Powder post-atomization treatment
Table of Contents
Overview of Powder Post-Atomization Treatment
Post-atomization treatment of powders is a critical step to modify and enhance the properties of metal powders after they have been atomized. This can involve several processes such as heat treatment, mechanical milling, sieving, and surface treatment. The aim is to improve the powder’s flowability, reduce particle size distribution, increase purity, and enhance other specific properties needed for various applications.
Key Processes in Post-Atomization Treatment
- Heat Treatment: Used to relieve internal stresses, modify phase structures, and improve mechanical properties.
- Mechanical Milling: Reduces particle size and refines the microstructure.
- Sieving: Ensures uniform particle size distribution.
- Surface Treatment: Enhances the surface properties of the powder particles.
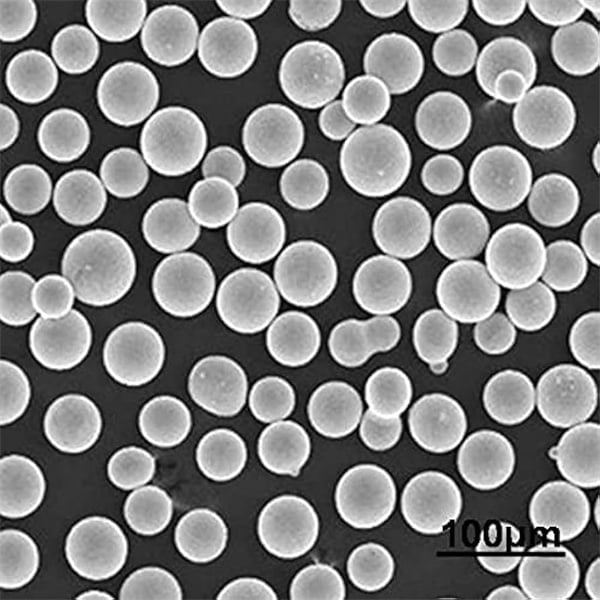
Specific Metal Powder Models
1. Inconel 625 Powder
Composition: Nickel-Chromium-Molybdenum alloy with additions of niobium.
Properties: Excellent corrosion resistance, high tensile, fatigue, and creep-rupture strength.
Characteristics: Suitable for extreme environments, high resistance to oxidation and carburization.
Applications: Aerospace, marine, chemical processing, and nuclear reactors.
2. Aluminum 6061 Powder
Composition: Magnesium and silicon as major alloying elements.
Properties: Good mechanical properties, weldability, and corrosion resistance.
Characteristics: Lightweight, strong, and versatile.
Applications: Automotive, aerospace, and structural components.
3. Titanium Ti-6Al-4V Powder
Composition: Titanium alloyed with aluminum and vanadium.
Properties: High strength, low weight, and excellent corrosion resistance.
Characteristics: Biocompatible, making it suitable for medical implants.
Applications: Aerospace, medical devices, and automotive.
4. Stainless Steel 316L Powder
Composition: Iron, chromium, nickel, and molybdenum.
Properties: Excellent corrosion resistance, high tensile strength, and durability.
Characteristics: Suitable for harsh environments and applications requiring high hygiene standards.
Applications: Medical, food processing, and marine.
5. Copper Cu-ETP Powder
Composition: Electrolytic tough pitch copper.
Properties: High electrical and thermal conductivity, good corrosion resistance.
Characteristics: Easy to fabricate and join.
Applications: Electrical components, heat exchangers, and plumbing.
6. Cobalt-Chromium Alloy Powder
Composition: Cobalt, chromium, and molybdenum.
Properties: High wear and corrosion resistance, good mechanical strength.
Characteristics: Suitable for high-temperature applications.
Applications: Orthopedic implants, dental devices, and aerospace.
7. Magnesium AZ91 Powder
Composition: Magnesium alloy with aluminum and zinc.
Properties: Low density, high strength-to-weight ratio.
Characteristics: Lightweight and machinable.
