Powder Making Technology
Table of Contents
Overview of Powder Making Technology
Powder making technology has revolutionized numerous industries, offering a versatile approach to creating metal powders with specific properties tailored to various applications. This technology encompasses various processes, including atomization, mechanical alloying, and electrolysis, each with unique advantages and limitations. As industries evolve, the demand for high-quality metal powders continues to grow, driving innovation in powder production methods.
Key Details of Powder Making Technology
Process | Description | Applications |
---|---|---|
Atomization | Involves breaking down a molten metal stream into fine droplets that solidify into powders. | Aerospace, automotive, additive manufacturing |
Mechanical Alloying | Blends powders through high-energy ball milling to create alloy powders. | Metallurgy, electronics, nanotechnology |
Electrolysis | Utilizes electrochemical reactions to produce high-purity metal powders. | Batteries, catalysts, chemical industries |
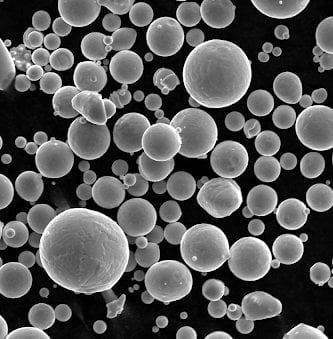
Types of Metal Powders and Their Models
Metal powders vary widely in composition, size, and properties, making them suitable for different applications. Here are some specific metal powder models:
- Aluminum Powder (Al-1001)
Composition: Pure aluminum
Properties: Lightweight, high thermal conductivity, corrosion-resistant
Applications: Aerospace components, automotive parts, electronics - Copper Powder (Cu-2002)
Composition: Pure copper
Properties: Excellent electrical and thermal conductivity, malleable
Applications: Electrical contacts, heat exchangers, conductive inks - Iron Powder (Fe-3003)
Composition: Pure iron
Properties: Magnetic, high strength, good ductility
Applications: Magnetic materials, automotive components, machinery - Nickel Powder (Ni-4004)
Composition: Pure nickel
Properties: Corrosion-resistant, high melting point, good conductivity
Applications: Batteries, superalloys, coatings - Titanium Powder (Ti-5005)
Composition: Pure titanium
Properties: High strength-to-weight ratio, corrosion-resistant, biocompatible
Applications: Medical implants, aerospace components, sporting goods - Stainless Steel Powder (SS-6006)
Composition: Iron-chromium-nickel alloy
Properties: Corrosion-resistant, high strength, durable
Applications: Surgical instruments, kitchenware, automotive parts - Cobalt-Chromium Powder (CoCr-7007)
Composition: Cobalt-chromium alloy
Properties: High wear resistance, biocompatible, high melting point
Applications: Medical implants, dental prosthetics, aerospace - Tungsten Powder (W-8008)
Composition: Pure tungsten
Properties: High density, high melting point, hard
Applications: Cutting tools, radiation shielding, aerospace - Silver Powder (Ag-9009)
Composition: Pure silver
Properties: Highest electrical conductivity, antimicrobial, malleable
Applications: Electrical contacts, medical devices, jewelry - Gold Powder (Au-1010)
Composition: Pure gold
Properties: Excellent corrosion resistance, high electrical conductivity, biocompatible
Applications: Electronics, medical devices, luxury goods
Applications of Powder Making Technology
Metal powders find applications in various fields, leveraging their unique properties to enhance product performance and manufacturing efficiency.
Application | Description | Examples |
---|---|---|
Additive Manufacturing | Utilizes metal powders to create complex, high-precision parts layer by layer. | Aerospace components, medical implants |
Metallurgy | Enhances properties of metals through powder blending and sintering. | High-strength alloys, wear-resistant parts |
Electronics | Metal powders are used in conductive pastes and components. | Conductive inks, circuit boards |
Automotive | Improves fuel efficiency and performance with lightweight components. | Engine parts, brake pads |
Medical | Biocompatible metal powders for implants and prosthetics. | Hip replacements, dental implants |
Aerospace | High-performance materials for critical aerospace applications. | Turbine blades, structural components |
Chemical Industry | Catalysts and filters made from specific metal powders. | Chemical reactors, filtration systems |
Specifications, Sizes, Grades, and Standards
When selecting metal powders, it’s crucial to consider their specifications, sizes, grades, and standards to ensure they meet the requirements of your application.
Model | Size Range (µm) | Grade | Standards |
---|---|---|---|
Al-1001 | 10-45 | A | ASTM B-214 |
Cu-2002 | 15-63 | B | ISO 4288 |
Fe-3003 | 5-150 | C | ASTM E-1079 |
Ni-4004 | 10-90 | A | ISO 9001 |
Ti-5005 | 20-100 | B | ASTM F-67 |
SS-6006 | 25-75 | C | ASTM A-240 |
CoCr-7007 | 15-45 | A | ISO 5832-12 |
W-8008 | 1-150 | B | ASTM B-777 |
Ag-9009 | 5-50 | A | ISO 10993-1 |
Au-1010 | 2-20 | B | ASTM B-488 |
Suppliers and Pricing Details
Finding the right supplier for metal powders is crucial to ensure quality and cost-effectiveness. Here are some key suppliers and indicative pricing details:
Supplier | Location | Models Available | Pricing (per kg) |
---|---|---|---|
Metal Powders Co. | USA | Al-1001, Cu-2002, Fe-3003 | $50 – $200 |
PowderTech Ltd. | Germany | Ni-4004, Ti-5005, SS-6006 | $100 – $500 |
Alloy Solutions Inc. | China | CoCr-7007, W-8008, Ag-9009 | $200 – $1000 |
Pure Metals Corp. | Japan | Au-1010, Al-1001, Cu-2002 | $500 – $2000 |
Advanced Powders | UK | Fe-3003, Ni-4004, Ti-5005 | $75 – $400 |
Comparing Pros and Cons of Powder Making Technology
Understanding the advantages and limitations of different powder making technologies can help in selecting the best method for your needs.
