The Ultimate Guide to Quality Materials
Table of Contents
When we talk about quality materials, we’re delving into the heart of what makes our products reliable, durable, and efficient. Quality materials can make or break a project, whether it’s constructing a skyscraper, building a car, or manufacturing a smartphone. In this guide, we’ll explore the intricacies of quality materials, focusing on metal powders, their properties, applications, and how they compare to one another. Ready to dive in? Let’s get started.
Understanding Quality Materials
Quality materials are the backbone of successful engineering and manufacturing. They are the raw components that ensure the longevity, functionality, and aesthetic appeal of the final product. Metals, polymers, ceramics, and composites each play a unique role in various industries. Among these, metal powders are particularly noteworthy due to their versatility and wide range of applications.
Metal powders are fine particles of metals, ranging from a few micrometers to a few millimeters in size. They are used in a variety of manufacturing processes, including powder metallurgy, additive manufacturing (3D printing), and coating processes. The properties of metal powders, such as particle size, shape, and distribution, significantly impact the quality of the final product.
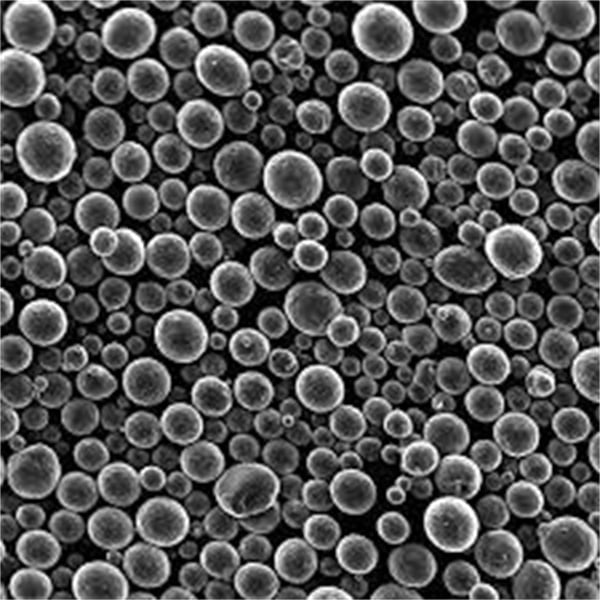
Types, Composition, Properties, and Characteristics of Metal Powders
Metal Powder | Composition | Properties | Characteristics |
---|---|---|---|
Aluminum Powder | Pure aluminum or aluminum alloys | Lightweight, high conductivity, corrosion-resistant | Used in automotive, aerospace, and electronics industries |
Titanium Powder | Pure titanium or titanium alloys | High strength-to-weight ratio, corrosion-resistant | Ideal for aerospace, medical implants, and sports equipment |
Stainless Steel Powder | Iron, chromium, nickel, and molybdenum | High strength, corrosion-resistant, wear-resistant | Commonly used in automotive, medical, and construction industries |
Iron Powder | Pure iron or iron alloys | Magnetic, high density, relatively low cost | Widely used in automotive, machinery, and structural applications |
Copper Powder | Pure copper or copper alloys | High conductivity, corrosion-resistant, malleable | Utilized in electrical components, electronics, and thermal applications |
Nickel Powder | Pure nickel or nickel alloys | Corrosion-resistant, high strength, magnetic | Used in aerospace, batteries, and electroplating industries |
Cobalt Powder | Pure cobalt or cobalt alloys | High temperature resistance, magnetic | Key material in superalloys, batteries, and magnetic applications |
Tungsten Powder | Pure tungsten or tungsten alloys | Very high melting point, high density, strong | Essential for cutting tools, electronics, and aerospace components |
Chromium Powder | Pure chromium or chromium alloys | Hard, corrosion-resistant, high melting point | Utilized in stainless steel production and coating applications |
Zinc Powder | Pure zinc or zinc alloys | Low melting point, corrosion-resistant | Used in galvanizing, batteries, and alloying with other metals |
Applications and Uses of Metal Powders
Understanding the applications of different metal powders helps in selecting the right material for the job. Here’s a table that shows where each type of metal powder shines:
Metal Powder | Applications |
---|---|
Aluminum Powder | Automotive parts, aerospace components, paints, and pyrotechnics |
Titanium Powder | Aircraft parts, medical implants, sports equipment |
Stainless Steel Powder | Automotive parts, medical devices, construction materials |
Iron Powder | Automotive components, machinery parts, structural applications |
Copper Powder | Electrical components, electronics, heat sinks |
Nickel Powder | Aerospace parts, battery electrodes, electroplating |
Cobalt Powder | Superalloys for jet engines, batteries, magnetic materials |
Tungsten Powder | Cutting tools, electronic components, aerospace parts |
Chromium Powder | Stainless steel production, coatings |
Zinc Powder | Galvanizing steel, battery production, alloying |
Specifications, Sizes, Grades, and Standards
When selecting metal powders, it’s crucial to consider their specifications, sizes, grades, and standards. These factors determine the suitability of the powder for specific applications.
