Titanium Aluminide Manufacturing
Table of Contents
Titanium aluminides are a class of lightweight, high temperature resistant alloys with excellent corrosion resistance and attractive properties for aerospace and automotive applications. This article provides a comprehensive guide to titanium aluminide manufacturing, including key processing methods, equipment considerations, design principles, and supplier landscape.
Titanium Aluminide Manufacturing Process
Titanium aluminides are challenging to fabricate using conventional titanium processing routes due to their low room temperature ductility. Advanced techniques have been developed to produce high quality titanium aluminide components.
Table 1. Comparison of major titanium aluminide manufacturing processes
Casting | Powder Metallurgy | Forging | Additive Manufacturing |
---|---|---|---|
Investment casting | Hot isostatic pressing | Closed die forging | Laser powder bed fusion |
Ceramic mold casting | Metal injection molding | Open die forging | Binder jetting |
Centrifugal casting | Rotary forging | Directed energy deposition | |
Plasma arc melting | Electron beam melting |
Casting of Titanium Aluminides
Investment casting is most widely used for titanium aluminides as it enables complex, net shape components with tight tolerances. Ceramic mold casting and centrifugal casting are also applied on a limited basis. Control of melt cleanliness, mold interaction, and cooling rate are critical during solidification to achieve target properties.
Powder Metallurgy Processing
Powder metallurgy techniques like hot isostatic pressing (HIP) and metal injection molding (MIM) are used due to their near net shape capability. Fine homogeneous microstructures can be attained through rapid cooling after HIP. MIM offers flexibility for complex shapes but has limitations on section thickness.
Forging of Titanium Aluminides
Forging requires high temperatures (900-1200°C) to achieve adequate workability. Closed die forging with rapid cooling produces sound structures but is limited to simpler geometries. Open die forging and rotary forging provide flexibility for larger components. Tight control of strain rate and temperature is essential to avoid defects.
Additive Manufacturing of Titanium Aluminides
Additive manufacturing (AM) methods like laser powder bed fusion (PBF), binder jetting, and directed energy deposition are beginning to be applied for titanium aluminides. AM enables complex geometries without dies/molds but has challenges with porosity, surface finish, and properties. Parameters must be precisely optimized.
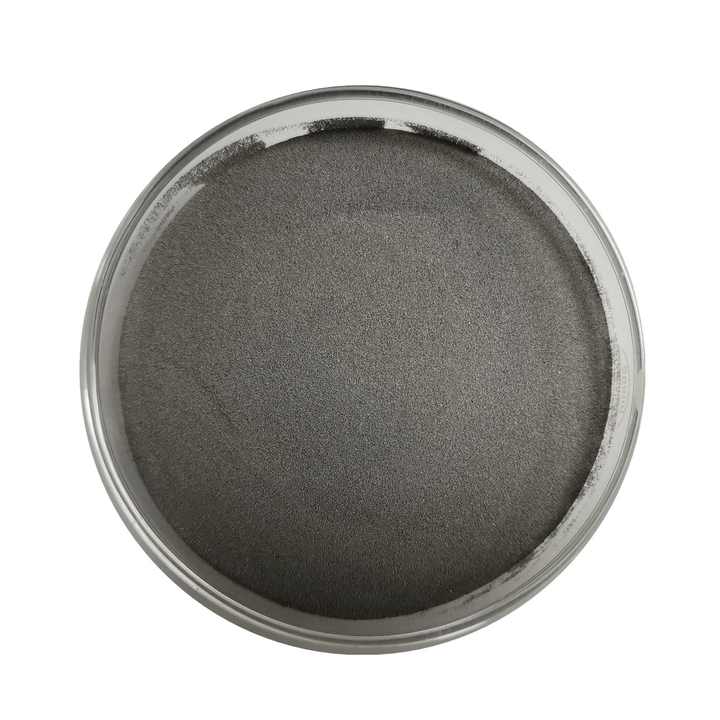
Equipment for Titanium Aluminide Production
Special equipment is necessary for melting, casting, consolidation, heat treatment, and machining of titanium aluminides due to their poor room temperature formability.
Table 2. Overview of equipment used in titanium aluminide manufacturing
Category | Example Equipment | Key Characteristics |
---|---|---|
Melting | Vacuum induction melting Electron beam melting Plasma arc melting | Controlled atmosphere melting with low contamination |
Casting | Investment casting equipment Ceramic mold rigs Centrifugal casting machines | Rapid cooling capabilities Chemically inert mold materials |
Consolidation | Hot isostatic presses Forging presses | High temperature, pressure, accuracy capabilities |
Heat Treatment | Vacuum/inert gas furnaces | Controlled atmosphere with rapid quenching |
Machining | CNC mills/lathes with rigid setup | Excellent surface finish standards |
The equipment must maintain cleanliness while achieving extremely high temperatures and pressures. Integrated vacuum or inert gas systems protect against contamination during processing. Precise control of temperature uniformity and cooling rates are also critical to achieve target microstructures.
