SLM: manufacturing various automotive components
Table of Contents
The Specific Applications of SLM in Aerospace
Imagine building a complex aircraft component, not by welding or machining chunks of metal, but by meticulously layering on microscopic particles with a laser beam. This is the magic of Selective Laser Melting (SLM), a 3D printing technology revolutionizing the aerospace industry.
SLM, also known as Laser Powder Bed Fusion (LPBF), offers a treasure trove of benefits for aerospace manufacturers. It enables the creation of intricate, lightweight parts with exceptional strength-to-weight ratios – a dream combination for building fuel-efficient and high-performance aircraft. But what exactly are these specific applications, and what metal powders are fueling this innovation? Let’s dive deep into the fascinating world of SLM in aerospace.
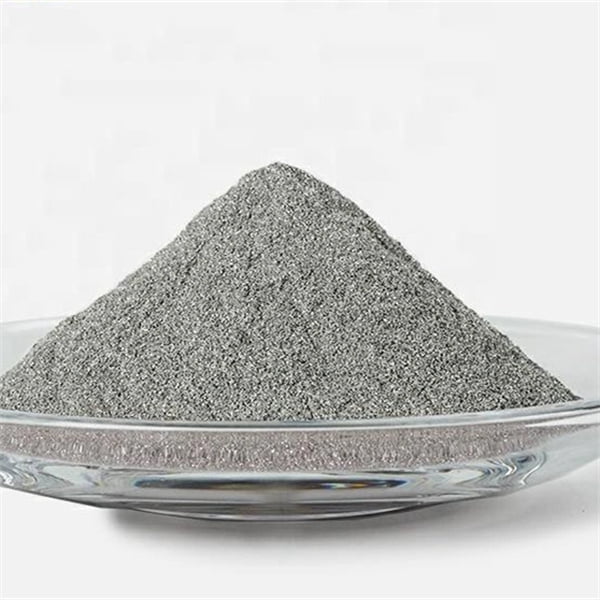
Metal Powders for SLM
The success of SLM hinges on the unique properties of metal powders used in the printing process. These fine, meticulously crafted particles transform from a bed of dust into intricately shaped components under the precise guidance of the laser beam. Here’s a closer look at ten widely used metal powders in aerospace SLM applications:
Metal Powders for SLM in Aerospace
Metal Powder | Composition (wt%) | Key Properties | Applications |
---|---|---|---|
Ti-6Al-4V (Grade 23) | Ti (balance), Al (6.0-6.8), V (3.5-4.5) | High strength-to-weight ratio, excellent biocompatibility | Landing gear components, engine mounts, airframe structures, prosthetic implants (medical applications) |
Inconel 718 | Ni (balance), Cr (17-21), Fe (balance), Nb (5.0-5.5), Mo (2.8-3.3) | High strength, good corrosion resistance, high-temperature performance | Turbine blades, combustor liners, heat exchangers, rocket engine components |
Aluminum AlSi10Mg | Al (balance), Si (9-11), Mg (0.3-0.6) | Good strength, lightweight, excellent weldability | Heat sinks, ducting components, lightweight structural parts |
Maraging Steel 1.2709 (AMS 5644) | Fe (balance), Ni (18-20), Mo (4.8-5.3), Ti (1.7-2.0), Al (0.8-1.2) | High strength, good toughness, excellent dimensional stability | Landing gear components, highly stressed structural parts |
Titanium Ti-6Al-4V ELI (Extra Low Interstitials) | Ti (balance), Al (6.0-6.8), V (3.5-4.5), Low O, N, C, H | High strength, excellent biocompatibility, improved ductility compared to Grade 23 | Medical implants, aerospace components requiring superior fatigue resistance |
Nickel Alloy 282 (Inconel 625) | Ni (balance), Cr (20-23), Mo (5-7), Fe (balance) | Excellent corrosion resistance, high-temperature performance | Exhaust systems, heat exchangers, components exposed to harsh environments |
Aluminum Scalmalloy (AA7075) | Al (balance), Zn (5.6-6.1), Mg (2.1-2.6), Cu (1.2-1.6) | High strength, good machinability | Wing components, fuselage structures, aerospace parts requiring high strength-to-weight ratio |
Cobalt Chrome CoCrMo (ASTM F75) | Co (balance), Cr (27-30), Mo (5-7) | High wear resistance, biocompatible | Hip and knee replacement components (medical applications), jet engine components requiring wear resistance |
Stainless Steel 17-4PH | Fe (balance), Cr (15.5-17.5), Ni (3.0-5.0), Cu (3.0-5.0) | High strength, good corrosion resistance, precipitation hardening | Springs, bearings, aerospace components requiring a combination of strength and corrosion resistance |
Nickel Alloy Rene 41 | Ni (balance), Cr (18-21), Co (9-11), Mo (9-11), Ti (1.0-1.5), Al (0.8-1.2) | High-temperature performance, excellent creep resistance | Turbine blades, combustor liners, aerospace components exposed to extreme temperatures |
The table above provides a glimpse into the diverse metal powders propelling SLM in aerospace. Let’s delve deeper into some key considerations when selecting the right powder for a specific application:
- Strength-to-weight ratio: This is paramount in aerospace, where components need to be incredibly strong yet lightweight to optimize fuel efficiency. Alloys like Ti-6Al-4V and Scalmalloy (AA7075) excel in this category.
