SLM 3D Printing Technology
Table of Contents
Overview of SLM 3D Printing
SLM (selective laser melting) is an additive manufacturing or 3D printing technology that uses a laser to fuse metallic powders into solid 3D objects. SLM is suited for processing reactive and high-strength metals like titanium, aluminum, stainless steel, cobalt-chrome, and nickel alloys into functionally dense parts with intricate geometries.
SLM 3D printing works by selectively melting successive layers of metal powder on top of each other using a focused laser beam. The laser fully melts and fuses particles in locations defined by the CAD model slice. After each layer is scanned, a fresh coating of powder is applied and the process repeats until the full part is built up. Parts made by SLM exhibit properties comparable or superior to traditional manufacturing.
SLM is valued for its ability to produce dense, lightweight, and complex metal components with enhanced mechanical properties and shapes not feasible by conventional methods. Read on for an in-depth guide on SLM 3D printing covering its key characteristics, applications, specifications, suppliers, costs, pros and cons, and more.
Main Features of SLM Technology
Characteristic | Description |
---|---|
Precision | SLM can build extremely intricate and delicate structures with small features down to 30 μm resolution. |
Complexity | Unrestricted by tooling, SLM can create complex shapes like lattices, internal channels, and optimized topology. |
Density | SLM produces over 99% dense metal parts with material properties approaching wrought metals. |
Surface Finish | While post-processing may be needed, SLM offers 25-35 μm Ra surface roughness. |
Accuracy | SLM exhibits ±0.1-0.2% dimensional accuracy and ±0.25-0.5% tolerances. |
Single Step | SLM forms fully functional parts directly from a 3D model without additional tooling steps. |
Automation | The SLM process is automated and minimal manual labor is required. Less waste too. |
Customization | SLM allows fast, flexible, and cost-effective customization and iterations. |
Main Applications of SLM 3D Printing
SLM is best suited for small to medium sized production volumes where complexity and customization are needed. It sees broad use for metal prototypes as well as end-use production parts across diverse industries. Some major applications include:
Area | Uses |
---|---|
Aerospace | Turbine blades, engine parts, lattice structures. |
Automotive | Lightweighting components, custom brackets, complex port designs. |
Medical | Patient-specific implants, prosthetics, surgical tools. |
Dental | Crowns, bridges, implants made of biocompatible cobalt-chrome. |
Tooling | Injection molding tools with conformal cooling channels. |
Jewelry | Intricate designs and structures using precious metals. |
Defense | Lightweight components for vehicles, aircraft, and body armor inserts. |
The technology is widely used in industries like aerospace, defense, automotive, and healthcare for its capability to produce fully functional metal parts with enhanced mechanical properties and complex geometries.
SLM Design Guidelines and Specifications
Proper part design is critical for avoiding SLM production issues like residual stresses, distortion, poor surface finish, and lack of fusion defects. Items to consider include:
Design Aspect | Guidelines |
---|---|
Minimum Wall Thickness | ~0.3-0.5 mm to avoid collapse and excess residual stress. |
Hole Size | >1 mm diameter to allow unfused powder removal. |
Supported Angles | Avoid angles below 30° from horizontal which require supports. |
Hollow Sections | Include escape holes for powder removal from internal cavities. |
Surface Finish | Design orientation and post-processing needed for critical surfaces. |
Supports | Use heat conductive cylinder or lattice supports to prevent part distortion. |
Text | Emboss text at 0.5-2 mm height for legibility. |
Tolerances | Account for +/- 0.1-0.2% size accuracy and anisotropic effects. |
By following design for additive manufacturing (DFAM) principles, parts can be optimized to fully utilize SLM’s benefits in complexity, weight reduction, performance gains, and consolidation of components.
SLM System Size Specifications
Parameter | Typical Range |
---|---|
Build Envelope | 100-500 mm x 100-500 mm x 100-500 mm |
Laser Power | 100-500 W |
Layer Thickness | 20-100 μm |
Beam Size | 30-80 μm |
Scanning Speed | Up to 10 m/s |
Inert Chamber Size | 0.5-2 m diameter |
SLM systems feature a chamber filled with inert gas, a powder recoater mechanism, and a high power laser focused into a tiny spot for melting the metal powder layers. Larger build volumes and higher laser power support bigger parts and faster build speeds.
