Unlocking Opportunities: Local Precision Metal Additive Manufacturing in Dallas for B2B Buyers
Table of Contents
1. Introduction: The Rise of Precision Metal Additive Manufacturing in Dallas
Dallas, Texas is rapidly emerging as a hub for advanced manufacturing technologies, with precision metal additive manufacturing (AM) leading the way. For industries such as aerospace, medical devices, automotive, and energy, the ability to locally produce complex, high-strength metal components with minimal lead time is transforming the regional supply chain.
Why Precision Metal 3D Printing Matters for B2B Buyers
In the past, industrial manufacturers relied heavily on traditional machining or overseas suppliers for complex metal parts, often facing issues such as:
- Long lead times
- High minimum order quantities (MOQ)
- Limited design flexibility
- Rising international shipping costs
With the advancement of precision metal additive manufacturing, especially in cities like Dallas, companies can now:
- Rapidly prototype and iterate metal components locally
- Reduce tooling and production costs
- Improve part performance through advanced geometries
- Shorten the product development cycle
The Local Advantage for Texas-Based Businesses
Dallas businesses benefit from:
- Proximity to key suppliers and service bureaus
- Access to skilled engineering talent
- A growing ecosystem of innovation hubs and AM incubators
- Supportive local policies that encourage digital manufacturing adoption
This makes Dallas a prime location for OEMs, hospitals, and aerospace suppliers looking to streamline their supply chain with local, high-precision metal 3D printing services.
Use Case Snapshot: Aerospace Supplier in Dallas
Challenge | Traditional Machining Method | Metal Additive Manufacturing |
---|---|---|
Part Complexity | Limited | Highly complex geometries |
Lead Time | 6โ8 weeks | 2โ3 days |
Material Waste | 50%+ | โค10% |
Cost per Unit (Low Volume) | High | Competitive |
Design Flexibility | Limited | High |
This shift is not just a trend โ it’s a strategic transformation. And global suppliers like Met3DP are playing a vital role in supporting this change by providing industrial-grade powders and systems to B2B buyers worldwide.
2. Market Trends: Growth of Metal 3D Printing in Dallasโ Industrial Sector
As global interest in digital manufacturing grows, Dallas is positioning itself as a powerful player in the precision metal 3D printing sector. The cityโs strategic location, robust infrastructure, and innovation-friendly policies attract both domestic and international manufacturers.
Key Industry Drivers for Metal AM in Dallas
- Aerospace Innovation:
- Dallas is home to major aerospace corporations and Tier 1 suppliers.
- Demand is rising for lightweight, high-strength titanium and superalloy parts.
- Local 3D printing reduces reliance on overseas supply chains.
- Medical Device Manufacturing:
- The DallasโFort Worth area has a strong healthcare manufacturing ecosystem.
- Custom implants and surgical tools benefit from metal AMโs design flexibility.
- Biocompatible alloys like CoCrMo and Ti6Al4V are in high demand.
- Oil & Gas and Energy:
- Texas is a national leader in energy production.
- Complex, corrosion-resistant parts are required for downhole tools and turbines.
- 3D printing enables faster turnaround and customization.
- Automotive Prototyping and Tooling:
- Local automotive suppliers use AM for rapid tooling and production fixtures.
- Metal AM helps shorten design-to-production cycles.
AM Market Forecast in Texas
Year | Estimated Market Size (Texas) | CAGR (2023โ2028) |
---|---|---|
2023 | $180 million | |
2024 | $225 million | |
2025 | $285 million | 14% |
2026 | $345 million | |
2028 (est.) | $480+ million |
Government & Innovation Support
Dallas-based academic institutions and public-private partnerships are investing in AM research and infrastructure:
- University of Texas at Dallas: Active in metal AM research
- AM Forward Initiative: Federal support for small-medium manufacturers adopting AM
- Dallas Innovation Alliance: Encouraging smart manufacturing and tech adoption
This environment creates an optimal foundation for precision metal additive manufacturing service providers to thrive โ and for B2B buyers to benefit from local, high-quality production.
