Powder Making Device
Table of Contents
If you’re diving into the world of powder making devices, you’re in the right place. Whether you’re a hobbyist or a professional, understanding these devices’ intricacies can be a game-changer. Let’s explore everything you need to know about powder making devices, from types and specifications to applications and comparisons.
Overview of Powder Making Devices
Powder making devices are specialized machines designed to convert solid materials into fine powders. These devices are crucial in various industries, including metallurgy, pharmaceuticals, cosmetics, and food processing. They offer precise control over particle size and distribution, enhancing the efficiency and quality of the final product.
Key Features:
- Versatility: Suitable for various materials.
- Precision: Control over particle size.
- Efficiency: High throughput and energy-efficient.
- Customization: Different models for specific needs.
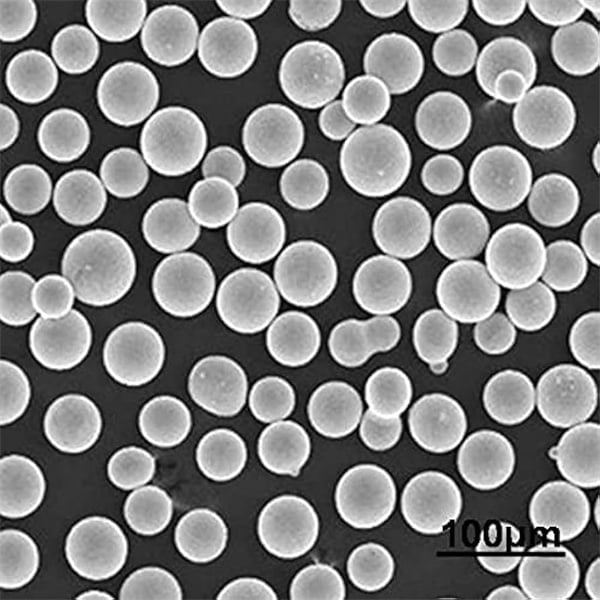
Types of Powder Making Devices
1. Ball Mills
Ball mills are cylindrical devices used to grind materials into fine powders through a rotating mechanism that uses balls to crush the material.
2. Jet Mills
Jet mills utilize high-velocity jets of gas to pulverize materials into micron-sized particles.
3. Hammer Mills
Hammer mills use rotating hammers to crush materials into fine powders.
4. Attrition Mills
Attrition mills operate based on the principle of grinding materials between two surfaces.
5. Fluid Energy Mills
Fluid energy mills, also known as micronizers, use high-speed gas streams to achieve particle reduction.
6. Planetary Ball Mills
Planetary ball mills are advanced versions of ball mills, offering higher energy impact and finer particle size control.
7. Vibration Mills
Vibration mills use vibrational energy to achieve grinding and milling.
8. Cryogenic Mills
Cryogenic mills cool materials to extremely low temperatures to facilitate grinding.
9. Disc Mills
Disc mills use rotating discs to grind materials into fine powders.
10. Pin Mills
Pin mills utilize pins to achieve fine particle size reduction.
Detailed Descriptions of Specific Metal Powder Models
Model 1: NanoGrind 2000
Type: Ball Mill
Composition: Stainless Steel
Properties: Produces ultra-fine powders with uniform particle distribution
Characteristics: High energy impact, programmable grinding time
Applications: Nanomaterials, pharmaceuticals, research labs
Model 2: MicroJet 150
Type: Jet Mill
Composition: Tungsten Carbide
Properties: Achieves particle sizes down to a few microns
Characteristics: High-speed gas streams, adjustable pressure
Applications: Pharmaceuticals, cosmetics, fine chemicals
Model 3: TurboMill 500
Type: Hammer Mill
Composition: High-Carbon Steel
Properties: Efficient for hard and brittle materials
Characteristics: Rotating hammers, adjustable screen size
Applications: Food processing, recycling, biomass
Model 4: Attritor 450
Type: Attrition Mill
Composition: Hardened Steel
Properties: Fine particle size with consistent distribution
Characteristics: Grinding between two surfaces, energy-efficient
Applications: Paints, coatings, ceramics
Model 5: Micronizer X100
Type: Fluid Energy Mill
Composition: Stainless Steel
Properties: Produces fine powders with minimal contamination
Characteristics: High-speed gas streams, fine control over particle size
Applications: Pharmaceuticals, pigments, industrial minerals
Model 6: PlanetMiller 6000
Type: Planetary Ball Mill
Composition: Alloy Steel
Properties: Produces nanoscale powders
Characteristics: High energy impact, multi-directional movement
Applications: Nanotechnology, advanced materials, research
Model 7: VibroGrind 350
Type: Vibration Mill
Composition: Hardened Steel
Properties: Efficient for medium-hard materials
Characteristics: Vibrational energy, low energy consumption
Applications: Mineral processing, metallurgy, ceramics
Model 8: CryoMiller 900
Type: Cryogenic Mill
Composition: Cryogenic-Grade Steel
Properties: Efficient at low temperatures, prevents thermal degradation
Characteristics: Uses liquid nitrogen, ultra-fine grinding
Applications: Biological samples, plastics, rubber
Model 9: DiscMill 200
Type: Disc Mill
Composition: High-Carbon Steel
Properties: Produces fine powders with minimal energy
Characteristics: Rotating discs, adjustable gap
Applications: Agriculture, food industry, chemical processing
Model 10: PinCrusher 300
Type: Pin Mill
Composition: Tungsten Carbide
Properties: Fine and consistent particle size
Characteristics: High-speed rotating pins, easy to clean
Applications: Pharmaceuticals, food additives, chemicals
Applications of Powder Making Devices
Industrial Applications
Powder making devices are indispensable in industries like metallurgy, where they’re used to produce metal powders for additive manufacturing and sintering processes.
