SLM Additive Manufacturing
Table of Contents
Overview of SLM Additive Manufacturing
Selective laser melting (SLM) is an additive manufacturing technology that uses a laser to selectively melt and fuse metallic powder material layer by layer to build up 3D objects. SLM is suited for processing reactive metals like titanium, aluminum, and stainless steel into fully dense and functional parts with complex geometries.
SLM offers several benefits compared to traditional manufacturing:
Benefits of SLM Additive Manufacturing
Benefit | Description |
---|---|
Design freedom | SLM can produce complex geometries like lattices, internal channels, and organic shapes not possible with machining |
Customization | Parts can be easily customized and optimized for function rather than manufacturability constraints |
Lightweighting | Organic shapes and lattices allow parts to be lightweight while retaining strength |
Material savings | SLM only uses the required amount of material versus machining from solid blocks |
Fast prototyping | Parts can be directly 3D printed from CAD vs. tooling for prototyping |
Just-in-time production | On-demand printing as needed reduces inventory costs |
Supply chain resilience | Distributed manufacturing reduces supply chain risks |
However, SLM also comes with some limitations:
Limitations of SLM Additive Manufacturing
Limitation | Description |
---|---|
Machine costs | Industrial SLM machines have high upfront capital costs of $100K-$1M+ |
Material options | Currently limited to reactive metals like titanium, aluminum, tool steels, and superalloys |
Accuracy | Typical accuracy of 0.1-0.2mm is lower than machining tolerances |
Surface finish | As-printed surface is rough and requires post-processing |
Build size | Maximum part size is restricted by printer chamber size |
Low batch production | Most economical for small batch and custom parts vs. mass production |
Post-processing | Additional steps like supports removal, heat treatment required |
How SLM 3D Printing Works
SLM is an powder bed fusion technology that uses a focused laser beam to selectively melt and fuse metallic powder material layer by layer.
The key steps in the SLM process are:
SLM 3D Printing Process
Step | Description |
---|---|
3D Model | A 3D CAD model is digitally sliced into layers |
Spread Powder | A recoater blade spreads a thin layer of powder across the build platform |
Laser Melting | A laser beam traces each layer melting powder to bond it based on the sliced CAD data |
Lower Platform | The build platform lowers and another layer of powder is spread on top |
Repeat Steps | The layer melting process is repeated until the full part is built up |
Remove Part | The completed 3D printed part is removed from the powder bed |
Post-Process | The part is cleaned and heat treated to relieve stresses |
SLM Materials
SLM is capable of processing a range of reactive metals into fully dense parts including:
SLM Materials
Material | Key Properties | Applications |
---|---|---|
Titanium Alloys | High strength-to-weight ratio, biocompatibility | Aerospace, medical implants |
Aluminum Alloys | Lightweight, high strength | Automotive, aerospace |
Stainless Steels | Corrosion resistance, high strength | Industrial tooling, marine |
Tool Steels | High hardness, heat resistance | Injection molds, dies |
Nickel Superalloys | Heat and corrosion resistance | Turbine blades, rocket nozzles |
Cobalt Chrome | Wear resistance, biocompatibility | Dental implants, orthopedics |
The most common SLM materials are titanium and aluminum alloys, along with tool steels and stainless steels. More exotic superalloys and metal composites can also be processed with SLM technology.
SLM Design Guidelines
To successfully design parts for SLM 3D printing, engineers should follow these guidelines:
SLM Design Guidelines
Guideline | Description |
---|---|
Avoid overhangs | Minimize overhangs requiring supports which must be removed |
Design anchors | Include small anchors or tabs to secure the part to the build plate |
Orient for strength | Align the part to maximize strength in functional direction |
Minimize part height | Orient to minimize Z-height to avoid collapsing delicate features |
Allow for post-machining | Add 0.1-0.3mm allowance for post-processing if tight tolerances needed |
Optimize lattice designs | Tune cell size and strut size to part loads and SLM constraints |
Include vent holes | Add small holes to prevent trapped powder causing defects |
Conformal cooling channels | Design complex internal cooling channels not possible with drilling/machining |
Combine parts | Consolidate assemblies into single parts to reduce assembly requirements |
Following these guidelines helps avoid common SLM print defects like poor surface finish, distortion, cracking, or trapped powder.
