The Comprehensive Guide to Thermal Spraying
Table of Contents
Thermal spraying is a fascinating and complex process that’s integral to numerous industrial applications. This article will dive deep into the intricacies of thermal spraying, offering a detailed overview, a discussion on specific metal powder models, and an analysis of its various applications, advantages, and limitations. We’ll also explore the specifications, grades, and standards involved, provide insights into suppliers and pricing, and conclude with a handy FAQ section.
Overview of Thermal Spraying
Thermal spraying is a coating process where melted or heated materials are sprayed onto a surface to form a protective or decorative layer. This technique is widely used in manufacturing, automotive, aerospace, and many other industries due to its versatility and effectiveness in improving surface properties.
What is Thermal Spraying?
Thermal spraying involves feeding a powder or wire into a flame or plasma jet to create a stream of molten particles. These particles are then propelled onto the surface to be coated, where they rapidly solidify, forming a durable layer. The process can be used to apply a wide range of materials, including metals, ceramics, plastics, and composites.
Why Use Thermal Spraying?
Thermal spraying offers several benefits:
- Enhanced Wear Resistance: It significantly improves the wear resistance of surfaces.
- Corrosion Protection: Provides excellent protection against corrosion.
- Thermal Insulation: Effective for thermal insulation applications.
- Electrical Conductivity: Can be used to create conductive coatings.
Key Processes in Thermal Spraying
The main thermal spraying processes include:
- Flame Spraying
- Plasma Spraying
- High-Velocity Oxy-Fuel (HVOF) Spraying
- Cold Spraying
- Electric Arc Spraying
Each of these processes has its unique advantages and is suited to specific applications.
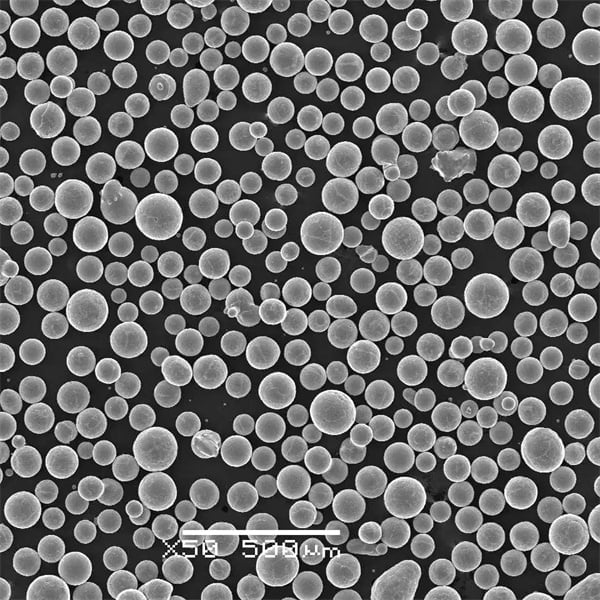
Types of Thermal Spraying Metal Powders
Metal powders used in thermal spraying are critical to the success of the coating process. Here are ten specific metal powder models widely used:
1. Alumina-Titania (Al2O3-TiO2) Powder
A blend of alumina and titania, this powder is known for its excellent wear resistance and electrical insulation properties. It’s often used in the electronics industry.
2. Chromium Carbide (Cr3C2) Powder
Chromium carbide powder is used for its exceptional hardness and resistance to wear and corrosion, making it ideal for high-temperature applications.
3. Cobalt-Chromium (CoCr) Powder
Cobalt-chromium alloys are favored for their high wear resistance and toughness. They are commonly used in medical implants and aerospace components.
4. Nickel-Aluminum (NiAl) Powder
Nickel-aluminum powders are known for their excellent bonding properties and are often used as a bond coat in thermal spraying applications.
5. Tungsten Carbide-Cobalt (WC-Co) Powder
This powder offers superior hardness and wear resistance, making it suitable for extreme wear conditions.
6. Stainless Steel (316L) Powder
316L stainless steel powder is corrosion-resistant and is used in a variety of applications, including marine and medical devices.
7. Zirconia (ZrO2) Powder
Zirconia powder is used for its thermal insulation properties and is commonly applied in thermal barrier coatings.
8. Molybdenum (Mo) Powder
Molybdenum powder is known for its high melting point and excellent thermal and electrical conductivity, making it useful in various industrial applications.
9. Copper (Cu) Powder
Copper powder is used for its electrical and thermal conductivity properties, often in the electronics industry.
10. Iron (Fe) Powder
Iron powder is used in applications requiring good wear resistance and magnetic properties.
