Quality Metal Powder
Table of Contents
Imagine a world without metal. Our cars, buildings, appliances, even the coins in your pocket – all would vanish. But what if I told you there’s a hidden hero in this metallic landscape? A tiny, unassuming powder that forms the foundation for countless objects: quality metal powder.
In this comprehensive guide, we’ll delve into the fascinating world of metal powders. We’ll explore their types, properties, applications, and the factors that define their quality. We’ll even unveil some of the specific models that power modern manufacturing. So, buckle up and get ready to discover the magic behind the metal!
the Composition and Properties of Quality Metal Powder
At its core, metal powder is exactly what it sounds like – finely divided metal particles. But don’t be fooled by their size. These tiny grains pack a powerful punch, boasting a unique set of properties that make them invaluable in various industries.
Here’s a table summarizing the key characteristics of quality metal powder:
Property | Description |
---|---|
Particle Size and Distribution | Affects flowability, packing density, and final product properties. Ideally, particles should be spherical and have a narrow size distribution for optimal performance. |
Chemical Composition | Determines the final properties of the metal object. High purity is crucial for consistent results and predictable behavior. |
Flowability | The ability of the powder to flow freely, essential for efficient manufacturing processes like additive manufacturing (3D printing). |
Apparent Density | The bulk density of the powder, impacting material handling and storage requirements. |
Sinterability | The ability of the powder particles to bond together during the sintering process (heating without melting) to form a solid object. |
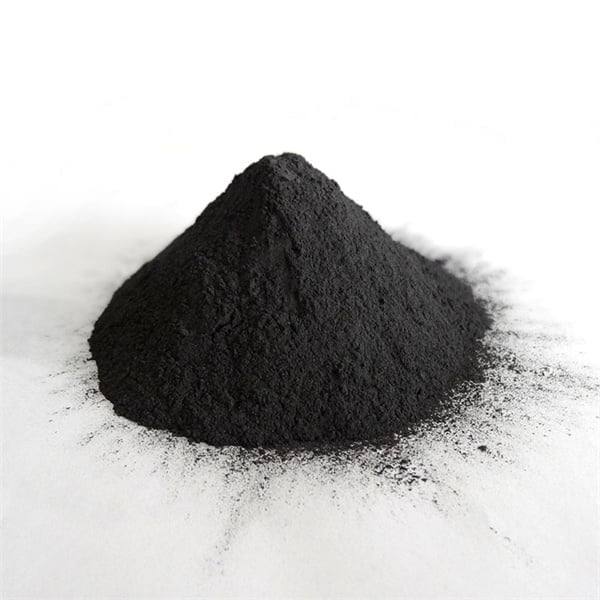
Common Types of Quality Metal Powder
Metal powders come in a vast array, each with its own unique properties and applications. Here are ten specific models to illustrate the variety:
- 316L Stainless Steel Powder: An austenitic stainless steel known for its excellent corrosion resistance, making it ideal for applications in harsh environments like medical implants and chemical processing equipment.
- Nickel Alloy Powders (Inconel 625, Inconel 718): High-performance alloys offering exceptional strength, heat resistance, and corrosion resistance. They find use in jet engine components, aerospace parts, and demanding industrial applications.
- Aluminum Powders: Lightweight and with good electrical conductivity, aluminum powders are widely used in electronics, food packaging, and pyrotechnics.
- Titanium Powders: Offering a fantastic combination of strength, low weight, and excellent biocompatibility, titanium powders are perfect for aerospace parts, medical implants, and high-performance sporting goods.
- Copper Powders: Highly conductive and ductile, copper powders are used in electrical applications like heat sinks, motor components, and conductive inks.
- Tool Steel Powders: Formulated for exceptional hardness and wear resistance, tool steel powders are ideal for creating cutting tools, dies, and molds.
- Iron Powders: The workhorse of metal powders, iron powders boast good magnetic properties and are used in applications like electrical components, metal injection molding (MIM), and iron fortification in food.
- Kovar Powders: A unique alloy with a thermal expansion coefficient that closely matches glass, making it perfect for sealing applications in electronics like cathode ray tubes and transistors.
- Molybdenum Powders: High melting point and excellent thermal conductivity make molybdenum powders valuable for crucibles, heating elements, and electrical contacts in high-temperature environments.
- Gold Powders: Beyond its aesthetic appeal, gold powders have valuable electrical properties and are used in electronics, connectors, and biomedical applications.