SLM Printer Manufacturers
The major SLM system manufacturers include:
SLM 3D Printer Manufacturers
Company | Printers | Key Features |
---|---|---|
EOS | EOS M290, EOS M300 x4 | Pioneer of metal 3D printing, excellent part properties |
SLM Solutions | SLM 280, SLM 500, SLM 800 | Very high laser power for productivity, large build volumes |
3D Systems | DMP Factory 500 | Scalable systems for high volume production |
GE Additive | Concept Laser M2, X Line 2000R | Now part of GE, reliable productivity workhorses |
Renishaw | RenAM 500Q | Excellent precision, integrated Quality Management System |
In choosing an SLM system, key factors are build volume, laser power, materials capabilities, precision, and software workflow. The leading manufacturers offer established systems, but many new entrants from China and India are also emerging.
SLM Printer Pricing
Industrial SLM systems have high upfront capital costs ranging from $100,000 for entry-level machines upto $1,000,000+ for high-end production systems:
SLM Printer Pricing
Manufacturer | Printer Model | Build Volume | Price Range |
---|---|---|---|
EOS | EOS M100 | 95 x 95 x 95 mm | $100k – $150k |
SLM Solutions | SLM 125 | 125 x 125 x 125 mm | $175k – $250k |
3D Systems | DMP Factory 500 | 500 x 500 x 500 mm | $500k – $800k |
GE Additive | Concept Laser M2 Series 5 | 250 x 250 x 280 mm | $700k – $900k |
Renishaw | RenAM 500M | 250 x 250 x 350 mm | $950k – $1.2M |
Larger build volumes, higher laser power, and productivity features drive up system costs. But choosing wisely based on application needs and production requirements is key.
SLM Facility Considerations
To operate an SLM facility successfully, businesses should consider:
SLM Facility Factors
Factor | Description |
---|---|
Facility Costs | Account for printer, materials, and facility buildout costs |
Material Handling | Install powder handling equipment and provide PPE for workers |
Post-Processing | Cleaning equipment, heat treatment, HIP, surface finishing etc. |
Software | Workflow software for scheduling, nesting, process monitoring |
Training | Train engineers on design and technicians on printer operation |
Safety | Follow powder handling procedures and have fire suppression systems |
Maintenance | Schedule regular system maintenance and calibration |
Quality Control | Measure dimensions and material properties, repeatability testing |
Certification | ISO 9001, AS9100 certification for regulated industries |
Choosing an experienced service provider can help navigate facility setup, operations, and certification for regulated applications like aerospace or medical devices.
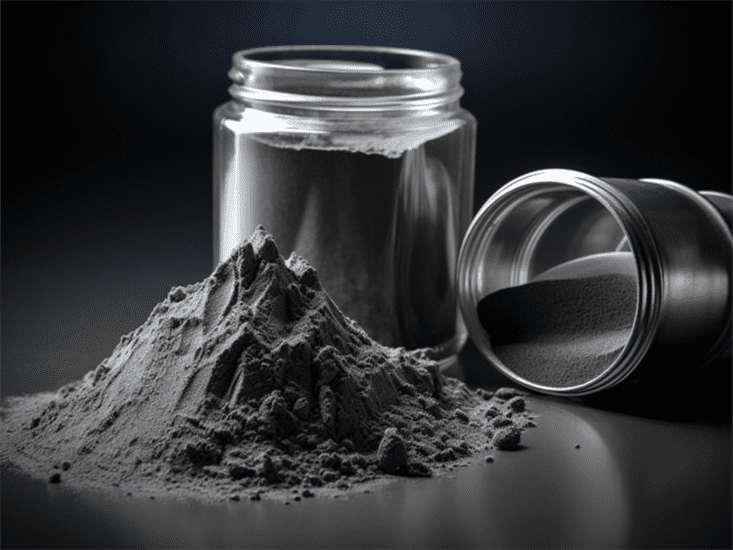
Advantages of SLM Additive Manufacturing
The key advantages of SLM 3D printing include:
SLM Additive Manufacturing Advantages
Advantage | Description |
---|---|
Complex Geometries | SLM can produce highly complex organic shapes and intricate internal lattices and channels |
Customized Parts | Easily create customized parts tailored to customer needs versus tooling constraints |
Weight Reduction | Lattice structures and topology optimization enables lightweight, strong designs |
Consolidated Assemblies | Combine multiple components into single complex parts |
Fast Lead Times | Print parts on-demand directly from CAD data versus months for machining |
Reduced Waste | Only use required amount of material versus machining from billet |
On-Demand Production | Enables distributed just-in-time manufacturing close to customers |
Inventory Reduction | Print parts as needed reducing tooling, warehousing, inventory costs |
High-Performance Materials | Process advanced metals like titanium and superalloys into end-use parts |
The design freedom, part customization, and distributed production capabilities make SLM ideal for low to medium volume production for aerospace, medical, industrial, and automotive applications.