Facility Design & Layout Considerations
Facility design requires close integration of foundry operations, machining, quality control, and heat treatment for titanium aluminide production.
Table 3. Facility considerations for titanium aluminide manufacturing
Parameter | Guidelines |
---|---|
Material Flow | Linear flow from melt to finish machines |
Building Layout | Adjacent stations; Minimal operator motion |
Flexibility | Extra floor space; Versatile equipment |
Containment & ventilation | Separated areas; Dedicated ventilation |
Contamination Control | Positive pressure zones; Airlocks |
Utility Requirements | Redundant power & cooling lines |
Quality Monitoring | Distributed lab space; Inline inspection |
Safety Systems | Spill containment; Inert gas detectors |
There should be optimized operator and material flow to minimize contamination opportunities. Flexible stations enable configuration changes to meet evolving demands. Utility capacity and redundancy levels must be sized appropriately to supply critical operations. Extensive monitoring and inline inspection identifies quality issues early. Integrated safeguards protect against gas leaks and spills.
Customization & Variants
Titanium aluminide alloy compositions and manufactured forms can be customized to meet application requirements.
Table 4. Major alloy variants and options for customization
Parameter | Variants |
---|---|
Alloying Elements | Al, Nb, Mo, Ta, Cr, Ni, Si |
Aluminum Content | 32-48% Al |
Product Form | Cast, Wrought, Powder, Coating |
Shape Complexity | Net shape to complex geometry |
Section Thickness | < 1mm to > 30mm |
Coatings | Diffusion coatings e.g. aluminides |
Post Processing | Heat treatment, HIP, Machining |
Testing/Certification | Mechanical, metallographic, NDT, process validation |
The high temperature performance can be tailored by adjusting aluminum levels and alloying additions. Products range from simple castings to intricate HIP powder metallurgy components. Section thickness, tolerances, surface finish, and inspection/testing standards can be specified as needed. Protective coatings further extend service life in demanding environments.
Supplier Ecosystem & Cost Metrics
A niche supply base has experience in titanium aluminide manufacturing. Buyers should assess suppliers on process maturity, certification status, and application expertise during vendor selection.
Table 5. Supplier landscape and cost structure for titanium aluminide parts
Type | Leading Companies | Pricing Factors | Cost Ranges |
---|---|---|---|
Cast Products | Access Technologies CIREX JAMCO | Complexity, volume, size, QA/QC | $40-150/lb |
Wrought Products | ATI VSMPO-AVISMA | Section thickness, purity, order size | $70-250/lb |
Powder/HIP | GKN Praxair | Final density, machining, tolerance | $90-350/lb |
Additive Manufacturing | Carpenter AP&C | Buy-to-fly ratio, post processing | $150-600/lb |
Cost metrics show wide value ranges depending on product type, order volume, quality requirements, section thickness, and degree of finishing operations. Economies of scale apply for large orders. Comprehensive quality documentation adds cost but ensures performance reliability and mitigates operational risks for end users.
Installation, Operation & Maintenance
Proper installation, operation, and preventative maintenance of equipment minimizes downtime and promotes safety in titanium aluminide production facilities.
Table 6. Guidelines for installation, operation, and maintenance
Stage | Actions |
---|---|
Installation | Ensure correct equipment alignment Verify utility & exhaust connections Calibrate sensors, controllers & safety systems |
Operation | Follow all loading/unloading procedures Maintain inert atmosphere always Control process parameters within certified range |
Preventative Maintenance | Regularly inspect welds, thermocouples etc. Proactively replace worn components |
Corrective Maintenance | Develop contingency plans for common failure modes Store spare parts onsite for critical equipment |
Thorough site acceptance testing should be conducted before commencing production campaigns. During runs, strict conformance to validated parameters is mandatory. Production equipment must be frequently monitored, maintained and updated to sustain output quality and volumes. Keeping contingency plans and spares helps minimize the impact of unplanned downtime.
Supplier Selection Guidelines
Careful assessment of suppliers using weighted criteria can help identify the right titanium aluminide manufacturing partner.
Table 7. Major parameters for rating and selecting suppliers
Category | Evaluation Criteria | Rating Metrics |
---|---|---|
Capability Profile | Years in business Types of alloys and products | >10 yrs preferred Align with application |
Facility Resources | Capacity scalability Inventory stations | Growth ability JIT supply readiness |
Technology Maturity | Process consistency Certification status | Cpk > 2.0 ISO, AS9100 compliant |
Quality & Delivery | Acceptance rate On-time rate trends | >99% preferred 95%+ on-time |
Cost Structure | Operating costs Economies of scale | Flexible overhead types Volume-based discounts |
Customer Support | Design assistance Application expertise Field troubleshooting | Full development partner Value-add beyond production |
Quantitative KPIs based on standards like acceptance rate as well as qualitative factors like technical alignment and responsiveness should factor into supplier selection rubrics. Two to three supplier candidates that rank favorably across weighted criteria help secure a resilient supply chain. backups provide continuity assurance if issues arise with a particular vendor.