This list just scratches the surface of the vast array of metal powders available. Each type offers distinct advantages and caters to specific needs.
Applications of Quality Metal Powder
The applications of quality metal powder are truly limitless. They play a crucial role in various industries, shaping the world around us in countless ways. Here’s a table outlining some of the most common uses:
Application | Metal Powders Used |
---|---|
Additive Manufacturing (3D Printing): Metal powders are the building blocks for creating complex 3D printed parts for aerospace, automotive, and medical industries. | Stainless steel, titanium, Inconel, aluminum |
Metal Injection Molding (MIM): A cost-effective way to produce intricate near-net-shape metal parts. | Iron, stainless steel, copper |
Thermal Spraying: Metal powders are used to coat surfaces to improve wear resistance, corrosion resistance, and thermal properties. | Nickel alloys, aluminum, titanium |
the Advantages and Limitations of Quality Metal Powder
Quality metal powder offers a treasure trove of benefits for manufacturers and engineers. Here’s a closer look at some of the key advantages:
- Design Freedom: Unlike traditional subtractive manufacturing techniques (machining, cutting), metal powders enable the creation of complex geometries with intricate details. This design freedom is particularly valuable in additive manufacturing (3D printing), allowing for the production of lightweight, highly functional parts.
- Material Efficiency: Metal powders minimize material waste compared to traditional methods. In 3D printing, for instance, unused powder can often be recycled and reused, reducing material costs and environmental impact.
- Mass Customization: The ease and flexibility of using metal powders make them ideal for producing customized parts in small batches. This allows manufacturers to cater to specific needs and applications without the high costs associated with traditional mass production.
- Lightweighting: Certain metal powders, like aluminum and titanium, are inherently lightweight. This translates to lighter final products, a crucial factor in industries like aerospace and automotive where weight reduction is paramount for fuel efficiency and performance.
- Near-Net-Shape Manufacturing: Techniques like metal injection molding (MIM) utilize metal powders to create parts with minimal post-processing requirements. This reduces production time and costs.
However, metal powders also come with some limitations to consider:
- Cost: High-quality metal powders can be expensive, particularly for precious metals or exotic alloys. This can be a barrier for some applications, especially in high-volume production.
- Process Complexity: Working with metal powders often requires specialized equipment and expertise. Additive manufacturing, for example, necessitates careful parameter control to ensure part quality and consistency.
- Safety Concerns: Metal powders can be flammable or pose inhalation risks. Proper handling and safety procedures are essential when working with these materials.
- Surface Finish: Parts made from metal powders may have a rougher surface finish compared to traditionally machined parts. Post-processing techniques like polishing or machining might be required to achieve a desired finish.
The Importance of Quality: Throughout this discussion, we’ve emphasized the importance of “quality” metal powder. But what exactly does that mean?
Quality refers to the consistency, purity, and overall performance characteristics of the powder. High-quality metal powders offer several advantages:
- Improved Flowability: Powders with a uniform particle size and shape flow freely, ensuring efficient processing in techniques like 3D printing and MIM.
- Enhanced Sinterability: Quality powders readily bond together during the sintering process, leading to stronger and more reliable final parts.
- Reduced Porosity: Minimal air pockets within the powder bed translate to denser final products with improved mechanical properties.
- Predictable Performance: Consistent powder quality ensures predictable results and minimizes production problems.
Finding the Right Fit: Given the vast array of metal powders available, selecting the right one for your application is crucial. Here are some factors to consider:
- Desired Properties: Identify the key properties you need in the final product – strength, weight, corrosion resistance, etc.
- Manufacturing Process: Choose a powder compatible with your chosen manufacturing technique (3D printing, MIM, thermal spraying).
- Cost Considerations: Balance the cost of the powder with the desired performance and production volume.
- Supplier Reputation: Opt for reputable suppliers who can provide consistent quality and reliable technical support.
The Future of Quality Metal Powder
The future of metal powder is bright. As technology advances, we can expect to see:
- Development of new and exotic metal powder alloys: These alloys will offer a wider range of properties, pushing the boundaries of what’s possible in various industries.
- Reduced powder costs: As production methods become more efficient, the cost of metal powders is expected to decrease, making them more accessible for a broader range of applications.
- Simplified processing techniques: Advancements in equipment and process control will make working with metal powders easier and more user-friendly.