Technology | Advantages | Limitations |
---|---|---|
Atomization | High production rate, fine and spherical powders, versatile | High energy consumption, expensive equipment |
Mechanical Alloying | Produces uniform alloys, ability to create unique materials | Long processing times, potential contamination |
Electrolysis | High purity powders, precise control over composition | Limited to certain metals, lower production rate |
Chemical Reduction | Cost-effective for specific metals, scalable | Environmental concerns, complex processing |
Centrifugal Atomization | Controlled particle size distribution, minimal oxidation | Limited to specific applications, higher operational costs |
Advantages of Powder Making Technology
Powder making technology offers numerous benefits that make it a preferred choice in various industries.
- Versatility: Powder making technology can produce powders of different compositions and sizes, suitable for diverse applications.
- Precision: Advanced techniques ensure precise control over particle size and composition, resulting in high-quality products.
- Efficiency: Processes like atomization and mechanical alloying allow for high production rates, meeting industrial demands efficiently.
- Customization: Metal powders can be tailored to meet specific requirements, such as enhanced strength, conductivity, or biocompatibility.
- Sustainability: Some powder production methods, such as mechanical alloying, can utilize recycled materials, promoting sustainability.
Disadvantages of Powder Making Technology
Despite its advantages, powder making technology has certain limitations that must be considered.
- High Costs: The equipment and energy required for some powder production methods, like atomization, can be expensive.
- Complexity: Processes like mechanical alloying require specialized knowledge and equipment, making them complex to implement.
- Environmental Impact: Certain methods, such as chemical reduction, can have negative environmental impacts due to the use of hazardous chemicals.
- Limitations in Material Selection: Not all metals can be processed efficiently using every powder making technique, limiting their applicability.
- Quality Control: Ensuring consistent quality across large batches of powder can be challenging, requiring stringent quality control measures.
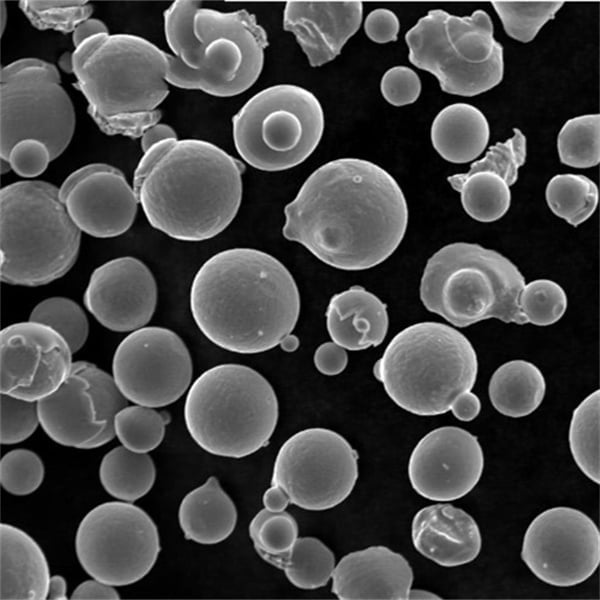
FAQ
What is powder making technology?
Powder making technology encompasses various methods used to produce fine metal powders for industrial applications. These methods include atomization, mechanical alloying, and electrolysis, each offering unique advantages
What is powder making technology?
Powder making technology refers to the processes used to create fine particles (powder) from bulk materials. These materials can be metals, plastics, ceramics, food products, and even pharmaceuticals. There are many different techniques, each with its own advantages and suited for creating powders with specific properties.
What are some applications of powder making technology?
- Additive manufacturing (3D printing): Powders are a key material for 3D printing processes like Selective Laser Sintering (SLS) and Selective Laser Melting (SLM).
- Powder metallurgy: Metal powders are used to create complex shapes through compaction and sintering.
- Coatings: Powders are used in paints, inks, and other coatings for protection, decoration, and adding functionality.
- Pharmaceuticals: Powders are a common dosage form for medications.
- Food: Powdered milk, coffee, and sugar are all examples of food products made using powder technology.
Types of Powder Making Techniques:
- Atomization: Molten metal is broken up into fine droplets using a gas or water stream, which solidify into spherical particles. This is a common method for metal powders.
- Grinding: Bulk material can be ground into a powder, but this method results in irregularly shaped particles. It’s often used for brittle materials.
- Electrolysis: An electric current is used to break down a metal compound into its elements, one of which may be a powder.
- Precipitation: A solution is used to create fine particles of a material, often used for plastics or pharmaceuticals.
Share On
MET3DP Technology Co., LTD is a leading provider of additive manufacturing solutions headquartered in Qingdao, China. Our company specializes in 3D printing equipment and high-performance metal powders for industrial applications.
Inquiry to get best price and customized Solution for your business!
Related Articles
About Met3DP
Recent Update
Our Product
CONTACT US
Any questions? Send us message now! We’ll serve your request with a whole team after receiving your message.
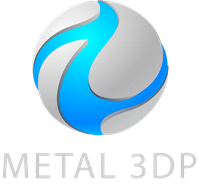
Metal Powders for 3D Printing and Additive Manufacturing