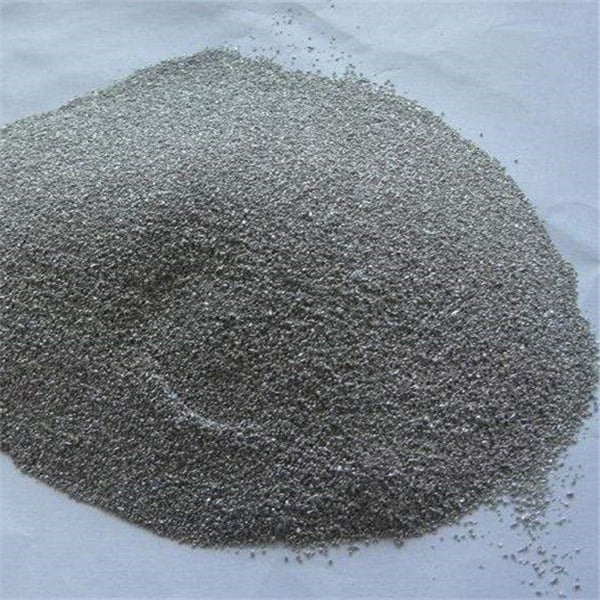
Suppliers and Pricing of powder for multi-laser printing
The world of multi-laser printing powders boasts a diverse range of suppliers, each with its own specialties and pricing structures. Here’s a glimpse into this landscape:
- Höganäs: A leading global supplier of metal powders, Höganäs offers a wide range of powders for multi-laser printing applications, including stainless steel, tool steels, and nickel alloys.
- EOS GmbH: This German multinational not only manufactures multi-laser printing systems but also offers a range of high-quality metal powders specifically optimized for their machines.
- SLM Solutions GmbH: Another major player in the multi-laser printing market, SLM Solutions offers metal powders tailored to their printing systems, ensuring optimal performance.
- ExOne: An American company known for its binder jetting additive manufacturing technology, ExOne also offers metal powders compatible with various multi-laser printing systems.
- Carpenter Additive Manufacturing: A subsidiary of Carpenter Technology Corporation, this company focuses on specialty alloys and offers metal powders for demanding applications.
Pricing for multi-laser printing powders can vary significantly depending on several factors:
- Material: Exotic materials like titanium or nickel alloys generally come with a higher price tag compared to common stainless steel powders.
- Quantity: Bulk purchases typically offer lower prices per kilogram compared to smaller quantities.
- Particle size and distribution: Powders with tighter particle size control might command a premium price.
- Supplier: Different suppliers may have varying pricing structures based on their production costs and market positioning.
It’s recommended to contact several suppliers and request quotes to get a competitive picture of powder pricing.
Comparing Powder Options
With a plethora of metal powders vying for your attention, choosing the right one can feel overwhelming. Here’s where a side-by-side comparison comes in handy:
Metal Powder Showdown: Stainless Steel Powders (316L & 17-4PH)
These two stainless steel workhorses are popular choices for multi-laser printing, but they have distinct characteristics:
Feature | 316L Stainless Steel | 17-4PH Stainless Steel |
---|---|---|
Composition | Chromium-nickel molybdenum alloy | Chromium-copper-niobium alloy |
Key Properties | Excellent corrosion resistance, good ductility | High strength, good ductility at high temperatures |
Applications | Medical implants, marine components | Automotive parts, molds and dies |
Advantages | Biocompatible, resists harsh environments | Offers good strength and toughness even at elevated temperatures |
Disadvantages | Lower strength compared to some other options | Slightly lower corrosion resistance compared to 316L |
Cost | Generally less expensive than some other metal powders | Can be slightly more expensive than 316L |
The Verdict:
316L shines when corrosion resistance is paramount, making it ideal for medical implants and marine components. 17-4PH steps up when high strength at elevated temperatures is needed, perfect for applications like automotive parts and molds.