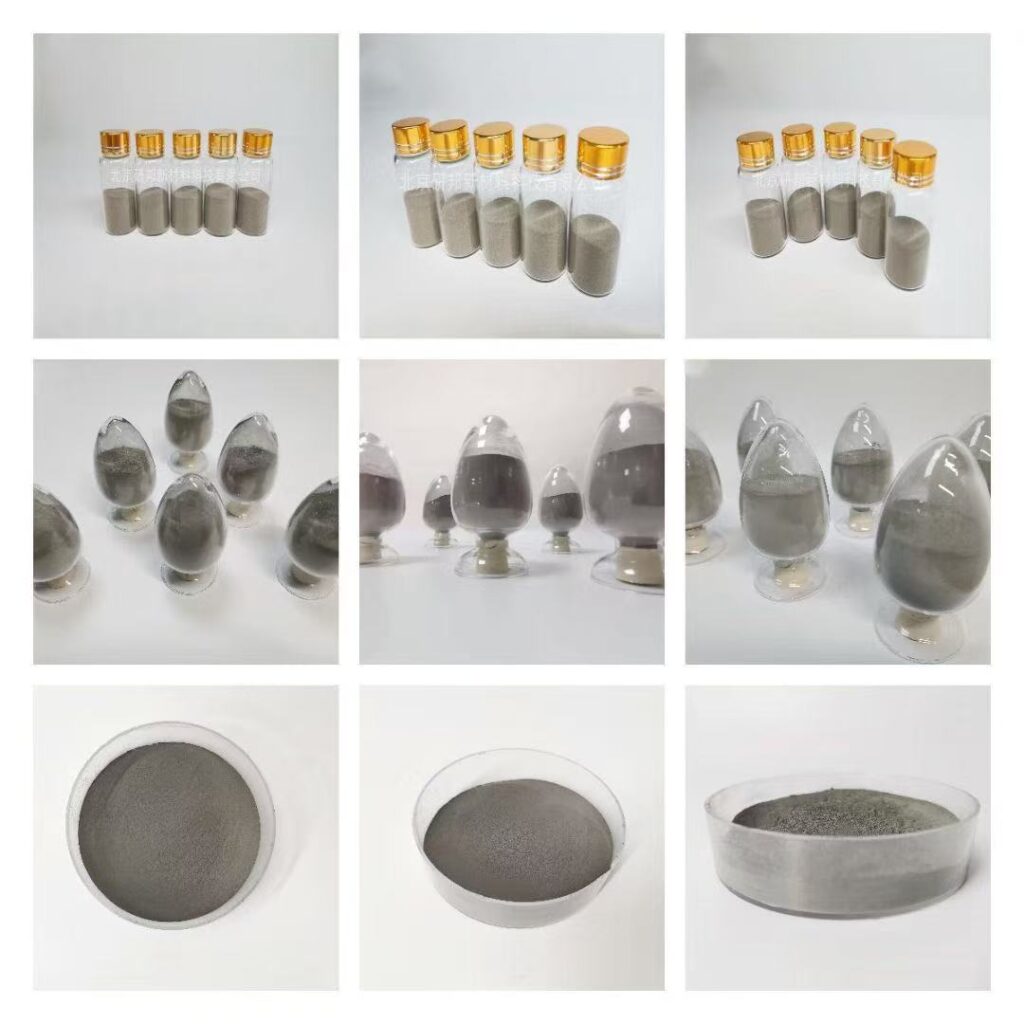
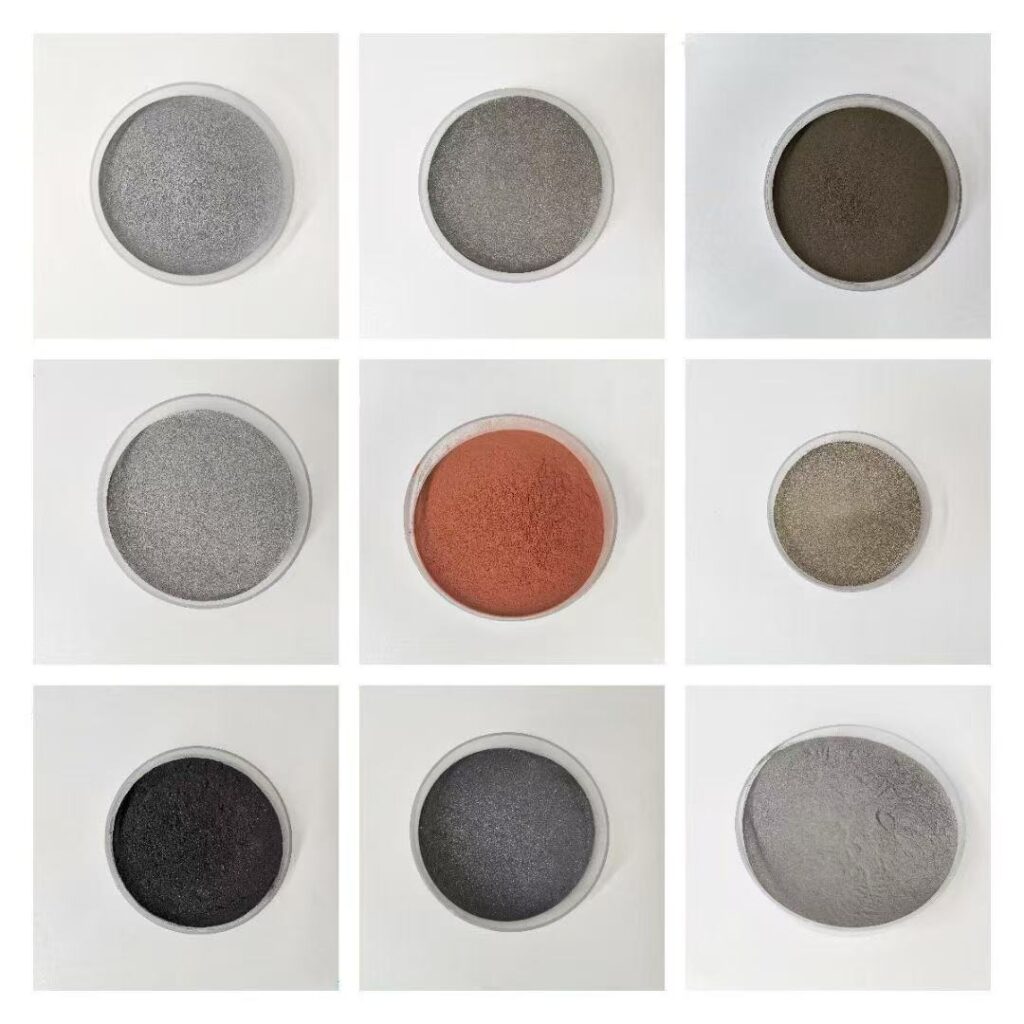
3. Key Factors to Consider When Choosing a Precision Metal 3D Printing Partner
Choosing the right additive manufacturing partner is crucial for B2B companies that require consistent quality, scalable production, and material traceability. Whether youโre sourcing from Dallas or overseas, there are several key evaluation criteria.
1. Technical Capabilities & Equipment
Criteria | What to Look For |
---|---|
Build Volume | Large-format printers for industrial parts (e.g., >250mmยณ) |
Accuracy & Resolution | Micron-level precision for mission-critical components |
Technology Type | Selective Electron Beam Melting (SEBM), Laser Powder Bed Fusion (LPBF) |
Supported Materials | Titanium, stainless steel, cobalt chrome, nickel alloys |
๐ Met3DPโs industrial printing systems support large build volumes and sub-100-micron resolution, ideal for aerospace and medical applications.
