metel power: application of SLM in making medical devices
Table of Contents
Imagine a world where personalized medical devices, tailored to your unique anatomy, can be created with unmatched precision and complexity. This isn’t science fiction; it’s the reality of Selective Laser Melting (SLM), a revolutionary 3D printing technology transforming the future of healthcare.
SLM, also known as Laser Powder Bed Fusion (LPBF), uses a high-powered laser to selectively melt and fuse metal powders, layer by layer, building intricate three-dimensional structures. This innovative process unlocks a plethora of possibilities for manufacturing intricate medical devices with unprecedented customization and functionality.
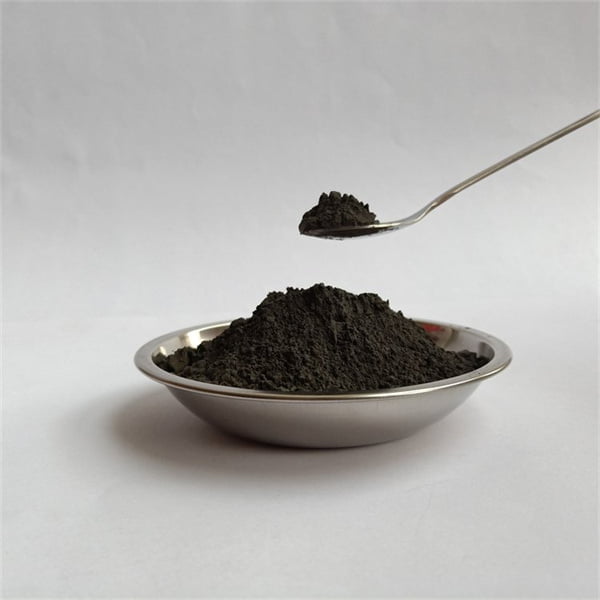
Metal Powders for SLM in Medical Applications
The foundation of SLM technology lies in the metal powders used as building blocks. These powders, with their unique properties and characteristics, play a crucial role in determining the performance and suitability of the final device. Here’s a glimpse into some of the most commonly used metal powders in SLM for medical applications:
Metal Powder | Composition | Properties | Applications |
---|---|---|---|
Titanium Alloy (Ti-6Al-4V) | 90% Titanium, 6% Aluminum, 4% Vanadium | Excellent biocompatibility, high strength-to-weight ratio, good corrosion resistance | Orthopedic implants (e.g., hip and knee replacements), dental implants, craniofacial implants |
Cobalt-Chromium Alloy (CoCrMo) | 60% Cobalt, 25% Chromium, 15% Molybdenum | High wear resistance, good biocompatibility, excellent mechanical properties | Hip and knee replacements, dental restorations, spinal implants |
Stainless Steel (316L) | 66% Iron, 16% Chromium, 10% Nickel, 2% Molybdenum | Affordable, good corrosion resistance, moderate strength | Surgical instruments, medical devices requiring biocompatibility and affordability |
Tantalum | 100% Tantalum | Excellent biocompatibility, high radiopacity (visible on X-rays), good corrosion resistance | Craniofacial implants, dental implants, spinal implants |
Nickel-Titanium (NiTi) | 55% Nickel, 45% Titanium | Shape memory effect, superelasticity, good biocompatibility | Orthodontic braces, stents, vascular grafts |
Beyond the table:
- Titanium Alloy (Ti-6Al-4V): This workhorse material is the gold standard for many medical applications due to its exceptional biocompatibility, lightweight nature, and durability. However, its high cost can be a limiting factor.
- Cobalt-Chromium Alloy (CoCrMo): Offering a balance between affordability and performance, CoCrMo finds favor in various joint replacement applications. While concerns regarding potential nickel release exist, advancements in nickel-free alternatives are ongoing.
- Stainless Steel (316L): This cost-effective option is suitable for medical devices requiring biocompatibility but not subjected to high stress. Its moderate strength necessitates careful design considerations for demanding applications.
- Tantalum: Prized for its excellent biocompatibility and radiopacity, tantalum is ideal for implants requiring visibility during X-ray imaging. However, its high cost and difficulty in machining can be drawbacks.
