Introduction to Stereolithography (SLA)
Table of Contents
Imagine a world where intricate designs materialize from a vat of liquid resin, layer by painstaking layer, with breathtaking detail and unparalleled smoothness. This isn’t science fiction; it’s the revolutionary realm of Stereolithography (SLA) 3D printing technology.
But what exactly is SLA, and how does it work its magic? Buckle up, because we’re about to embark on a journey into the fascinating world of this additive manufacturing process, where precision meets innovation.
The Process Flow of SLA
Think of SLA as a meticulous sculptor, meticulously building an object one tiny slice at a time. Here’s a breakdown of the process:
- Digital Design: The first step, just like any creative endeavor, is the design. You create a 3D model using CAD software, meticulously detailing every aspect of the object you wish to bring to life.
- Slicing the Design: Imagine a loaf of bread being sliced into thin pieces. Software takes your 3D model and virtually divides it into hundreds, or even thousands, of incredibly thin horizontal layers. Each layer represents a single slice of the final object.
- The Printing Vat: Picture a vat filled with a light-sensitive liquid resin. This resin is the magic potion that transforms from a fluid state to a solid form, creating the building blocks of your masterpiece.
- Laser Beam Dance: Here’s where the real magic happens. An ultraviolet (UV) laser beam acts as a conductor, meticulously tracing the pattern of each layer on the surface of the liquid resin. As the laser sweeps across the resin, it cures (solidifies) the specific areas according to the digital blueprint.
- Layer by Layer: The platform holding the object lowers slightly after each layer is cured. A fresh layer of resin flows over the top, and the laser beam performs its dance once again, solidifying the next slice. This iterative process continues tirelessly, building the object one layer at a time.
- Post-Processing: Once the printing is complete, the platform rises out of the resin bath, revealing your creation in its uncured state. A support removal process might be necessary, depending on the design complexity. Finally, the object undergoes a post-curing stage under UV light to ensure complete solidification and achieve the desired mechanical properties.
The result? A stunningly detailed, high-resolution 3D object with a smooth surface finish, ready to take center stage in your project.
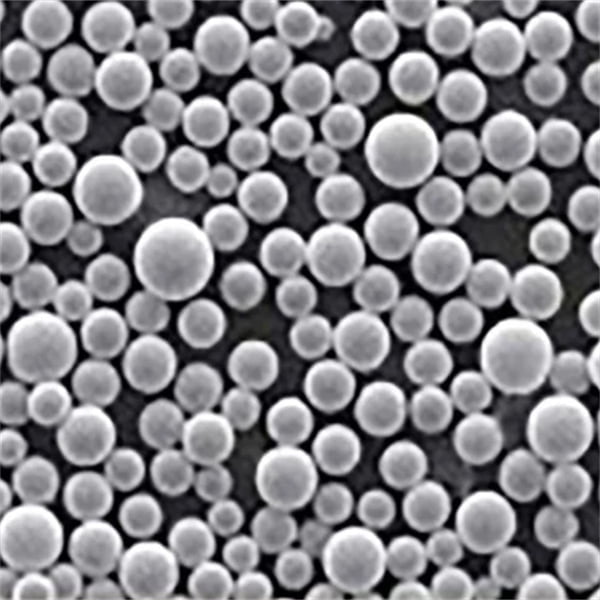
The Advantages of SLA Technology
SLA boasts a unique set of advantages that make it a highly sought-after 3D printing technology for various applications:
- Unmatched Accuracy and Resolution: SLA produces parts with exceptional detail and dimensional accuracy, making it ideal for intricate designs, functional prototypes, and even medical models. Compared to other 3D printing methods like FDM (Fused Deposition Modeling), SLA delivers superior surface quality with minimal layer lines.
- Wide Range of Materials: SLA offers a vast selection of engineering-grade resins with diverse properties. You can choose from materials that are rigid, flexible, biocompatible, or even castable, allowing you to tailor the printed object’s functionality to your specific needs.