Pharmaceutical Applications
In the pharmaceutical industry, these devices ensure the production of fine, uniform powders essential for drug formulation and delivery.
Food Processing Applications
Food processors use these devices to produce fine powders of spices, flours, and other food ingredients, enhancing texture and flavor.
Cosmetic Applications
In cosmetics, powder making devices help create fine powders for products like makeup and skincare, ensuring smooth application and consistency.
Specifications of Powder Making Devices
Model | Type | Material | Particle Size | Capacity | Power Consumption | Applications |
---|---|---|---|---|---|---|
NanoGrind 2000 | Ball Mill | Stainless Steel | Nano-scale | 5 kg/hr | 3 kW | Nanomaterials, Pharma |
MicroJet 150 | Jet Mill | Tungsten Carbide | Micron-scale | 10 kg/hr | 5 kW | Pharma, Cosmetics |
TurboMill 500 | Hammer Mill | High-Carbon Steel | Fine | 20 kg/hr | 7 kW | Food, Recycling, Biomass |
Attritor 450 | Attrition Mill | Hardened Steel | Fine | 8 kg/hr | 4 kW | Paints, Coatings, Ceramics |
Micronizer X100 | Fluid Energy Mill | Stainless Steel | Ultra-fine | 15 kg/hr | 6 kW | Pharma, Pigments |
PlanetMiller 6000 | Planetary Ball Mill | Alloy Steel | Nano-scale | 3 kg/hr | 2.5 kW | Nanotechnology, Research |
VibroGrind 350 | Vibration Mill | Hardened Steel | Medium-fine | 12 kg/hr | 4.5 kW | Mineral Processing, Ceramics |
CryoMiller 900 | Cryogenic Mill | Cryogenic-Grade Steel | Ultra-fine | 4 kg/hr | 5 kW | Biological, Plastics |
DiscMill 200 | Disc Mill | High-Carbon Steel | Fine | 25 kg/hr | 6 kW | Agriculture, Food |
PinCrusher 300 | Pin Mill | Tungsten Carbide | Fine | 10 kg/hr | 5.5 kW | Pharma, Food, Chemicals |
Suppliers and Pricing Details
Supplier | Model | Price Range | Location | Contact |
---|---|---|---|---|
PowderTech Inc. | NanoGrind 2000 | $20,000 – $30,000 | USA | [email protected] |
JetMills Ltd. | MicroJet 150 | $15,000 – $25,000 | UK | [email protected] |
HammerMills Corp. | TurboMill 500 | $10,000 – $18,000 | Germany | [email protected] |
AttritionWorks | Attritor 450 | $12,000 – $20,000 | Canada | [email protected] |
Micronizer Solutions | Micronizer X100 | $18,000 – $28,000 | Japan | [email protected] |
PlanetaryMills | PlanetMiller 6000 | $25,000 – $35,000 | USA | [email protected] |
VibroTech | VibroGrind 350 | $14,000 – $22,000 | South Korea | [email protected] |
CryoMills Inc. | CryoMiller 900 | $22,000 – $32,000 | USA | [email protected] |
DiscMills Ltd. | DiscMill 200 | $8,000 – $15,000 | UK | [email protected] |
PinMill Technologies | PinCrusher 300 | $16,000 – $24,000 | China | [email protected] |
Comparing Pros and Cons
Advantages of Powder Making Devices:
- Precision:Achieve uniform particle size.
