Introduction to Titanium Metal Powder
Table of Contents
Titanium metal powder is a versatile material with unique properties that make it suitable for a wide range of applications across industries. This article provides a comprehensive guide to titanium metal powder, including an overview of its properties, manufacturing methods, applications, suppliers, costs, installation, operation and maintenance considerations.
Overview of Titanium Metal Powder
Titanium metal powder refers to fine particles of titanium metal used as a raw material for various manufacturing processes. Here are some of its key traits:
- High strength-to-weight ratio
- Excellent corrosion resistance
- Ability to withstand extreme temperatures
- Non-toxic and non-allergic
- Non-magnetic
- Reactive and flammable in pure form
The unique combination of physical, chemical and mechanical properties allows titanium metal powder to outperform other materials in specific applications. It is as strong as steel but much lighter in weight, making titanium metal parts ideal for aerospace and automotive uses. The high resistance to corrosion facilitates use in seawater environments. Biocompatibility expands options in the medical sector.
There are four main grades of titanium metal powder categorized by purity levels:
- Grade 1 – Most commercially pure with lowest alloy content
- Grade 2 – Very similar properties to Grade 1
- Grade 3/4 – Stronger with the addition of aluminum and vanadium alloys
- Grade 5/23 – Contains 6% aluminum, 4% vanadium allowing further enhancement of strength for high temperature applications
Table 1: Grades of titanium metal powder and their properties
Grade | Purity | Alloying Elements | Properties |
---|---|---|---|
Grade 1 | 99.2%+ pure titanium | N/A | Excellent corrosion resistance, good formability and weldability |
Grade 2 | 99%+ pure titanium | N/A | Similar properties as Grade 1 |
Grade 3/4 | 96 – 98.9% titanium | Aluminum, vanadium | Higher strength while retaining good corrosion resistance |
Grade 5/23 | 90 – 94.5% titanium | 6% aluminum, 4% vanadium | Highest strength, heat treatable |
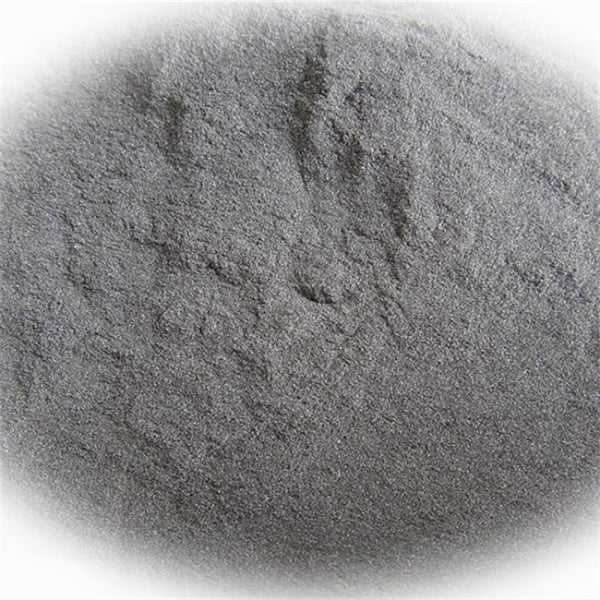
Manufacturing Processes for Titanium Metal Powder
Titanium metal powder is not found naturally – the manufacturing process involves reducing titanium dioxide or titanium tetrachloride to pure titanium metal, which is then converted into a powder. The three primary production methods include:
1. Gas Atomization Process
- Inert gas used to atomize molten titanium stream into fine droplets that solidify into powder
- Nitrogen, argon or helium gases can be used
- Produces spherically shaped powder ideal for additive manufacturing uses
- Tight distributions of particle size and morphology
2. Plasma Atomization Process
- Uses plasma torches to melt feed material and break it into particles
- Produces high quality spherical powders from reactive materials like titanium
- Advanced control over particle size distribution
- Provides high deposition rates and process efficiency
3. Hydride-Dehydride (HDH) Process
- Powder produced through repeated exposure of titanium material to hydrogen gas
- Input material crushed and hydrogenated to make brittle titanium hydride
- Further crushing creates fine particle powder
- Final hydrogen removal via vacuum leaves titanium metal powder
- Cost-effective process but can leave porous, irregularly shaped particles
Table 2: Comparison of titanium metal powder production methods
Parameter | Gas Atomization | Plasma Atomization | HDH Process |
---|---|---|---|
Feed Material | Titanium ingots | Titanium ingots | Titanium sponge, scrap |
Process Principle | Inert gas atomization | Plasma torch heating | Hydrogenation/dehydrogenation |
Particle Morphology | Highly spherical | Highly spherical | Irregular, porous |
Particle Size Control | Excellent | Excellent | Moderate |
Purity | High | Very high | Moderate |
Cost | High | Very high | Low |
Applications of Titanium Metal Powder
The distinct material properties of titanium metal powder make it suitable for niche applications across the following industries:
Aerospace Applications
- Aircraft engine and structural components
- Missiles, rockets, space vehicles
- Strength-to-weight ratio ideal for performance
Biomedical Applications
- Orthopedic and dental implants
- Surgical instruments and medical devices
- Biocompatibility and non-toxic properties critical
Automotive Applications
- Connecting rods, valves, springs, fasteners
- Wheels, under-the-hood components
- Motorsports use high-performance alloys
Chemical Applications
- Process equipment for corrosive environments
- Heat exchangers, tanks, pipes, pumps
- Resistance to wide range of acids
Additive Manufacturing
- 3D printing of titanium metal parts
- Aerospace, automotive, medical sectors
- Design freedom and customization
For each area, specific titanium grades and alloys are chosen to meet mechanical property, corrosion resistance and high temperature stability demands. Product design engineers normally determine the optimum grade based on service conditions.