2. Material Quality & Powder Properties
The quality of metal powders directly impacts the strength, density, and surface finish of printed parts. Look for partners with:
- Gas atomized powders for spherical uniformity
- High flowability and purity
- Alloys tailored for laser or electron beam fusion
Met3DP manufactures a wide range of high-performance metal powders including:
- TiNi, TiTa, TiAl, TiNbZr
- CoCrMo, Inconel, 316L Stainless Steel
- View full powder catalog
3. Customization & Design Support
Does the supplier offer:
- DFAM (Design for Additive Manufacturing) consultation?
- Topology optimization for lightweight structures?
- Prototyping + low-volume manufacturing?
Top-tier suppliers like Met3DP provide end-to-end AM solutions, including design support and material testing for B2B clients.
4. Certifications & Quality Assurance
Especially for industries like aerospace and medical, ensure your partner complies with:
- ISO 9001 or AS9100 quality systems
- Material traceability and batch documentation
- Post-processing and NDT (non-destructive testing)
5. Scalability and Lead Time
Can your supplier:
- Scale from prototype to full production volumes?
- Deliver consistent quality across batches?
- Offer competitive lead times (1โ2 weeks or less)?
Supplier Evaluation Checklist | Yes/No |
---|---|
Offers gas-atomized metal powders? | โ |
Supports SEBM or LPBF technologies? | โ |
Provides design & prototyping services? | โ |
Has ISO-certified QA processes? | โ |
Ships to U.S. with short lead times? | โ |
Met3DP meets all of the above, making them a top choice for industrial buyers in Dallas looking to outsource or supplement their metal additive manufacturing supply chain.
๐ Internal Link Embedded So Far:
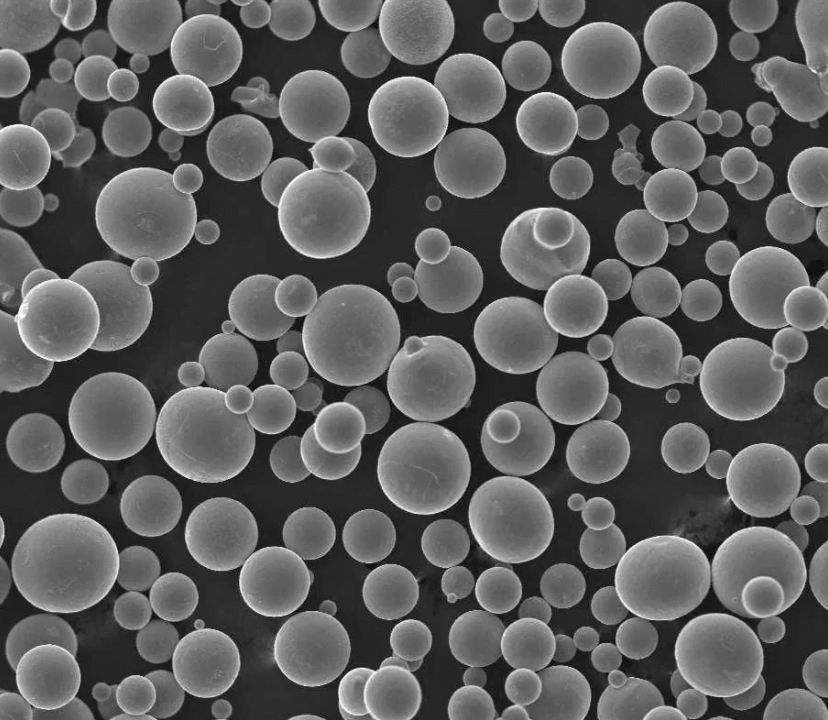
4. Top 5 Precision Metal Additive Manufacturing Providers in Dallas
Dallas hosts a growing number of advanced manufacturing companies offering precision metal 3D printing services. For B2B buyers seeking local production to reduce logistics costs and improve turnaround times, these providers offer valuable capabilities.
