spheroidising powder
Table of Contents
Imagine a world where your 3D printer could churn out objects with unparalleled strength, uniformity, and flow. This isn’t science fiction; it’s the reality unlocked by spheroidising powder. But what exactly are these wonder materials, and how do they revolutionize various industries? Buckle up, because we’re diving deep into the fascinating realm of spheroidized powders!
What is Spheroidization?
Think of a bag of flour. Those tiny, irregular particles are the norm in the world of powders. Spheroidization takes these haphazard shapes and transforms them into near-perfect spheres, much like tiny marbles. This seemingly simple change unlocks a treasure trove of benefits.
Why Spheres?
Spheres are nature’s masterclass in efficiency. They boast the highest packing density, meaning you can cram more powder into a smaller space. This translates to better flowability, making these powders dream material for processes like additive manufacturing (3D printing) and metal injection molding (MIM). But the magic doesn’t stop there. spheroidising powder offer:
- Enhanced Strength: Spherical particles distribute stress more evenly, leading to stronger final products.
- Improved Surface Finish: Imagine a smoother, more aesthetically pleasing object. That’s the power of spherical powders!
- Reduced Porosity: Spherical shapes minimize trapped air pockets, resulting in denser, more consistent materials.
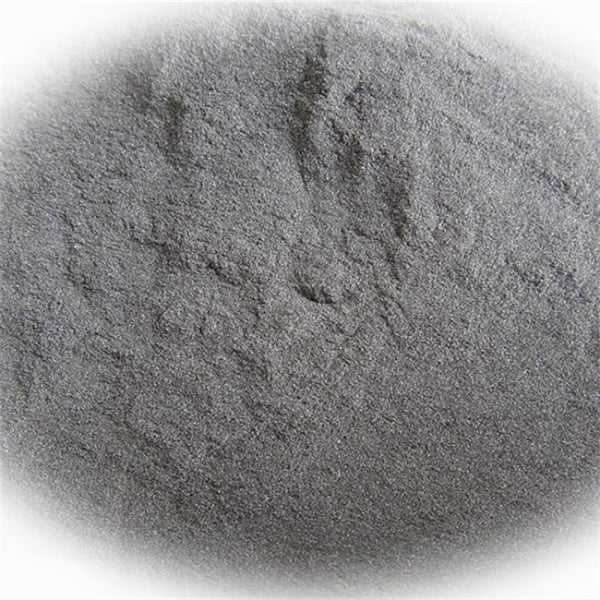
the Spheroidized Powder Arsenal: A Look at 10 Key Players
Now that we understand the “why” behind spheroidization, let’s meet some of the “who.” Here’s a closer look at 10 prominent metal powders that benefit from the spheroidization treatment:
1. Stainless Steel Powders (316L, 17-4PH): These workhorses of the metal world offer excellent corrosion resistance and come in various grades, making them ideal for applications like medical implants, aerospace components, and jewelry. Spheroidization enhances their flowability, leading to more intricate 3D printed designs and smoother MIM parts.
2. Titanium Powders (Ti-6Al-4V, Grade 2): Known for their exceptional strength-to-weight ratio, these titanium powders are the go-to choice for aerospace components, prosthetics, and sporting goods. Spheroidization elevates their mechanical properties, resulting in lighter, stronger parts.
3. Aluminum Powders (AlSi10Mg, AA2024): Lightweight and versatile, aluminum powders find use in everything from automotive parts to consumer electronics. Spheroidization improves their packing density, leading to more efficient use of material and cost savings.
4. Nickel Powders (Nickel 200, Inconel 625): These high-temperature resistant powders are crucial for applications like heat exchangers, turbine blades, and chemical processing equipment. Spheroidization enhances their flowability and packing density, ensuring consistent performance in extreme environments.
5. Copper Powders (C101, C110): Highly conductive and malleable, copper powders are vital for electrical components, heat sinks, and filtration systems. Spheroidization improves their packing density and flowability, leading to more uniform conductivity and efficient filtering performance.
6. Cobalt Powders (CoCrMo): This biocompatible material shines in the medical field, particularly for joint replacements. Spheroidization enhances its wear resistance and surface finish, crucial for long-lasting, comfortable implants.