How to Choose a Titanium Metal Powder Supplier
With critical applications relying on consistent high quality powder, proper supplier selection is vital when sourcing titanium metal powder. Below are key considerations:
Table 3: Selection criteria for titanium metal powder suppliers
Parameter | Details |
---|---|
Powder Production Method | Gas atomization, plasma atomization and HDH process based powders available. Choose based on required powder characteristics. |
Powder Morphology and Size Distribution | Spherical powder morphology provides better packing density and properties. Narrow distribution ensures process stability. |
Chemical Composition | Purity levels vary across grades. Use grade required for target material properties. |
Quality Standards | Supplier should have quality management certification for processes used. |
Customization Available | Ability to customize particle size distribution, morphology and alloying possible. Check if supplier offers this flexibility. |
Post Processing Capabilities | Additional services like thermal treatment, sieving, blending, surface modification add value. |
Technical Support | Application engineering assistance for materials selection and technical queries increases confidence. |
Delivery Lead Times | Shorter lead times allow quicker customer production scheduling after orders. |
Location | Geographic proximity lowers costs and lead times. |
Carefully examining each parameter allows the selection of the best titanium powder supplier for your production requirements. Analyzing a few potential suppliers on these criteria gives a relative standing. Additional factors like market reputation, customer references, certifications and pricing terms help finalize the decision.
Cost Analysis of Titanium Metal Powder
As a specialized high performance material, titanium metal powder sits at a premium price point. Cost depends on:
- Titanium grade: Higher purity grades are more expensive
- Powder production method: Gas atomization and plasma atomization powders command very high pricing
- Morphology and size distribution: Spherical powders with controlled distributions cost more
- Quantity ordered: Prices are highest for low volume orders and reduce significantly with scale
- Processing: Additional services like thermal treatment, blending, and sieving increase costs
Industrial grade titanium powder suitable for additive manufacturing starts at approximately $50 per kg, going up to $500 per kg for the highest quality variants. Aerospace and medical grades used in critical applications can cost between $200 per kg up to $1000 per kg. For context, aluminum and steel powders for 3D printing use cost $20-30 per kg and $10-15 per kg respectively.
Table 4: Price range for titanium metal powder based on grade, order volume and processing
Parameter | Price Range |
---|---|
Powder Grade | $50 – $1000 per kg |
Order Quantity | <10 kg: $200+ per kg 100 kg: $100 – $150 per kg 1000 kg: $50 – $100 per kg |
Production Method | Gas atomized: $150+ per kg HDH Process: $50+ per kg |
Particle Morphology | Spherical: $100+ per kg Irregular: $50+ per kg |
Alloying Additions | Unalloyed: $50 – $500 per kg Alloyed Grades: $100 – $1000+ per kg |
Post Processing | Basic powder: $50 – $500 per kg Thermal treatment: +$100 per kg Sieving: +$50 per kg |
Installing and Operating Titanium Powder Production Equipment
Setting up powder production lines requires significant capital investment, with specialized equipment costing several million dollars. For gas atomization and plasma atomization plants, the key components include:
- High capacity induction melting furnaces
- Large inert gas supply and storage tanks
- Gas delivery control modules with flow control valves and spray nozzles
- Cyclone separators to extract fine powder from gas streams
- Complete system automation hardware and software
Table 5: Installation and operation guidelines for titanium powder production plants
Stage | Guidelines |
---|---|
Site Selection | – Choose location with infrastructure for material delivery and powder distribution – Ensure adequate space, utilities supply |
Foundation | – Strong concrete flooring required to support heavy equipment – Vibration damping supports for certain equipment |
Assembly | – Assemble sections as per equipment vendor instructions – Ensure gas, power and water connections set up |
Safety | – Install emergency stop circuits, pressure relief valves – Exhaust gas management system – Explosion suppression system |
Commissioning | – Follow vendor protocols for dry run, inert gas flushing, parameter tuning, trial powder production |
Operation | – Maintain inert gas levels continuously – Control melting temperatures precisely – Meet all environment health and safety requirements |
Maintenance | – Equipment inspections as per maintenance manual – Replace worn out consumable parts regularly |
In addition to production equipment, equally important auxiliary systems need installation for material handling, powder recovery, powder characterization, storage and packaging.
