Spherical Powders
Table of Contents
Imagine a world where metal isn’t just clunky and solid, but comes in tiny, perfectly round particles. That’s the realm of spherical powders, and they’re revolutionizing industries from manufacturing to medicine. Buckle up, because we’re diving deep into the fascinating world of these little spheres!
What are Spherical Powders?
Spherical powders are metal powders meticulously crafted into near-perfect spheres. Unlike their irregularly shaped cousins, these spherical particles boast unique properties that make them superstars in various applications.
Types, Composition, Properties, and Characteristics of Spherical Powders
Type | Composition | Properties | Characteristics |
---|---|---|---|
Metal Powders | Various Metals (e.g., Titanium, Stainless Steel, Aluminum) | High Flowability, Packing Density, Uniform Size Distribution, Smooth Finish | Shiny, Free-flowing |
Ceramic Powders | Ceramic Materials (e.g., Alumina, Zirconia) | High Melting Point, Chemical Resistance, Wear Resistance | Heat Resistant, Durable |
Polymer Powders | Polymers (e.g., Nylon, Polypropylene) | Lightweight, Insulative, Low Friction | Flexible, Versatile |
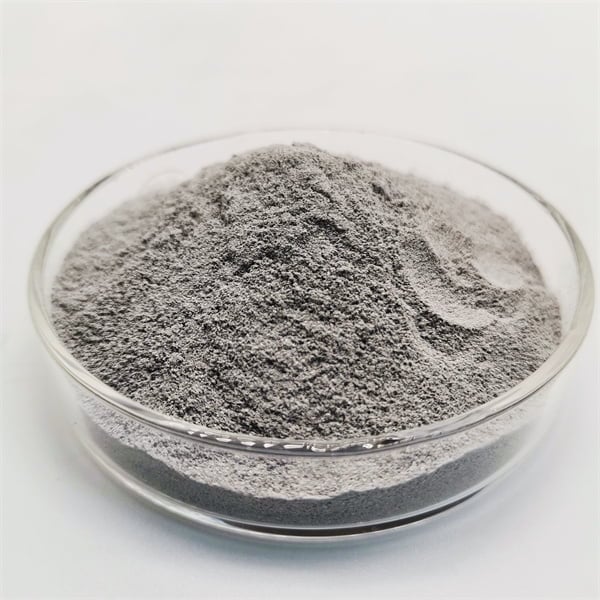
specific metal spherical powder models
Now, let’s delve into the metallic side of things and explore some specific metal spherical powder models:
- Stainless Steel Powders: Imagine tiny, near-perfect spheres of stainless steel. These versatile powders, available in various grades like 316L and 17-4PH, shine in applications requiring corrosion resistance and high strength. Think medical implants, aerospace components, and even intricate jewelry.
- Titanium Powders: For those seeking lightweight yet incredibly strong options, titanium spherical powders are the answer. Used extensively in 3D printing for aerospace and medical applications, these powders boast exceptional strength-to-weight ratios and biocompatibility.
- Nickel Powders: Nickel spherical powders are workhorses in the electronics industry. Their excellent electrical conductivity makes them ideal for electrodes in batteries and other electronic components.
- Aluminum Powders: Lightweight and readily available, aluminum spherical powders are a popular choice for applications requiring good thermal conductivity and low weight. They find use in heat sinks, brazing materials, and even pyrotechnics (think fireworks!).
- Copper Powders: Highly conductive and malleable, copper spherical powders are a mainstay in electrical applications. Imagine tiny copper spheres packed together to create efficient heat sinks or intricate electrical components.
- Cobalt-Chromium-Molybdenum (CoCrMo) Powders: An alloy known for its exceptional wear resistance and high-temperature performance, CoCrMo spherical powders are used in demanding applications like orthopedic implants and jet engine components.
- Inconel Powders: This group of nickel-chromium-based superalloy powders offers exceptional resistance to high temperatures, oxidation, and corrosion. They’re used in demanding environments like gas turbine engines and chemical processing equipment.
- Tungsten Powders: Dense and boasting a very high melting point, tungsten spherical powders are used in applications requiring high density and extreme temperatures. Think of them as tiny, heat-resistant spheres used in weightlifting equipment, radiation shielding, and even certain types of ammunition.
- Molybdenum Powders: Similar to tungsten, molybdenum spherical powders offer excellent high-temperature performance and are used in applications like heating elements, electrodes, and refractory linings for furnaces.