SLM Process Parameters
Variable | Role |
---|---|
Laser Power | Melting and fusion of the powder particles. |
Scan Speed | Controlling overall energy input and cooling rates. |
Hatch Spacing | Overlapping melt pools for uniform consolidation. |
Layer Thickness | Resolution and surface roughness. |
Focus Offset | Laser spot size and penetration depth. |
Scanning Strategy | Even distribution of heat and residual stresses. |
Optimizing SLM process parameters helps achieve maximum part density, minimum defects, controlled microstructure and mechanical properties, good surface finish, and geometric accuracy.
SLM Powder Requirements
Characteristic | Typical Specification |
---|---|
Material | Stainless steel, aluminum, titanium, cobalt chrome, nickel alloys. |
Particle Size | 10-45 μm typical range. |
Size Distribution | D90/D50 ratio < 5. Narrow distribution for flowability. |
Morphology | Spheroidal or potato shaped particles with low satellites. |
Purity | >99.5% with low oxygen, nitrogen, and hydrogen. |
Apparent Density | 40-60% for good powder flow and packing density. |
High purity, spherical powders with controlled particle size distribution and morphology are required for high density and quality parts by SLM. Powders meeting these criteria allow smooth recoating during the layerwise build process.
SLM Post-Processing Steps
While SLM produces near net-shape parts, some post-processing is typically needed:
Method | Purpose |
---|---|
Powder Removal | Clean loose powder from internal cavities. |
Support Removal | Cut away support structures used to anchor part. |
Surface Finishing | Reduce roughness via bead blasting, CNC machining, polishing, etc. |
Heat Treatment | Relieve stresses and achieve desired mechanical properties. |
Hot Isostatic Pressing | Close residual porosity, homogenize structure. |
Post-processing via multi-axis CNC machining, grinding, polishing, etching, and other surface finishing methods help achieve critical dimensions, smooth surface finish, and aesthetics required by the final application.
Cost Analysis of SLM Printing
Cost Factor | Typical Range |
---|---|
Machine Price | $100,000 to $1,000,000+ |
Material Price | $100 to $500 per kg |
Operating Cost | $50 to $500 per build hour |
Labor | Machine operation, post-processing |
Powder Recycling | Can reduce material costs significantly |
The main costs of SLM printing stem from the initial system purchase, materials, machine operation and labor. Larger production runs offer economy of scale benefits. Recycling unused powder mitigates material expenses.
Choosing an SLM 3D Printer Supplier
Considerations | Guidance |
---|---|
Printer Models | Compare build volume, materials, accuracy, speed specs. |
Manufacturer Reputation | Research experience, customer reviews and case studies. |
Service and Support | Consider training, maintenance contracts, responsiveness. |
Software Capabilities | Assess ease of use, flexibility and features. |
Production Throughput | Match production volumes and lead time needs. |
Quality Procedures | Review repeatability, quality assurance steps, and part validation. |
Post-Processing Offered | Availability of hot isostatic pressing, surface finishing, etc. |
Leading SLM system manufacturers include EOS, 3D Systems, SLM Solutions, Renishaw, and AMCM. When selecting a supplier, evaluate machine specifications, manufacturer reputation, quality procedures, services, and costs.
Pros and Cons of SLM Printing
Advantages | Disadvantages |
---|---|
Complex geometries beyond other methods | Small build volumes limit part size |
Rapid design iterations | Slow process for mass production |
Consolidated lightweight components | High machine and material costs |
Exceptional mechanical properties | Limited material options |
Reduced waste | May require support structures |
Just-in-time manufacturing | Post-processing often required |
SLM 3D printing delivers unprecedented design freedom, part consolidation, lightweight strength, and customization potential. Downsides include system costs, slow speeds, size constraints, and material limitations.
FAQ
Here are answers to some common questions about selective laser melting technology:
What materials can you print with SLM?