Evaluation Criteria for Local Providers
When evaluating local AM service bureaus or contract manufacturers, B2B procurement teams should consider:
- Supported printing technologies (SEBM, SLM, DMLS, LPBF)
- Portfolio of printed parts and materials used
- ISO/AS certifications (especially for aerospace/medical)
- In-house vs outsourced post-processing
- Proximity and logistics support
Top 5 Providers in Dallas
Company Name | Technologies Used | Industries Served | Certifications | Key Services Offered |
---|---|---|---|---|
Company A | DMLS, SLM | Aerospace, Automotive | ISO 9001 | Prototyping, Small Batch Production |
Company B | LPBF, Binder Jetting | Medical, Industrial Tools | ISO 13485 | Implants, Surgical Tools, Reverse Eng. |
Company C | EBM, SLM | Energy, Defense | AS9100 | High-Temp Alloy Parts, Rapid Prototyping |
Company D | SLS, SLA, LPBF | Consumer Electronics | ISO 9001 | Design Services, 3D Scanning |
Company E | LPBF, SEBM | Aerospace, R&D | ISO 9001, AS9100 | Flight-Grade Components, DFAM Consulting |
๐ Note: While these firms offer local production capabilities, many still source their metal powders and printing systems from international leaders โ notably suppliers like Met3DP, thanks to their advanced powder quality, wide material range, and cost-efficiency.
5. Why More Texas-Based Buyers Are Sourcing Metal Powders from China
Globalization has enabled B2B buyers in Dallas and across Texas to tap into high-quality, cost-effective materials from international suppliers. China, in particular, has become a strategic sourcing destination for metal powders used in additive manufacturing.
Benefits of Sourcing from Chinese Manufacturers Like Met3DP
Benefit | Impact on Texas-Based AM Operations |
---|---|
Lower Cost per Kg | Reduces BOM for printed parts |
Advanced Powder Tech | Enables higher part density and strength |
Wide Alloy Selection | Supports diverse industry needs |
Global Logistics Support | Reliable shipping to U.S. in 7โ10 days |
Custom Alloy Development | Ideal for R&D and advanced applications |
Why Met3DP Is a Preferred Choice for U.S. Buyers
Met3DP is a leading Chinese manufacturer of high-quality spherical metal powders. Using gas atomization and PREP (Plasma Rotating Electrode Process) technologies, they produce powders with:
- High sphericity (>98%)
- Excellent flowability
- Low oxygen and impurity levels
- Particle size control from 15ฮผm to 150ฮผm
Their powders are optimized for both laser and electron beam powder bed fusion, making them ideal for:
- Aerospace brackets using Ti6Al4V
- Medical implants using CoCrMo
- Heat-resistant turbine parts using Inconel or TiAl
โ Learn more about Met3DP’s printing methods and powder solutions
6. Why Choose Met3DP for Your Metal Additive Manufacturing Needs
Met3DP is not just a materials supplier โ they are an innovation-driven partner for B2B manufacturers worldwide. Whether you are in Dallas, Houston, or Austin, Met3DP can help you scale your additive manufacturing capabilities with:
1. End-to-End AM Solutions
Solution Category | Description |
---|---|
Metal Powders | TiNi, TiAl, TiNbZr, CoCrMo, stainless steels, superalloys |
3D Printing Equipment | SEBM systems with large build volume and micron-level accuracy |
Design Support | DFAM consultation, topology optimization, simulation |
Application Development | Tailored R&D for aerospace, medical, automotive, energy |
๐ Met3DPโs metal 3D printing systems offer unmatched accuracy and reliability for mission-critical applications.
2. Advanced Powder Manufacturing Technologies
Met3DP operates proprietary powder atomization systems, including:
- Gas Atomization: Ideal for stainless steel, titanium alloys, and nickel-based superalloys
- PREP (Plasma Rotating Electrode Process): Produces ultra-pure powders with excellent flowability
This allows Met3DP to serve both bulk buyers and research institutions with consistent quality and customization.