- Tantalum Powders: Corrosion-resistant and biocompatible, tantalum spherical powders are finding increasing use in medical implants and capacitors.
Applications of Spherical Powders
Application | Spherical Powder Type | Why Spherical Powders? |
---|---|---|
3D Printing | Metal Powders (e.g., Stainless Steel, Titanium) | Excellent flowability for smooth deposition, high packing density for strong parts |
Metal Injection Molding (MIM) | Metal Powders | Uniform particle size for precise molding, good flowability for easy filling of molds |
Thermal Spraying | Metal Powders (e.g., Aluminum, Nickel) | Spherical shape creates smooth coatings, high packing density for strong layers |
Battery Electrodes | Nickel Powders | High conductivity for efficient energy transfer |
Medical Implants | Titanium, Tantalum Powders | Biocompatible, excellent strength-to-weight ratio |
the Advantages and Disadvantages of Spherical Powders
Spherical powders, with their near-perfect roundness, offer a multitude of advantages over their irregularly shaped counterparts. But, as with all things in engineering, there are also limitations to consider. Let’s delve into this tale of two sides.
Advantages of Spherical Powders: A Symphony of Benefits
- Flowability: Imagine pouring sand – it flows freely due to the round particles. Spherical powders mimic this behavior, moving smoothly in hoppers, feeders, and during 3D printing processes. This translates to better process control, reduced waste, and more uniform product formation.
- Packing Density: Think of packing oranges in a box – spheres leave minimal gaps compared to irregularly shaped objects. Spherical powders achieve a higher packing density, meaning you can cram more powder into a smaller space. This translates to stronger parts in 3D printing, denser coatings in thermal spraying, and more efficient use of materials.
- Uniform Size Distribution: Consistency is key in engineering. Spherical powders boast a much narrower size distribution compared to irregular powders. This uniformity ensures predictable behavior in various processes, leading to more consistent product quality and fewer defects.
- Smooth Finish: The smooth, near-perfect surface of spherical powders minimizes friction during flow and handling. This translates to less wear and tear on machinery in processes like 3D printing and metal injection molding (MIM).
- Improved Conductivity: For applications like battery electrodes and thermal management, maximizing conductivity is crucial. The spherical shape of these powders minimizes contact resistance between particles, leading to a more efficient flow of electricity or heat.
Disadvantages of Spherical Powders: A Shadow Cast by Perfection
While spherical powders offer a plethora of advantages, it’s important to acknowledge their limitations:
- Higher Cost: The meticulous process of creating perfectly round particles often translates to a higher cost compared to irregular powders. This can be a deciding factor for applications where cost is a primary concern.
- Reduced Workability: The smooth surface and spherical shape of these powders can sometimes lead to reduced workability. For processes like cold pressing, irregular-shaped powders can interlock better, creating a stronger initial bond.
- Limited Material Selection: Not all metals can be easily formed into perfect spheres. The production process might limit the availability of certain exotic or specialty metals in spherical powder form.
- Segregation Potential: Due to their uniform size and smooth surface, spherical powders can sometimes exhibit segregation during handling or storage. This can lead to variations in composition within the powder bed, potentially affecting the final product properties.
Spherical Powders vs. Irregular Powders
Let’s put spherical and irregular powders head-to-head to see how they compare across key parameters:
Parameter | Spherical Powders | Irregular Powders |
---|---|---|
Flowability | Excellent | Good, but can bridge or clump |
Packing Density | High | Moderate |
Size Distribution | Narrow | Broad |
Surface Finish | Smooth | Rough |
Conductivity | High | Moderate |
Cost | Higher | Lower |
Workability | Lower | Higher |
Material Selection | Wider range (but limitations exist) | Wider range |
Segregation Potential | Higher | Lower |
The Verdict: Choosing the Right Powder for the Job
The decision between spherical and irregular powders boils down to your specific application needs. If flowability, packing density, and uniform size are paramount, spherical powders are the clear winner. However, if cost is a major concern, irregular powders might be a viable option, especially if the application can tolerate their limitations.
