TC4 Powder: A Technical Overview
Table of Contents
TC4 powder, also known as titanium carbide, is an extremely hard ceramic material made up of titanium and carbon. It is characterized by high hardness, excellent wear resistance, good thermal conductivity, and high resistance to chemical attack. TC4 powder has a range of applications across diverse industries including aerospace, automotive, military, metal cutting and forming tools, and more.
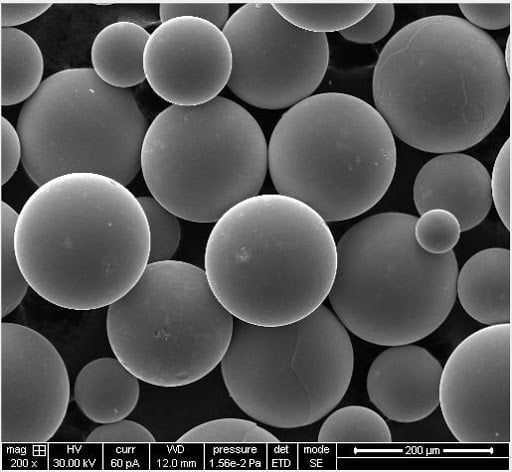
Composition of TC4 Powder
TC4 powder contains both titanium and carbon in varying proportions based on the grade. The titanium carbide chemical formula is TiC, but commercial TC4 powder can have carbon content ranging from 6.25% to 11.7% by weight.
Element | Weight % |
---|---|
Titanium (Ti) | 88.3 – 93.75 |
Carbon (C) | 6.25 – 11.7 |
By controlling the ratio of titanium to carbon, manufacturers can tailor the properties like hardness, toughness, and thermal conductivity. Higher carbon TC4 grades have higher hardness whereas lower carbon variants have greater toughness.
Properties and Characteristics of TC4 Powder
TC4 powder stands out due to its exceptional hardness and wear properties combined with good corrosion resistance. Here are the key technical characteristics and capabilities:
Property | Details |
---|---|
Hardness | 2800-3100 HV, up to 3500 HV for high carbon variants |
Density | 4.9 – 5.2 g/cm3 |
Melting point | 3160°C |
Thermal conductivity | ~35 W/m-K |
Coefficient of thermal expansion | 7.4 x 10-6/K |
Young’s modulus | 450 GPa |
Compressive strength | 1.7 – 3.5 GPa |
Chemical resistance | Resistant to acids, bases, salts, oxidizing environments up to 800°C |
The unparalleled hardness makes TC4 ideal for wear protection and cutting applications. It retains strength and corrosion resistance at high temperatures. The high thermal conductivity improves heat dissipation in tools and inserts.
Specifications and Grades of TC4 Powder
TC4 powder is available in a range of particle sizes, carbon content, and purity levels to meet application requirements:
Specification | Details |
---|---|
Particle sizes | 0.5 – 45 microns |
Carbon content | Low (6.25%), Medium (8%), High (10-11.7%) |
Purity | Up to 99% |
Crystal structure | Cubic |
Powder morphology | Angular, granular, spherical |
Grades | R, P, S, M |
Standards | ISO, RoHS |
Common TC4 powder grades include:
- Grade R – For sintered products with medium carbon 8%
- Grade P – High purity for special applications
- Grade S – For spraying and welding products
- Grade M – For molding and pressing
Higher purity, controlled particle size distribution, and consistent morphology results in higher quality sintered parts.
Applications and Uses of TC4 Powder
The unique properties of TC4 powder make it suitable for the following applications:
Industry | Applications |
---|---|
Metal cutting | Indexable inserts, end mills, drills, reamers |
Metal forming | Extrusion dies, swaging dies, wire drawing dies |
Mining | Rock drill bits, well drilling inserts |
Automotive | Camshafts, valves, seals |
Aerospace | Air seals, engine components |
Electronics | Thermal conductors, contacts |
Textiles | Textile machinery parts |
Pumps | Seals, bearings |
Medical | Surgical tools, implants |
The automotive sector uses TC4 powder for cams, valves and other engine components needing heat and wear resistance. The aerospace industry relies on it for air seals needing stability at high temperatures. TC4 powder also makes excellent cutting inserts with increased tool life.