Pros and Cons of Titanium Aluminide Parts
Table 8. Comparison of advantages and limitations for titanium aluminide alloys
Benefits & Drivers | Challenges & Limitations |
---|---|
– High strength-to-weight ratio – Retains strength at >600°C – Outstanding corrosion resistance – Enables lightweight aerospace designs – Reduces component weight 20-30% vs nickel alloys | – Relatively high materials cost – Low room temperature ductility – Difficult to machine and form – Requires advanced processing methods – Limited industry experience and data |
Titanium aluminide alloys enable game changing weight reduction in aerospace systems together with excellent environmental durability which drives adoption despite steep pricing. However manufacturers still face hurdles with attaining adequate ductility at room temperature for some applications. The operating envelope is narrow which complicates designing components and modeling failure modes without extensive test data. Limited commercial usage history poses challenges with qualifying lifing methodologies over full lifecycles.
Industry Outlook and Key Trends
Adoption of titanium aluminide alloys is projected to expand at 9% CAGR over the next decade driven by rising demand for lightweighting in aerospace engines and airframes.
Figure 1. Global titanium aluminide market size forecast
Additive manufacturing and powder metallurgy breakthroughs are making complex geometries feasible. Multi-material designs with titanium aluminide inserts are gaining traction as well. Continued advancements in processing science and frontrunner usage in defense programs will spur further commercial deployment.
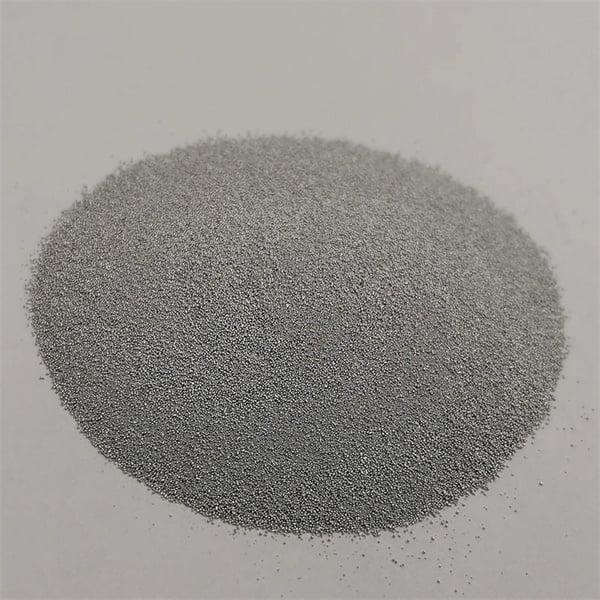
FAQ
Q: What are some example components made from titanium aluminide alloys?
A: Rotating blades, casings, fasteners, seals, valves, landing gear components, and structural brackets in aircraft engines and airframes are prime candidates in aerospace systems. Wheels, turbocharger rotors, valves, connecting rods and drive shafts in automotive also take advantage of titanium aluminides.
Q: What post-treatment options are commonly used with titanium aluminide parts?
A: Protective coatings (aluminide or ceramic-based), heat treatments, hot isostatic pressing, and various finishing operations like CNC machining, drilling, contour grinding are frequently employed depending on requirements.
Q: How should I estimate lead times for titanium aluminide parts?
A: Cast products typically require 90-120 days lead time. HIP and wrought products commonly need 120-180 days. For qualified suppliers under contract, customers ordering repeated designs may attain lead times as low as 45-60 days.
Q: What quality standards apply for titanium aluminide parts?
A: Many customers insist on ISO, AS9100, and/or Nadcap certification for aerospace orders. Full traceability and compliance to AMS standards are also expected. Stringent testing includes chemical analysis, mechanical testing, metallography, non-destructive inspection, and process validation.
Q: How should titanium aluminide components be handled and stored?
A: Care should be taken to avoid any contamination during post-production handling including use of gloves. Storage recommendations are to keep sealed titanium aluminide parts in dry nitrogen atmosphere. Proper handling precautions need to be flowed down through the supply chain.
Share On
MET3DP Technology Co., LTD is a leading provider of additive manufacturing solutions headquartered in Qingdao, China. Our company specializes in 3D printing equipment and high-performance metal powders for industrial applications.
Inquiry to get best price and customized Solution for your business!
Related Articles
About Met3DP
Recent Update
Our Product
CONTACT US
Any questions? Send us message now! We’ll serve your request with a whole team after receiving your message.
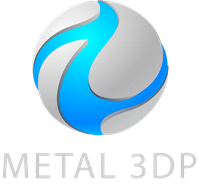
Metal Powders for 3D Printing and Additive Manufacturing