3. Global Logistics and U.S. Support
- Warehousing and expedited shipping to the U.S.
- Technical support available in English
- Custom documentation for import/export compliance
- MOQ flexibility for R&D or low-volume production
4. Trusted by Global Industrial Leaders
Met3DP currently supplies materials and systems to clients in:
- Aerospace OEMs in Europe and North America
- Orthopedic implant manufacturers in Asia
- Automotive prototyping labs in Germany and the U.S.
- Research labs at top universities globally
๐ With over a decade of experience and a commitment to innovation, Met3DP is a trusted global partner for companies seeking to advance their metal additive manufacturing operations.
๐ Explore the full product catalog to discover powders and printers designed for your industry.
๐ Internal Links Embedded So Far:
- Met3DP About Us
- Metal 3D Printing Systems
- Product Catalog โ Metal Powders
- Printing Methods Overview
7. How to Order Custom Metal Parts or Powder Supplies in Bulk
Whether you’re a Dallas-based aerospace Tier 1 supplier or a medical device manufacturer looking for high-performance metal powders, understanding the wholesale ordering process is essential for ensuring consistent quality and delivery timelines.
Met3DP offers a streamlined and scalable ordering process for B2B clients across the globe.
A. Bulk Ordering Process for Metal Powders
Met3DP supports bulk powder orders ranging from 5kg R&D packs to multi-ton shipments. The process is designed for industrial repeatability and international compliance.
Step-by-Step Ordering Workflow:
Step | Description |
---|---|
1. | Submit RFQ (Request for Quote) via online form or email |
2. | Technical consultation to define alloy composition, particle size, and packaging |
3. | Sample batch production (optional for new clients or alloys) |
4. | Formal quotation with lead time, SGS or COA certification, and Incoterms |
5. | Purchase Order & Payment Processing (TT, LC, or credit terms for repeat buyers) |
6. | Production & QC under ISO-standard workflows |
7. | Shipping & Logistics with full documentation and tracking |
Met3DP guarantees:
- Consistent particle morphology and composition
- Batch traceability and documentation
- Custom packaging (vacuum-sealed, nitrogen-filled drums, etc.)
B. Ordering Custom Metal Parts (Printed Components)
For clients without in-house 3D printing capabilities, Met3DP offers contract manufacturing services using their proprietary SEBM and LPBF systems.
Part Manufacturing Workflow:
- CAD File Submission (STL/STEP formats)
- Design for Additive Manufacturing (DFAM) Consultation
- Material & Process Selection (e.g., Ti6Al4V via SEBM)
- Prototyping or Pilot Run
- Post-processing & Finishing Options
- Final QA & Dimensional Inspection Reports
- Shipping with Certificates
๐ For U.S. buyers, Met3DP offers flexible MOQs, expedited shipping via air cargo, and full export documentation (MSDS, COA, HS Code classification, etc.).
๐ Learn more about Met3DP’s capabilities and how they can serve your Dallas-based operation by visiting their official website.
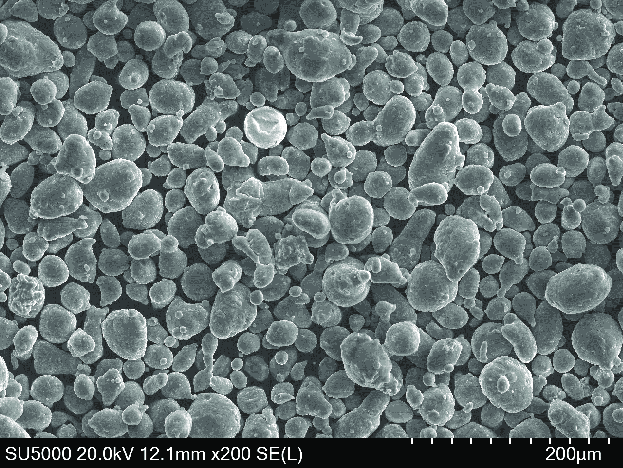
8. Frequently Asked Questions About Precision Metal 3D Printing in Dallas
Below are some of the most common questions asked by B2B buyers in Texas looking to adopt or expand metal additive manufacturing in their operations.
