Tungsten 3D Printing:Specifications,Pricing,Pros
Table of Contents
Tungsten and tungsten alloy powders enable printing high-density components with excellent mechanical and thermal properties using laser powder bed fusion (LPBF) and electron beam melting (EBM). This guide provides an overview of tungsten metal 3D printing.
Introduction to Tungsten 3D Printing
Tungsten is a unique material for additive manufacturing due to its:
- Exceptionally high density – 19 g/cm3
- High hardness and strength
- Excellent thermal conductivity
- High melting point of 3422°C
- Challenging processability and machinability
Key applications of printed tungsten parts:
- Radiation shielding
- Aerospace and motorsport components
- Radiotherapy devices and collimators
- Medical implants like dental posts
- Counterweights and balancing components
- Electrical contacts and heating elements
Common tungsten alloys for AM:
- Tungsten heavy alloys with Ni, Fe, Cu, Co
- Tungsten carbides
- Potassium doped tungsten oxides
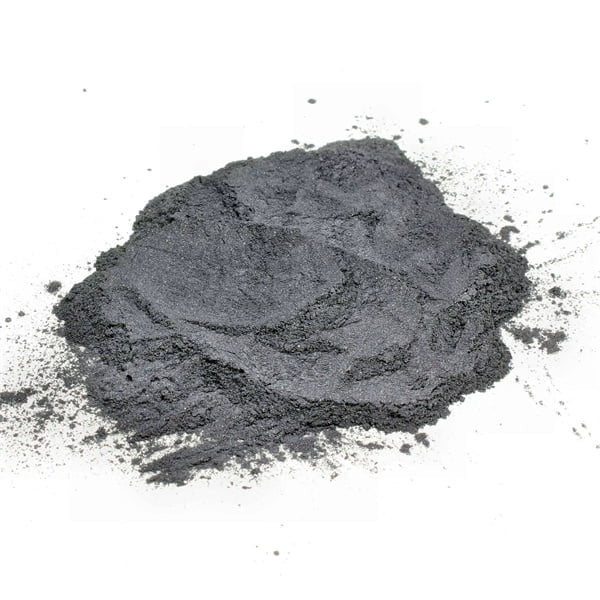
Pure Tungsten Powder
Pure tungsten powder provides the highest densities:
Properties:
- Density of 19.3 g/cm3
- Excellent radiation blocking and shielding
- High hardness up to 400 Hv
- Strength up to 1200 MPa
- Melting point of 3422°C
- Good electrical and thermal conductivity
Applications:
- Medical radiation shielding
- X-ray collimators and appertures
- Aviation counterweights
- Vibration damping in motorsport
- Electrical contacts and heaters
Suppliers: TRU Group, Buffalo Tungsten, Midwest Tungsten
Tungsten Heavy Alloys
Tungsten heavy alloys with nickel, iron and copper provide ideal balance of density, strength and ductility:
Common grades:
- WNiFe (90W-7Ni-3Fe)
- WNiCu (90W–6Ni–4Cu)
- WNi (90W-10Ni)
Properties:
- Density of 17-18 g/cm3
- Strength up to 1 GPa
- Good corrosion and wear resistance
- High temperature strength
Applications:
- Automotive and motorsport components
- Aerospace and defense systems
- Vibration damping weights
- Radiation shielding
- Medical implants like dental posts
Suppliers: Sandvik, TRU Group, Nanosteel
Tungsten Carbides
Tungsten carbide powders print extremely wear resistant parts:
Types
- WC-Co hardmetals with 6-15% cobalt
- WC-Ni cemented carbides
- WC-CoCr cermets
Properties
- Hardness up to 1500 HV
- Compressive strength over 5 GPa
- High Young’s modulus
- Excellent abrasion and erosion resistance
Applications
- Cutting tools and drill bits
- Wear parts and seals
- Ballistic armor components
- Metal forming and stamping tools
Suppliers: Sandvik, Nanosteel, Buffalo Tungsten
Doped Tungsten Oxides
Potassium doped tungsten oxides like K2W4O13 provide unique electrical properties:
Characteristics
- Semiconducting behavior
- Electrical conductivity tunable with doping levels
- High density up to 9 g/cm3
- High radiation stability
Applications
- Electronics and electrical components
- Electrodes, contacts and resistors
- Thermoelectric generators
- Radiation detectors
Suppliers: Inframat Advanced Materials
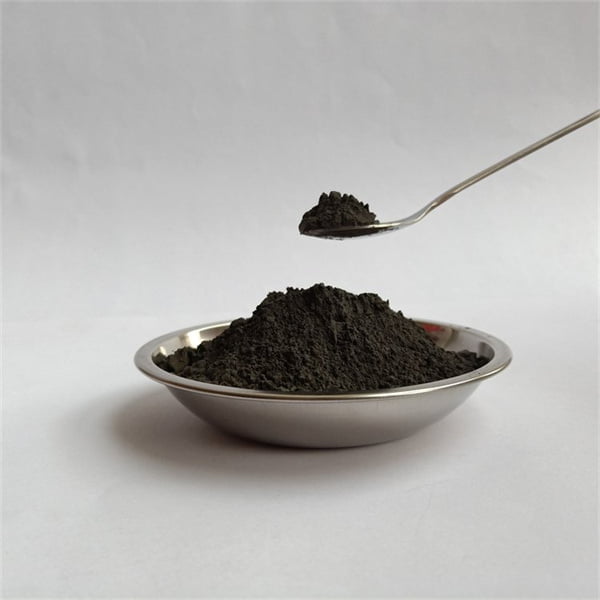
Material Properties Comparison
Material | Density (g/cm3) | Strength (MPa) | Hardness (HV) | Electrical Resistivity (μΩ-cm) |
---|---|---|---|---|
Pure Tungsten | 19.3 | 850 | 260 | 5.5 |
WNiFe | 18 | 1000 | 380 | 8.1 |
WC-12Co | 15.5 | 2000 | 1300 | 60 |
K-doped WO3 | 9 | – | – | 1-100 |
Tungsten Powder Production Methods