- Smooth Surface Finish: Objects printed with SLA have a smooth, almost glass-like finish, eliminating the need for extensive post-processing in many cases. This makes SLA ideal for applications where aesthetics and a professional look are paramount.
- Versatility in Applications: From intricate jewelry designs and dental prosthetics to complex engineering prototypes and end-use parts, SLA’s versatility shines. Its ability to produce highly detailed and functional objects makes it a valuable tool across various industries.
Disadvantages of SLA Technology
While SLA offers a plethora of advantages, it’s essential to consider its limitations before diving in:
- Slower Print Speeds: Compared to some other 3D printing methods, SLA can be a slower process. The layer-by-layer curing with a laser beam can take time, especially for larger objects.
- Material Costs: Engineering-grade resins used in SLA tend to be more expensive than filaments used in FDM printing. This can be a factor when printing large objects or prototypes requiring multiple iterations.
- Post-Processing Requirements: While minimal in some cases, SLA parts may require support structure removal and additional post-processing steps, adding to the overall production time.
- Safety Considerations: Liquid resins used in SLA can be hazardous if not handled properly. It’s crucial to follow safety protocols and wear appropriate personal protective equipment (PPE) when working with SLA printers.
The Applications of SLA Technology
SLA’s ability to produce high-resolution, functional objects with diverse material properties has propelled it to the forefront of various applications. Let’s delve into some of the key areas where SLA shines:
1. Prototyping: SLA’s exceptional accuracy and smooth surface finish make it a perfect fit for creating realistic and functional prototypes. Imagine needing a prototype for a new medical device or a complex mechanical component. SLA allows you to create a highly detailed model that closely resembles the final product, enabling rigorous testing and design iteration before mass production.
Advantages over Other Methods: Compared to traditional prototyping methods like machining or injection molding, SLA offers several advantages. It’s significantly faster and more cost-effective for creating intricate prototypes, especially for complex geometries. Additionally, SLA allows for rapid design changes and quicker turnaround times, accelerating the development process.
Real-world Example: A leading automotive manufacturer utilizes SLA to create prototypes for new car components, such as intricate air vents and gear shift knobs. The high resolution and smooth finish of SLA prototypes allow for detailed testing of form and function, ensuring a seamless user experience in the final product.
2. Healthcare: The medical field has embraced SLA for its ability to produce biocompatible models and prosthetics. Imagine creating custom-made dental implants or intricate anatomical models for surgical planning. SLA allows for the creation of highly detailed and biocompatible objects that meet the specific needs of each patient.
Advantages in Medical Applications: SLA surpasses traditional techniques for medical models by offering unparalleled precision and the ability to create complex structures. For instance, surgeons can utilize SLA-printed models of a patient’s bones to plan complex surgeries with greater accuracy, leading to improved patient outcomes.
Real-world Example: A renowned dental clinic utilizes SLA printing to create custom-fit dentures and implants for their patients. The technology allows for a perfect fit and a natural look, significantly improving patient comfort and satisfaction.
3. Jewelry Design: SLA has become a game-changer in the world of jewelry design. Imagine creating intricate and detailed pieces with exceptional smoothness, ready for casting or direct use. SLA allows designers to bring their creative visions to life with unparalleled precision and detail.
Advantages for Jewelry Makers: Compared to traditional methods like wax carving, SLA offers significant advantages. The technology allows for rapid design iteration and the creation of highly complex and delicate pieces that would be challenging to produce with traditional methods.
Real-world Example: A leading jewelry designer utilizes SLA to create one-of-a-kind, custom-designed pieces for her clients. The high resolution and smooth finish of SLA-printed pieces allow for intricate details and a luxurious look, setting her creations apart from the competition.