- Versatility: Suitable for various materials.
- Efficiency: High throughput with minimal waste.
- Customization: Models for specific industry needs.
Disadvantages of Powder Making Devices:
- Cost: High initial investment.
- Maintenance: Regular maintenance required.
- Complexity: Requires skilled operators.
- Energy Consumption: Can be energy-intensive.
Applications and Uses
Industry | Application | Benefits |
---|---|---|
Metallurgy | Metal powder production | Improved material properties |
Pharmaceuticals | Drug formulation | Consistent dosage and efficacy |
Food Processing | Spice and flour production | Enhanced flavor and texture |
Cosmetics | Makeup and skincare product formulation | Smooth application and consistency |
Chemicals | Fine chemical production | Increased reactivity and purity |
Nanotechnology | Nanomaterials synthesis | Advanced material properties |
Research Labs | Experimental material preparation | Precise control over variables |
Recycling | Material reclamation and reuse | Sustainable practices |
Comparative Analysis
Parameter | Ball Mill | Jet Mill | Hammer Mill | Attrition Mill |
---|---|---|---|---|
Precision | High | Very High | Moderate | High |
Versatility | High | High | High | Moderate |
Efficiency | High | Very High | Moderate | High |
Cost | Moderate | High | Low | Moderate |
Energy Use | Moderate | High | High | Moderate |
Maintenance | High | Moderate | High | Moderate |
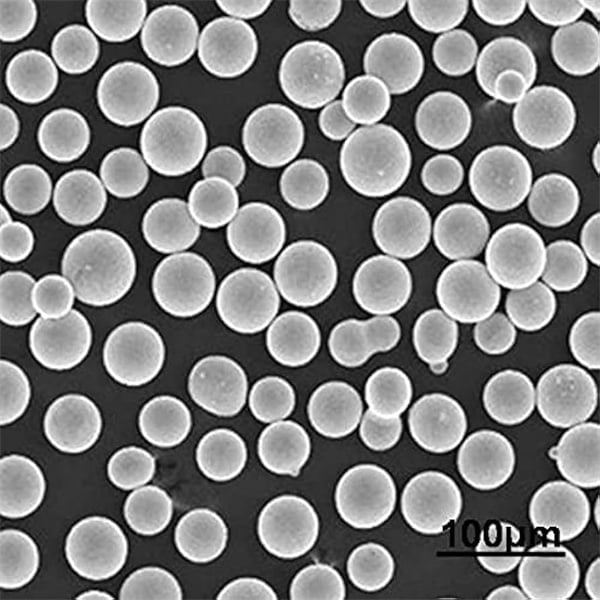
FAQ
Question | Answer |
---|---|
What is a powder making device? | A machine designed to convert solid materials into fine powders for various applications. |
What industries use powder making devices? | Industries like metallurgy, pharmaceuticals, food processing, and cosmetics. |
What are the advantages of using these devices? | Precision, versatility, efficiency, and customization. |
What are the common types of powder making devices? | Ball mills, jet mills, hammer mills, attrition mills, and fluid energy mills. |
How do I choose the right powder making device? | Consider your material, desired particle size, and application needs. |
What maintenance is required for these devices? | Regular cleaning, part replacement, and performance checks. |
Are these devices energy-efficient? | Efficiency varies by type; some are more energy-intensive than others. |
Can these devices handle all types of materials? | They are versatile but some models are better suited for specific materials. |
What is the cost range for these devices? | Prices vary widely depending on the type and model, ranging from $8,000 to $35,000. |
Where can I purchase powder making devices? | From specialized suppliers like PowderTech Inc., JetMills Ltd., and HammerMills Corp. |
Conclusion
Powder making devices are essential tools in many industries, offering the precision and efficiency needed for producing fine powders. By understanding the types, applications, specifications, and pros and cons, you can make an informed decision on the best device for your needs. Remember, choosing the right supplier and maintaining your equipment are key to maximizing performance and longevity. Happy powder making!
Share On
MET3DP Technology Co., LTD is a leading provider of additive manufacturing solutions headquartered in Qingdao, China. Our company specializes in 3D printing equipment and high-performance metal powders for industrial applications.
Inquiry to get best price and customized Solution for your business!
Related Articles
About Met3DP
Recent Update
Our Product
CONTACT US
Any questions? Send us message now! We’ll serve your request with a whole team after receiving your message.
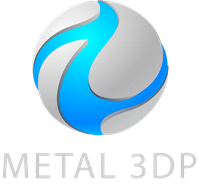
Metal Powders for 3D Printing and Additive Manufacturing