Spherical Powder:Overview,Types,price
Table of Contents
Overview
Spherical powder refers to metallic or ceramic powders with a rounded morphology produced by specialized atomization processes. Compared to irregular powder particles, spherical powders offer benefits like excellent flowability, higher packing density, and reduced inner-particle friction. This makes them ideal for demanding industrial applications using powder metallurgy, thermal spraying, metal additive manufacturing, and ceramic processing.
This comprehensive guide covers different types of spherical powders, their properties, manufacturing methods, key applications, specifications, suppliers, handling procedures, equipment maintenance, selection criteria for vendors, pros and cons, and answers frequently asked questions.
Types of Spherical Powder
The main types of spherical powder based on material and production method include:
Material
- Metal powders – stainless steel, tool steel, superalloys, titanium, aluminum etc.
- Ceramic powders – alumina, zirconia, silica, carbides, nitrides etc.
- Composite/alloy powders – nickel-based, cobalt-based, Fe-based etc.
Production Method
- Gas atomized powders
- Plasma atomized powders
- Electrode induction-melting gas atomization (EIGA)
- Rotating electrode process (REP)
- Plasma rotating electrode process (PREP)
- Thermal spray powders
Gas atomization is the most widely used process but methods like PREP yield superior sphericity and smooth surface morphologies. The production method controls the final powder characteristics.
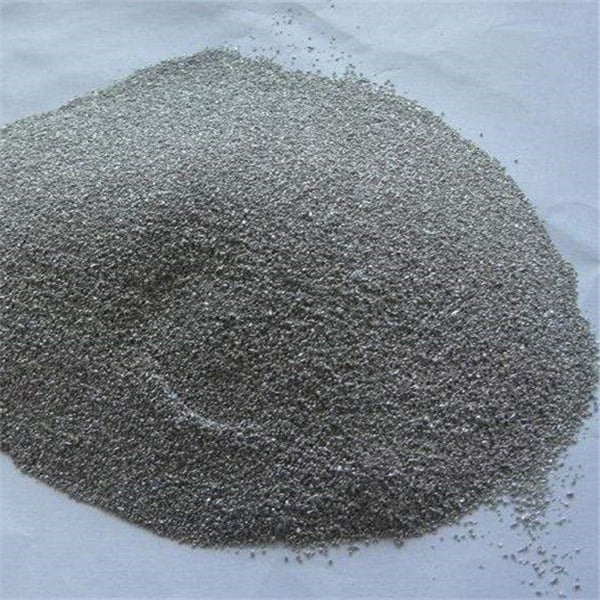
Properties and Applications
Properties and typical applications of major spherical powder types:
Stainless steel
- High hardness and corrosion resistance
- Valves, pumps, medical devices
Tool steel
- Excellent wear resistance
- Cutting tools, dies, punches
Superalloys
- Withstand high temperatures and stresses
- Turbine blades, aerospace components
Titanium
- High strength-to-weight ratio
- Aerospace fasteners, biomedical implants
Aluminum
- Lightweight, excellent thermal conductivity
- Automotive parts, heat sinks
Ceramics
- High hardness, wear and corrosion resistance
- Bearings, seals, armor coatings
Spherical morphology improves powder packing density and flow in addition to the inherent properties of the base material.
Manufacturing Methods
Common methods for producing spherical powders:
Gas Atomization
- Metal alloy melted and atomized by inert gas jets
- Lower investment cost
- 10 – 150 μm size range
Plasma Atomization
- Use of plasma energy to melt and atomize
- Finer powder down to 5 μm
- Higher purity, more spherical
EIGA
- Electrodes inductively melted in atomization chamber
- Rapid solidification of fine droplets
- Control over size, morphology
PREP
- Rotating electrode melted by plasma torches
- Centrifugal disintegration into fine powder
- Smooth spherical shape
Thermal Spray
- Feedstock wires/rods atomized by hot gas
- Oxide dispersion strengthened alloys
- Rougher surfaces than other methods
Specifications
Typical specifications for spherical powder include:
Parameter | Specification |
---|---|
Particle size | 10 – 150 μm |
Particle shape | Spherical |
Flow rate | 25 – 35 s/50g |
Apparent density | 40 – 60% |
Tap density | Up to 90% theoretical |
Surface oxide | < 1% by weight |
Residual gases | Minimized |
Meeting size distribution, high sphericity, smooth surface, and composition requirements is critical. Smaller sizes improve densification while larger sizes reduce costs.