7. Tungsten Powders (W): Dense and heat-resistant, tungsten powders are used for weights, armor-piercing projectiles, and radiation shielding. Spheroidization improves their flowability for additive manufacturing, enabling the creation of complex tungsten-based components.
8. Molybdenum Powders (Mo): Similar to tungsten, molybdenum powders offer high melting points and strength. Spheroidization allows for more efficient use of this material in applications like high-temperature furnace components and electronics.
9. Niobium Powders (Nb): Superconducting properties make niobium powders valuable for MRI machines and particle accelerators. Spheroidization improves their packing density, leading to more efficient superconducting performance.
10. Tantalum Powders (Ta): Corrosive-resistant and biocompatible, tantalum powders are used in capacitors, implants, and chemical processing equipment. Spheroidization enhances their flowability and packing density, enabling the creation of intricate, high-performance parts.
This list is just a glimpse into the vast world of spheroidized metal powders. As technology evolves, we can expect even more materials to benefit from this transformative process.
Applications of spheroidising powder
spheroidising powder aren’t just a party trick for materials science; they’re revolutionizing various industries. Here’s a peek at some of their most impactful applications:
1. Additive Manufacturing (3D Printing): This revolutionary technology thrives on precise powder layering. Spheroidized powders excel here, offering:
- Unparalleled Flowability: Imagine smoother, more consistent powder deposition during printing. This translates to intricate designs, minimal waste, and superior surface finishes for your 3D printed creations.
- Enhanced Strength: Say goodbye to weak, brittle 3D printed parts. Spheroidized powders, with their even stress distribution, create stronger, more reliable objects. This is particularly crucial for functional parts like aerospace components and medical implants.
- Reduced Porosity: spheroidising powder leave minimal air pockets, resulting in denser, more consistent 3D printed objects. This translates to improved mechanical properties and reduced risk of failure under stress.
2. Metal Injection Molding (MIM): This process injects a metal powder slurry into a mold to create complex shapes. spheroidising powder shine here by offering:
- Improved Flowability: Imagine the powder slurry flowing effortlessly through the mold, filling intricate cavities with ease. This reduces the risk of defects and ensures consistent part geometry.
- Reduced Binder Content: Spheroidized powders, with their superior packing density, require less binder to hold their shape during molding. This translates to cleaner debinding processes and improved final part quality.
- Dimensional Accuracy: The spherical shapes allow for tighter tolerances and more precise part dimensions in MIM, crucial for creating high-performance components.
3. Battery Electrode Materials: The future of energy storage hinges on efficient batteries. spheroidising powder play a key role here by offering:
- High Packing Density: More active material can be packed into a smaller battery, leading to increased energy density and longer battery life.
- Improved Conductivity: The spherical shapes provide better pathways for electrons to flow, leading to more efficient battery performance.
- Enhanced Cycle Life: The uniform structure of spheroidized powders contributes to longer battery lifespans by minimizing stress and wear during charging and discharging cycles.
4. Catalyst Applications: Catalysts accelerate chemical reactions, andspheroidising powder are making their mark here too. Their benefits include:
- High Surface Area: Spherical shapes offer a larger surface area per unit volume, maximizing the catalyst’s interaction with reactants and leading to faster, more efficient reactions.
- Controlled Porosity: Tailored spheroidization techniques can create powders with specific pore sizes, allowing for precise control of the catalytic process.
- Improved Heat Transfer: The spherical shapes facilitate better heat transfer within the catalyst bed, ensuring optimal reaction conditions and consistent results.
5. Advanced Filtration: From water purification to industrial processes, filtration plays a vital role. spheroidising powder are making waves here by offering:
- Uniform Pore Size Distribution: The controlled shapes allow for precise control over the filter media’s pore size, ensuring efficient capture of specific particles while allowing desired fluids to pass through.
- High Flow Rates: The spherical shapes minimize resistance to flow, leading to faster and more efficient filtration processes.
- Enhanced Filter Life: The uniform structure of spheroidized powders reduces filter clogging and extends their service life.
These are just a few examples of how spheroidising powder are transforming various industries. As research and development continue, we can expect even more innovative applications to emerge in the future.
the Specifications: A Deep Dive into spheroidising powder
Choosing the right spheroidized powder requires considering various specifications. Here’s a breakdown of some key parameters to keep in mind:
Particle Size Distribution: This refers to the range of sizes present in the powder. A narrow size distribution ensures consistent flowability and packing density, crucial for many applications.
