Application of titanium alloy 3D printed powders in the aerospace
Table of Contents
The aerospace industry is constantly pushing the boundaries of what’s possible. Imagine building an airplane lighter, stronger, and more fuel-efficient than ever before. That’s the promise of titanium alloy 3D printed powder, a revolutionary technology transforming how we design and manufacture aircraft. Buckle up, because we’re about to delve into the fascinating world of 3D printed titanium and explore its numerous applications in the exciting realm of aerospace.
The Allure of Titanium: A Marriage of Strength and Lightness
For decades, titanium has been a darling of the aerospace industry. Why? It’s all about that magic combination of strength and lightness. Titanium boasts a high strength-to-weight ratio, meaning it’s incredibly strong for its weight. This translates to aircraft that can carry more weight, fly further, and achieve better fuel efficiency. Think of it like this: Imagine a car built from feathers – that’s the kind of weight reduction titanium offers while maintaining the structural integrity needed to soar through the skies.
But traditional manufacturing of titanium parts has limitations. Machining complex shapes can be challenging and wasteful, leaving behind significant scrap metal. Enter 3D printing, a game-changer for the aerospace industry.
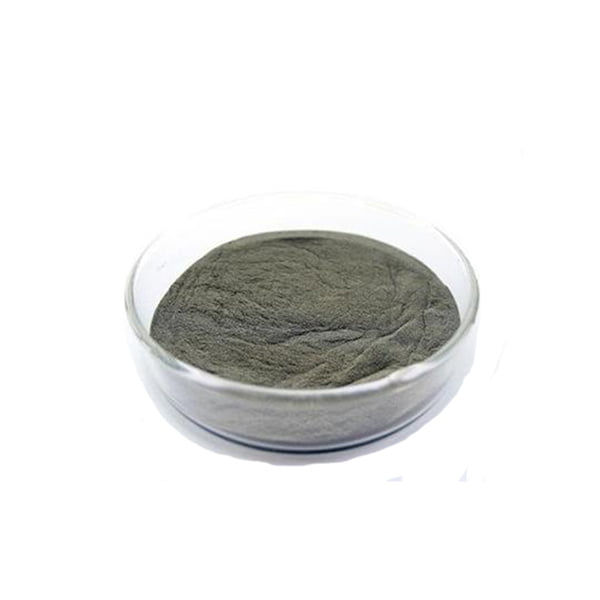
3D Printing: Building with Powder, One Layer at a Time
3D printing, also known as additive manufacturing, works like a magical sculptor, building objects layer by layer. In the case of titanium alloy powder, a laser beam melts tiny particles of the powder together, meticulously following a digital blueprint. This allows for the creation of intricate, lightweight structures that would be impossible with traditional methods.
Here’s the beauty of titanium alloy 3D printed powders:
- Design Freedom: Unleash your imagination! Complex geometries and internal lattice structures become achievable, leading to significant weight reduction and improved performance.
- Reduced Waste: Say goodbye to mountains of scrap metal. 3D printing uses only the necessary material, minimizing waste and environmental impact.
- Customization: Need a part with specific properties? No problem! Different titanium alloys can be used, and printing parameters can be adjusted to tailor the final product’s strength and weight characteristics.
Popular titanium alloy 3D printed powder in Aerospace
There’s no one-size-fits-all solution when it comes to titanium alloys for 3D printing in aerospace. Different applications demand specific properties. Let’s explore some of the most popular choices:
- TC4 Titanium Alloy Powder: This workhorse alloy offers a good balance of strength, ductility (the ability to bend without breaking), and weldability. It’s a popular choice for manufacturing components of aircraft engines and important load-bearing components of aircraft, such as landing gear parts.
- TC6 Titanium Alloy Powder: Known for its exceptional strength and high fatigue resistance, TC6 titanium alloy powder is a champion for aircraft structural components. Think of it as the titanium skeleton of the airplane, providing the framework for everything else. Additionally, it finds application in engine components and landing gear components where high strength is paramount.
- TA15 Titanium Alloy Powder: Corrosion resistance is key in the harsh environment of high altitudes. TA15 titanium alloy powder shines in this area, making it ideal for manufacturing corrosion-resistant aircraft structural components and engine components that can withstand the elements.
It’s important to note that this is not an exhaustive list. Researchers are constantly developing new and improved titanium alloys specifically designed for the demands of 3D printing and aerospace applications.
Examples of 3D Printed Titanium in Action
The potential of titanium alloy 3D printed powder isn’t just theoretical; it’s taking flight in real-world applications. Here are some exciting examples:
- Airbus: The European aviation giant, Airbus, has been at the forefront of utilizing 3D printed titanium components. They’ve successfully incorporated 3D printed titanium brackets into the A350 XWB passenger jet, achieving significant weight reduction.