1. Hydrogen Reduction
- Most common and economical process
- Tungsten oxide reduced by hydrogen
- Irregular powder morphology
2. Plasma Spheroidization
- Improves powder shape and flowability
- Done after hydrogen reduction
- Provides high purity
3. Plasma Atomization
- Superior powder sphericity and flow
- Control over particle size distribution
- Lower oxygen pickup than gas atomization
4. Chemical Vapor Synthesis
- Ultrafine nano-scale tungsten powders
- High purity with small particle sizes
- Used for tungsten oxide powders
Printer Technology for Tungsten
Laser Powder Bed Fusion (LPBF)
- High power fiber lasers > 400W
- Inert argon atmosphere
- Precise melt pool control critical
Electron Beam Melting (EBM)
- Powerful electron beam > 3kW
- High vacuum environment
- Most suited for highly dense materials
Binder Jetting
- Adhesive binder used to selectively join powder
- Post-processing needed for full density
- Lower part strength compared to LPBF and EBM
LPBF and EBM allow printing high-density tungsten components.
Technical Specifications
Typical tungsten powder specifications for AM:
Parameter | Specification | Test Method |
---|---|---|
Particle size | 15 – 45 microns | Laser diffraction |
Apparent density | 9 – 11 g/cc | Hall flowmeter |
Tap density | 11 – 13 g/cc | ASTM B527 |
Flow rate | 25 – 35 s/50g | ASTM B213 |
Oxygen content | < 100 ppm | Inert gas fusion |
Carbon content | < 50 ppm | Combustion analysis |
Sphericity | 0.9 – 1 | Image analysis |
Controlling powder characteristics like particle size distribution and morphology is critical for high density prints.
Print Process Development
Optimizing LPBF process parameters for tungsten:
- Preheating to control cracking – typ. 100-150°C
- High laser power > 400W with precise control
- Small layer thickness around 20-30μm
- Scanning strategies to minimize stresses
- Controlled cooling after printing
For EBM:
- Heating to >600°C to sinter powder
- High beam current with small point size
- Slower scan speeds for full melting
- Minimizing thermal gradients
Test prints are required to characterize properties.
Suppliers and Pricing
Supplier | Grades | Price Range |
---|---|---|
TRU Group | Pure W, WNiFe | $350 – $850/kg |
Nanosteel | WC-Co, WNiFe | $450 – $1000/kg |
Buffalo Tungsten | Pure W, W-Cr | $250 – $750/kg |
Inframat | Doped WO3 | $500 – $1500/kg |
Sandvik | WC-Co, W-Ni-Cu | $300 – $800/kg |
- Pure tungsten costs ~$350 to $850 per kg
- Heavy alloys cost ~$450 to $1000 per kg
- Doped oxides up to $1500 per kg
Pricing depends on purity, morphology, powder quality, and order volume.
Post-Processing
Typical post-processing steps for tungsten AM parts:
- Support removal using EDM or waterjet
- Hot isostatic pressing to eliminate voids
- Infiltration with lower-melt alloys
- Machining to improve surface finish
- Joining to other components if needed
Proper post-processing is vital to achieve final part quality.
Applications of Printed Tungsten Components
Aerospace: Turbine blades, satellite components, counterweights
Automotive: Balancing weights, vibration damping parts
Medical: Radiation shielding, collimators, dental implants
Electronics: Heatsinks, electrical contacts, resistors
Defense: Radiation shielding, ballistics protection
Printed tungsten components enable performance improvements in demanding applications across industries.