Sphericity: This parameter measures how closely the particles resemble perfect spheres. Higher sphericity translates to better flowability, strength, and surface finish in the final product.
Apparent Density: This is the bulk density of the powder, considering the space between particles. Higher apparent density indicates better packing efficiency and material utilization.
Flowability: This refers to the ease with which the powder flows. spheroidising powder typically boast excellent flowability, making them ideal for automated processes like 3D printing and MIM.
Chemical Composition: This specifies the elements present in the powder and their exact proportions. Different applications require specific compositions to achieve desired properties.
Surface Area: The total surface area per unit mass of the powder. Higher surface area can be beneficial for applications like catalysis and filtration but may require additional surface treatments in some cases.
Standards and Certifications: When selecting spheroidized powders, understanding relevant standards and certifications is crucial. Here’s a breakdown of some key considerations:
- ASTM International (ASTM): This prominent organization sets international standards for various materials, including metal powders. Specific ASTM standards, like ASTM B822 for stainless steel powders and ASTM F451 for titanium powders, define requirements for chemical composition, particle size distribution, and flowability.
- Additive Manufacturing Standards: Organizations like the American Society for Testing and Materials International (ASTM International) and the International Organization for Standardization (ISO) are developing specific standards for metal powders used in additive manufacturing. These standards address factors like powder flowability, laser compatibility, and mechanical properties for optimal 3D printing performance.
- Medical Device Standards: For medical applications, powders must adhere to stringent regulations set by organizations like the International Organization for Standardization (ISO) and the US Food and Drug Administration (FDA). These standards ensure the biocompatibility, purity, and consistency of the powder material for safe and reliable medical implants.
- Supplier Certifications: Reputable powder suppliers often obtain certifications like ISO 9001 for quality management systems and ISO 14001 for environmental management systems. These certifications demonstrate the supplier’s commitment to consistent quality control and responsible manufacturing practices.
By considering these standards and certifications, you can ensure that the spheroidising powder you choose meet the specific requirements of your application and adhere to relevant safety and quality regulations.
the Benefits of spheroidising powder
Spheroidized powders offer a compelling set of advantages, but it’s important to acknowledge their limitations as well. Here’s a balanced perspective:
Advantages:
- Enhanced Flowability: Spheroidized powders excel in this area, leading to smoother processing in techniques like 3D printing and MIM.
- Improved Strength and Density: Spherical shapes distribute stress more evenly, resulting in stronger and denser final products.
- Reduced Porosity: Minimal air pockets translate to more consistent and reliable parts with improved mechanical properties.
- High Packing Density: More material can be packed into a smaller space, leading to material efficiency and potentially reducing costs.
- Enhanced Surface Finish: Spheroidized powders contribute to smoother and more aesthetically pleasing final products.
Limitations:
- Higher Production Cost: The spheroidization process can be more expensive compared to traditional powder production methods.
- Material Limitations: Not all materials can be effectively spheroidized. Some materials may require specialized techniques or may not benefit significantly from the process.
- Process Optimization: Utilizing spheroidized powders effectively might require adjustments to existing processing parameters for optimal results.
By understanding these advantages and limitations, you can make informed decisions about whether spheroidized powders are the right fit for your specific application.
Spheroidized Powders: A Cost-Benefit Analysis
The cost of spheroidized powders can vary depending on the material, particle size, sphericity, and supplier. Generally, spheroidized powders are more expensive than their non-spheroidized counterparts due to the additional processing involved. However, the benefits often outweigh the cost.
Here are some factors to consider when evaluating the cost-effectiveness of spheroidized powders:
- Improved Material Utilization: Spheroidized powders offer higher packing density, potentially reducing the amount of material needed compared to non-spheroidized variants.
- Reduced Waste: Improved flowability leads to less powder waste during processing, particularly in 3D printing and MIM.
- Enhanced Product Quality: Spheroidized powders contribute to stronger, denser parts with improved surface finishes, potentially reducing the need for rework or scrap.
- Process Efficiency: The superior flowability of spheroidising powder can translate to faster processing times and potentially lower production costs.