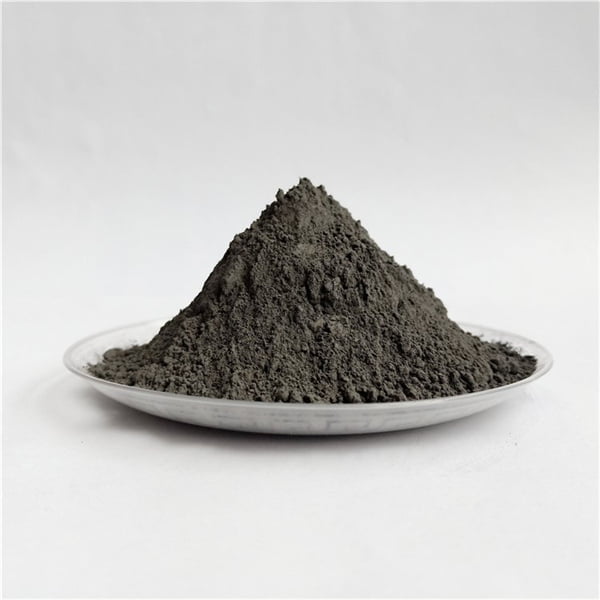
Suppliers and Pricing of Spherical Powders
Spherical powders are produced by various companies worldwide. Here’s a glimpse into the supplier landscape, keeping in mind that specific pricing can vary depending on factors like material, quantity, and market fluctuations.
- Höganäs AB (Sweden): A leading global supplier of metal powders, offering a wide range of spherical powders in various materials and sizes.
- AMETEK (United States): Provides high-performance spherical powders for additive manufacturing and other applications.
- LPKF Laser & Electronics AG (Germany): Specializes in high-purity spherical powders for electronic and medical applications.
- Sandvik Materials Technology (Sweden): Offers a variety of spherical metal powders for demanding applications in aerospace, medical, and other sectors.
- Elementum (United States): A global manufacturer of specialty metal products, including spherical powders for various applications.
FAQs
Q: Are spherical powders always better than irregular powders?
A: Not necessarily. Spherical powders offer distinct advantages in flowability, packing density, and size consistency. However, these benefits come at a cost, with spherical powders typically being more expensive than irregular ones. The choice between the two depends on your specific application:
- Choose spherical powders if:
- Flowability and ease of handling are crucial (e.g., 3D printing)
- High packing density is needed for strong parts (e.g., metal injection molding)
- Consistent product quality is paramount (e.g., medical implants)
- Opt for irregular powders if:
- Cost is a primary concern and the application can tolerate slight variations
- The process benefits from some interparticle friction (e.g., cold pressing)
- A wider range of exotic or specialty metals is required (availability in spherical form might be limited)
Q: How are spherical powders manufactured?
A: There are several methods for producing spherical powders, each with its own advantages and limitations. Here are two common techniques:
- Atomization: Molten metal is broken up into tiny droplets using a high-pressure gas or water stream. The droplets then solidify in mid-air, forming near-perfect spheres due to surface tension.
- Plasma Spheroidization: Irregular-shaped metal powders are injected into a high-temperature plasma torch. The intense heat melts the surface of the particles, causing them to form spheres due to surface tension.
Q: What are some emerging applications of spherical powders?
A: Spherical powders are constantly finding new uses due to their unique properties. Here are a few exciting possibilities:
- Additive Manufacturing (3D Printing) of Electronics: Spherical powders with precisely controlled conductivity could be used to 3D print intricate electronic components.
- Lightweight Batteries: Spherical powders with high energy density could pave the way for lighter and more powerful batteries for electric vehicles and portable electronics.
- Bioprinting: Biocompatible spherical powders could be used to create 3D printed tissues and organs for medical applications.
The Future of Spherical Powders: A World of Possibilities
Spherical powders are revolutionizing various industries with their unique properties. As production techniques evolve and costs decrease, we can expect to see even wider adoption of these tiny spheres in the years to come. From 3D printing marvels to advancements in medicine and electronics, the future of spherical powders is brimming with possibilities.
Share On
MET3DP Technology Co., LTD is a leading provider of additive manufacturing solutions headquartered in Qingdao, China. Our company specializes in 3D printing equipment and high-performance metal powders for industrial applications.
Inquiry to get best price and customized Solution for your business!
Related Articles
About Met3DP
Recent Update
Our Product
CONTACT US
Any questions? Send us message now! We’ll serve your request with a whole team after receiving your message.
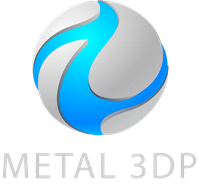
Metal Powders for 3D Printing and Additive Manufacturing