Limitations of SLM Additive Manufacturing
SLM does have some limitations including:
SLM Additive Manufacturing Limitations
Limitation | Description |
---|---|
Machine Cost | SLM printers have high capital costs often over $500,000 |
Material Availability | Currently limited to reactive structural metals versus plastics |
Accuracy | Typical accuracy of 0.1-0.2mm is lower than CNC machining |
Surface Finish | As-printed surface is relatively rough with stair-stepping effect |
Post-Processing | Support removal, machining, polishing often required |
Print Speed | Build rates typically 5-100 cc/hr limit speed versus mass production |
Max Part Size | Limited by printer build volume, typically under 500 x 500 x 500 mm |
Process Monitoring | Lack of in-situ monitoring can lead to undetected defects |
Operator Expertise | SLM technicians require significant training on procedures |
Material Costs | Powder metals can be 2-5x more expensive than raw stock |
For very high accuracy needs, extremely large parts, or mass production volumes, subtractive methods like CNC machining tend to be more suitable than SLM additive.
The Role of SLM in Manufacturing
SLM is best suited for:
Best Roles for SLM in Manufacturing
Manufacturing Role | Examples |
---|---|
Rapid prototyping | Fast design iterations and proof-of-concept parts |
Low-volume production | Aerospace brackets, impellers, medical implants |
Bridge tooling | Producing early units while injection molds are made |
Part consolidation | Combining multiple components into single parts |
Mass customization | Customized end-use products like dental aligners |
Distributed manufacturing | On-demand local production close to customers |
For very high volumes, conventional high-pressure die casting or plastic injection molding tend to be more cost-effective than SLM 3D printing. But for short run production, SLM excels.
The Future of SLM Additive Manufacturing
SLM is expected to expand into wider applications in the future through:
The Future of SLM
Trend | Description |
---|---|
Larger printers | Build volumes over 1 meter length and height |
Multi laser systems | Higher power multi-laser machines over 1 kW |
Faster speeds | Print speeds up to 500 cc/hr via scanned galvo lasers |
New materials | High temperature alloys, MMCs, novel composites |
Hybrid manufacturing | Combined AM and subtractive processes in one system |
Automated post-processing | Reduced manual labor for support removal, surface finishing |
In-process monitoring | In-situ monitoring of melt pool, powder bed, and part defects |
Simulation | Physics-based simulations to predict behavior and optimize builds |
Machine learning | AI for design, process optimization, quality assurance |
Digital supply chain | Seamless digital workflow from design to production |
Choosing an SLM Service Provider
When selecting an SLM service provider, buyers should evaluate:
Choosing an SLM Service Provider
Factor | Description |
---|---|
Printing Equipment | Look for reputable industrial metal printers with high beam power and large build volumes |
Materials | Ability to process desired alloys like titanium, tool steel, stainless steel |
Post-Processing | Offer full range of post-print processing like HIP, machining, polishing |
Quality Procedures | ISO 9001 or AS9100 certified with strict QA processes |
Application Experience | Expertise and case studies in target applications like aerospace, automotive, medical |
Design Support | Capability to design and optimize parts for AM manufacturability |
Lead Times | Ability to deliver sample and production parts within required timeframes |
File Preparation | Accept standard CAD and polygon file formats with design analysis |
Post Build Services | Cleaning, heat treat, surface finishing, coating services |
Additional Services | Inspection, rapid prototyping, bridge tooling, castings, molding |
Pricing | Competitive and scalable pricing for different build volumes |
Location | Proximity for supply chain logistics and communication |
Choosing a service provider with end-to-end capabilities from design to post-processing ensures high quality results. Checking case studies and visiting facilities helps verify experience.