4. End-use Parts: Beyond prototyping, SLA’s ability to produce functional parts with various material properties makes it suitable for some end-use applications. Imagine needing a strong, heat-resistant component for a low-volume production run. Certain SLA resins can meet these requirements, offering a viable alternative to traditional manufacturing methods.
Considerations for End-use Parts: While SLA can produce functional parts, it’s crucial to consider factors like material properties, post-processing requirements, and overall production costs compared to traditional methods like injection molding for high-volume production.
Real-world Example: A small manufacturing company utilizes SLA to create custom enclosures for their electronic devices. The SLA process allows them to produce low-volume batches with complex geometries and a high-quality finish, meeting their specific needs without the high upfront costs of traditional injection molding.
These are just a few examples of the diverse applications of SLA technology. As the technology continues to evolve and new materials are developed, we can expect SLA to play an even greater role in various industries, pushing the boundaries of design and innovation.
Exploring Advanced Concepts in SLA
While we’ve covered the core functionalities of SLA, there’s a whole world of advanced concepts and considerations to delve into for those seeking to maximize the potential of this technology.
1. Support Structures in SLA: Imagine building a bridge; you need temporary scaffolding to hold everything in place during construction. Similarly, in SLA printing, support structures are crucial for creating objects with overhangs or unsupported features.
- Types of Support Structures: Several support structure styles exist, each with its advantages and disadvantages. Common types include:
- Light touch supports: These delicate supports minimize contact with the printed object, reducing post-processing time but might not be suitable for very heavy features.
- Heavy duty supports: These provide stronger support for larger overhangs but can leave more prominent marks on the final object.
- Lattice supports: These intricate, web-like structures offer a good balance of strength and minimal post-processing effort.
- Software and Automation: Thankfully, advanced SLA software often features automated support generation tools. These tools analyze the 3D model and suggest optimal support structures, saving time and minimizing manual intervention.
2. Layer Thickness and Resolution: Just like the resolution on your phone screen, SLA printing offers varying layer thicknesses. Thicker layers print faster but can result in a stepped appearance on the final object. Conversely, thinner layers create smoother surfaces but take longer to print.
- Finding the Sweet Spot: The ideal layer thickness depends on the desired balance between print speed, surface quality, and overall object size. For high-detail prototypes, thinner layers are preferred. For larger, less detailed objects, a balance can be struck between speed and acceptable resolution.
3. Resin Vat Care and Maintenance: The resin vat in an SLA printer plays a vital role. Here are some key points to remember:
- Resin Filtering: Over time, resin particles can accumulate in the vat, affecting print quality. Regular filtering of the resin is crucial to maintain optimal performance.
- Vat Lifetime: Resin vats have a finite lifespan and may degrade over time due to exposure to UV light and wear. Regular inspection and replacement when necessary are essential.
- Cleaning Procedures: Proper cleaning of the resin vat after each print job is vital to prevent resin residue buildup and ensure successful subsequent prints.
4. Post-Processing Techniques for SLA:
While SLA offers a smooth surface finish compared to other 3D printing methods, some post-processing techniques might be necessary depending on the application.
- Support Removal: Carefully removing support structures without damaging the printed object is crucial. Tools like tweezers, clippers, and even soaking solutions might be used depending on the support structure type.
- Surface Treatment: In some cases, additional surface treatment techniques like sanding, polishing, or painting might be employed to achieve the desired final finish.
the Potential of SLA Technology
SLA 3D printing technology offers a unique blend of precision, detail, and versatility. From creating intricate prototypes to producing functional end-use parts, SLA empowers designers and manufacturers to bring their innovative ideas to life. As the technology continues to evolve with advancements in materials, software, and printer capabilities, we can expect SLA to play an even greater role in shaping the future of various industries.
Whether you’re a seasoned engineer, a budding entrepreneur, or simply fascinated by the world of 3D printing, SLA technology offers a gateway to a world of possibilities. With its ability to transform digital designs into tangible objects with exceptional detail and functionality, SLA stands as a testament to human ingenuity and its relentless pursuit of pushing the boundaries of creation.