- Integration with other technologies: Metal powders will likely be increasingly integrated with other technologies like robotics and automation, leading to more efficient and cost-effective manufacturing processes.
In conclusion, quality metal powder is a transformative material with the potential to revolutionize various industries. By understanding its properties, applications, and limitations, engineers and manufacturers can leverage its power to create innovative and high-performance products. As the technology continues to evolve, the possibilities with metal powder are truly limitless.
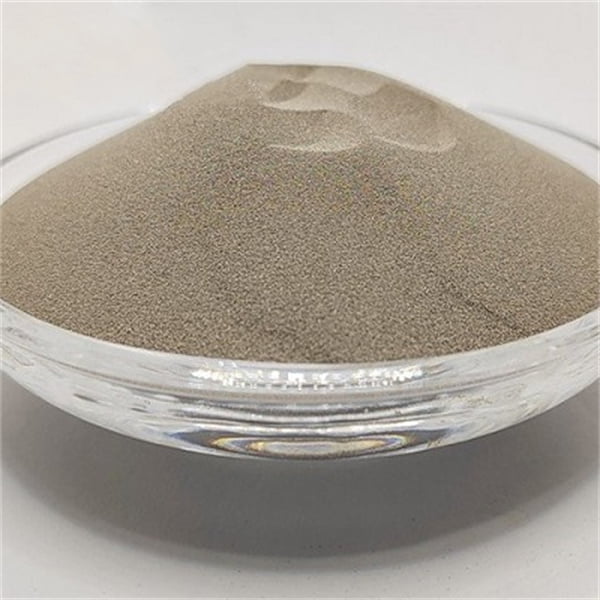
FAQ
Q: What are some safety precautions to take when handling metal powder?
A: Metal powders can be flammable or pose inhalation risks. Here are some safety tips:
- Always wear appropriate personal protective equipment (PPE) like gloves, safety glasses, and a respirator when handling metal powders.
- Work in a well-ventilated area to minimize dust inhalation.
- Properly dispose of used metal powder according to local regulations.
- Educate yourself on the specific safety hazards associated with the type of metal powder you’re using.
Q: How is metal powder manufactured?
A: There are several methods for metal powder production, each with its advantages and limitations. Here are some common techniques:
- Atomization: Molten metal is broken up into fine droplets using a gas or water stream, which rapidly solidify into spherical particles.
- Reduction: Metallic oxides are converted to pure metal powders through a chemical reduction process.
- Electrolysis: An electric current is used to extract metal ions from a solution, depositing them as metal powder on a cathode.
- Mechanical Milling: Bulk metal is crushed and milled into fine particles using high-energy grinding equipment.
The choice of manufacturing method depends on the desired powder properties, metal type, and production scale.
Q: Can metal powder rust?
A: Not all metal powders rust. Rusting is a specific type of corrosion that occurs with iron and steel. However, some metal powders, like aluminum and titanium, can corrode in certain environments. The corrosion resistance of a metal powder depends on its composition and the presence of any protective oxide layers.
Q: Where can I buy quality metal powder?
A: Several reputable suppliers offer various metal powders. It’s crucial to choose a supplier that can provide high-quality powder, technical data sheets, and support for your specific application. Here are some factors to consider when selecting a supplier:
- Reputation: Look for a supplier with a proven track record of providing consistent quality powders.
- Product Range: Ensure the supplier offers the specific type of metal powder you need.
- Technical Expertise: Choose a supplier with knowledgeable staff who can answer your questions and provide technical support.
- Pricing and Availability: Compare prices and lead times from different suppliers to find the best fit for your needs.
Online marketplaces and directories can help you locate potential metal powder suppliers.
By considering these factors, you can find a reliable supplier who can provide the quality metal powder you need to bring your project to life.
Share On
MET3DP Technology Co., LTD is a leading provider of additive manufacturing solutions headquartered in Qingdao, China. Our company specializes in 3D printing equipment and high-performance metal powders for industrial applications.
Inquiry to get best price and customized Solution for your business!
Related Articles
About Met3DP
Recent Update
Our Product
CONTACT US
Any questions? Send us message now! We’ll serve your request with a whole team after receiving your message.
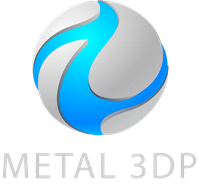
Metal Powders for 3D Printing and Additive Manufacturing