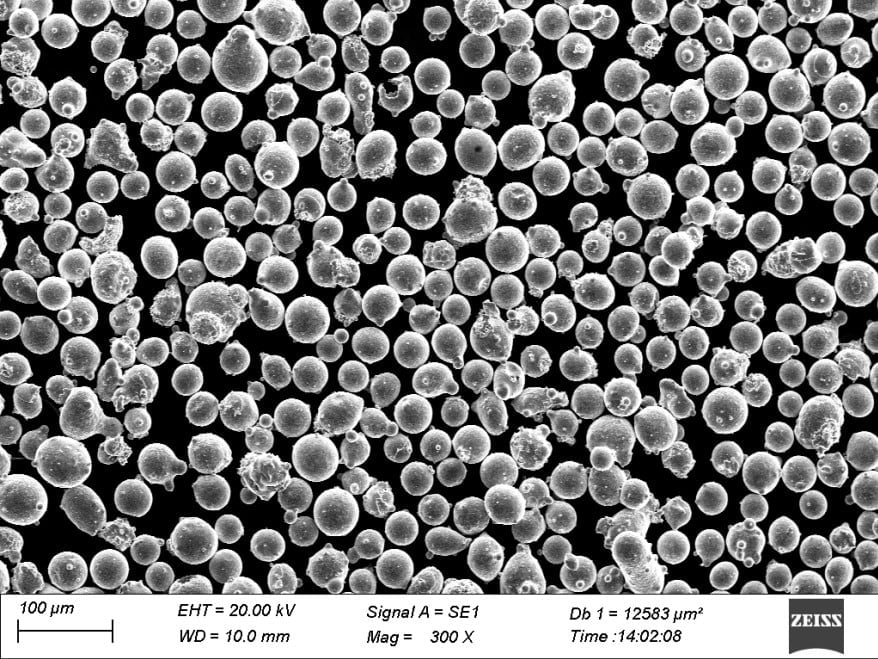
FAQs
Q: What materials can be 3D printed with SLM technology?
A: SLM is capable of processing a range of reactive metals like stainless steel, tool steel, titanium alloys, nickel superalloys, aluminum alloys, and cobalt chrome. The most popular SLM materials are titanium Ti6Al4V and AlSi10Mg aluminum.
Q: How accurate is SLM 3D printing?
A: SLM typically produces accuracy around 0.1-0.2mm. While lower than CNC machining tolerance, post-processing like machining and polishing can improve accuracy. Feature sizes below 0.3mm are not recommended.
Q: What industries use SLM additive manufacturing?
A: Aerospace, medical, dental, automotive, and industrial sectors are major users of SLM technology today due to benefits like lightweighting, part consolidation, mass customization, and rapid turnaround times.
Q: What post-processing is required after SLM printing?
A: Common post-printing processing includes support removal, stress relieving heat treatment, Hot Isostatic Pressing (HIP), CNC machining, polishing, and coating. The requirements depend on application, material, and finish needs.
Q: How expensive is SLM metal 3D printing?
A: Industrial SLM systems range from $100,000 to over $1 million depending on build volume, laser power, and features. Material costs for metal powder can be 2 to 5 times the cost of raw stock. But total costs are coming down.
Q: Can SLM print overhangs and complex shapes?
A: Yes, SLM can print geometries like overhangs, lattices, and thin walls through the use of support structures. Careful orientation is needed to avoid deformation and balance support requirements.
Q: What software is used for SLM printing?
A: SLM printers come with proprietary software for printing. Additional software is used for design, file repair, simulation, build preparation, nesting, build management, and quality management.
Q: How long does it take to 3D print a part with SLM?
A: Print times range from hours to days depending on the part size, geometry complexity, and print parameters. For metal parts, SLM printers typically operate from 5 to 100 cc/hour build rate. Larger parts take longer.
Q: Does SLM produce safe and functional end-use metal parts?
A: Yes, with proper design and processing, SLM can produce fully dense metal parts meeting or exceeding material properties of traditionally manufactured parts for functional end-use in demanding applications.
Share On
MET3DP Technology Co., LTD is a leading provider of additive manufacturing solutions headquartered in Qingdao, China. Our company specializes in 3D printing equipment and high-performance metal powders for industrial applications.
Inquiry to get best price and customized Solution for your business!
Related Articles
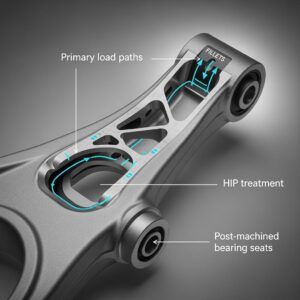
Metal 3D Printing for U.S. Automotive Lightweight Structural Brackets and Suspension Components
Read More »About Met3DP
Recent Update
Our Product
CONTACT US
Any questions? Send us message now! We’ll serve your request with a whole team after receiving your message.