- Long-Term Performance: Products made with spheroidising powder may exhibit superior strength, durability, and performance, leading to longer lifespans and reduced replacement costs.
By carefully weighing the initial cost against the potential long-term benefits in terms of material espheroidising powderspheroidized powders offer a cost-effective solution for your application.
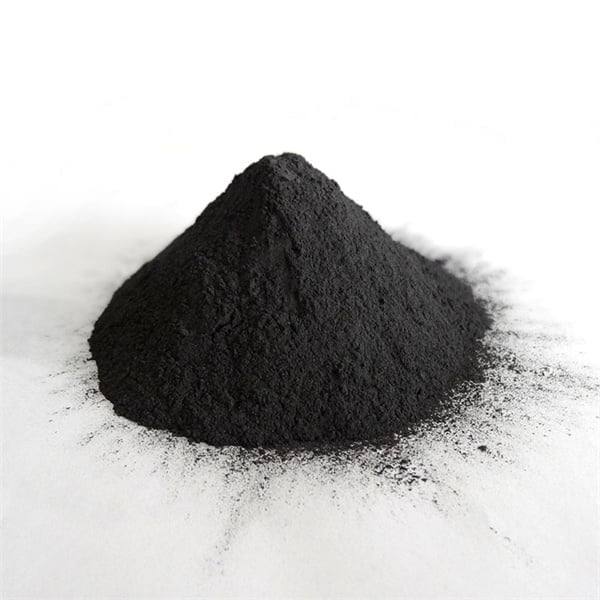
FAQ
What are the advantages of using spheroidized powders in 3D printing?
Spheroidized powders offer several advantages in 3D printing:
- Improved flowability: This leads to smoother powder deposition, enabling intricate designs and minimal waste.
- Enhanced strength: Spheroidized powders create stronger and more reliable 3D printed parts due to their even stress distribution.
- Reduced porosity: Minimized air pockets result in denser, more consistent 3D printed objects with improved mechanical properties.
What are the disadvantages of using spheroidized powders in 3D printing?
While advantageous, spheroidized powders do have some limitations in 3D printing:
- Higher cost: The spheroidization process adds to the overall powder price compared to non-spheroidized alternatives.
- Limited material selection: Not all printable materials can be effectively spheroidized.
- Process optimization: Utilizing spheroidized powders might require adjustments to existing 3D printing parameters for optimal results.
Are spheroidized powders safe to handle?
The safety of spheroidized powders depends on the specific material. Many common metals used in spheroidization, like stainless steel and titanium, are generally safe to handle with proper precautions. However, some materials may require specific handling procedures due to potential health risks like inhalation hazards.
Always consult the safety data sheet (SDS) for the specific spheroidized powder you’re using and follow recommended personal protective equipment (PPE) guidelines.
How are spheroidized powders produced?
Several techniques can be employed for spheroidization, but some of the most common methods include:
- Centrifugal Atomization: Molten metal is atomized into droplets that solidify into near-spherical particles during a high-speed spinning process.
- Plasma Rotating Electrode Process (PREP): A rotating electrode melts metal feedstock, and the molten droplets are spheroidized by plasma gas forces.
- Gas-assisted Spheroidization: Powder particles are fluidized in a hot environment and collide with each other, gradually rounding their shapes.
What are the future prospects for spheroidized powders?
The future of spheroidized powders is bright. As research and development continue, we can expect advancements in:
- Material selection: More materials are likely to become efficiently spheroidized, expanding the application possibilities.
- Cost-effective production: Technological advancements may lead to more economical spheroidization processes, making these powders more accessible.
- Tailored properties: Spheroidization techniques may be further refined to achieve specific properties in the final powder, such as controlled porosity or enhanced surface characteristics.
Share On
MET3DP Technology Co., LTD is a leading provider of additive manufacturing solutions headquartered in Qingdao, China. Our company specializes in 3D printing equipment and high-performance metal powders for industrial applications.
Inquiry to get best price and customized Solution for your business!
Related Articles
About Met3DP
Recent Update
Our Product
CONTACT US
Any questions? Send us message now! We’ll serve your request with a whole team after receiving your message.
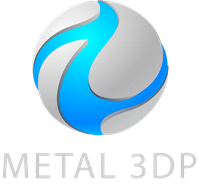
Metal Powders for 3D Printing and Additive Manufacturing