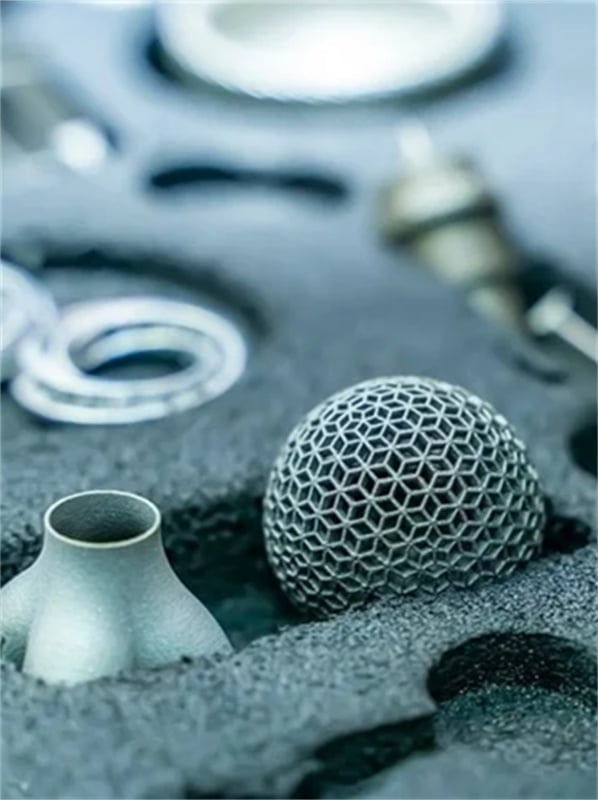
Pros and Cons of Tungsten AM
Advantages
- High density for radiation shielding
- Excellent strength and hardness
- Good thermal and electrical properties
- Customized geometries
- Consolidates multiple parts
Disadvantages
- Difficult and expensive to process
- Brittle material requiring supports
- Low ductility and fracture toughness
- Requires specialized equipment
Troubleshooting Printing Issues
Issue | Possible Causes | Corrective Actions |
---|---|---|
Porosity | Low powder density | Use high density powders near theoretical density |
Inaccurate print parameters | Adjust laser power, speed, hatch spacing through test prints | |
Cracking | Large thermal gradients | Optimize preheating, scanning strategy |
High residual stresses | Use hot isostatic pressing post-print | |
Contamination | Ensure high purity processing atmosphere | |
Warping | Uneven heating or cooling | Optimize scan patterns, anchor part firmly to build plate |
FAQs
Q: What is the typical particle size used for tungsten printing powder?
A: 15-45 microns is common, with a tight control of the particle size distribution around 20-35 microns.
Q: What level of porosity can be expected in printed tungsten parts?
A: Less than 1% porosity is typically achieved through process optimization and hot isostatic pressing.
Q: What alloys provide a good balance of density and mechanical properties?
A: Tungsten heavy alloys with 6-10% Ni, Fe, and Cu provide high density with good ductility and fracture toughness.
Q: What post-processing is required on printed tungsten parts?
A: Support removal, hot isostatic pressing, infiltration, and machining are commonly used post-print processes.
Q: What preheating temperatures are used?
A: For LPBF, preheating up to 150°C is common to reduce residual stresses and cracking.
Q: What safety precautions are necessary when handling tungsten powder?
A: Use appropriate PPE, avoid inhalation, and follow safe powder handling procedures recommended by the supplier.
know more 3D printing processes
Q: What standards are used for qualifying tungsten printing powder?
A: ASTM B809, ASTM F3049, and MPIF Standard 46 cover chemical analysis, sampling, and testing.
Conclusion
Tungsten and its alloys enable additive manufacturing of high-density components with unrivaled stiffness, strength, hardness, and thermal properties using advanced 3D printing processes like LPBF and EBM. With its ultra-high melting point, density, and radiation blocking abilities, printed tungsten components find uses across aerospace, motorsport, medical, defense, and electronics applications. However, the challenging printability and post-processing requirements necessitate rigorous process control and parameter optimization to achieve full densification and ideal material properties. As expertise and experience in printing tungsten develops, its unique advantages can be leveraged to manufacture high-performance components with capabilities exceeding traditional manufacturing limitations.
Share On
MET3DP Technology Co., LTD is a leading provider of additive manufacturing solutions headquartered in Qingdao, China. Our company specializes in 3D printing equipment and high-performance metal powders for industrial applications.
Inquiry to get best price and customized Solution for your business!
Related Articles
About Met3DP
Recent Update
Our Product
CONTACT US
Any questions? Send us message now! We’ll serve your request with a whole team after receiving your message.
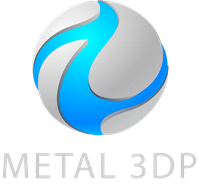
Metal Powders for 3D Printing and Additive Manufacturing