- High-temperature performance: Components in jet engines and other high-heat environments demand powders like Inconel 718 and Rene 41, which can withstand extreme temperatures without compromising structural integrity.
- Corrosion resistance: Aircraft need to endure harsh weather conditions. Nickel alloys like Inconel 625 and Stainless Steel 17-4PH offer excellent resistance to corrosion.
- Biocompatibility: For aerospace applications that dovetail with medical fields, like prosthetic implants, powders like Ti-6Al-4V ELI become crucial due to their biocompatible nature.
- Weldability: If post-processing techniques like welding are part of the manufacturing process, powders like Aluminum AlSi10Mg are preferred for their good weldability.
Beyond the table, here are some additional factors to consider when choosing a metal powder for SLM:
- Powder flowability: The powder needs to flow freely and consistently for optimal layer formation during the printing process.
- Laser absorptivity: The powder’s ability to absorb the laser beam’s energy efficiently is crucial for proper melting and bonding of particles.
- Surface roughness: The desired surface finish of the final component can influence the choice of powder, as some powders result in rougher surfaces compared to others.
Selecting the optimal metal powder is a vital step in ensuring the success of an SLM project in aerospace. By carefully considering the application’s specific requirements and the properties of available powders, manufacturers can unlock the full potential of this transformative technology.
SLM in Action: Taking Flight with Specific Applications
SLM’s ability to create complex geometries with exceptional precision has opened doors for a multitude of applications in the aerospace industry. Here are some key areas where SLM is making significant strides:
SLM can be used to manufacture various engine components:
- Turbine blades: The intricate internal cooling channels of turbine blades are ideal candidates for SLM. This allows for lighter and more efficient blade designs, contributing to improved engine performance.
- Combustor liners: These components are exposed to extreme temperatures and require high-temperature resistant materials like Inconel 718. SLM enables the creation of complex cooling channels within the liners, enhancing their durability and efficiency.
- Heat exchangers: SLM facilitates the manufacturing of heat exchangers with intricate internal flow paths, optimizing heat transfer within aircraft engines.
SLM can be used for manufacturing airframe structures:
- Landing gear components: SLM allows for the creation of lightweight yet high-strength landing gear components using alloys like Ti-6Al-4V and Maraging Steel.
- Wing components: SLM can be used to manufacture lightweight and structurally sound wing components from aluminum alloys like Scalmalloy (AA7075).
- Fuselage structures: SLM offers the potential to create complex and lightweight fuselage structures, contributing to overall aircraft weight reduction.
SLM can be used for manufacturing other aerospace components:
- Satellite components: The ability to create highly customized and lightweight satellite parts makes SLM a valuable tool in the space industry.
- Unmanned aerial vehicles (UAVs): SLM is well-suited for manufacturing lightweight and high-performance components for UAVs.
- Rocket engine components: SLM can produce complex and high-temperature resistant components for rocket engines using alloys like Rene 41.
The applications of SLM in aerospace are continuously expanding as the technology matures and the range of suitable metal powders broadens. This promises to revolutionize aircraft design and manufacturing, leading to a new generation of fuel-efficient, lightweight, and high-performing aircraft.
SLM offers several additional advantages for the aerospace industry
- Design freedom: SLM enables the creation of complex geometries that would be difficult or impossible to manufacture using traditional methods like machining or casting. This opens doors for lightweight designs with internal lattices and channels, optimizing performance and fuel efficiency.
- Weight reduction: A core tenet of aerospace engineering is achieving the highest strength-to-weight ratio possible. SLM facilitates the use of lightweight metal alloys like titanium and aluminum, significantly reducing aircraft weight compared to traditional manufacturing techniques. Lower weight translates to improved fuel efficiency, increased range, and enhanced payload capacity.