Metal Powder | Specifications | Sizes | Grades | Standards |
---|---|---|---|---|
Aluminum Powder | ASTM B928 | 1-100 microns | 1100, 6061, 7075 | ASTM, ISO |
Titanium Powder | ASTM B348 | 1-100 microns | Grade 1, Grade 2, Grade 5 | ASTM, ISO |
Stainless Steel Powder | ASTM A240 | 1-200 microns | 304L, 316L, 17-4PH | ASTM, ISO |
Iron Powder | ASTM A131 | 1-200 microns | A, D, E grades | ASTM, ISO |
Copper Powder | ASTM B187 | 1-150 microns | C11000, C12200 | ASTM, ISO |
Nickel Powder | ASTM B160 | 1-150 microns | Ni 200, Ni 201 | ASTM, ISO |
Cobalt Powder | ASTM F75 | 1-200 microns | CoCr, CoCrMo | ASTM, ISO |
Tungsten Powder | ASTM B777 | 1-100 microns | W1, W2, W3 | ASTM, ISO |
Chromium Powder | ASTM B550 | 1-200 microns | 99.9% purity | ASTM, ISO |
Zinc Powder | ASTM B6 | 1-150 microns | SHG, HG, PW | ASTM, ISO |
Suppliers and Pricing Details
Finding the right supplier is essential for getting quality materials at competitive prices. Here are some leading suppliers and their pricing details for different metal powders.
Metal Powder | Suppliers | Price Range (per kg) |
---|---|---|
Aluminum Powder | Valimet, Toyal America, Tekna | $15 – $40 |
Titanium Powder | Arcam AB, AP&C, Praxair Surface Technologies | $100 – $300 |
Stainless Steel Powder | Carpenter Technology, Höganäs, Sandvik | $50 – $150 |
Iron Powder | Höganäs, Rio Tinto Metal Powders, JFE Steel | $10 – $30 |
Copper Powder | GGP Metal Powder, SCM Metal Products, American Elements | $20 – $50 |
Nickel Powder | Vale, American Elements, SMM Group | $40 – $100 |
Cobalt Powder | Umicore, Freeport Cobalt, Hanrui Cobalt | $60 – $150 |
Tungsten Powder | Global Tungsten & Powders, H.C. Starck | $200 – $500 |
Chromium Powder | Metal Powder Supply, American Elements | $50 – $120 |
Zinc Powder | EverZinc, Grillo-Werke AG, American Elements | $5 – $20 |
Pros and Cons of Metal Powders
Every material has its strengths and weaknesses. Here’s a comparison of the pros and cons of different metal powders to help you make informed decisions.
Metal Powder | Pros | Cons |
---|---|---|
Aluminum Powder | Lightweight, corrosion-resistant, conductive | Lower strength compared to some metals |
Titanium Powder | High strength-to-weight ratio, biocompatible | Expensive, difficult to process |
Stainless Steel Powder | High strength, corrosion-resistant, durable | Expensive, high density |
Iron Powder | Cost-effective, magnetic, strong | Prone to rust, relatively heavy |
Copper Powder | Excellent conductivity, corrosion-resistant | Expensive, relatively soft |
Nickel Powder | Corrosion-resistant, high strength, magnetic | Expensive, can cause allergic reactions |
Cobalt Powder | High temperature resistance, magnetic | Very expensive, limited supply |
Tungsten Powder | Extremely high melting point, very strong | Very expensive, difficult to work with |
Chromium Powder | Hard, corrosion-resistant, high melting point | Brittle, expensive |
Zinc Powder | Corrosion-resistant, low melting point | Lower strength, can be toxic |
Detailed Comparisons and Insights
Aluminum Powder vs. Titanium Powder
When comparing aluminum powder to titanium powder, we see some clear distinctions:
- Weight: Aluminum is lighter than titanium, making it more suitable for applications where weight is a critical factor.