- Nickel-Titanium (NiTi): This unique material possesses the remarkable ability to remembe its original shape after deformation, making it ideal for orthodontic braces and vascular grafts. However, its processing complexity and potential biocompatibility concerns require further investigation.
This list is not exhaustive, and other metal powders, such as molybdenum and inconel, also find specialized applications in SLM for medical devices. It’s crucial to carefully select the appropriate metal powder based on the specific requirements of the device, considering factors like biocompatibility, mechanical properties, cost, and processing complexity.
Applications of SLM in Making Medical Devices
SLM’s ability to create complex geometries with unmatched precision unlocks a wide range of possibilities in the medical field. Let’s delve into some of the most impactful applications:
SLM can be used to manufacture personalized orthopedic implants:
Imagine custom-designed implants that perfectly match your unique bone anatomy. This is the reality with SLM. By utilizing patient CT scans, surgeons can create personalized implants that seamlessly integrate with the patient’s bone, potentially leading to improved long-term outcomes, reduced risk of rejection, and faster recovery times.
For instance: A patient with a complex fracture requiring a replacement can benefit from a custom-made implant fabricated using SLM. This implant, designed specifically for the patient’s bone structure, can offer a better fit and improved stability, potentially leading to a faster recovery and a more natural range of motion.
SLM can be used to manufacture personalized dental restorations:
Gone are the days of ill-fitting dentures. SLM allows for the creation of highly customized dental implants, crowns, and bridges that perfectly match a patient’s unique dental anatomy. This not only improves aesthetics and functionality but also enhances patient comfort and satisfaction.
For example: A patient requiring a dental implant can receive a custom-designed implant created using SLM. This implant, precisely tailored to the patient’s jawbone, offers superior stability and functionality compared to traditional implants, potentially leading to improved long-term implant success and a more natural-looking smile.
SLM can be used to manufacture complex surgical instruments:
SLM empowers the creation of intricate surgical instruments with unparalleled precision and functionality. These instruments, featuring thin walls, delicate features, and intricate lattice structures, are impossible to manufacture using traditional methods. This opens doors for minimally invasive surgeries with reduced tissue damage, faster recovery times, and improved patient outcomes.
For instance: Surgeons performing delicate neurosurgery can utilize specially designed instruments fabricated using SLM. These instruments, featuring microscopic features and lightweight design, enable greater precision and control during surgery, potentially leading to reduced complications and improved patient outcomes.
SLM can be used to create realistic medical models:
SLM facilitates the creation of highly realistic medical models replicating anatomical structures like bones, organs, and tumors. These models, derived from patient scans, provide surgeons with invaluable pre-operative planning tools. They can be used to simulate surgeries, practice procedures, and improve communication with patients about their conditions and treatment options.
For instance: A surgeon planning a complex jaw reconstruction surgery can utilize a patient-specific model created using SLM. This model allows the surgeon to practice the procedure beforehand, visualize potential challenges, and communicate the surgical plan more effectively with the patient, potentially leading to improved surgical outcomes and reduced patient anxiety.
Beyond the applications:
These are just a few examples of how SLM is revolutionizing medical care. As the technology continues to evolve, we can expect to see even more innovative applications emerge, transforming the way we diagnose, treat, and manage various medical conditions.
Weighing the Benefits of SLM in Medical Device Manufacturing
While SLM offers immense potential, it’s essential to acknowledge its advantages and limitations to gain a holistic understanding of its applicability in the medical field.
Advantages:
- Unmatched precision and complexity: SLM allows for the creation of highly intricate structures with microscopic features, impossible to achieve using traditional manufacturing methods.
- Customization: The ability to personalize medical devices based on individual patient anatomy can significantly improve their fit, functionality, and long-term success.
- Reduced invasiveness: SLM-made surgical instruments enable minimally invasive procedures, leading to faster recovery times and reduced patient discomfort.
- Improved pre-operative planning: SLM-created medical models provide invaluable tools for surgical planning and communication, potentially leading to improved surgical outcomes.