- Part consolidation: SLM allows for the consolidation of multiple parts into a single component. This simplifies manufacturing processes, reduces assembly time and costs, and minimizes potential failure points in the final product.
- Inventory reduction: With on-demand manufacturing capabilities, SLM minimizes the need for large stockpiles of spare parts. This reduces inventory costs and improves logistics for aerospace companies.
- Rapid prototyping: The ability to quickly create functional prototypes using SLM accelerates the design and development process in the aerospace industry. This allows engineers to test and iterate on designs more efficiently, leading to faster innovation cycles.
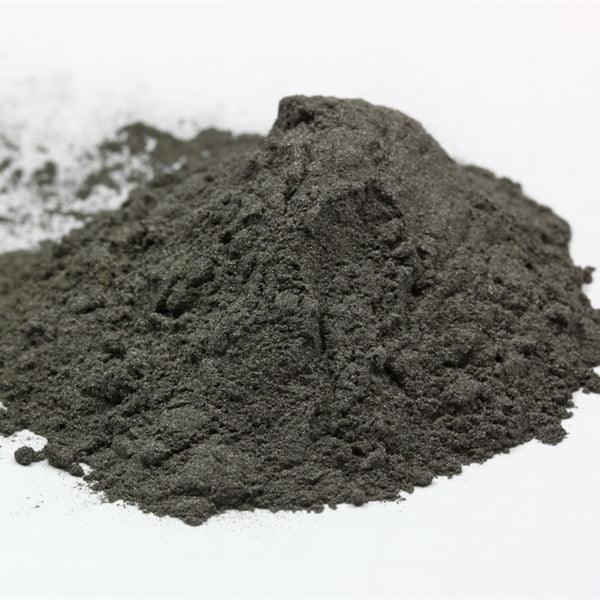
However, SLM in aerospace also comes with some considerations:
- Cost: SLM machines and metal powders can be expensive, making this technology costlier than traditional manufacturing methods for high-volume production.
- Surface roughness: SLM-produced parts can have a rougher surface finish compared to machined components. Post-processing techniques like machining or polishing may be required to achieve the desired surface quality.
- Part size limitations: Current SLM machines have limitations on the size of parts they can produce. This may restrict the use of SLM for certain large-scale aerospace components.
- Powder quality: The quality and consistency of the metal powder used in SLM significantly impact the mechanical properties of the finished part. Strict quality control measures are essential for successful SLM applications.
Despite these considerations, the advantages of SLM are propelling its adoption in the aerospace industry. As technology advances, costs decrease, and powder quality improves, SLM is poised to transform aircraft design and manufacturing, paving the way for a new era of fuel-efficient, lightweight, and high-performance air travel.
FAQ
Q: What are the main benefits of using SLM in aerospace?
A: The primary benefits include design freedom for complex geometries, weight reduction for improved fuel efficiency, part consolidation for simplified manufacturing, and rapid prototyping for faster design cycles.
Q: What are some of the challenges associated with SLM in aerospace?
A: The main challenges include higher costs compared to traditional methods, potential for rough surface finishes, limitations on part size, and the critical dependence on high-quality metal powders.
Q: What types of metal powders are commonly used in SLM for aerospace applications?
A: Widely used metal powders include Ti-6Al-4V (for strength and biocompatibility), Inconel 718 (for high temperature resistance), Aluminum AlSi10Mg (for good strength and weldability), and Maraging Steel (for high strength and dimensional stability).
Q: What is the future of SLM in the aerospace industry?
A: The future looks bright! As technology advances, costs decrease, and the range of suitable metal powders expands, SLM is expected to play an increasingly significant role in revolutionizing aircraft design and manufacturing for the next generation of aerospace vehicles.
Share On
MET3DP Technology Co., LTD is a leading provider of additive manufacturing solutions headquartered in Qingdao, China. Our company specializes in 3D printing equipment and high-performance metal powders for industrial applications.
Inquiry to get best price and customized Solution for your business!
Related Articles
About Met3DP
Recent Update
Our Product
CONTACT US
Any questions? Send us message now! We’ll serve your request with a whole team after receiving your message.
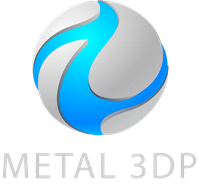
Metal Powders for 3D Printing and Additive Manufacturing