Applications of Thermal Spraying
Thermal spraying is used across a broad spectrum of industries. Here’s a detailed look at some key applications:
Industry | Application | Description |
---|---|---|
Aerospace | Turbine Blades | Thermal spraying provides thermal barriers and wear resistance to turbine blades. |
Automotive | Engine Components | Enhances wear resistance and lifespan of engine parts. |
Oil & Gas | Pipelines | Protects against corrosion and wear in harsh environments. |
Medical | Implants | Used in coatings for biocompatibility and wear resistance in implants. |
Electronics | Circuit Boards | Provides conductive coatings and thermal management solutions. |
Power Generation | Boiler Tubes | Protects against high-temperature corrosion and erosion. |
Manufacturing | Molds and Dies | Improves surface hardness and extends tool life. |
Advantages of Thermal Spraying
Thermal spraying offers numerous benefits compared to other coating methods. Here’s a detailed comparison:
Advantage | Description |
---|---|
Versatility | Can be used with a wide range of materials. |
Cost-Effective | Provides a cost-effective solution for extending the life of components. |
Performance | Enhances performance by improving wear, corrosion, and heat resistance. |
Flexibility | Suitable for various shapes and sizes of components. |
Efficiency | Rapid application process with minimal downtime. |
Disadvantages of Thermal Spraying
Despite its advantages, thermal spraying has some limitations:
Disadvantage | Description |
---|---|
Surface Preparation | Requires thorough surface preparation for effective adhesion. |
Equipment Cost | High initial investment in thermal spraying equipment. |
Complexity | The process can be complex and requires skilled operators. |
Thickness Limitation | Limited to certain coating thicknesses without compromising quality. |
Specifications, Sizes, Grades, and Standards
Thermal spraying materials and processes must meet specific standards and specifications to ensure quality and performance. Here are some details:
Material | Standard | Grade | Size |
---|---|---|---|
Alumina-Titania | ISO 14919 | 99% Purity | 15-45 µm |
Chromium Carbide | ASTM B833 | 75-80% Cr3C2 | 10-45 µm |
Cobalt-Chromium | AMS 5889 | CoCrW | 15-53 µm |
Nickel-Aluminum | ISO 14920 | Ni5Al | 10-45 µm |
Tungsten Carbide-Cobalt | ASTM B794 | WC-12Co | 15-45 µm |
Stainless Steel | ISO 5832-1 | 316L | 15-53 µm |
Zirconia | ASTM F1598 | 8Y-ZrO2 | 15-53 µm |
Molybdenum | ASTM B387 | 99% Purity | 15-53 µm |
Copper | ASTM B216 | 99% Purity | 10-45 µm |
Iron | ASTM B749 | Fe | 10-45 µm |
Suppliers and Pricing Details
Finding the right supplier is crucial for obtaining high-quality thermal spraying materials. Here’s a table with some leading suppliers and their pricing:
Supplier | Material | Price (per kg) | Location |
---|---|---|---|
Praxair | Tungsten Carbide-Cobalt | $100 | USA |
Höganäs | Nickel-Aluminum | $60 | Sweden |
Metco | Chromium Carbide | $80 | Switzerland |
Carpenter | Cobalt-Chromium | $120 | USA |
Oerlikon | Alumina-Titania | $70 | Switzerland |
Kennametal | Stainless Steel | $50 | USA |
HC Starck | Zirconia | $90 | Germany |
Sandvik | Molybdenum | $85 | Sweden |
Tekna | Copper | $40 | Canada |
H.C. Starck | Iron | $30 | Germany |
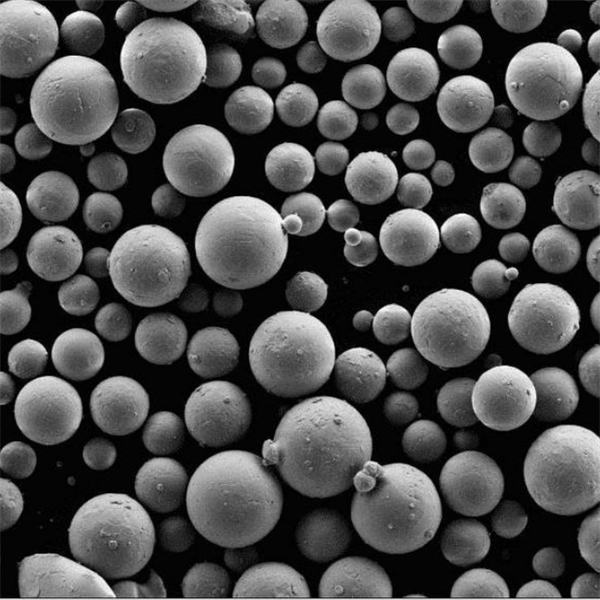
Comparing Pros and Cons of Thermal Spraying
When choosing a coating process, it’s essential to weigh the pros and cons. Here’s a comparison:
Aspect | Pros | Cons |
---|---|---|
Cost | Cost-effective for large components | High initial equipment cost |
Durability | Excellent wear and corrosion resistance | Surface preparation required |
Versatility | Suitable for various materials and applications | Complexity in operation |
Efficiency | Rapid coating process | Thickness limitations |
FAQ
Q1: What materials can be used in thermal spraying?
A1: A wide range of materials including metals, ceramics, plastics, and composites.
Q2: What industries benefit the most from thermal spraying?
A2: Aerospace, automotive, oil & gas, medical, electronics, power generation, and manufacturing.
Q3: What are the primary advantages of thermal spraying?
A3: Enhanced wear resistance, corrosion protection, thermal insulation, and electrical conductivity.
Q4: What are the typical limitations of thermal spraying?
A4: Requires surface preparation, high equipment cost, complexity, and thickness limitations.
Share On
MET3DP Technology Co., LTD is a leading provider of additive manufacturing solutions headquartered in Qingdao, China. Our company specializes in 3D printing equipment and high-performance metal powders for industrial applications.
Inquiry to get best price and customized Solution for your business!
Related Articles
About Met3DP
Recent Update
Our Product
CONTACT US
Any questions? Send us message now! We’ll serve your request with a whole team after receiving your message.