Applications: Automotive, aerospace, and electronics.
8. Nickel 718 Powder
Composition: Nickel-chromium alloy with molybdenum, niobium, and titanium.
Properties: High strength, good corrosion and oxidation resistance.
Characteristics: Suitable for high-temperature applications.
Applications: Aerospace, power generation, and oil and gas.
9. Tungsten Carbide Powder
Composition: Tungsten and carbon.
Properties: Extremely hard, high wear resistance.
Characteristics: Suitable for cutting tools and wear-resistant applications.
Applications: Mining, machining, and industrial tooling.
10. Zirconium Zr702 Powder
Composition: Commercially pure zirconium.
Properties: Excellent corrosion resistance, high melting point.
Characteristics: Suitable for nuclear applications.
Applications: Nuclear reactors, chemical processing, and medical devices.
Applications of Powder Post-Atomization Treatment
Post-atomization treatment enhances the properties of metal powders, making them suitable for a wide range of applications. Here, we outline some key uses across different industries:
Industry | Applications |
---|---|
Aerospace | Jet engine components, structural parts |
Automotive | Engine parts, lightweight structures |
Medical | Implants, surgical instruments |
Electronics | Conductive inks, thermal management components |
Chemical | Catalysts, filtration systems |
Marine | Propellers, underwater fittings |
Nuclear | Reactor components, fuel cladding |
Oil and Gas | Drill bits, corrosion-resistant fittings |
Tooling | Cutting tools, wear-resistant parts |
Specifications, Sizes, Grades, and Standards
The specifications, sizes, grades, and standards for metal powders vary based on their composition and intended application. Here is a detailed overview:
Metal Powder Model | Particle Size Range (µm) | Grade | Standards |
---|---|---|---|
Inconel 625 | 15-53 | Premium | AMS 5666, UNS N06625 |
Aluminum 6061 | 10-75 | AA6061 | ASTM B209, SAE AMS 4025 |
Ti-6Al-4V | 20-60 | Grade 5 | ASTM F136, ISO 5832-3 |
Stainless Steel 316L | 15-45 | 316L | ASTM A240, AMS 5653 |
Copper Cu-ETP | 20-100 | C11000 | ASTM B152, SAE J463 |
Cobalt-Chromium | 10-50 | ASTM F75 | ASTM F799, ISO 5832-4 |
Magnesium AZ91 | 30-100 | AZ91D | ASTM B93/B93M |
Nickel 718 | 15-63 | UNS N07718 | AMS 5662, ASTM B637 |
Tungsten Carbide | 5-30 | WC-Co | ISO 9001, ASTM B777 |
Zirconium Zr702 | 20-50 | Zr702 | ASTM B551, ISO 9001 |
Suppliers and Pricing Details
Finding the right supplier is crucial for obtaining high-quality metal powders. Below is a list of notable suppliers and a general pricing overview for different metal powders:
Supplier | Metal Powder Models | Price Range (per kg) |
---|---|---|
Höganäs | Inconel 625, Stainless Steel 316L | $200 – $350 |
Carpenter Technology | Ti-6Al-4V, Nickel 718 | $250 – $400 |
Sandvik | Cobalt-Chromium, Tungsten Carbide | $300 – $500 |
GKN Additive | Aluminum 6061, Magnesium AZ91 | $150 – $300 |
Praxair Surface Technologies | Copper Cu-ETP, Zirconium Zr702 | $100 – $250 |
Pros and Cons: Advantages and Limitations
Understanding the advantages and limitations of each metal powder is crucial for selecting the right material for your application. Here, we compare some key parameters:
Metal Powder Model | Advantages | Limitations |
---|---|---|