SLM is suited for reactive and high-strength metals including stainless steel, aluminum, titanium, cobalt-chrome, nickel alloys, and more. Each system is designed for specific material capabilities.
How accurate is SLM printing?
SLM offers accuracies of around ±0.1-0.2% with surface finishes from 25-35 μm Ra depending on the material, parameters, and part geometry. Resolution is as fine as 30 μm.
How strong are SLM printed parts?
SLM produces over 99% dense metal parts with material strengths comparable or superior to conventional manufacturing methods for metals.
What are some example components made by SLM?
SLM sees broad use in aerospace, medical, dental, automotive and other industries for items like turbine blades, implants, injection molds, and lightweight brackets.
What size parts can SLM print?
Typical SLM build volumes range from 100-500 mm x 100-500 mm x 100-500 mm. Larger systems exist for bigger parts. Size is limited by the chamber and required supports.
How long does SLM printing take?
Build times range from hours to a couple days depending on factors like the part size, layer thickness, and number of components packed in the platform. SLM prints metal at 5-100 cm3/hour rates.
Does SLM require supports?
Minimal support structures are often needed during SLM printing. They act as anchors and thermal conductors to prevent deformation during the build. Supports are removed after printing.
What temperatures does SLM reach?
The localized laser in SLM can briefly reach up to 10,000 °C at the melt pool, rapidly cooling to form solidified metal. The chamber operates below 100 °C.
What makes SLM different from other 3D printing?
SLM uses a laser to fully melt metal powder into dense, functional parts. Other metal 3D printing like binder jetting uses glues and sintering which produce more porous results.
What are the main steps in the SLM process?
- CAD model is digitally sliced into layers
- Powder is rolled across the build platform
- Laser scans each layer fusing powder particles
- Steps 2-3 repeat until part is complete
- Post-processing like supports removal and surface finishing
What powder is used in SLM?
SLM uses fine 10-45 μm metal powders with spherical morphology and a controlled particle size distribution. Common materials are stainless steel, titanium, aluminum, nickel alloys and more.
What industries use SLM printing?
Aerospace, medical, dental, automotive, tooling, and jewelry industries utilize SLM technology for its ability to produce complex, customizable metal parts with high precision and strength.
How expensive is SLM printing?
SLM has high systems costs from $100,000 – $1,000,000+. Materials are $50-500/kg. Economies of scale kick in for larger production volumes. Operating costs range $50-500/hour.
What safety precautions are needed with SLM?
SLM involves laser hazards, hot surfaces, reactive fine metal powders, and potential emissions. Proper laser safety, inert gas ventilation, and personal protective equipment must be used.
Conclusion
SLM additive manufacturing delivers extraordinary capabilities for producing dense, robust metal components with structural integrity similar to machined parts. It expands the design freedom, complexity, customization, lightweighting and consolidation possible relative to traditional fabrication approaches. However, the process comes with significant system costs and slow build speeds.
With continuing advancements in materials, quality, build size, accuracy, software, and parameters, SLM adoption for end-use production applications across aerospace, medical, dental, automotive and other sectors is accelerating. By leveraging the advantages of SLM while being mindful of its limitations, manufacturers can implement it for competitive advantages.
Share On
MET3DP Technology Co., LTD is a leading provider of additive manufacturing solutions headquartered in Qingdao, China. Our company specializes in 3D printing equipment and high-performance metal powders for industrial applications.
Inquiry to get best price and customized Solution for your business!
Related Articles
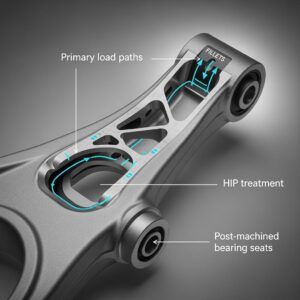
Metal 3D Printing for U.S. Automotive Lightweight Structural Brackets and Suspension Components
Read More »About Met3DP
Recent Update
Our Product
CONTACT US
Any questions? Send us message now! We’ll serve your request with a whole team after receiving your message.