Design Considerations
Key design factors for components using spherical powder:
- Dimensional tolerances – Accounting for sintering shrinkage
- Surface finish requirements – Minimal post-processing
- Mechanical properties – Matching material and process to properties needed
- Production costs – Optimizing part design to balance performance and cost
- Secondary operations – Avoiding large machining allowances
- Assembly requirements – Designing joining surfaces, interlocking features
- Standards compliance – For aerospace, biomedical etc. applications
The design freedom enabled by advanced manufacturing processes like additive manufacturing allow more optimized designs not possible with wrought metal.
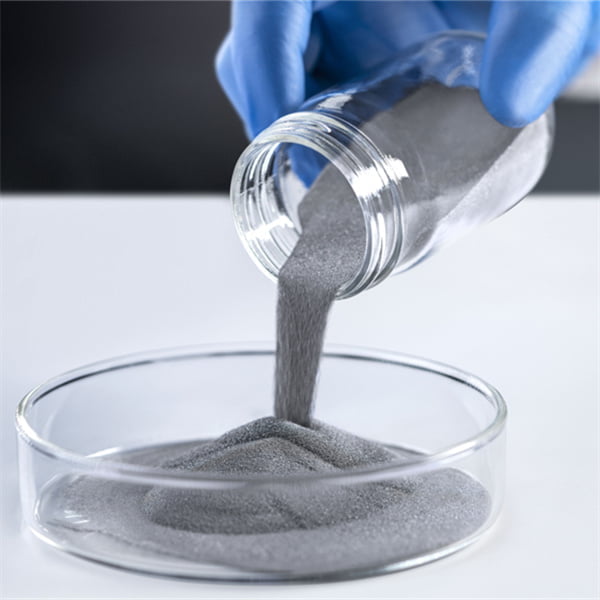
Consolidation Processes
Common powder consolidation processes suitable for spherical powders:
- Additive manufacturing – Selective laser melting, electron beam melting etc. offer maximum flexibility
- Metal injection molding – High volume production of small, complex parts
- Cold/hot isostatic pressing – Produces net shape or near-net shape parts
- Press and sinter – Conventional powder metallurgy process combining shaping and sintering
- Thermal spray – Deposits molten powder onto a prepared substrate
- Slurry-based methods – Slip casting, tape casting, electrophoretic deposition etc. for ceramics
Spherical shape improves powder packing and flow during processing, enabling high density and uniform microstructures.
Suppliers and Pricing
Leading global suppliers of spherical powders include:
Supplier | Materials | Price Range |
---|---|---|
Sandvik | Alloy steels, stainless steels | $50-200/kg |
Carpenter Additive | Tool steels, superalloys | $70-250/kg |
Höganäs | Stainless steels | $45-180/kg |
Praxair | Titanium, superalloys | $100-350/kg |
LPW Technology | Aluminum alloys, composites | $60-220/kg |
Prices depend on alloy composition, quality, lot size, and purchase quantity. Small R&D quantities are more expensive than bulk production volumes.
Handling and Storage
Guidelines for safe handling and storage of spherical powders:
- Store sealed containers in a cool, dry, inert atmosphere to prevent oxidation and contamination
- Limit exposure to moisture to avoid powder agglomeration
- Use mild steel or plastic containers instead of aluminum to prevent reaction
- Ensure containers are properly grounded to avoid static charge accumulation
-Handle containers and powders gently to prevent particle damage during transport and transfer
- Avoid sparks, flames, ignition sources near storage and handling areas
- Install appropriate ventilation and dust collection equipment
- Use appropriate PPE for handling fine powders – gloves, respirators, eye protection
Proper procedures prevent powder property changes that can negatively impact consolidation and final part properties.
Equipment Maintenance
Maintenance tips for key powder handling systems:
Sieves:
- Replace damaged mesh screens to avoid tears and openings
- Clean sieves regularly to prevent clogging which can lead to particle damage
- Check vibration amplitude and time settings to prevent work hardening
Hoppers and feeders:
- Inspect outlet ports for buildup and remove any material blocking flow
- Verify feeder settings match powder properties to ensure reliable flow
- Check hopper linings for wear and replace if deteriorated
Mixing vessels:
- Replace worn baffles and intensifiers for homogeneous mixing without segregation
- Inspect blade condition and repair/replace damaged items
- Verify gaskets and seals to prevent powder leaks during operation
Tooling:
- Monitor dimensional accuracy and repair/replace as needed
- Apply lubricant on presses and dies per schedule to ensure easy release
- Verify heating elements and temperature controls on furnaces
Selecting Spherical Powder Suppliers
Key factors in selecting suppliers:
- Technical expertise in materials, manufacturing processes, part design etc. to support customers
- Range of powder options including different materials, sizes, morphologies and coatings
- Stringent quality assurance covering chemical analysis, microscopic inspection, process control etc.