Operation must follow environmental health safety guidelines regarding gas handling, combustion risks, explosions and metal fume exposure. Staff operating the equipment requires thorough technical training to ensure safe, efficient and sustainable production. Periodic maintenance is vital – any uncontrolled impurity ingress or parameter excursion can ruin entire powder batches costing huge losses.
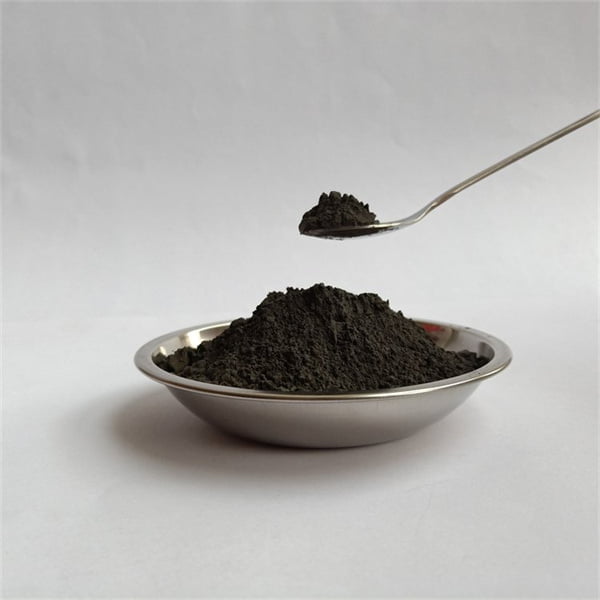
FAQ
Q: What particle size range does titanium metal powder normally fall into?
A: The typical size range is 10 – 150 microns, though it depends on the production technique used. Gas atomized spherical powder is generally on the lower end between 10 – 45 microns. Irregular HDH powder can go up to around 150 microns.
Q: Does titanium powder require special storage?
A: Yes, titanium reacts easily with oxygen so the powder is stored in sealed containers under inert argon or nitrogen atmosphere to prevent oxidation. This maintains powder properties during storage and transport.
Q: Is titanium metal powder flammable?
A: Yes, as a finely divided reactive material titanium powder can combust when exposed to air under certain conditions, generating intense heat. Care needs to be taken to prevent static build up or sparks during powder handling.
Q: What is the typical bulk density of titanium powder?
A: The tap density for titanium powder usually falls between 2 – 5 g/cc based on the grade, particle morphology and size distribution. Spherical gas atomized powders with controlled size ranges have the highest densities on the top end around 4-5 g/cc. HDH powders exhibit lower densities between 2 – 3 g/cc.
Q: What effect does the energy input during production have on resulting powder characteristics?
A: Higher plasma power or increased melt superheat in gas atomization results in finer powder fractions. Fast solidification kinetics also leads to more chemical homogeneity and purity. However, high energy processing is more expensive. An optimum balance needs to achieved based on target material performance requirements vs economics.
Conclusion
With capabilities to meet the most demanding application requirements across diverse sectors, high performance titanium metal powder sees increasing adoption. However, intricate production techniques tailored to achieve unique powder particle characteristics make it an expensive proposition currently restricted to specialized usages. As manufacturing scales up and costs decline over time, titanium could potentially displace a section of traditional metal powders. For discerning industries though, the unmatched properties today justify the costs to harness the full potential of titanium metal powder in enabling next generation components and parts.
Share On
MET3DP Technology Co., LTD is a leading provider of additive manufacturing solutions headquartered in Qingdao, China. Our company specializes in 3D printing equipment and high-performance metal powders for industrial applications.
Inquiry to get best price and customized Solution for your business!
Related Articles
About Met3DP
Recent Update
Our Product
CONTACT US
Any questions? Send us message now! We’ll serve your request with a whole team after receiving your message.
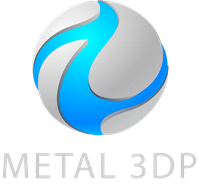
Metal Powders for 3D Printing and Additive Manufacturing