TC4 Powder vs. Alternatives
Here is how TC4 powder compares to other hard materials in terms of properties and performance:
Property | TC4 | Tungsten Carbide | Silicon Carbide |
---|---|---|---|
Hardness | 2800 – 3500 HV | 1300 – 1900 HV | 2300 – 3000 HV |
Toughness | Medium | Higher | Lower |
Thermal conductivity | Higher | Lower | Higher |
Chemical resistance | Excellent | Poor | Excellent |
Oxidation resistance | Good | Excellent | Good |
Cost | Medium | Higher | Lower |
Advantages of TC4 powder:
- Extremely hard with excellent wear resistance
- Better corrosion resistance than tungsten carbide
- More thermally conductive than tungsten carbide
- Lower cost than tungsten carbide
Limitations of TC4 powder:
- More brittle than tungsten carbide, prone to chipping
- Not as chemically inert as silicon carbide
- Lower temperature stability than silicon carbide
So TC4 provides the best combination of hardness, toughness, thermal properties and cost for most applications. It outperforms tungsten carbide for wear protection and silicon carbide for high temperature stability.
TC4 Powder Pricing
TC4 powder is more expensive than titanium powder but lower cost compared to tungsten carbide powder. Here are typical prices per kg:
Grade | Purity | Price ($/kg) |
---|---|---|
R | 99% | 70 – 90 |
P | 99.5% | 100 – 130 |
S | 97% | 50 – 70 |
M | 96% | 40 – 60 |
Prices vary based on:
- Purity and oxygen/nitrogen content
- Particle size distribution
- Powder morphology (angular, spherical)
- Purchase quantity
- Supplier brand
High purity TC4 powder with controlled particle sizes can cost up to $130/kg whereas lower purity grades for pressing or welding start around $40/kg.
Where to Buy TC4 Powder
Here are some of the leading global suppliers manufacturing and selling TC4 titanium carbide powder:
Supplier | Location |
---|---|
Micron Metals | USA |
Atlantic Equipment Engineers | USA |
Met3DP | China |
I-Matec | Germany |
Inframat Advanced Materials | USA |
Beijing BoYu Tech | China |
When selecting a TC4 powder supplier, consider:
- Reputation and years in business
- Quality certifications
- Purity levels
- Particle size control
- Powder morphology
- Production capacity
- Pricing
- Customer service and technical support
Established companies like Micron Metals, ZhuZhou GuangYuan and Inframat Advanced Materials are leading producers with strict quality control and competitive pricing.
TC4 Powder: FAQs
Q: What is the difference between TC4 and TC16 powder grades?
A: TC16 powder has lower carbon content around 6.25% while TC4 powder has medium carbon around 8%. So TC16 has higher toughness while TC4 is harder.
Q: Is TC4 powder toxic?
A: TC4 powder is considered relatively non-toxic. But it may cause irritation upon contact with skin or eyes. Proper PPE should be used when handling.
Q: What is the best way to make TC4 parts?
A: Most TC4 components are made by sintering TC4 powder. Cold pressing and hot isostatic pressing can also be used. CVD deposition of TC4 is also possible.
Q: What industries use TC4 powder the most?
A: Cutting tools, aerospace engine parts, automotive components, and mining tools account for the bulk of TC4 powder consumption. The combination of hardness, wear resistance and temperature capabilities make it ideal for these applications.
Q: Does TC4 powder rust?
A: No, TC4 powder does not rust or corrode easily. It offers excellent corrosion resistance due to the presence of stable titanium carbide. TC4 retains its properties in a wide range of chemicals.
Q: Is TC4 powder fine grain or coarse?
A: TC4 powder is available in both fine micrograin sizes and coarser grain sizes. Fine powder below 10 microns is preferred for sintering while coarser 20-45 micron powder is used for welding or thermal spraying.
Q: Can TC4 powder be 3D printed?
A: Yes, advanced binder jetting and laser powder bed fusion techniques allow 3D printing complex geometries using TC4 powder for added hardness, strength, and wear resistance.
Share On
MET3DP Technology Co., LTD is a leading provider of additive manufacturing solutions headquartered in Qingdao, China. Our company specializes in 3D printing equipment and high-performance metal powders for industrial applications.
Inquiry to get best price and customized Solution for your business!
Related Articles
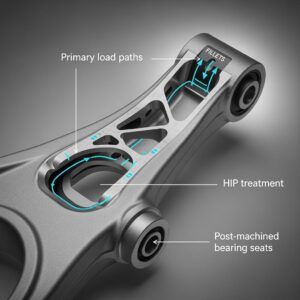
Metal 3D Printing for U.S. Automotive Lightweight Structural Brackets and Suspension Components
Read More »About Met3DP
Recent Update
Our Product
CONTACT US
Any questions? Send us message now! We’ll serve your request with a whole team after receiving your message.