Metal Marvels: Titanium Powders (Ti-6Al-4V & Grade 2)
Titanium powders are renowned for their strength-to-weight ratio and biocompatibility:
Feature | Ti-6Al-4V Titanium | Grade 2 Titanium |
---|---|---|
Composition | Titanium alloy with aluminum and vanadium | Pure titanium |
Key Properties | High strength-to-weight ratio, biocompatible | Excellent biocompatibility, good strength |
Applications | Aerospace parts, prosthetics | Dental implants, surgical instruments |
Advantages | Lightweight, strong, good for high-stress applications | Biocompatible, ideal for applications requiring close contact with bone |
Disadvantages | Relatively expensive | Lower strength compared to Ti-6Al-4V |
Cost | One of the more expensive metal powders | Generally less expensive than Ti-6Al-4V |
The Verdict:
Ti-6Al-4V takes the crown for applications demanding exceptional strength-to-weight ratio, making it a favorite in the aerospace industry. Grade 2 titanium reigns supreme when biocompatibility is the top priority, ideal for medical implants.
Remember, this is just a glimpse into the vast world of metal powders for multi-laser printing. New materials and formulations are constantly emerging, offering even more possibilities for creating groundbreaking applications.
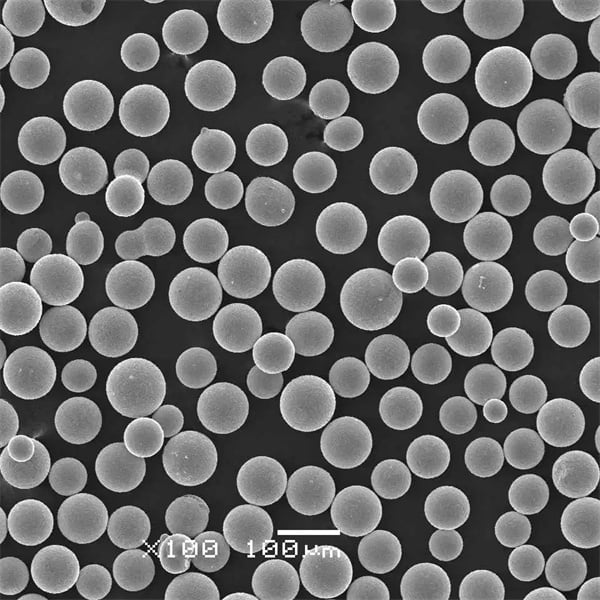
FAQs
Let’s address some frequently asked questions to solidify your understanding of powders for multi-laser printing:
1: Is multi-laser printing with powders safe?
The safety of multi-laser printing with powders depends on the specific material being used. Some metal powders can pose health risks if inhaled, so proper safety protocols need to be followed. This includes wearing appropriate personal protective equipment (PPE) such as respirators and gloves when handling powders. Additionally, it’s crucial to have proper ventilation systems in place to minimize exposure to airborne particles.
2: How strong are parts printed with multi-laser printing powders?
The strength of parts printed with multi-laser printing powders depends on the chosen material and the printing process parameters. Generally, metal powders can produce parts with excellent strength properties comparable to traditionally manufactured components.
3: What is the future of powders for multi-laser printing?
The future of powders for multi-laser printing is bright! Researchers are constantly developing new powder formulations with improved properties, like increased strength, enhanced conductivity, or even the ability to change color. Additionally, advancements in multi-laser printing technology will lead to faster printing speeds and better surface finishes, making this technology even more attractive for a wider range of applications.
Share On
MET3DP Technology Co., LTD is a leading provider of additive manufacturing solutions headquartered in Qingdao, China. Our company specializes in 3D printing equipment and high-performance metal powders for industrial applications.
Inquiry to get best price and customized Solution for your business!
Related Articles
About Met3DP
Recent Update
Our Product
CONTACT US
Any questions? Send us message now! We’ll serve your request with a whole team after receiving your message.
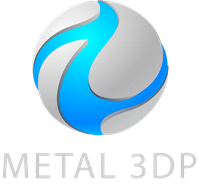
Metal Powders for 3D Printing and Additive Manufacturing