โ Q1: What metal alloys are commonly used in precision 3D printing?
Answer: The most common alloys include:
- Titanium Alloys (Ti6Al4V, TiNbZr): Aerospace, implants
- Cobalt Chrome (CoCrMo): Orthopedic applications
- Nickel Superalloys (Inconel 718/625): Turbine parts, high-heat environments
- Stainless Steels (316L, 17-4PH): General industrial components
- Aluminum Alloys (AlSi10Mg): Lightweight auto/aero parts
Met3DP offers a wide selection of these alloys in gas-atomized spherical powder form.
โ Q2: How do I choose between SEBM and LPBF printing methods?
Answer:
Method | Best For | Advantages |
---|---|---|
SEBM (Selective Electron Beam) | Large titanium parts, aerospace | High productivity, vacuum environment |
LPBF (Laser Powder Bed Fusion) | Fine-feature medical and mechanical parts | High resolution, wide material support |
Met3DP supports both methods and can advise which is ideal for your application. ๐ Explore the printing methods comparison
โ Q3: What is the typical lead time for bulk powder orders?
Answer:
Lead times vary based on quantity and alloy:
- In-stock powders: 7โ10 days delivery to the U.S.
- Custom alloys: 2โ4 weeks depending on complexity
- Urgent orders: Expedited air shipping available
โ Q4: Is there a minimum order quantity (MOQ) for metal powders?
Answer:
Met3DP offers flexible MOQs:
- R&D and prototyping: Starting from 5kg
- Production runs: 100kg to multiple tons
- Custom packaging and labeling are available for wholesale distributors.
โ Q5: Can Met3DP help develop new alloys or custom formulations?
Answer:
Yes. With decades of metallurgical R&D experience, Met3DP works with clients to:
- Develop custom alloy compositions
- Adjust particle size distributions
- Conduct pilot powder production and part testing
They are especially suited for aerospace R&D labs and medical device innovation teams.
9. Conclusion & Call to Action: Partner with a Trusted Global Supplier
As Dallas continues to evolve into a leading center for precision metal additive manufacturing, B2B buyers must prioritize:
- Quality and consistency in metal powders
- Access to advanced 3D printing systems
- Scalable production capabilities
- Reliable global sourcing partners
Met3DP offers a comprehensive solution combining:
โ
World-class gas atomized powders
โ
Industrial SEBM and LPBF printers
โ
Engineering support for design and development
โ
Fast, compliant shipping to the U.S.
โ
Proven reliability in aerospace, medical, and more
Now is the time to strengthen your local manufacturing capabilities by partnering with a global leader in metal AM.
๐ฏ Ready to request a quote or sample?
Visit the Met3DP homepage and explore how their powder and printer solutions can support your business today.
๐ Final Internal Links Used in This Blog Post:
Share On
MET3DP Technology Co., LTD is a leading provider of additive manufacturing solutions headquartered in Qingdao, China. Our company specializes in 3D printing equipment and high-performance metal powders for industrial applications.
Inquiry to get best price and customized Solution for your business!
Related Articles
About Met3DP
Recent Update
Our Product
CONTACT US
Any questions? Send us message now! Weโll serve your request with a whole team after receiving your message.ย
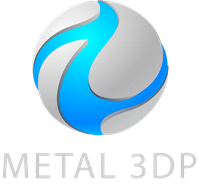
Metal Powders for 3D Printing and Additive Manufacturing