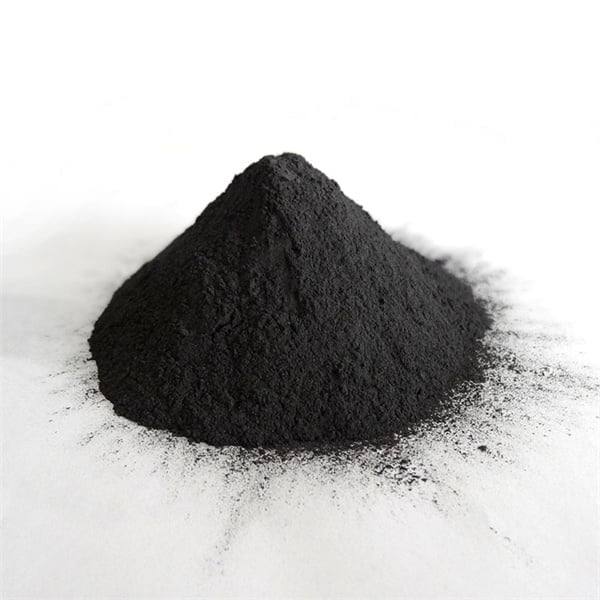
FAQ
What is Stereolithography (SLA)?
Stereolithography (SLA) is a 3D printing technology that uses a laser or projector to cure liquid resin into solid layers, building a 3D object layer-by-layer. It’s one of the oldest and most precise 3D printing methods, known for its high resolution and smooth surface finishes.
How does SLA work?
- Digital Model: The process starts with a 3D model sliced into thin layers.
- Resin Vat: Liquid resin sits in a vat.
- Curing with Light: A laser or projector targets specific areas of the resin, curing (solidifying) them based on the sliced model.
- Layer by Layer: The platform holding the object lowers slightly, and a new layer of resin is applied. The laser cures the next layer on top of the previous one.
- Building the Object: This process repeats until the entire 3D object is complete.
- Post-Processing: The printed object is then cleaned, supported structures are removed, and it may undergo curing with UV light for additional strength.
What are the benefits of SLA?
- High Resolution: SLA produces highly detailed and accurate prints with smooth surface finishes.
- Wide Range of Materials: SLA offers a variety of resins with different properties like strength, flexibility, and biocompatibility.
- Precise Features: SLA is ideal for printing intricate parts and objects with fine details.
What are the drawbacks of SLA?
- Cost: SLA printers and materials tend to be more expensive compared to other 3D printing technologies.
- Resin Handling: Liquid resin can be messy and requires careful handling due to potential health hazards.
- Limited Build Size: Build volumes on SLA printers are often smaller than other 3D printing methods.
What is SLA used for?
- Prototyping: SLA is widely used for creating high-quality prototypes for design, engineering, and product development.
- Jewelry: SLA is used for creating detailed jewelry molds and patterns.
- Medical and Dental: SLA is used for printing custom prosthetics, dental models, and surgical instruments.
Is SLA right for me?
If you need high-precision, detailed prints and prioritize smooth surface finishes, SLA is a great option. However, if you’re on a tight budget or require large prints, other 3D printing technologies might be more suitable.
Share On
MET3DP Technology Co., LTD is a leading provider of additive manufacturing solutions headquartered in Qingdao, China. Our company specializes in 3D printing equipment and high-performance metal powders for industrial applications.
Inquiry to get best price and customized Solution for your business!
Related Articles
About Met3DP
Recent Update
Our Product
CONTACT US
Any questions? Send us message now! We’ll serve your request with a whole team after receiving your message.
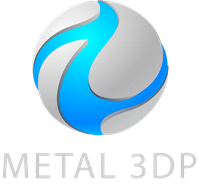
Metal Powders for 3D Printing and Additive Manufacturing