- Production capacity to meet demands in a timely manner
- Services offered like sampling, prototyping, testing, analysis etc.
- Industry reputation for consistently supplying high quality powders
- Certifications such as ISO 9001, AS9100, ISO 13485 etc.
- Competitive pricing combined with value-added services and customer support
- Shipping and logistics capabilities for timely delivery with minimal lead times
The right partner provides both spherical powders tailored to needs as well as technical expertise for success.
Advantages vs Limitations
Advantages
- Excellent powder flow and packing density
- Improved sintered density and microstructure
- Reduced internal stresses during compaction
- Allows complex geometries to be manufactured
- Consistent metallurgical properties
- Good surface finish on sintered parts
Limitations
- More expensive than irregular powder
- Require advanced manufacturing techniques
- Limited sizes available for very fine powders
- Controlling particle size distribution can be difficult
- Some materials are challenging to atomize into spherical powder
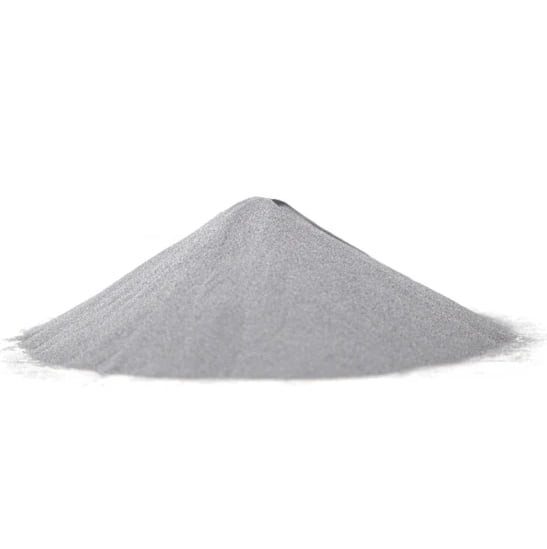
FAQs
What are the main advantages of using spherical powder?
The main benefits are excellent flowability for ease of handling, high packing density for improved compaction, lower interparticle friction allowing complex geometries, and consistent metallurgical properties.
Which materials are commonly available as spherical powder?
Common materials include stainless steels, tool steels, superalloys, titanium alloys, aluminum alloys, nickel-based alloys, and ceramic powders.
What industries typically use spherical powder?
Key industries include aerospace, medical, automotive, defense, energy, electronics, and industrial equipment manufacturing.
What is the typical size range for spherical powders?
Conventional gas atomized spherical powders range from around 10-150 microns. Specialized techniques can produce submicron to nano-scale spherical powders.
How much more expensive is spherical powder compared to irregular powder?
The premium for spherical shape is typically 20-50% over irregular powders. However, the benefits often justify the higher cost for critical applications.
Conclusion
With their characteristic rounded shape and smooth surface, spherical powders enable higher density and superior flow compared to irregular powders. Their consistent particle characteristics impart excellent compressibility, compactability, and sinterability across a range of metals and ceramics. Continued development of atomization processes makes spherical powders available in a wider selection of materials and sizes than ever before. Part design and process optimization to take full advantage of the benefits of starting with spherical powder can yield high performance parts cost-effectively.
Share On
MET3DP Technology Co., LTD is a leading provider of additive manufacturing solutions headquartered in Qingdao, China. Our company specializes in 3D printing equipment and high-performance metal powders for industrial applications.
Inquiry to get best price and customized Solution for your business!
Related Articles
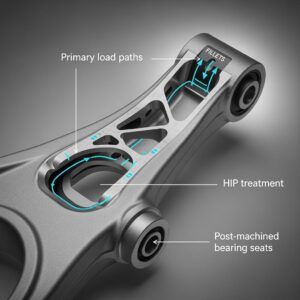
Metal 3D Printing for U.S. Automotive Lightweight Structural Brackets and Suspension Components
Read More »About Met3DP
Recent Update
Our Product
CONTACT US
Any questions? Send us message now! We’ll serve your request with a whole team after receiving your message.