- GE Aviation: This industry leader is leveraging 3D printing to manufacture complex fuel nozzles for jet engines. These nozzles are not only lighter but also boast improved cooling efficiency, leading to better fuel burn.
- Boeing: The American aerospace giant, Boeing, is also embracing 3D printing technology. They’ve used 3D printed titanium components in their 787 Dreamliner aircraft, contributing to its impressive fuel efficiency.
These are just a few examples, and as the technology matures, we can expect to see even more widespread adoption of titanium alloy 3D printed powder in aerospace applications.
The Future Soars Bright: Challenges and Opportunities
While 3D printed titanium alloy powder offers a revolution in aerospace manufacturing, there are still challenges to overcome. Here are some key considerations:
- Cost: Currently, titanium alloy 3D printed powder can be a costly proposition compared to traditional manufacturing methods. The cost of the titanium powder itself, coupled with the specialized equipment and expertise required for printing, adds up. However, as the technology matures and production scales up, we can expect costs to come down.
- Post-Processing: 3D printed titanium parts may require additional post-processing steps, such as heat treatment and surface finishing, to achieve the desired properties. These steps can add to the overall production time and cost.
- Quality Control: Ensuring consistent quality in 3D printed titanium parts requires robust quality control procedures. Monitoring the printing process and rigorously testing the final product are crucial to ensure the safety and performance of aircraft components.
Despite these challenges, the opportunities offered by titanium alloy 3D printed powder are vast:
- Lightweighting: The relentless pursuit of lighter aircraft continues. 3D printing’s ability to create complex, lightweight structures with minimal waste will be a key driver in achieving even greater fuel efficiency and range.
- Performance Optimization: The ability to customize parts through different alloys and printing parameters opens doors to optimizing components for specific applications. Imagine designing an engine blade that’s not only lighter but also has superior heat resistance.
- Supply Chain Agility: Traditional manufacturing often involves long lead times and geographically dispersed production lines. 3D printing allows for on-demand production, potentially reducing lead times and increasing supply chain flexibility.
- Spare Parts: Imagine needing a replacement part for an aircraft on the ground. With 3D printing, the possibility of on-site or near-site production of spare parts becomes a reality, minimizing downtime and delays.
The future of aerospace is undoubtedly intertwined with the advancements in titanium alloy 3D printed powder. As we overcome the challenges and unlock the full potential of this technology, we can expect to see a new generation of lighter, more efficient, and high-performance aircraft gracing the skies.
FAQ
Here are some of the most common questions regarding titanium alloy 3D printed powder in aerospace:
Q: What are the advantages of using 3D printed titanium alloy powder in aerospace?
A: The key advantages include:
- Lighter aircraft: Reduced weight translates to improved fuel efficiency and increased range.
- Design freedom: Complex geometries and internal structures become achievable, leading to further weight reduction and performance optimization.
- Reduced waste: 3D printing minimizes scrap metal compared to traditional manufacturing methods.
- Customization: Tailoring parts for specific applications through different alloys and printing parameters.
Q: What are the limitations of 3D printed titanium alloy powder?
A: Current limitations include:
- Cost: 3D printing titanium powder can be expensive compared to traditional methods.
- Post-processing: Additional steps like heat treatment and surface finishing might be required.
- Quality control: Rigorous procedures are essential to ensure consistent quality in printed parts.
Q: What are some real-world examples of 3D printed titanium being used in aerospace?
A: Here are a few examples:
- Airbus A350 XWB: 3D printed titanium brackets contribute to weight reduction.
- GE Aviation jet engines: Complex fuel nozzles are 3D printed for improved performance.
- Boeing 787 Dreamliner: 3D printed titanium components contribute to fuel efficiency.
Q: What does the future hold for 3D printed titanium alloy powder in aerospace?
A: The future is bright! We can expect:
- Reduced costs: As technology matures, production scales up, and costs are expected to come down.
- Performance optimization: Customization will lead to parts designed for specific applications with superior performance.
- Supply chain agility: On-demand production might revolutionize spare parts availability.
The potential of 3D printed titanium alloy powder to transform aerospace manufacturing is clear. With continued advancements and collaboration between engineers, material scientists, and manufacturers, the future of flight promises to be lighter, more efficient, and soar to new heights.
Share On
MET3DP Technology Co., LTD is a leading provider of additive manufacturing solutions headquartered in Qingdao, China. Our company specializes in 3D printing equipment and high-performance metal powders for industrial applications.
Inquiry to get best price and customized Solution for your business!
Related Articles
About Met3DP
Recent Update
Our Product
CONTACT US
Any questions? Send us message now! We’ll serve your request with a whole team after receiving your message.
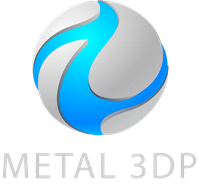
Metal Powders for 3D Printing and Additive Manufacturing