- Strength: Titanium has a higher strength-to-weight ratio, which is ideal for high-stress applications like aerospace and medical implants.
- Cost: Aluminum is generally less expensive than titanium, which can be a deciding factor for budget-conscious projects.
Stainless Steel Powder vs. Iron Powder
Stainless steel powder and iron powder also have unique differences:
- Corrosion Resistance: Stainless steel is much more corrosion-resistant than iron, making it suitable for harsh environments.
- Strength: Both materials are strong, but stainless steel has the edge due to its alloying elements like chromium and nickel.
- Cost: Iron powder is typically less expensive, which can be a benefit for large-scale industrial applications.
Copper Powder vs. Nickel Powder
Comparing copper powder to nickel powder highlights their distinctive properties:
- Conductivity: Copper is an excellent conductor of electricity, making it ideal for electrical and electronic applications.
- Corrosion Resistance: Nickel offers better corrosion resistance, which is crucial for aerospace and battery applications.
- Magnetic Properties: Nickel is magnetic, while copper is not, which can influence material selection based on application requirements.
FAQs
Q: What are the most common applications for aluminum powder?
A: Aluminum powder is commonly used in automotive parts, aerospace components, paints, and pyrotechnics due to its lightweight and corrosion-resistant properties.
Q: Why is titanium powder so expensive?
A: Titanium powder is expensive because of its high strength-to-weight ratio and biocompatibility, making it ideal for specialized applications like aerospace and medical implants.
Q: How is stainless steel powder different from iron powder?
A: Stainless steel powder contains alloying elements like chromium and nickel, making it more corrosion-resistant and durable compared to iron powder.
Q: What makes copper powder a good choice for electrical components?
A: Copper powder has excellent electrical conductivity and corrosion resistance, making it ideal for use in electrical components and electronics.
Q: Can nickel powder cause allergic reactions?
A: Yes, nickel powder can cause allergic reactions in some individuals, which is an important consideration for applications involving direct skin contact.
Q: What industries commonly use cobalt powder?
A: Cobalt powder is commonly used in the aerospace industry for superalloys, in batteries, and in magnetic materials due to its high temperature resistance and magnetic properties.
Q: Why is tungsten powder preferred for cutting tools?
A: Tungsten powder has an extremely high melting point and exceptional strength, making it ideal for use in cutting tools that need to withstand high temperatures and wear.
Q: Is chromium powder brittle?
A: Yes, chromium powder is hard and corrosion-resistant but also brittle, which can be a limitation in some applications.
Q: What are the safety considerations for handling zinc powder?
A: Zinc powder can be toxic if inhaled or ingested in large quantities, so proper safety measures, including protective equipment and ventilation, are essential when handling it.
Conclusion
Understanding the different types of metal powders, their properties, applications, and how they compare to one another is crucial for making informed decisions in engineering and manufacturing. Whether you’re selecting a material for a high-performance aerospace component, a durable medical implant, or an efficient electrical component, the right choice of metal powder can significantly impact the success of your project.
By exploring specific metal powder models like aluminum, titanium, stainless steel, iron, copper, nickel, cobalt, tungsten, chromium, and zinc, and comparing their pros and cons, you can better understand their unique advantages and limitations. This knowledge will help you select the most suitable material for your needs, ensuring the quality and performance of your final product.
Remember, the key to choosing quality materials is not just about understanding their technical specifications but also considering their practical applications, cost, and overall performance in real-world scenarios. So, next time you’re faced with a material selection decision, refer back to this guide to make a well-informed choice.
Share On
MET3DP Technology Co., LTD is a leading provider of additive manufacturing solutions headquartered in Qingdao, China. Our company specializes in 3D printing equipment and high-performance metal powders for industrial applications.
Inquiry to get best price and customized Solution for your business!
Related Articles
About Met3DP
Recent Update
Our Product
CONTACT US
Any questions? Send us message now! We’ll serve your request with a whole team after receiving your message.
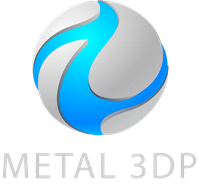
Metal Powders for 3D Printing and Additive Manufacturing