Limitations:
- High cost: SLM machines and metal powders can be expensive, making the technology less accessible to all healthcare institutions.
- Limited material selection: While the range of compatible metal powders is expanding, it’s still not as extensive as those readily available for traditional manufacturing methods.
- Surface roughness: SLM-produced parts can have a rougher surface finish compared to traditionally manufactured counterparts, which may require additional post-processing in certain applications.
- Regulatory considerations: As a relatively new technology, SLM faces ongoing regulatory scrutiny to ensure the safety and efficacy of medical devices produced using this method.
Balancing the scales:
Despite its limitations, the advantages of SLM in creating personalized, highly functional medical devices are undeniable. As the technology matures, costs are expected to decrease, the material selection is likely to broaden, and regulatory pathways will become more established, paving the way for wider adoption of SLM in the medical field.
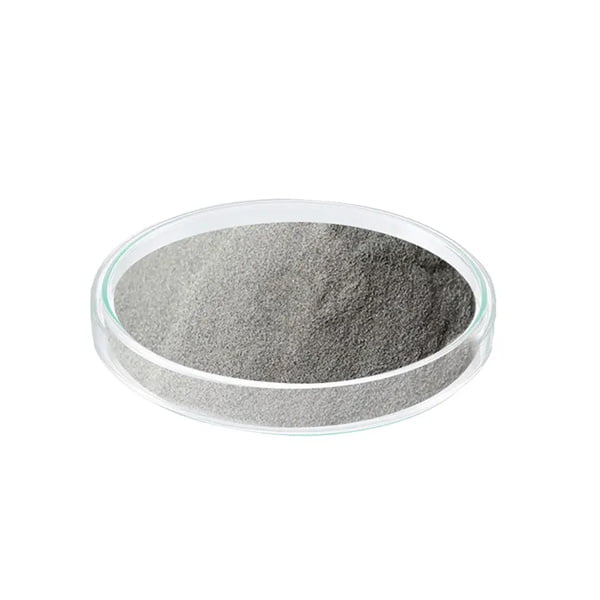
FAQs
1. Is SLM safe for medical devices?
SLM-produced medical devices undergo rigorous testing and regulatory approval to ensure their safety and efficacy. The biocompatibility of the metal powders used is crucial, and ongoing research is focused on developing new materials.
2. How strong are SLM-made medical devices?
The strength of SLM-made devices depends on the specific metal powder used and the design of the device. However, SLM can produce devices with mechanical properties comparable or even exceeding those of traditionally manufactured counterparts.
3. How much do SLM-made medical devices cost?
Currently, SLM-made devices can be more expensive than traditionally manufactured devices due to the higher cost of materials and equipment. However, as the technology matures and adoption increases, costs are expected to decrease.
4. What are the future prospects of SLM in medical device manufacturing?
The future of SLM in medical device manufacturing is bright. With ongoing advancements in technology, materials, and regulations, SLM is poised to play an increasingly important role in creating personalized, functional, and cost-effective medical devices, ultimately improving patient care and outcomes.
Conclusion
SLM represents a paradigm shift in the way we manufacture medical devices. Its ability to create personalized, intricate, and highly functional devices opens doors for personalized medicine and improved patient care. While challenges remain, the future of SLM in the medical field is promising, and its potential to revolutionize healthcare is undeniable. As the technology continues to evolve, we can expect to see even more innovative applications emerge, shaping the future of medicine and ushering in a new era of personalized and effective healthcare.
Share On
MET3DP Technology Co., LTD is a leading provider of additive manufacturing solutions headquartered in Qingdao, China. Our company specializes in 3D printing equipment and high-performance metal powders for industrial applications.
Inquiry to get best price and customized Solution for your business!
Related Articles
About Met3DP
Recent Update
Our Product
CONTACT US
Any questions? Send us message now! We’ll serve your request with a whole team after receiving your message.
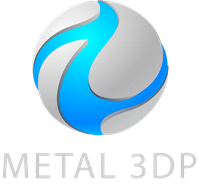
Metal Powders for 3D Printing and Additive Manufacturing