Inconel 625 | Excellent corrosion resistance, high strength | High cost |
Aluminum 6061 | Lightweight, versatile, good machinability | Lower strength compared to other alloys |
Ti-6Al-4V | High strength-to-weight ratio, biocompatible | Expensive, difficult to machine |
Stainless Steel 316L | Excellent corrosion resistance, durability | Heavier than some other metals |
Copper Cu-ETP | High conductivity, easy to work with | Susceptible to oxidation |
Cobalt-Chromium | High wear resistance, good mechanical properties | Expensive, difficult to process |
Magnesium AZ91 | Very lightweight, good machinability | Flammable in fine powder form |
Nickel 718 | High strength at high temperatures | High cost |
Tungsten Carbide | Extremely hard, high wear resistance | Brittle, difficult to machine |
Zirconium Zr702 | Excellent corrosion resistance, high melting point | Expensive, limited availability |
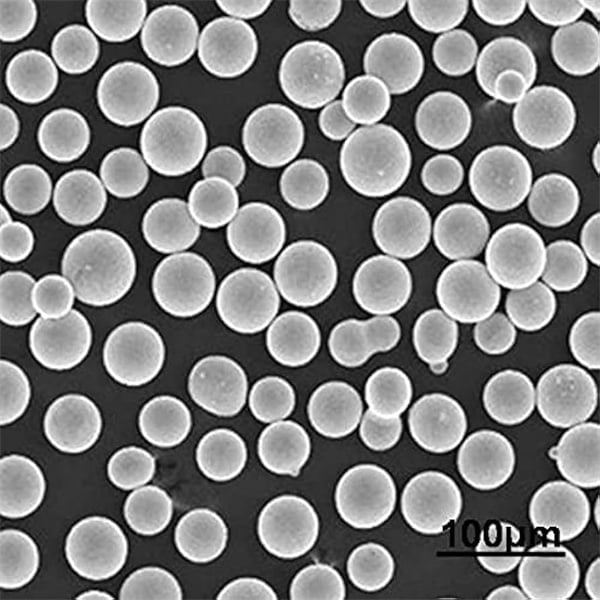
FAQ
What is post-atomization treatment of metal powders?
Post-atomization treatment refers to the additional processing steps taken after the initial atomization of metal powders. These steps can include heat treatment, mechanical milling, sieving, and surface treatment to enhance the powder’s properties.
Why is post-atomization treatment necessary?
It is necessary to improve the flowability, particle size distribution, purity, and other specific properties of metal powders to meet the requirements of various applications.
Which industries benefit from post-atomization treated powders?
Industries such as aerospace, automotive, medical, electronics, chemical, marine, nuclear, oil and gas, and tooling benefit from these enhanced powders.
What are some common metal powders used in post-atomization treatment?
Common metal powders include Inconel 625, Aluminum 6061, Titanium Ti-6Al-4V, Stainless Steel 316L, Copper Cu-ETP, Cobalt-Chromium, Magnesium AZ91, Nickel 718, Tungsten Carbide, and Zirconium Zr702.
How do the properties of metal powders change after post-atomization treatment?
Properties such as strength, corrosion resistance, particle size distribution, and surface characteristics can be significantly improved after post-atomization treatment.
What should I consider when selecting a metal powder for my application?
Consider the powder’s composition, properties, particle size distribution, and the specific requirements of your application. Additionally, take into account the cost, availability, and supplier reputation.
Are there any limitations to using post-atomization treated powders?
Yes, limitations can include higher costs, potential difficulties in processing certain materials, and the need for specialized equipment and expertise.
Share On
MET3DP Technology Co., LTD is a leading provider of additive manufacturing solutions headquartered in Qingdao, China. Our company specializes in 3D printing equipment and high-performance metal powders for industrial applications.
Inquiry to get best price and customized Solution for your business!
Related Articles
About Met3DP
Recent Update
Our Product
CONTACT US
Any questions? Send us message now! We’ll serve your request with a whole team after receiving your message.
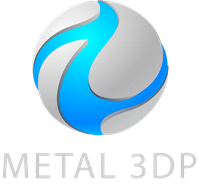
Metal Powders for 3D Printing and Additive Manufacturing